Factors Affecting the Cost of CNC Machining Parts
CNC machines have revolutionized the manufacturing industry, allowing product designers to automate manufacturing and produce high-quality machined parts. Machining disc brake rotors is an alternative to purchasing new products. Rotor machining near me can do it all.
However, many product designers find CNC machining cost estimates quite challenging. As a result, they are often overwhelmed when they receive project quotes from manufacturers.
Several factors affect the cost of a CNC machining part project, including product design, material selection, manufacturing techniques, tooling, and surface finish. This article will cover all of these factors. After reading this article, you’ll know how to estimate (and reduce) CNC machining costs and create the perfect part for your project.
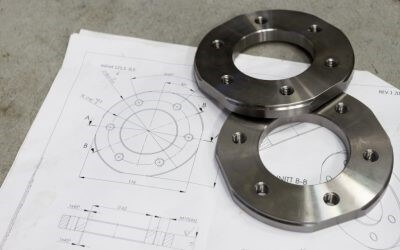
1.Factors Affecting the Cost of CNC Machining Parts
1) Complexity of design
CNC machining is a subtractive manufacturing process – meaning it uses a cutting tool to remove portions of material from a workpiece until the desired part is formed. Due to this mode of operation, CNC machining has certain design limitations. For example, the internal vertical corners of a CNC machining part always have a radius, regardless of the size of the cutting tool. Additionally, CNC cutting tools typically contact the workpiece from the top surface of the workpiece, which makes it challenging (and costly) to manufacture certain features or parts.
The more complex the product design, the longer it takes to machine the part, resulting in higher machining costs. Therefore, to simplify product design and reduce manufacturing costs, you should optimize your design by implementing the following tips:
- Add fillet radii to inside edges to accommodate the cylindrical shape of the CNC cutting tool. The radius should be at least one-third of the cavity depth, and the radius should be the same for all inside edges to save time and eliminate the need for extra tools.
- Use undercuts when you need to create 90° inside edges, because reducing the size of the end mill will not do the job.
- Limit the depth of a cavity to four times its length (or width). Pockets with a small depth-to-width ratio require specialized end mills, which increase manufacturing costs.
- Design undercuts so that they are about twice as deep as they are wide, with enough clearance to allow the cutting tool to enter. Generally speaking, the clearance should be at least four times the depth of the undercut, especially if you are using a T-slot cutting tool. Unless absolutely necessary, keep features to one side of the workpiece to minimize the number of machining directions.
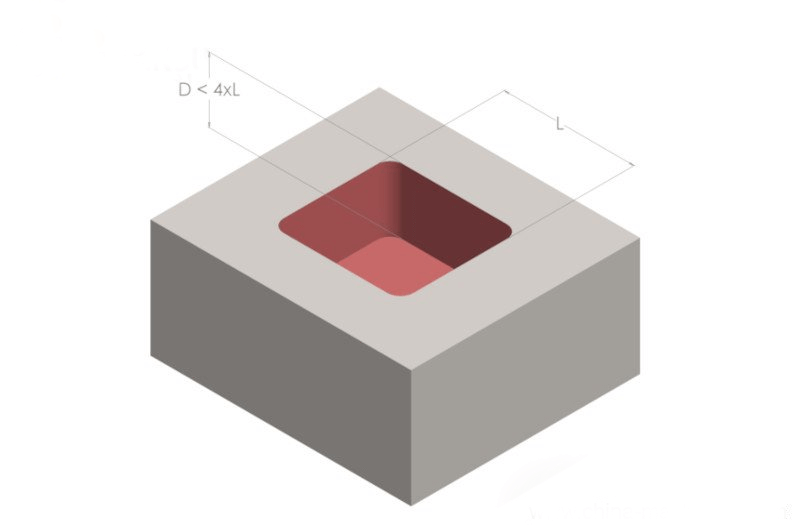
2) Labor
The process of product development using CNC machines involves several steps. For example, you need to create a 3D CAD file first and then convert it into a computer program that the CNC machine uses for automated manufacturing. Because these processes add labor costs, you can reduce costs by performing some of the processes yourself (rather than outsourcing). For example, you can create the 3D CAD of your product first and then outsource the review and production to a manufacturing engineer.
