Introduction to CNC Milling Machine Parts
With the advancement of technology, it is easier than ever to make the parts you need. Computer numerical control (CNC) has changed the landscape of manufacturing. It involves using pre-programmed computer software to control the movement and precision of machine tools.
Common types of CNC machines include: CNC lathes, CNC milling machines, CNC routers, 3D printers, and laser and plasma cutters.
In this article, I will focus on the basics of CNC milling machines. Read on to learn everything you need to know, from CNC milling machine parts to how CNC milling works and everything in between.
1.CNC Milling Machine Parts
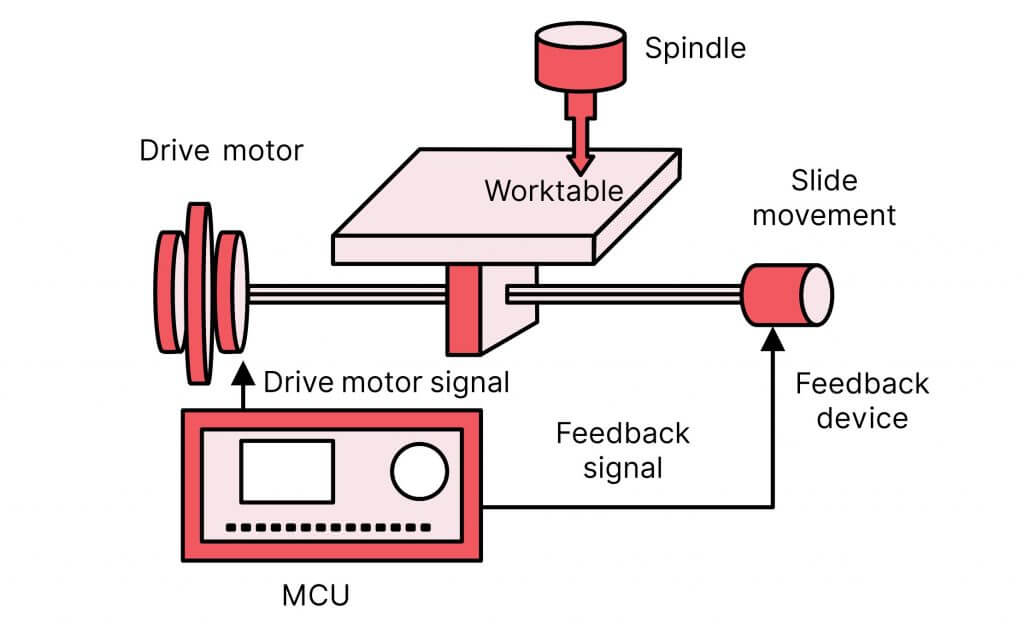
CNC milling machines are a popular manufacturing tool that are used across a wide range of industries. Therefore, it is not surprising that there are many different brands of this equipment and that CNC milling machines vary from shop to shop.
That being said, every CNC milling machine has some basic parts that allow it to function as intended. I have listed the standard and most common CNC milling machine parts you need to know.
1) CNC Controller
The CNC controller is the brain of the machine. It is responsible for controlling the movements and functions of the CNC milling machine. CNC controllers eliminate the need for manual machining. They read the CNC program or G-code provided by the input device and convert these codes into the corresponding machine movements.
The CNC controller then executes the commands by sending appropriate signals to the stepper motors and servo motors. This helps in achieving an efficient and precise machining process.
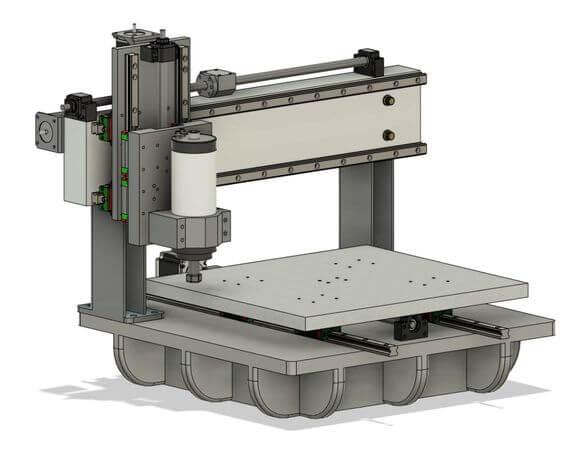
2) Columns and Bases
The columns and bases are used to support all other parts in the CNC machine. They also provide rigidity and resist vibrations generated during machining. These parts are usually made of cast iron.
