Comparative Analysis of CNC Milling and Turning: Technology and Application
In modern manufacturing, CNC technology has been widely used in production lines. As the two most common CNC processing methods, CNC milling and turning have significant differences in process characteristics, scope of application, processing accuracy and efficiency.
This article will conduct a comprehensive comparative analysis of CNC milling and turning from multiple dimensions to help manufacturing practitioners better choose the appropriate processing method.
1.Basic Overview of CNC Milling and Turning
(1) CNC Milling
CNC milling is a processing method that removes material through the relative motion between a rotating tool and a workpiece. The tool rotates, while the workpiece is fixed or fed a small amount on the CNC milling machine. The CNC system controls the tool’s motion trajectory to achieve precision processing of the workpiece.
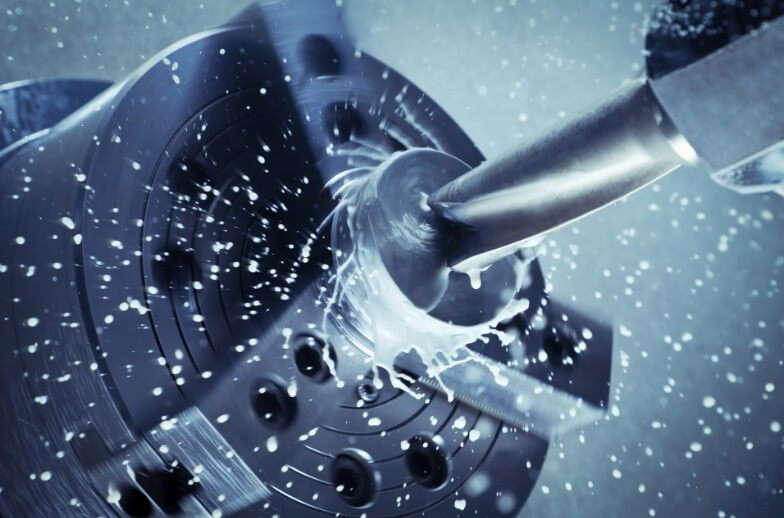
(2) CNC Turning
CNC turning is a processing method that removes material by rotating the workpiece and feeding the tool along the axial or radial direction of the workpiece. The tool mainly moves in a straight line during the processing, and the workpiece rotates at high speed. Turning is suitable for machining axially symmetrical parts, such as shafts, disks, etc.
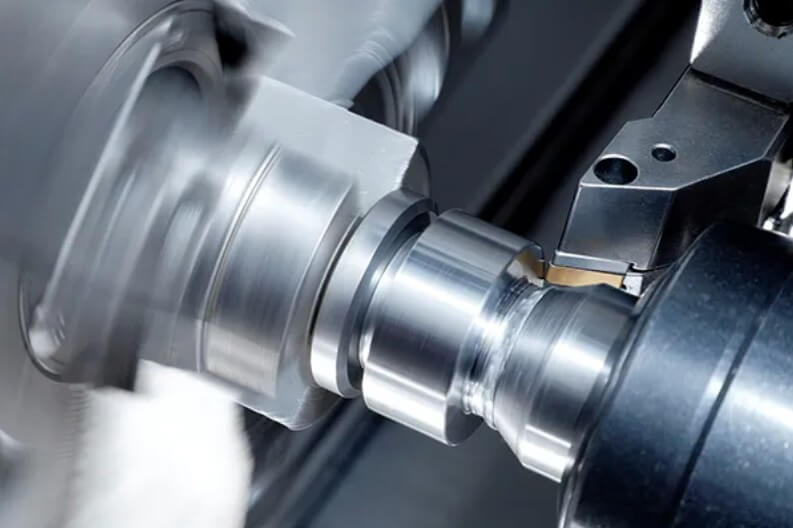
2.Comparison of tool movement between CNC milling and turning
(1) Tool movement in CNC milling
In CNC milling, the tool rotates and can move in multiple directions, including longitudinal, transverse and vertical directions.
This enables CNC milling to process complex geometric shapes in three-dimensional space, including complex features such as holes, slots, bevels, and curved surfaces. The tool path can be flexibly controlled by the CNC program.
