Precautions for CNC milling thin-walled parts processing
In the field of CNC machining, the processing technology of thin-walled parts has attracted much attention. As an advanced CNC machining technology, thin-wall machining mainly performs precise cutting and shaping on thin and delicate materials. Usually, the material thickness of thin-walled parts is often less than 2 mm. Due to its delicate nature and easy deformation and warping, it is extremely difficult to process. Therefore, in-depth research on the CNC machining process of thin-walled parts is very important.
This blog will introduce in detail the matters that need special attention during the processing of thin-walled parts.
1.Current status and problems of thin-walled parts
Thin-walled parts have complex internal structures, which can easily cause various problems during CNC milling. Thin-walled parts also have complex structures and low rigidity, and are very easy to deform during processing, resulting in uneven thin-wall thickness and inappropriate size. In order to ensure processing accuracy, fine machining and multiple light cutting methods without feed are usually used. Although this can improve the quality of parts, it also increases consumption, wastes time, and reduces productivity.
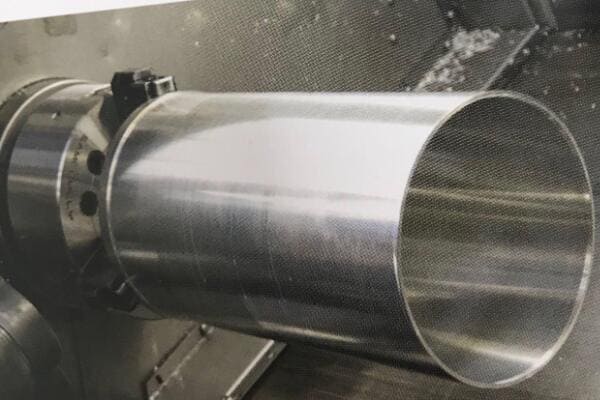
2.Factors affecting the deformation of thin-walled parts
1.Cutting force and cutting heat
Thin-walled parts have poor rigidity, and the deformation caused by milling force is difficult to predict. Chip deformation causes thermal stress on the surface of the part, which will further aggravate the deformation of the part under the combined action of cutting force and cutting heat.
2.Workpiece material characteristics
Most thin-walled parts are made of aluminum alloy, titanium alloy, etc. These materials have small elastic modulus and high specific strength, and are prone to rebound deformation.
3.Clamping conditions
The clamping force of the fixture will cause elastic deformation of thin-walled parts, thereby affecting the surface shape and dimensional accuracy. The interaction between cutting force and clamping force will cause more serious deformation of parts.
4.Residual stress
Includes initial residual stress and processing residual stress. Cutting force and cutting heat break the balance of initial residual stress, and workpiece deformation makes the internal stress balanced again.
5.Tool path
Different tool paths will cause different release orders of residual stress, resulting in different processing deformations. The combined action of multiple factors will affect the deformation of the workpiece.
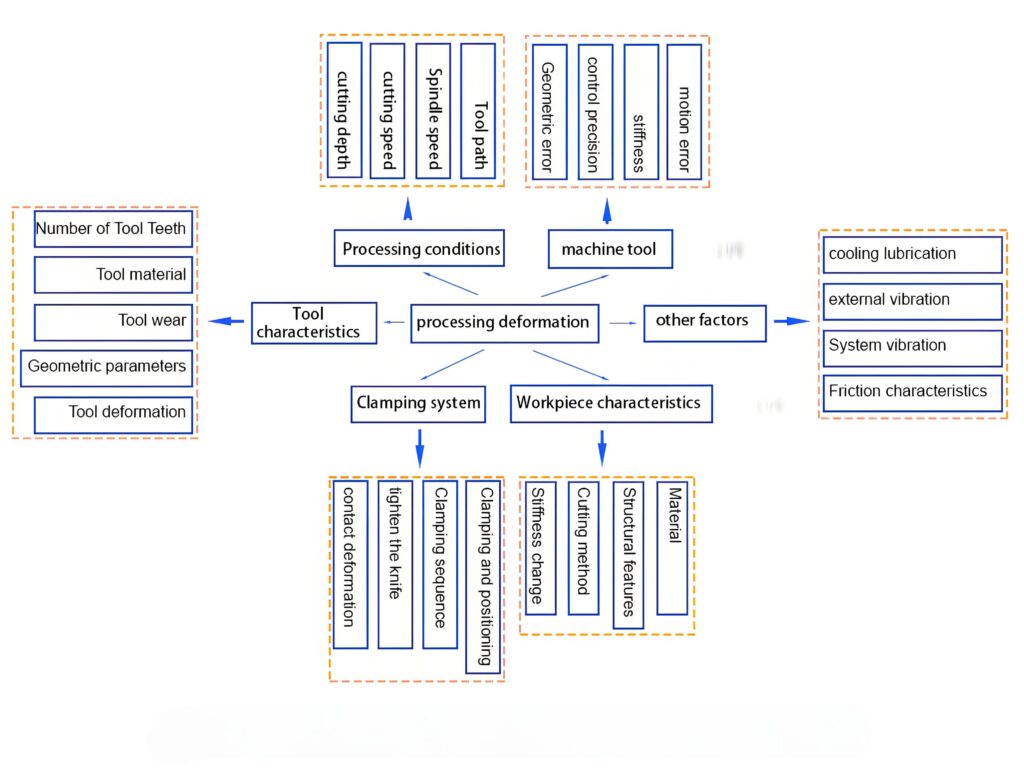
3.Methods to improve the machining accuracy of thin-walled parts
1.Processing using the overall rigidity of the part
During the cutting process, use the unprocessed part of the part as support as much as possible to keep the cutting in a good rigidity state and reduce cutting deformation and vibration.