The columns and bases are also usually filled with epoxy granite to improve their ability to resist vibrations during machining. This improves the quality of the machined parts.
The base supports the weight of the entire machine tool. The column is a vertical part connected to the base and moves along the axis. The column supports the tool holder and houses the oil and cooling system.
3) Knee
The support is a cast iron part that is fixed to the column by a dovetail. It can be moved up and down by vertical positioning screws. This allows for vertical adjustment of the table. The support also provides additional support for the saddle and milling table.
CNC milling machines are equipped with automated systems that adjust the position of the knee according to the G-code provided to the CNC controller. You can also move the knee manually by means of a hand crank.
4) Saddle
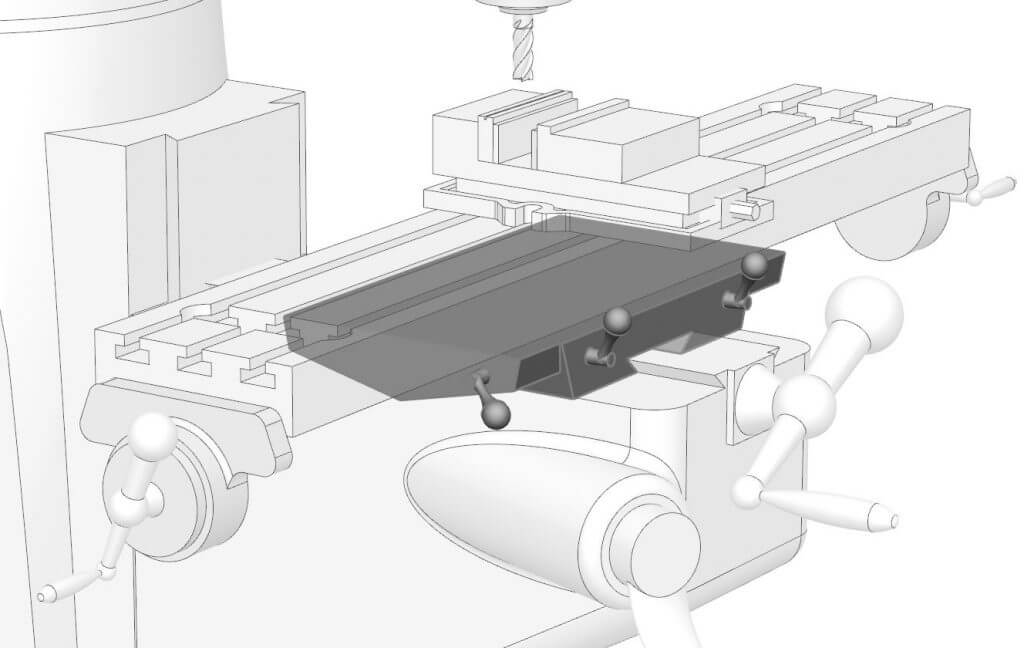
The saddle is located between the knee and the table and is generally made of cast iron and serves to support the table.
The saddle allows for vertical and horizontal adjustment of the workpiece.
5) Feed Mechanism
The feed mechanism of a CNC machine is located at the knee of the machine. This electromechanical system controls vertical (up and down), longitudinal (left and right), and lateral (in and out) feeds. The feed mechanism includes a motor that receives signals from the controller and produces the required motion in the workpiece to facilitate the cutting operation.
6) Work Table
As the name suggests, most machining operations are performed on a work table. The work table is a flat platform used to hold the workpiece during machining. It is mounted on top of the saddle.
In most CNC machine tools, the work table is made of cast iron and is equipped with T-slots. These T-slots allow the workpiece to be fixed to the table by different fastening devices such as clamps or vises. The table is adjustable and a powered feed mechanism is responsible for its movement.
7) Memory
The spindle box is an adjustable arm-shaped part that is unique to vertical milling machines. The spindle box is located on the top of the column and is used to hold the milling head.
8) Cantilever
Just as the ram is unique to vertical milling machines, the cantilever is also a feature of horizontal milling machines. This cast iron beam is mounted on the top of the column and is used to hold the milling head that supports the milling cutter assembly.
