CNC Metal Cutting Machines: The Ultimate Selection Guide
When it comes to metal cutting, choosing the right CNC machine is essential to ensuring precision and efficiency on your project.
1. Importance of Choosing the Right CNC Metal Cutting Machine
Choosing the right CNC metal cutting machine is essential for any metal fabrication project.
Here is a breakdown of key factors to consider to ensure you choose the best machine for your needs:
1. Production Needs: Determine the size of your project – low-volume, medium-volume, or high-volume production. This will determine the machine’s capacity and level of automation.
2. Material Compatibility: Consider the type of metal you’ll be machining. Different cutting techniques work well with different materials.
3. Machine Capabilities: Research cutting speeds, accuracy requirements, and the size and thickness of metal the machine can handle.
4. Features and Functionality: Explore features like automatic tool changers, chip handling systems, and dust collection for efficient operation.
5. Budget and ROI: Consider initial cost, ongoing maintenance needs, and how the machine can improve your productivity and ROI.
6. Manufacturer Reputation: Choose a reputable manufacturer known for quality machines, reliable support, and readily available replacement parts.
By carefully considering these factors, you will be able to select the ideal CNC metal cutting machine for your shop, optimize your workflow, and achieve exceptional results.
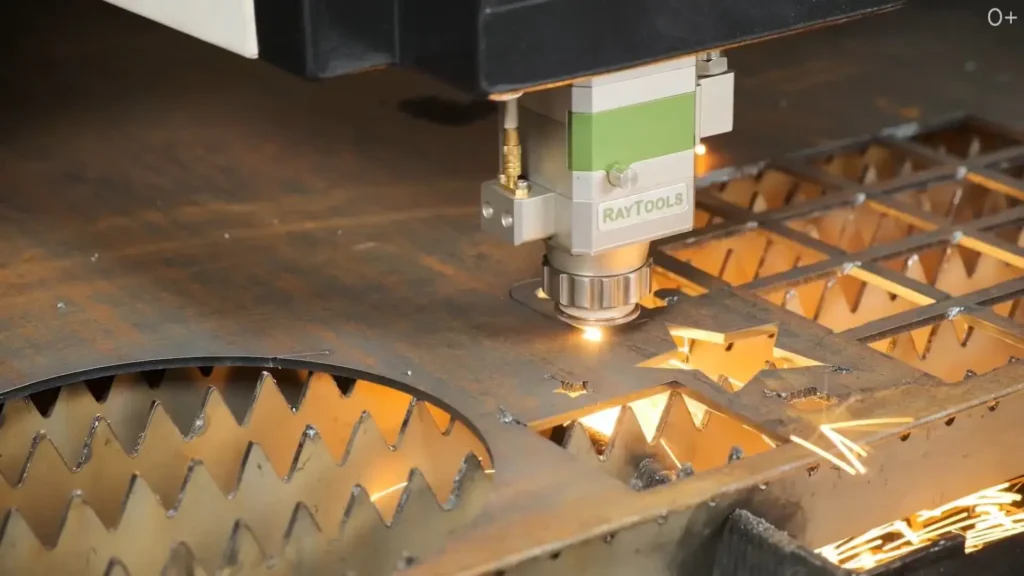
2. Learn about CNC Metal Cutting Machines
CNC metal cutting machines are advanced tools that use computer programming to control the movement and operation of the cutting tools. They are designed specifically for precision metal cutting and provide an efficient and precise method for various types of metal forming.
One of the main advantages of using CNC machines for metal cutting is their ability to automate the entire process. With computer programming, operators can easily input the desired dimensions and specifications, allowing the machine to make precise cuts without human intervention. This not only saves time, but also ensures consistent and accurate results.
There are different types of CNC metal cutting machines on the market, each with unique features and capabilities. Some popular choices include CNC laser metal cutting machines, plasma cutters, water jet cutters, and milling machines. Each type offers specific advantages, depending on the requirements of your metal cutting project.
CNC laser metal cutting machines utilize a focused laser beam to melt or vaporize metal, allowing for precise cuts with minimal heat-affected zones. These machines offer fast cutting speeds, high precision, and the flexibility to handle a wide range of metals.
Plasma cutters, on the other hand, use ionized gas to create an arc to melt metal. They are known for their ability to quickly cut thick materials, but can produce rougher cut edges than laser cutters.
Water jet cutters utilize a high-pressure stream of water mixed with abrasive particles to erode metal. They excel at cutting complex shapes without thermal deformation, but are generally slower than laser or plasma cutters.
Milling machines use a rotating multi-point tool to remove material from a workpiece by pushing or rotating the tool into the workpiece. They offer great flexibility and precision, but can require more setup time and expertise.