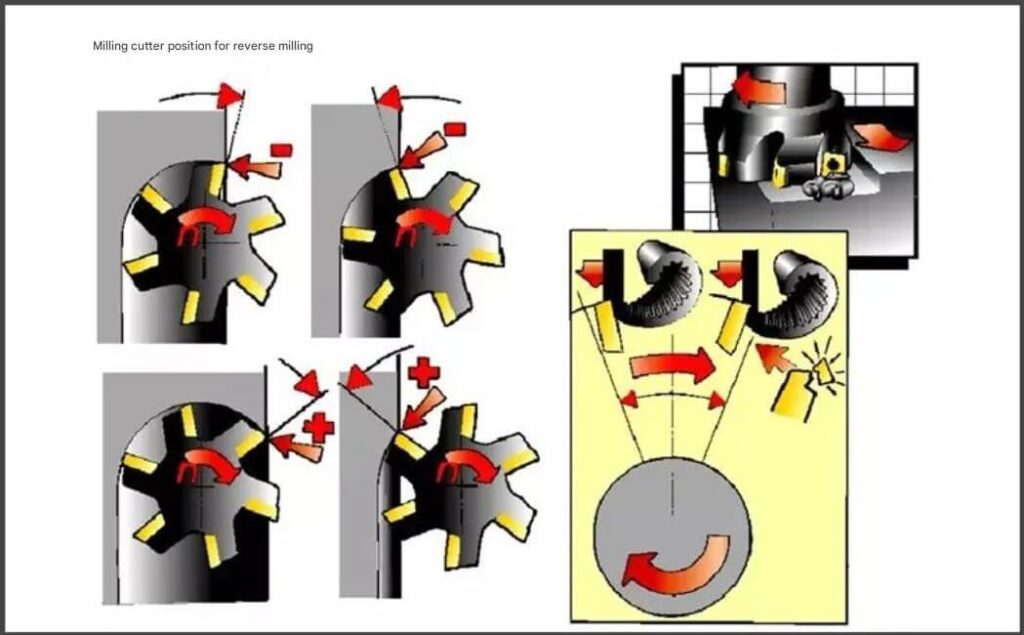
(2) Tool movement in CNC turning
CNC turning is centered on workpiece rotation, and the tool feed is mainly carried out in the radial (lateral) or axial (longitudinal) direction. Turning is usually used to machine shafts or circularly symmetrical parts. The tool movement is relatively simple, usually linear or curved feed.
Therefore, turning has a higher processing efficiency for symmetrical parts, but for parts with complex shapes, the turning capacity is limited.
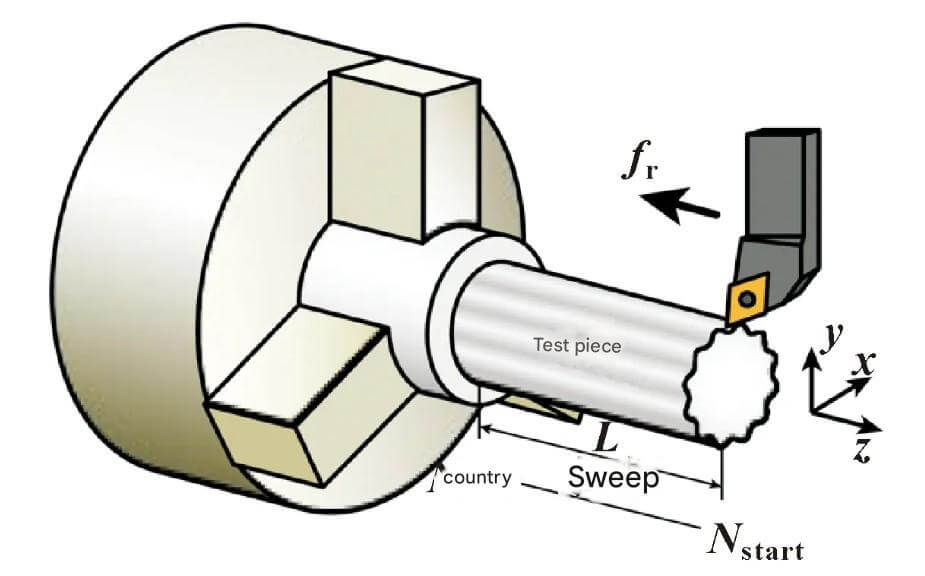
3.Differences in machining accuracy between CNC milling and turning
(1) Machining accuracy of CNC milling
CNC milling is suitable for precision machining because its tool can move freely in multiple directions. Through precise control of the tool path, CNC milling can achieve high-precision machining, which is particularly suitable for the manufacture of parts with complex geometric shapes.
The advantages of CNC milling are particularly obvious when machining hard materials, thin-walled parts and complex surfaces.