9) Spindle support
The spindle support is a cast iron part that is unique to horizontal milling machines. It is connected to the spindle through bearings and is responsible for supporting the cutting tool. The spindle support also plays an important role in reducing the vibration generated during the machining process.
10) Spindle
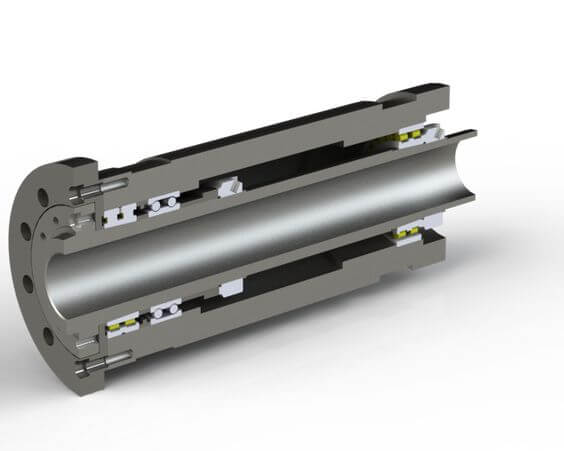
The spindle is one of the key parts of the CNC system. It consists of a taper that is used to hold the milling cutter. The spindle is connected to the main motor of the CNC machine. The CNC controller reads and translates the G-code to rotate the spindle at the specified speed.
Spindle rotation is important because it drives the cutting tool. This part also houses the milling chuck.
11) Tool Changer
An automatic tool changer is often used with CNC machines, especially when the workpiece requires different milling operations. This component allows the machine to perform a series of machining operations in a single run without stopping to use another cutting tool.
The types of tool changers vary depending on the arrangement of the tool magazine and the tool capacity. For example, an automatic tool changer with a chain magazine can hold more than 100 tools, while a turret head tool changer can hold up to 8 tools. A drum ATC can hold up to 30 tools, while a disc ATC can hold 32 to 64 tools.
12) Milling Tool
As the name suggests, the milling cutter is the part responsible for the actual cutting operation. This cutting tool is attached to the column and performs the milling operation based on the G-code provided by the operator.
There are different cutting tools, each designed for different types of milling operations. Therefore, the choice of milling tool depends on the type of operation, i.e., are you performing straddle milling, face milling, corner milling, etc.
Also, different materials require different cutting tools. For example, machining titanium uses rigid tools, while machining copper requires tools with fewer flutes.
13) Control Panel
The control panel is one of the main parts of a CNC machine. It provides a way for the operator to interact with the CNC machine and control its functions.
The control panel consists of input devices, display units, keyboards, and other control switches and buttons. It allows the operator to issue commands, select functions, and monitor operations.
2.Tools Used in CNC Milling Machines
CNC milling cutters remove material from a workpiece with a rotary motion. They are available in a variety of different designs, each suitable for a specific application.
The choice of milling cutter depends on the type of machining operation to be performed. For example, face milling cutters are used in face milling operations to machine flat surfaces. Similarly, end mills are ideal when machining holes and slots in a workpiece. When creating complex geometries, especially in tight spaces, ball-end milling cutters are the go-to solution.
Other factors to consider when selecting a milling cutter include the workpiece material, desired surface finish, cutting speed, and material removal per revolution.
CNC milling cutters are available in a variety of grades, each with their own advantages and disadvantages. For example, carbon steel cutters are relatively inexpensive but are only suitable for slow-speed operations.
Conversely, high-speed steel (HSS) cutters are more efficient in high-speed operations and can cut harder materials. Carbide milling cutters are designed to handle the toughest projects and provide a high-quality surface finish.
Choosing the right tool for your milling operation is critical to the performance and quality of your machined parts.