When considering the right CNC metal cutting machine for your project, it is important to evaluate your specific requirements. Factors such as the type and thickness of metal you are using, the cutting speed you require, your accuracy requirements, and your budget should all be taken into account.
3. Factors to Consider When Choosing a CNC Metal Cutting Machine
When choosing a CNC metal cutting machine, you should consider several important factors. These factors will help ensure that the machine you choose will meet the specific requirements of your metal cutting project while also providing the necessary accuracy and precision.
1) Specific Requirements of Your Metal Cutting Project
Before selecting a CNC metal cutting machine, it is critical to evaluate the specific requirements of your metal cutting project. Consider factors such as the type and thickness of material to be cut and the size and complexity of the parts that need to be produced. This information will help determine which type of CNC machine will best suit your needs.
2) Importance of Machine Accuracy and Precision
In metal cutting, getting the results you expect depends on two key factors: machine accuracy and precision.
Here is a breakdown of the key benefits of high machine accuracy and precision:
1. Ensure parts are cut to exact dimensions: Accurate machines ensure that your metal parts meet the exact specifications of your design, eliminating inconsistencies and ensuring proper assembly.
2. Guarantee smooth edges with minimal errors: Precision machines provide clean cuts with minimal errors or imperfections, reducing the need for rework and improving the overall quality of the final product.
3. Lead to a higher quality final product: By ensuring exact dimensions and smooth surfaces, the accuracy and precision of the machine contribute greatly to the overall quality and functionality of the final metal product.
4. Reduced material waste and production costs: Precision cutting minimizes material waste, which saves costs. Reducing rework due to errors also reduces production time and labor costs.
5. Improved overall production efficiency: When machines provide consistent, high-quality cuts, production runs more smoothly with fewer interruptions for adjustments or corrections, which improves overall efficiency.
When selecting a CNC machine, prioritize features that increase accuracy and precision, such as high-resolution linear scales and rigid structures. These features are essential to achieving optimal metal cutting results.
In summary, machine accuracy and precision are essential to a successful metal cutting operation. By prioritizing these factors, you can ensure high-quality parts, minimize waste, and achieve greater efficiency in your production process.
3) Evaluate the cutting capabilities of different machines
Different CNC machines offer different cutting capabilities, so it is critical to evaluate these capabilities before making a decision. Consider maximum spindle speed, feed rate, and tool change time. In addition, look for machines that offer multiple cutting options, such as multi-axis machining or laser cutting capabilities, if it fits your project requirements.
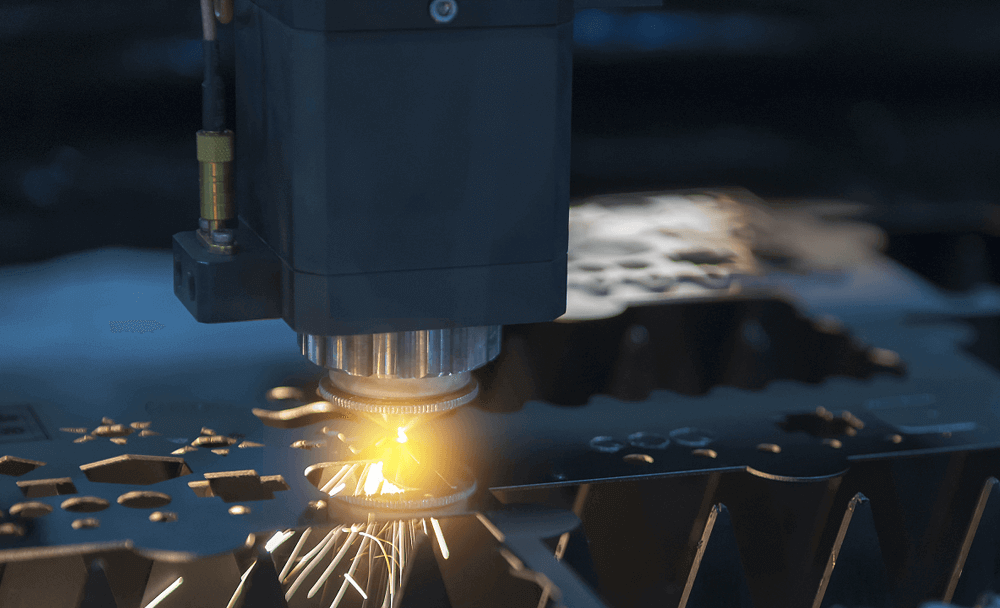
4. Comparison of CNC laser metal cutting machines
1) Explore different types of laser metal cutting machines
There are several types of laser metal cutting machines on the market today. Fiber lasers are popular for their high energy efficiency and low maintenance requirements. They are suitable for cutting thin to medium thickness metals, such as stainless steel and aluminum. On the other hand, CO2 lasers are better suited for cutting thicker materials, such as wood, plastics, and acrylics.