Your manufacturing costs also depend on the number of parts (or units) you want to produce. The more units you have, the higher the manufacturing cost. However, mass production parts cost less than small batches.
3) Selection of Engineering Materials
The material you choose for your product is an important determinant of CNC machining costs. Because CNC machining is a subtractive process, it tends to use more material than additive manufacturing processes such as 3D printing. CNC machine shops usually purchase these materials in blocks and calculate the price per block. Two materials commonly used for CNC machining projects are metals and plastics. Metals are generally more expensive than plastics, so the cost of manufacturing metal parts is higher than the cost of manufacturing plastic parts. Table 1 lists the approximate material costs for CNC machining projects.
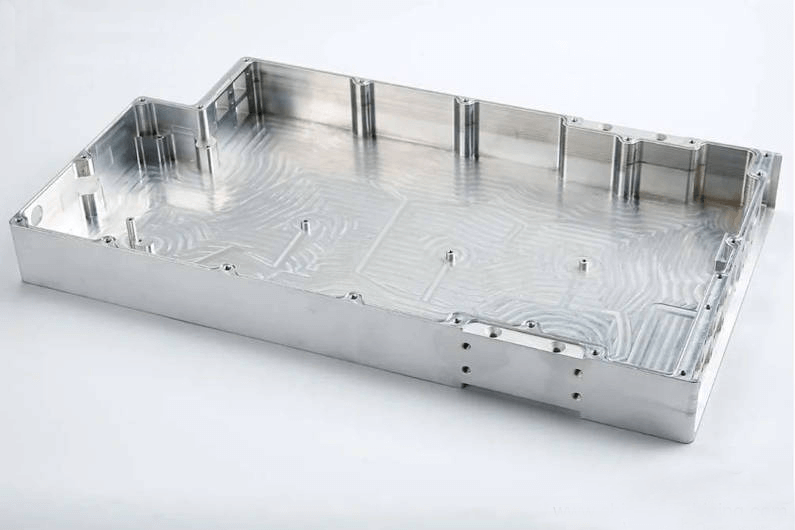
4) Surface Finishing
CNC machined parts usually come out of the production line with an impressive surface finish. Machinists will not charge you extra to manufacture these machined parts. However, if your product requires additional post-processing operations such as anodizing, polishing, and powder coating, you should expect a higher project quote.
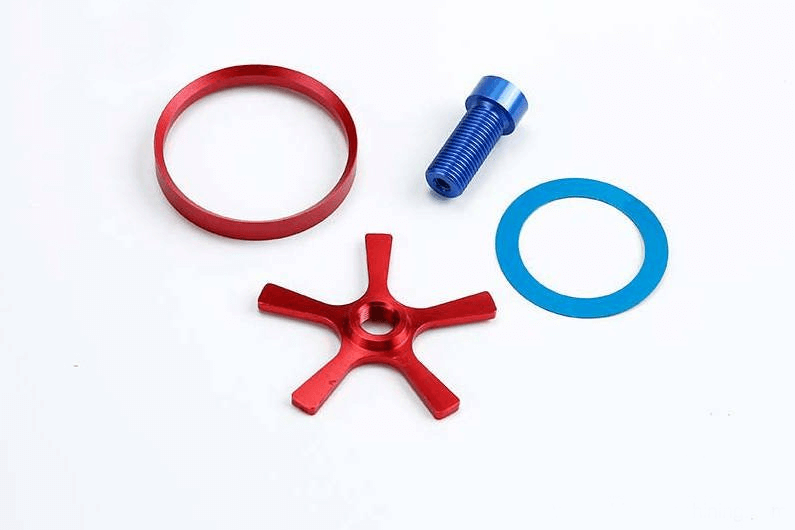
2.Outsourcing can help you reduce manufacturing costs
Many top product designers and business owners reduce machining costs by outsourcing their manufacturing projects to CNC machining plants in China. For example, let’s say you want to manufacture a complex part using a multi-axis CNC machine. You can choose a manufacturer with the most advanced CNC technology as well as highly qualified engineers, technicians, and quality control (QC) experts.