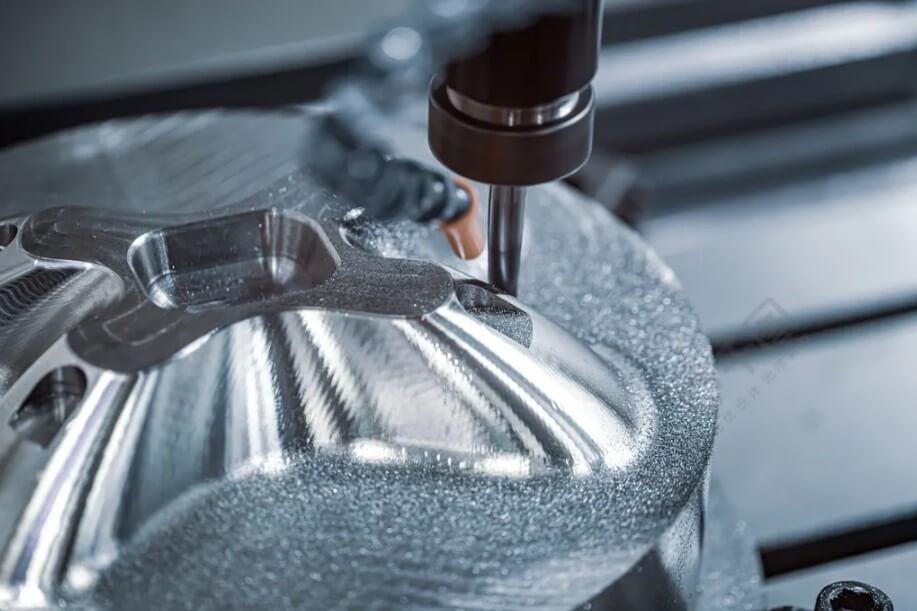
(2) Machining accuracy of CNC turning
CNC turning is usually used to machine parts with symmetrical shapes and has high machining accuracy and stability. Since the workpiece is rotating, the cutting force during turning is relatively uniform, which is suitable for mass production of shaft parts, circular parts, etc.
Although turning has high precision, for some complex parts, the turning capacity will be limited, and it is impossible to achieve precision machining of complex surfaces or special-shaped features.
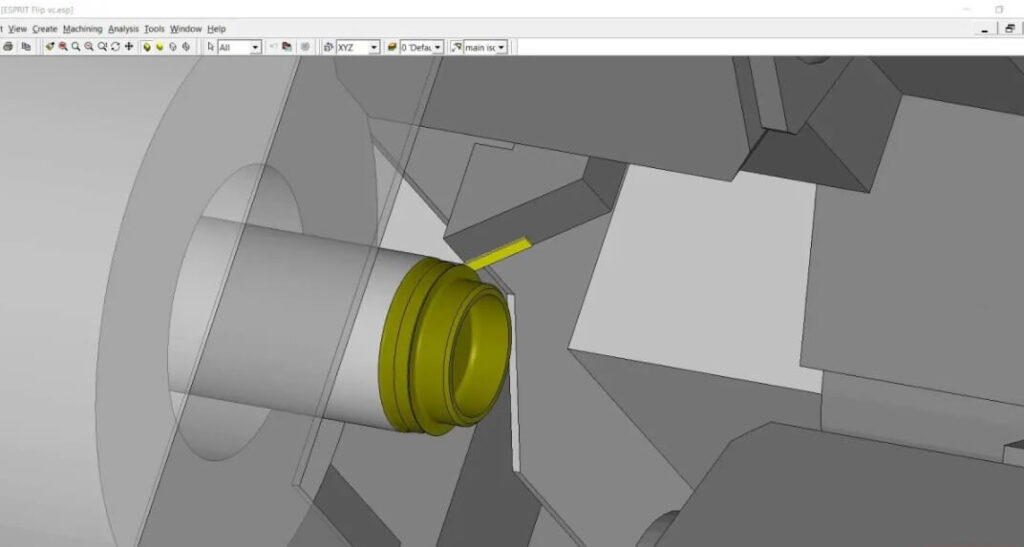
4.Differences in surface quality between CNC milling and turning
(1) Surface quality of CNC milling
The contact between the tool and the workpiece in CNC milling is complex, and the force and heat during the cutting process are relatively dispersed, so the control of surface quality is relatively strict.
By reasonably selecting the tool and cutting parameters, CNC milling can obtain better surface roughness, especially when processing hard materials, it can significantly improve the surface quality.
(2) Surface quality of CNC turning
The contact between the tool and the workpiece in CNC turning is relatively simple, and the heat and cutting force generated during the cutting process are relatively uniform. For symmetrical parts such as shafts and circles, turning can achieve better surface quality.
Although the surface quality of turning is better, the tool wears faster, which may affect the stability and consistency of the processing.