2) Advantages and disadvantages of using laser metal cutting machines
Laser metal cutting machines have revolutionized the metalworking process, providing a precise and efficient cutting method. However, like any technology, they also have advantages and disadvantages.
① Advantages of laser metal cutting machines:
1. High precision and minimal distortion: The laser beam enables high-precision cutting while minimizing warping or material deformation, which is ideal for complex designs and tight tolerances.
2. Fast cutting speed: Compared with traditional cutting methods, laser cutting has significantly faster processing time, thereby increasing productivity.
3. Automation capability: Laser cutting machines are computer-controlled, which enables automation, reduces the need for human intervention, and improves overall production efficiency.
4. Material versatility: Laser cutting machines can process a wide range of metals, providing flexibility for project materials.
② Disadvantages of laser metal cutting machines:
1. High initial cost: Laser cutting machines are a significant investment compared to other CNC metal cutting options.
2. Maintenance requirements: Maintaining optimal performance and service life requires regular maintenance, which increases operating costs.
3. Material thickness limitations: While it works well for thin to medium thickness metals, thicker metals may pose a challenge to some laser cutters.
Laser metal cutting machines provide a powerful and precise solution for a variety of metal processing needs. However, understanding the limitations and costs compared to other methods is essential to making a wise investment decision.
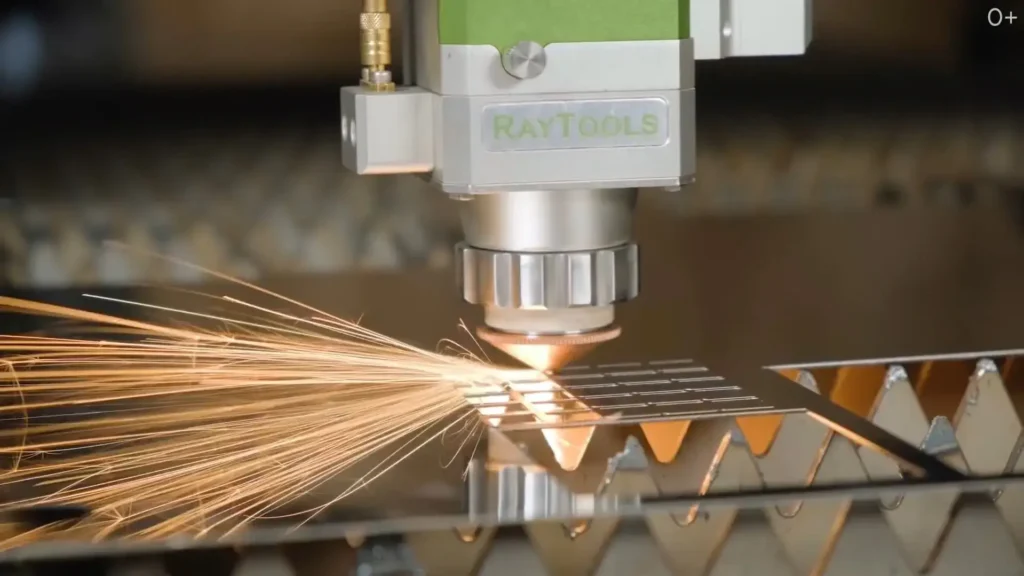
5. Explore metal cutting CNC machining centers
CNC machining centers are advanced machines used for metal cutting and forming processes. These centers utilize computer numerical control (CNC) technology to automate and simplify the metal cutting process, thereby improving efficiency and precision.
1) Understand the functions of CNC machining centers
CNC machining centers provide a wide range of functions for metal cutting tasks. They can perform a variety of operations, such as milling, drilling, tapping, and contouring, with high precision and repeatability. These machines are equipped with multiple axes, allowing for complex and fine cuts on various types of metals.
2) Benefits of using CNC machining centers for metal cutting
CNC machining centers have revolutionized the metal cutting process, bringing a range of benefits to manufacturers. They are as follows:
1. Improved speed and efficiency: CNC machines operate at high speeds and automate processes, significantly reducing production time compared to traditional methods.
2. Superior precision and accuracy: These machines provide consistent and highly accurate results even for complex metal cutting tasks.
3. Material versatility: CNC machining centers can process a wide range of metals, from aluminum and steel to various alloys, giving great flexibility in material selection.
4. Reduce human error and improve safety: Automation minimizes the need for human intervention, greatly reducing the risk of human error and improving workplace safety.
