Introduction to CNC Machining
Wondering about CNC machining and why it’s so important in manufacturing? You’re not alone. Computer numerical control (CNC) machining is a key element of modern manufacturing, using advanced technology to precisely cut, shape, and manufacture parts.
This article takes a closer look at how CNC machines work and their role in manufacturing everything from automotive parts to high-tech products. We’ll also take a look at the many industries that rely on this technology and why it’s so important.
1.Overview of CNC Machining
CNC machining is computer-controlled and produces high-precision parts and components. During this process, a computer program controls the movement of a cutting tool, which is controlled by the CNC programming to remove material from the workpiece to create a finished part.
CNC technology can produce a wide variety of parts, including those made from metal, plastic, and other materials. The process can also produce parts with complex geometries and high levels of precision, making it a popular choice for a wide range of industries, including aerospace, automotive, medical devices, and consumer products.
It offers several advantages over traditional machining methods, including greater accuracy, consistency, and speed, as well as the ability to produce complex geometries and intricate details. It also allows the use of advanced cutting tools and techniques, such as multi-axis machining centers and high-speed machining, which can further improve machining efficiency and quality.
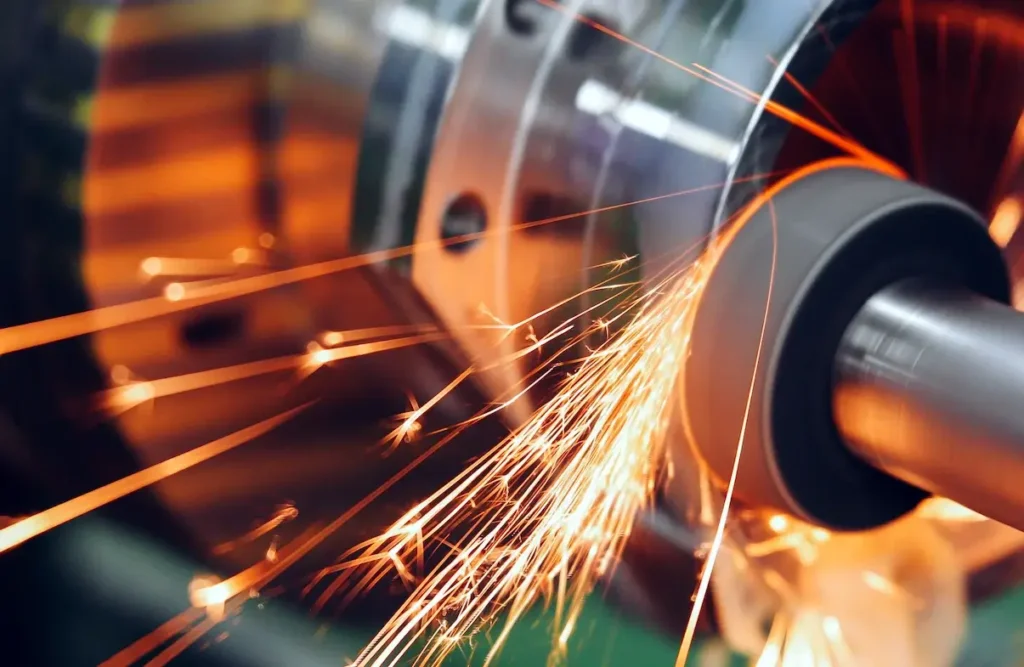
2.History of CNC Machining
Its history dates back to the 1940s, when the first numerically controlled (NC) machines were developed. Over time, these machines became more and more popular and sophisticated. This allowed them to meet the needs of a variety of industries, including aerospace, automotive, and defense.
However, older CNC machines still required manual input and had limited functionality. The transformation of the manufacturing industry began in the 1970s, when computers were introduced and brought about a breakthrough: the first CNC machine.