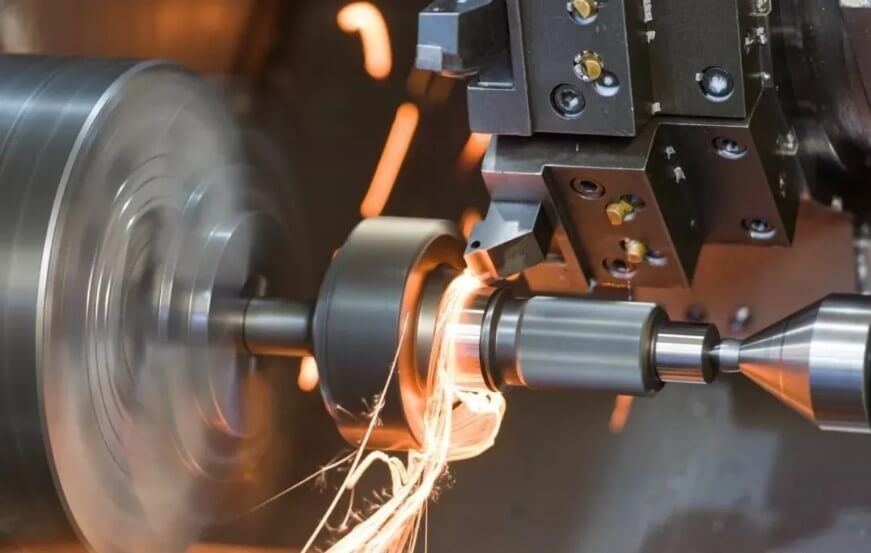
5.Processing efficiency of CNC milling and turning
(1) Processing efficiency of CNC milling
CNC milling has higher flexibility and diversity when processing parts with complex shapes. Through reasonable programming and optimized cutting paths, milling can complete the processing of various shapes in a shorter time.
However, due to the more complex movement of milling cutters, the processing efficiency may not be as high as turning when facing mass production.
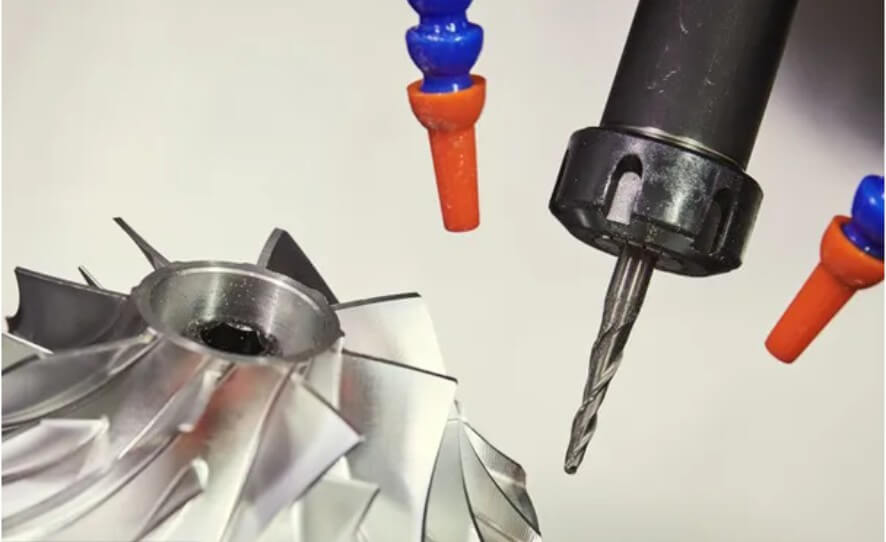
(2) Processing efficiency of CNC turning
The processing efficiency of CNC turning is usually higher. Since the movement of turning cutters is relatively simple and the cutting force is uniform when the workpiece rotates, a large number of processing tasks can be completed in a short time.
Turning is suitable for the processing of shafts, circles and other parts in large-scale, standardized production. Especially when turning long workpieces, turning efficiency is much higher than milling.
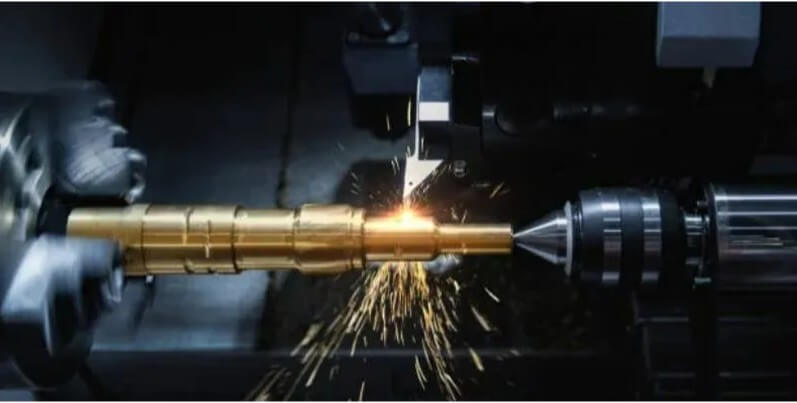
6.CNC milling and turning tool selection and service life
(1) Tool selection for CNC milling
There are many types of CNC milling tools, including end mills, face mills, ball end mills, angle mills, etc. Different types of tools can be selected according to different processing requirements.