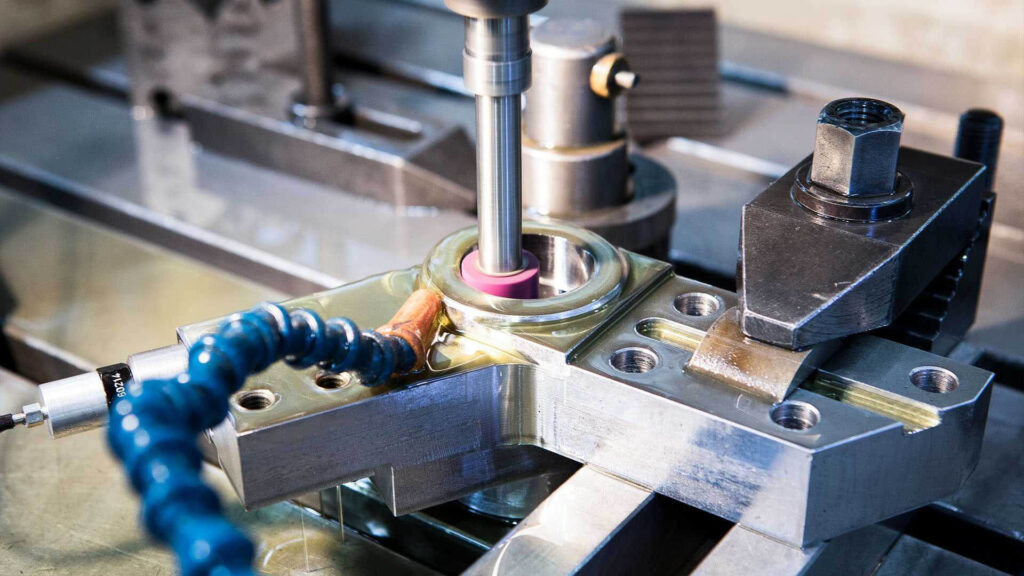
3.How does a CNC machine work?
Now that you’re familiar with the standard parts of a CNC mill, you may be curious about how this CNC machine works.
So, how exactly does a CNC machine work? In this section, I’ll dive into the fundamental principles and basic mechanics of a CNC machine.
With CNC machining, operators use CAD models to generate custom parts. Here’s how it works.
- The operator converts the CAD model into a set of instructions called G-code. Using input devices, this data is fed into the machine control unit (MCU).
- The raw material or workpiece is fixed on a workbench. The workpiece can be clamped in a vise or mounted directly on the machine bed. To produce high-precision parts, the workpiece needs to be correctly positioned and aligned.
- The machine control unit interprets the G-code and transmits the relevant instructions to the drive system. The drive system includes motors, such as servo motors, that move the tool along the different machine axes.
- The machine tool removes material from the workpiece to form the desired part. Usually, the machine tools first remove material quickly with low precision to create an approximate geometry. Then, they perform several high-precision operations to produce the desired part.
- The feedback system monitors the position and speed of the machine tool and transmits feedback signals to the machine control unit. If errors occur, the MCU transmits new signals to make the necessary adjustments.
- After the machining activity is completed, critical dimensions may need to be verified if tolerances have been provided. The part is then ready for use or post-processing.
In most cases, CNC milling machines move along three linear axes: X, Y, and Z. Advanced systems will have rotary axes in addition to linear motion. 5-axis CNC machines can easily manufacture complex geometries.
4.Factors that Affect the Cost of CNC Milling Machines
There are different types of CNC milling machines on the market, with varying levels of complexity and capabilities. These differences result in varying prices for milling machines. In this section, I will explore some of the factors that determine the cost of a CNC milling machine.
1) Table Size
The cost of a CNC milling machine varies with the table size, and the larger the table, the more you will have to pay. However, larger tables can accommodate larger workpieces.
If you are shopping for a CNC milling machine, consider your machining needs and choose the table size that best meets your requirements.
2) Spindle Power
Spindle power directly affects the milling capabilities of the machine. However, more powerful spindles require a larger financial investment. The type of material being machined determines the spindle power required. For example, machining a steel workpiece requires more spindle power than machining a softer material such as plastic.
In addition, tool size also plays a role in determining the appropriate spindle power. The larger the tool size, the more spindle power is required.
3) Frame Rigidity
Another key factor that affects the cost of a CNC mill is the rigidity of the frame. The rigidity of a CNC mill frame depends on the material it is made of. A rigid frame reduces vibrations during cutting, which is beneficial for machining quality parts with better surface finish.
Since most CNC mills are used to machine metal parts, they usually require a rigid metal frame. Steel is usually used for CNC mill frames. Stronger materials provide better frame rigidity and improve the performance of the mill. However, such mills are usually more expensive.
5.Conclusion
That’s it! In this article, I introduced standard CNC mill parts, common tools for the machine, factors that affect CNC milling costs, and how CNC machining works. I hope you have mastered the basics of this important manufacturing process.