These advanced machine tools equipped with computer controls were able to process data with unprecedented speed and accuracy. This innovation enabled CNC operators to input commands directly to the machine tool, which then automatically performed the necessary operations, greatly simplifying the manufacturing process.
This was just the beginning for CNC machines, as technology has continued to advance over the years. The development of more advanced software and hardware and the introduction of new materials and tooling options meant that manufacturing units had more possibilities. Today, CNC machinery is common in multiple industries, capable of producing a wide variety of products with high precision.
3.How does CNC machining work?
Modern CNC systems focus on minimizing human intervention. This ensures consistent and continuous performance, which promotes smart manufacturing and provides excellent results.
However, CNC manufacturing requires careful consideration from initial design to final manufacturing. The entire process is divided into three distinct steps:
1) Design
The first critical step in CNC machining involves software applications such as CAD, CAM, and CAE. Engineers and designers rely on these tools to design parts and products and then evaluate their manufacturability.
This evaluation, called Design for Manufacturing (DFM), is critical. It ensures that the design is optimized to maximize efficiency and reduce costs while working within the limitations of existing technology.
In most cases, CAD tools available on the market come with internal CAM tools to facilitate pre-processing and programming. After completing the CAD design, the designer converts it into a CNC-compatible file format, usually STEP or IGES.
2) Preprocessing and Programming
CNC machine programming primarily involves communicating with the machine using G-code and M-code. These codes are generated by the CAM software package and serve as a guide for the cutting tool paths in CNC operations.
Typically, if the design meets DFM (Design for Manufacturing) standards, the CNC machinist does not need to intervene in the preprocessing or operation stages. However, if the design does not meet these standards, some degree of manual intervention may be required to ensure optimal performance.
Preprocessing is a standard step in CNC machining, and its duration depends on the quality of the design. Writing G-code or M-code usually takes only a few minutes. However, the success of CNC programming depends on whether the design adheres to DFM practices. Accurate designs produce correct code and satisfactory results, while design flaws lead to incorrect code and poor results.
3) Machining
The final stage is the machining process, which uses the code provided in the previous step to remove excess material from the block. The accuracy of machine tool processing is critical, but replicating the exact dimensions of the CAD model is often challenging.
That’s why machinists typically apply standard ISO 2768 tolerances, which vary depending on industry requirements. It is a widely accepted principle that tighter tolerances lead to increased manufacturing costs.
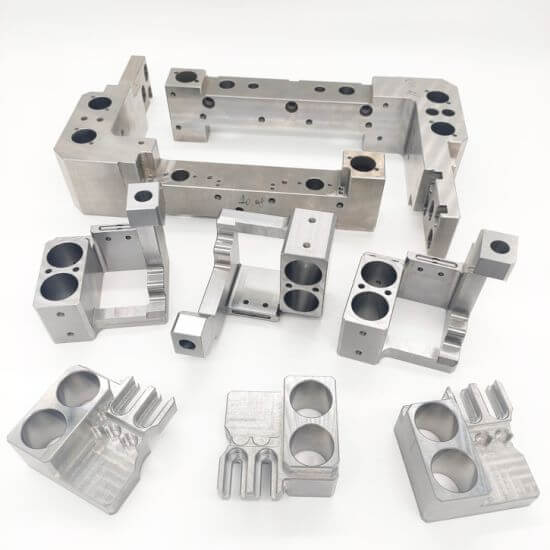
4.Common CNC operations in the industry
CNC machining is a versatile process, and operations vary depending on specific requirements. Simple designs may be achieved with a single operation, such as milling. However, more complex designs often require a greater variety of operations.
Below are some of the key CNC machining equipment widely used in the industry.
1) CNC Milling
CNC milling is a high-precision, versatile machining process used to remove material from a solid block to form a specific shape or design. It involves manipulating a multi-point cutting tool (usually a milling cutter) with extreme precision using a CNC system.
During this process, the workpiece is firmly mounted on a table and the milling cutter rotates at high speed to systematically remove material. This method is particularly effective for generating flat surfaces, but its capabilities extend far beyond simple shapes.