During milling, the contact area between the tool and the workpiece is large, so the selection of tool materials and coatings is crucial. Commonly used tool materials include high-speed steel, cemented carbide, ceramics, etc.
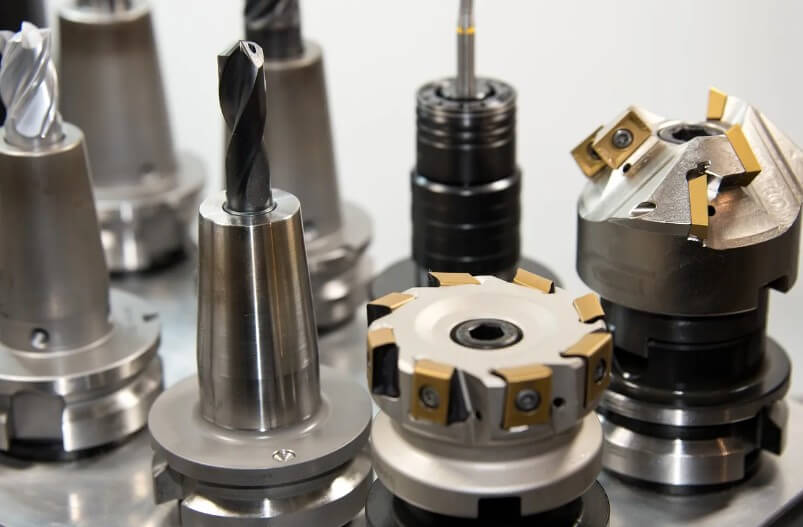
(2) Tool selection for CNC turning
The tools for CNC turning are relatively simple, usually blades or turning tools. The types of tools mainly include external cylindrical turning tools, internal hole turning tools, thread turning tools, etc.
Due to the high-speed rotation of the workpiece during turning, the tool wears quickly. Therefore, the tool needs to be replaced regularly to maintain processing accuracy and surface quality. Tool materials usually choose high-wear-resistant materials such as cemented carbide and diamond.
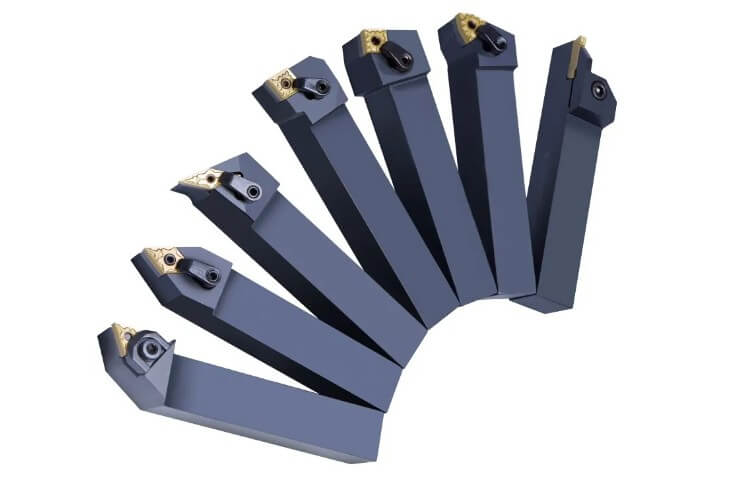
7.Comparison of advantages and disadvantages of CNC milling and turning
(1) Advantages and limitations of CNC milling
1) Advantages:
○ High-precision processing:
CNC milling can achieve higher processing accuracy, especially suitable for processing parts with complex geometric shapes.
○ Strong adaptability:
By adjusting the tool path, diversified processing can be achieved to adapt to different materials and processing requirements.
○ High flexibility:
On the same CNC milling machine, tool movement in multiple directions can be achieved to adapt to multiple processing modes.
2) Limitations:
○ Fast tool wear:
During milling, the contact between the tool and the workpiece is more complicated, the tool wears faster, and may need to be replaced frequently.
○ Slow processing speed:
Especially when processing hard materials or large-sized parts, the milling speed is relatively slow.
○ High equipment requirements:
CNC milling machines usually have high precision and stability requirements, and the equipment cost is high.