2.Use auxiliary brackets
You can add tires to the cavity or use filling methods and other process methods to strengthen the support, increase the rigidity of the part, and suppress deformation.
3.Design strengthening ribs to improve rigidity
For thin-walled parts, adding process ribs is one of the common methods to improve rigidity.
4.Symmetrical layered milling
Release the initial residual stress of the blank symmetrically, and use the principle of equal removal of the upper and lower edges to process in sequence to reduce processing deformation.
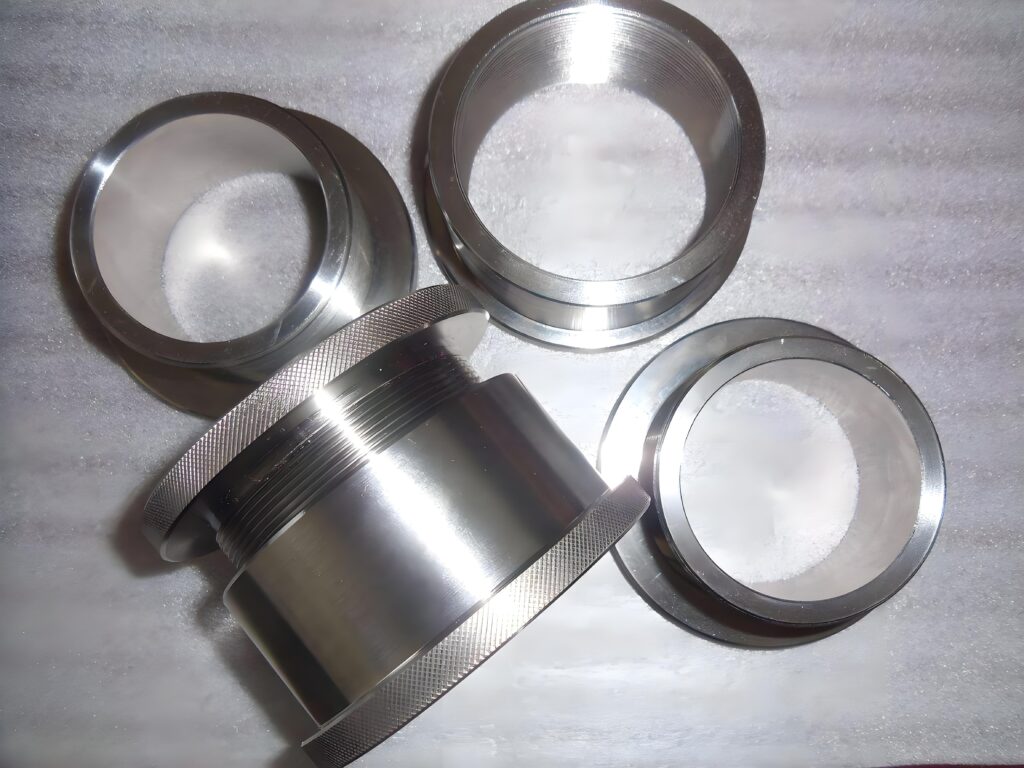
5.Optimize tool cutting methods
Tool cutting methods have a direct impact on part processing deformation, and appropriate cutting methods need to be selected.
6.Use CNC high-speed machining
Control deformation, use the “small cutting depth, fast cutting” method to reduce cutting force, quickly take away cutting heat, and eliminate deformation caused by processing.
7.Heat treatment to remove stress
Stress relief treatment is performed after rough machining, and multiple stress relief is performed for high-precision parts with severe deformation.
8.Reasonable selection of workpiece positioning and clamping methods
Reduce the influence of clamping force on deformation.
5.At last
Thin-walled parts are widely used in key fields such as aerospace. Due to their special usage scenarios, they have extremely high requirements for precision. In-depth research and optimization of the cutting process of thin-walled parts have great theoretical significance and practical value.
If you are looking for an experienced CNC processing manufacturer, Xavier is undoubtedly your best choice. The Xavier team has sophisticated equipment and can provide you with high-quality CNC processing solutions to fully meet your personalized processing needs. If you need more information or to discuss your processing needs with us, please feel free to contact us.