Importance of CNC Machining Plastic Prototypes
The versatility and numerous benefits of plastics make them one of the most important engineering materials today. This article describes different ways to make plastic prototypes, specifically CNC machining. It will help you decide the best plan for your project.
1.Why use CNC machining for plastic prototypes?
CNC machining has many advantages, and here are four scenarios where CNC plastic machining is appropriate.
Scenario 1: Your plastic prototype design contains tiny details
Does your design have a small radius pattern and requires tight tolerances? Then CNC machining may be a good fit for your project. CNC milling machines can achieve radii as small as R0.05 mm and tolerances as small as 4 microns.
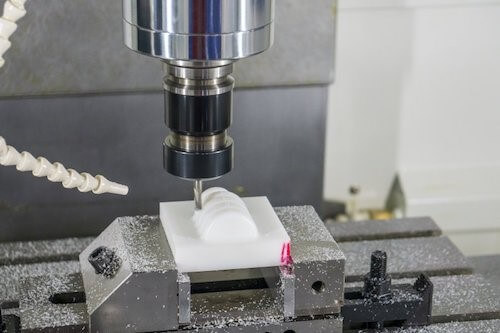
Scenario 2: You need a high-quality surface finish
If you just want to make a plastic prototype to visualize a concept or idea, then you should consider CNC machining. It provides a high-quality surface finish and does not leave layer marks that are common during the 3D printing process.
Scenario 3: You want to use a special plastic material
Plastics and polymers such as PVC, PEI, POM, and PEEK are almost impossible to 3D print. CNC machines are compatible with these plastics and others. As long as you have a block of plastic material, a machinist can easily create a CNC plastic prototype design.
Scenario 4: You need an adaptable and fast machining method
Do you want to create a functional plastic prototype so that you can test and fix design flaws? Because CNC machines rely on 3D CAD models and computer instructions to produce machined plastic prototypes, you can quickly change the design and subject it to new tests.
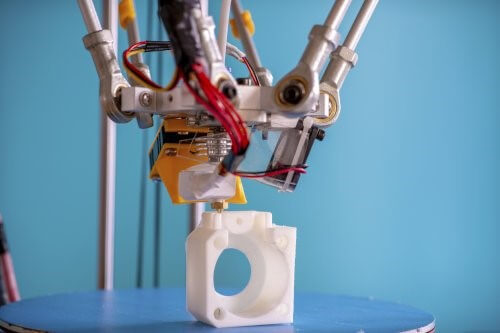
2.Some alternative methods for producing plastic prototypes
Method 1: 3D printing
3D printing, also known as additive manufacturing, originated in the 1980s as a rapid prototyping tool. It covers several different technologies – fused deposition modeling (FDM), stereolithography (SLA) and selective laser sintering (SLS) – all of which involve adding plastic material layer by layer to build plastic parts.
Both 3D printing and CNC machining processes rely on 3D digital models to manufacture parts. However, 3D printing has less material waste than CNC machining. In addition, 3D printing does not require production tools and can create complex geometries. The technology is compatible with thermoplastics such as ABS, nylon, PLA, and ULTEM.
Method 2: Injection Molding
Injection molding is another ideal method for quickly producing plastic prototype parts. The process begins with the creation of an aluminum or steel mold with a runner system that allows the molten plastic to flow to the mold cavity. When the molten plastic material is injected into the mold, cools, and solidifies, it forms the desired shape of the plastic prototype.
Using injection molding ensures that the prototype requires little to no additional work or surface treatment after production. Plastic injection molding also increases strength because fillers can be used in the injection mold. What’s more? This method of plastic prototyping is cost-effective and can be used to manufacture complex designs.
Method 3: Vacuum Casting
Vacuum casting, also known as polyurethane or urethane casting, is a technique for making high-quality plastic prototypes. The process uses silicone molds and a pourable casting resin to replicate a master model. You can use these plastic replicas to visualize ideas (alpha prototypes) or to address design flaws (beta prototypes).
The physical properties and surface finish of vacuum cast parts are comparable to those of injection molded prototypes. The vacuum casting process is also very versatile, as different types of polyurethane (or urethane) can be cast to produce a specified hardness and desired surface texture.
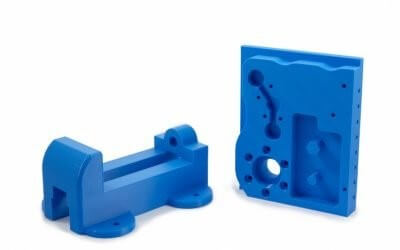
3.How to Determine the Best Method for Prototyping
CNC machining, 3D printing, injection molding, and vacuum casting each have their own characteristics and advantages, making them suitable for different scenarios.
If you are looking to work with difficult-to-machine plastic materials or create complex prototypes with greater structural integrity, then CNC machining is your best choice. While injection molding also provides better structural integrity and good mechanical properties, it is more suitable for large-scale prototyping or production due to the high cost of making aluminum or steel molds.
Silicone molds in the vacuum casting process can produce up to 25 parts; therefore, the process is suitable for small-scale production. However, vacuum cast plastic prototypes usually have a very good surface finish, which is ideal for visual representation of design concepts.
Like the vacuum casting process, 3D printing is also suitable for small-scale production. However, with 3D printing, you can prepare a prototype in a few hours, while the turnaround time for vacuum casting can take up to 5 days.