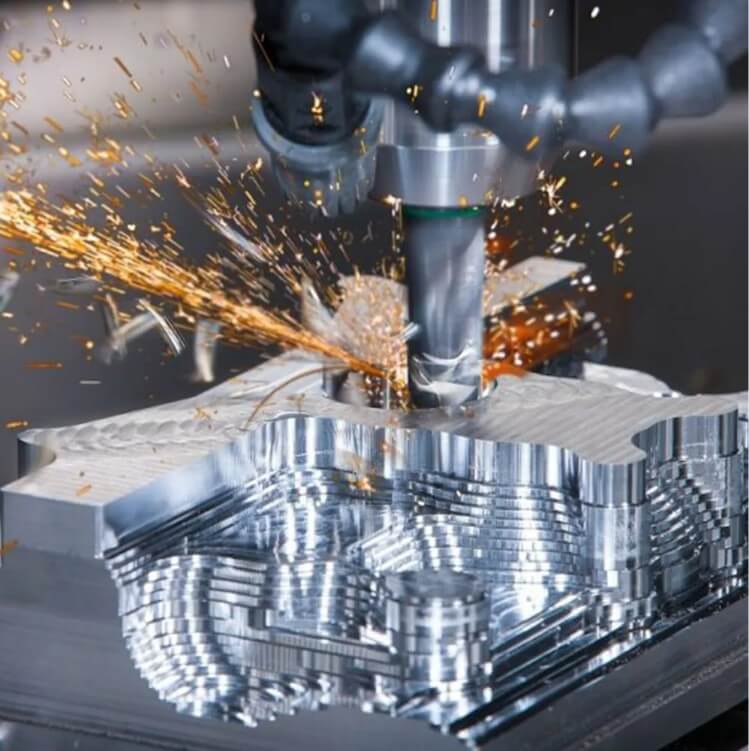
(2) Advantages and limitations of CNC turning
1) Advantages:
○ Fast processing speed:
During the turning process, the workpiece rotates and the tool movement is simple, which is suitable for mass production and can achieve higher production efficiency.
○ Strong stability:
Since the contact between the tool and the workpiece is relatively simple and the cutting force is uniform, the turning process has good stability.
○ Wide applicability:
It has obvious advantages in the processing of shaft and disk parts and is suitable for large-scale production.
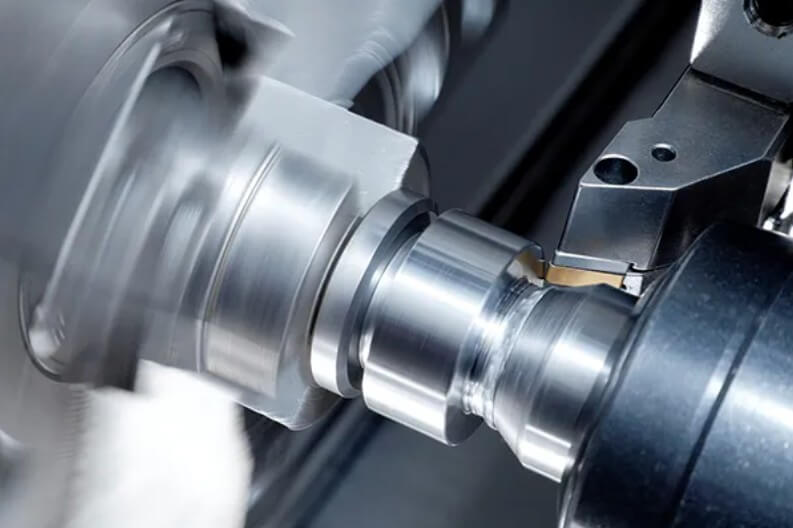
2) Limitations:
○ Limited processing shapes:
CNC turning is mainly suitable for symmetrical circular or shaft parts, and has weaker capabilities for processing complex shapes or curved surfaces.
○ Faster tool wear:
Due to the high-speed rotation of the workpiece, the tool is prone to wear during the turning process and needs to be replaced frequently.
○ Limited processing accuracy:
Although turning is suitable for high-precision processing, its accuracy may not be as good as CNC milling for very complex parts processing.
8.Differences in the scope of application of CNC milling and turning
(1) CNC milling is suitable for:
○ Processing of parts with complex geometric shapes, such as polyhedrons, curved surfaces, inclined surfaces, holes, etc.
○ Processing of parts with asymmetrical shapes, such as molds, complex brackets, aerospace parts, etc.
○ Small batch customized production, suitable for flexible and changeable processing needs.