One of the main features of a CNC milling machine is its ability to efficiently create complex geometries by performing intermittent cutting through multiple machining steps. The technology has evolved to include 3-, 4-, and 5-axis milling machines:
- 3-Axis Milling: Movement along the X, Y, and Z axes enables basic operations such as drilling and planing. This method is ideal for simple projects that require simple shapes and is popular for its simplicity. However, it is limited in creating complex geometries, making it best suited for less complex designs.
- 4-Axis Milling: With the addition of a rotary axis, it allows for more complex operations than 3-axis milling. This method is ideal for angled cuts and more complex shapes, expanding the capabilities of CNC machining. It is particularly useful for parts that require additional precision that a 3-axis milling machine cannot provide.
- 5-Axis Milling: This machining method is the pinnacle of CNC milling, with movement along five axes simultaneously, allowing for extreme precision and complexity. It is extremely useful in high-precision industries and can be used to create complex shapes with tight tolerances. This method streamlines production by reducing the need for multiple setups, ensuring efficiency and accuracy.
2) CNC Turning
CNC turning is an efficient machining process that is primarily used to machine cylindrical workpieces, but can also machine square or hexagonal raw materials. The core of CNC turning is the use of a computer-controlled lathe that rotates the workpiece onto a variety of cutting tools. These tools trim and shape the material into the desired cylindrical shape.
The uniqueness of a lathe lies in its versatility and precision, determined by different spindle and speed capabilities. The process can be performed on both vertical and horizontal settings, each suitable for a specific type of workpiece and machining requirements.
There are two main types of machines:
- CNC Lathe: It excels in precision turning operations and is well suited to making high-precision cylindrical parts. It operates by rotating the workpiece relative to a fixed tool, and is well suited to simple to moderately complex shapes, and is commonly used in the automotive and aerospace industries.
- CNC Turning Center: It combines turning with additional functions such as milling and drilling. This multitasking capability allows complex parts to be produced in a single setup, thereby improving efficiency and accuracy. It is essential in industries that require complex, multi-faceted components, such as advanced manufacturing.
3) CNC Drilling
Drilling is an important manufacturing process that creates threaded holes of varying sizes on a workpiece. The process is fully automated thanks to the involvement of computers, which allow for precise control of the movement and speed of the drill.
CNC drilling is very common in many industries, including printed circuit boards, metal parts, and plastics. The process offers several advantages over traditional manual drilling, including greater accuracy, repeatability, and efficiency.
4) CNC Routing
The rough operation of a CNC router is the same as that of a milling machine. Routers typically work with softer materials, such as wood, while milling is often used for harder metals. Like any CNC operation, routers also offer excellent consistency, efficiency, and accuracy.
During the milling process, the workpiece remains completely stationary while the spindle moves in different directions. Since the milling process targets softer materials, the overall spindle speed can be very low. There are many CNC milling machines, including desktop milling machines, gantry milling machines, and mobile gantry milling machines. The choice of machine and cutting tool depends on the specific requirements of the workpiece and the desired end product.
5) Electrospark Machining
Electrodischarge machining (EDM) is a manufacturing process that uses electrical spark discharge to erode materials and produce complex shapes and geometries.
The process works by creating a spark between an electrode and the workpiece. The machinist immerses the workpiece in a dielectric fluid that isolates the electrical energy and enables precise control of the spark. The spark discharge vaporizes the workpiece and removes excess material to achieve the desired shape.
There are two main types of EDM: Sinking EDM and Wire EDM. Sinking EDM uses a consumable electrode to create the spark. In contrast, Wire EDM uses a thin wire that moves back and forth to create the spark.
6) CNC Plasma Cutting
CNC plasma cutting is a dynamic manufacturing process that is widely used in large industrial settings and is known for its ability to perform high-speed, precise cutting of conductive materials such as steel, stainless steel, aluminum, brass, and copper.