5. Minimize material waste: The precise control of CNC machining can optimize the use of materials, minimize waste and production costs.
CNC machining centers offer a powerful and versatile solution for metal cutting, providing manufacturers with faster production times, superior precision, material flexibility, and increased safety.
6. Factors to Consider When Selecting a CNC Machining Center
When choosing a CNC machining center for your metal cutting needs, you should consider several factors:
1. Machine Size: Determine the size requirements based on your specific project and the space available in your shop.
2. Spindle Power: Consider the power output required to effectively cut different types of metals.
3. Control System: Look for a user-friendly control system that allows for easy programming and operation.
4. Tool Options: Make sure the machine offers a variety of tool options to accommodate different cutting needs.
5. Maintenance and Support: Choose a machine made by a reputable manufacturer.
By carefully considering these factors, you can select the right CNC machining center to meet your metal cutting requirements while ensuring long-term reliability and efficiency.
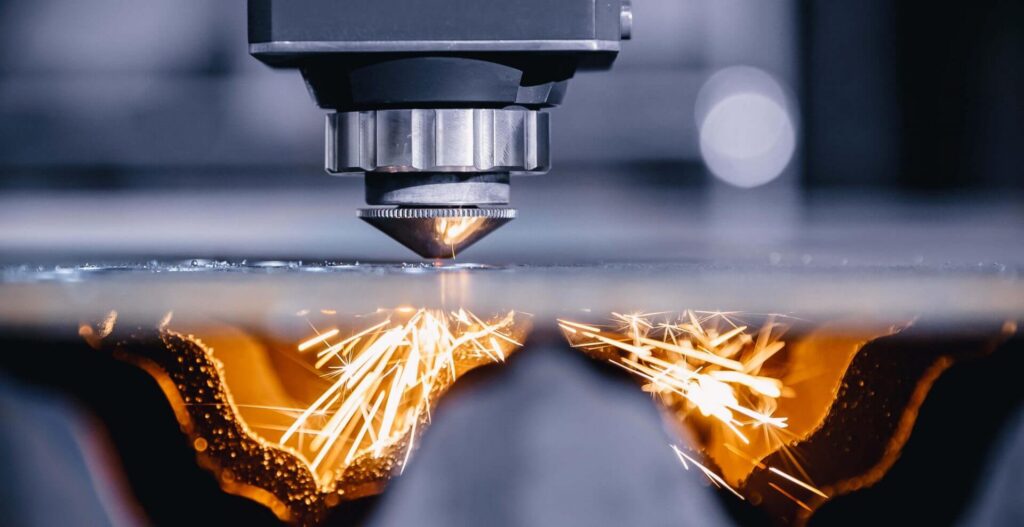
7. Choosing the Right CNC Machine for Your Metal Cutting Needs
When choosing a CNC machine for your metal cutting needs, it is important to consider several factors.
1) Evaluate Your Production Volume and Requirements
It is crucial to evaluate your production volume and requirements before making a decision. Determine the amount of metal cutting you need to complete on a regular basis, and consider any future growth projections. This will help you choose a CNC machine that can handle the workload efficiently.
2) Importance of Machine Reliability and Durability
When choosing a CNC machine for metal cutting, you should prioritize machines that are built to last. Here are the reasons why:
1. Uninterrupted Production: Reliable machines minimize downtime, ensuring your projects stay on schedule. No unexpected breakdowns mean a smooth and efficient workflow.
2. Consistent Performance: Durability means consistent performance. You can count on precise cuts and high-quality results for every project.
3. Reduced Costs: Reliable machines require fewer repairs and replacements, saving you money in the long run.
4. Sustainable Choice: Durable machines are long-lasting, reduce waste, and minimize environmental impact.
3) Explore Other Features and Options
In addition to production, reliability, and durability, it is important to explore the other features and options that different CNC machines offer for metal cutting. Consider factors such as cutting speed, versatility in handling different types of metals, ease of use, and compatibility with other tools or software.
8. Conclusion
Making an informed decision when choosing a CNC metal cutting machine is essential to the success of your metal cutting project. By choosing a CNC machine that fits your metal cutting needs, you can bring advanced technology and increased productivity to your project. Whether you choose a laser metal cutting machine or a CNC machining center, carefully evaluate your production volume and requirements to make an informed decision. In addition to considering production volume, it is also important to prioritize the reliability and durability of the machine. Additionally, exploring additional features and options can further enhance the capabilities of a CNC metal cutting machine.
If you are looking for an experienced CNC machining manufacturer, Xavier is your ideal choice. The Xavier team is well-equipped to provide high-quality CNC machining solutions. If you need more information or to discuss your machining needs with us, please feel free to contact us.