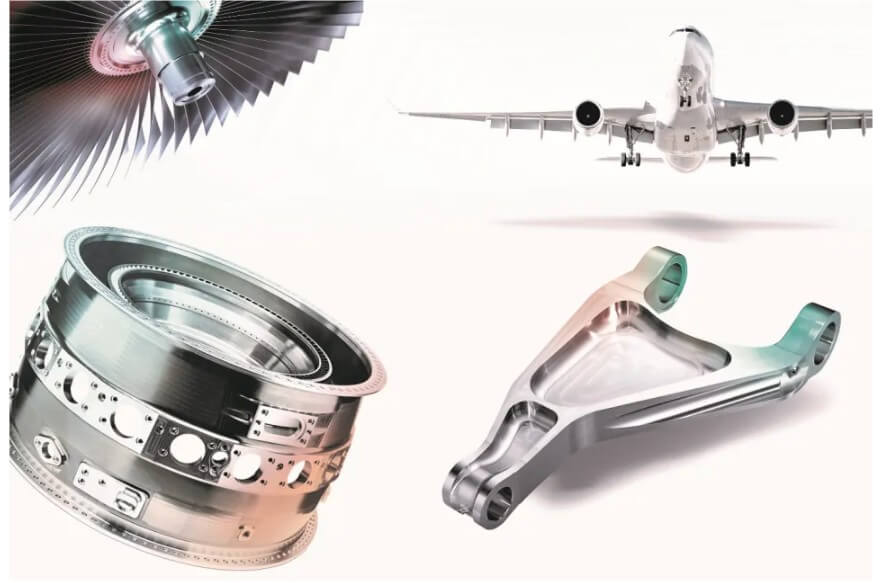
(2) CNC turning is suitable for:
○ Symmetrical parts, such as shafts, discs, gears, etc.
○ Machining of standardized parts in mass production.
○ Machining of long-sized parts (such as automobile engine crankshafts, machine tool spindles, etc.).
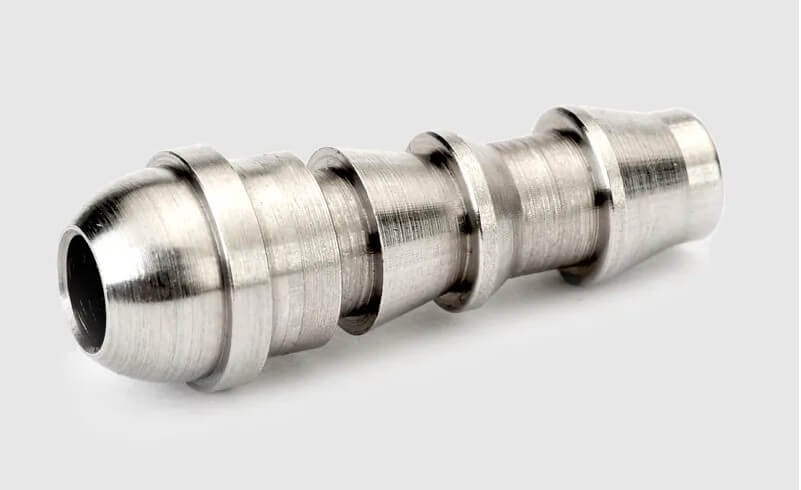
(3) Composite processing trend
With the complexity of processing requirements, turning and milling composite machining centers are becoming more and more popular. This type of equipment integrates turning and milling functions, and can complete all processing steps of complex parts on a single machine tool, greatly improving processing efficiency and accuracy.
9.Cost and economic analysis of CNC milling and turning
(1) Cost of CNC milling
The equipment investment for CNC milling is high, and the operation is complex, requiring high skills from the operator. In addition, the milling tool wears quickly, so the cost of maintenance and tool replacement is high.
However, for complex parts or small-batch production, the flexibility and precision of CNC milling make up for its higher cost.
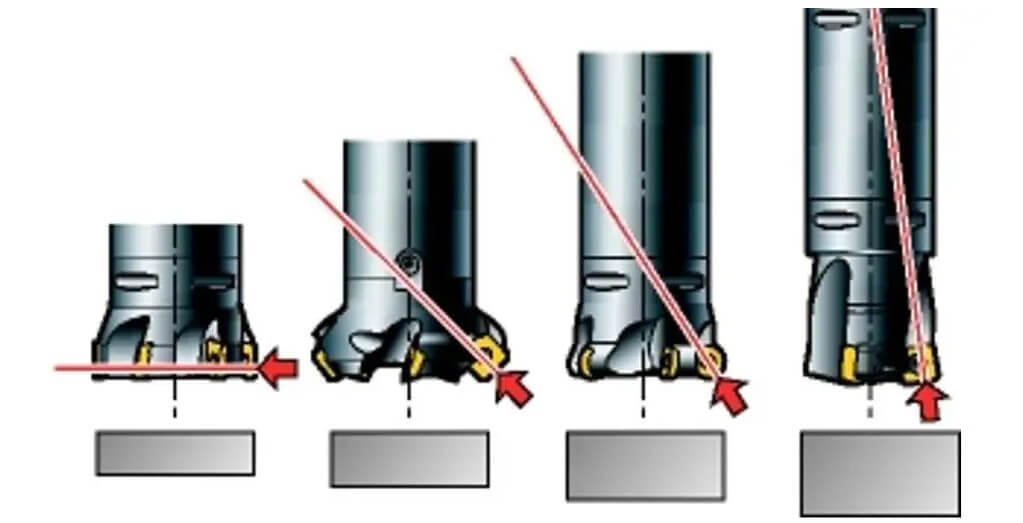
(2) Cost of CNC turning
The equipment cost of CNC turning is relatively low, and due to the simple processing process, the skill requirements of the operator are low.