This method involves a plasma torch that creates a powerful plasma arc between the electrode and the workpiece, effectively melting and vaporizing the material at the point of contact. A key component of the process is a high-pressure gas flow, such as air or nitrogen, which expels the molten material away from the cutting area, resulting in a clean, precise edge with minimal deformation or discoloration.
The technology stands out for its versatility, seamlessly cutting both thin and thick materials, which has expanded its range of industrial applications. In addition, plasma cutting is cost-effective, with lower operating costs compared to other methods. Its combination of speed, precision, and economy makes it an essential tool in modern manufacturing, especially in industries where efficiency and accuracy are critical.
7) CNC Laser Cutting
CNC laser cutting is an important technology in industrial manufacturing, known for its precision and speed. It uses advanced lasers, including CO2, Nd, and Nd:YAG types, to effectively vaporize materials, ensuring clean and precise cuts. The technology is widely used across industries because it is versatile and can process a wide range of materials.
The technology’s precision is not limited to a single operation; it excels in repeatability, which is critical for large-scale production. This consistent precision is particularly beneficial in industries such as aerospace and automotive, where precision is critical. CNC laser cutting is also known for its efficiency, minimizing material waste and achieving superior precision.
In addition, the process simplifies workholding and reduces workpiece contamination, which improves overall productivity. With its ability to create fine cuts and hold tight tolerances, it has become an indispensable tool in contemporary manufacturing.
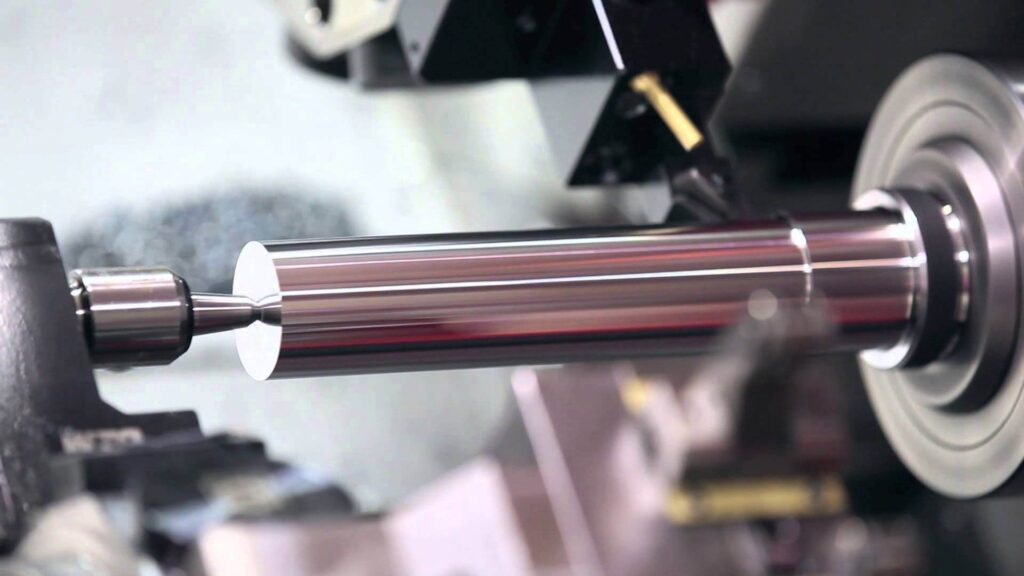
5.Conclusion
CNC machining is a cornerstone of modern industry, sparking the curiosity of those outside the industry. It is a key driver of the industrial age and will play a major role in the future.
The rise of smart factories and Industry 4.0 depends on the capabilities of CNC machining. The technology combines manual machining with digital control to ensure unparalleled precision and consistency. While there are some limitations to the manufacturing technology, its advantages far outweigh these challenges. As the technology develops, it is expected that current issues will be resolved, further increasing its impact.