Turning tools have a long service life and wear slowly, so maintenance costs are low. For mass production, CNC turning is more economical.
10.Process parameters and quality control of CNC milling and turning
(1) Cutting parameter selection
The selection of cutting parameters for milling needs to consider multiple factors such as tool diameter, cutting depth, feed speed, etc.
The cutting parameters for turning mainly focus on cutting speed, feed rate and cutting depth.
The parameter optimization of both processing methods needs to consider material properties, processing requirements and machine tool performance.
(2) Surface quality control
The surface quality of milling is greatly affected by factors such as tool trajectory, cutting parameters, and machine tool vibration.
The surface quality of turning mainly depends on tool geometry parameters, cutting parameters and machine tool accuracy.
Both processing methods require process optimization to achieve the best surface quality.
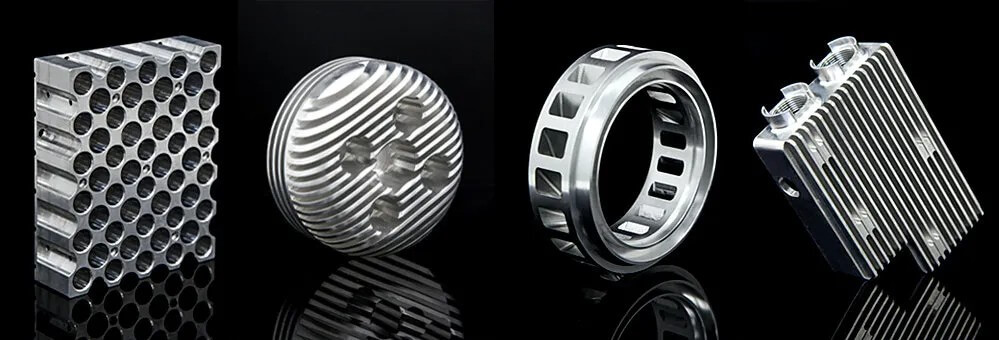
(3) Processing deformation control
During milling, the direction of cutting force changes continuously, which easily causes workpiece deformation.
In turning, the direction of cutting force is relatively stable, but thin-walled parts are also prone to deformation.
Both processing methods require appropriate process measures to control deformation.
11.Conclusion
CNC milling and turning are two indispensable processing methods in modern manufacturing, each with its own unique advantages and applicable fields. CNC milling is suitable for processing complex parts and asymmetrical parts with high precision and flexibility; while CNC turning is suitable for mass production of symmetrical parts with high processing efficiency and economy.
In actual production, according to the shape of the workpiece, processing requirements and production batch, reasonable selection of CNC milling or turning technology can effectively improve production efficiency and processing accuracy. If there are extremely high quality requirements for complex parts, turning and milling composite technology can also be selected.
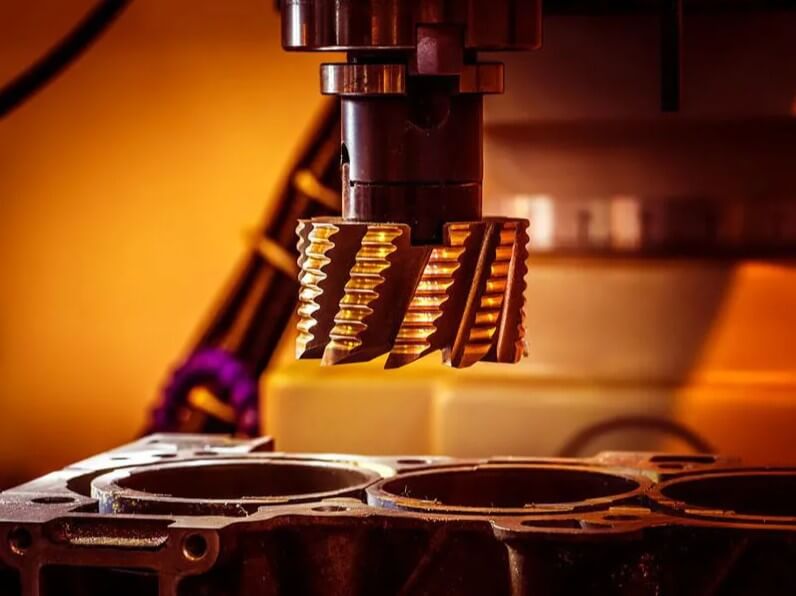
.
If you are looking for an experienced CNC milling and turning manufacturer, Xavier will be your ideal choice. The Xavier team is well-equipped to provide high-quality CNC milling and turning processing solutions. If you need any further information or want to discuss your processing needs with us, please feel free to contact us.