How to improve CNC precision? From entry to mastery
As one of the core technologies of modern manufacturing, the precision of CNC technology directly affects the quality and performance of products.
With the rapid development of Industry 4.0 and intelligent manufacturing, the requirements for CNC precision are getting higher and higher. This article will give you a comprehensive understanding of CNC precision from six aspects: basic knowledge, CNC precision definition and indicators, factors affecting precision, error types, precision improvement and application cases.
1.Basic knowledge of CNC precision
(1) Overview of CNC machine tools
CNC machine tools are automated machine tools equipped with program control systems that can automatically complete the processing of parts according to pre-programmed programs. Compared with traditional machine tools, CNC machine tools have the advantages of high processing precision, high production efficiency and high degree of automation.
(2) Principle of CNC system
The CNC system is the core part of the CNC machine tool, which is responsible for receiving, processing and outputting control signals, and controlling the motion trajectory and speed of each moving part of the machine tool. The CNC system is mainly composed of an input device, a CNC device, a servo drive device, a detection feedback device and a machine tool body.
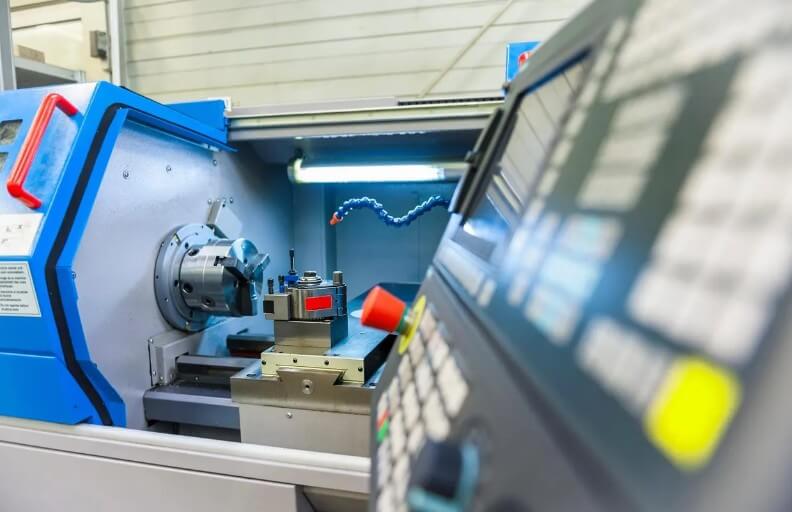
(3) Basics of CNC Programming
CNC programming refers to the process of writing CNC machining programs based on part drawings and machining process requirements. CNC programs consist of a series of instruction codes that are used to control the machine tool’s motion trajectory, speed, spindle speed and other parameters.
2.Definition and indicators of CNC precision
CNC precision refers to the degree of closeness between the actual size, shape and position of the parts processed by the CNC machine tool during the machining process and the ideal value. Commonly used CNC precision indicators include:
(1) Positioning accuracy:
The deviation between the actual arrival position and the target position when the machine tool moving part moves from one position to another.
(2) Repeated positioning accuracy:
The maximum deviation between the actual arrival positions when the machine tool moving part repeatedly positions to the same position.
(3) Machining accuracy:
The degree to which the size, shape and position of the parts processed by the machine tool conform to the requirements of the drawing.
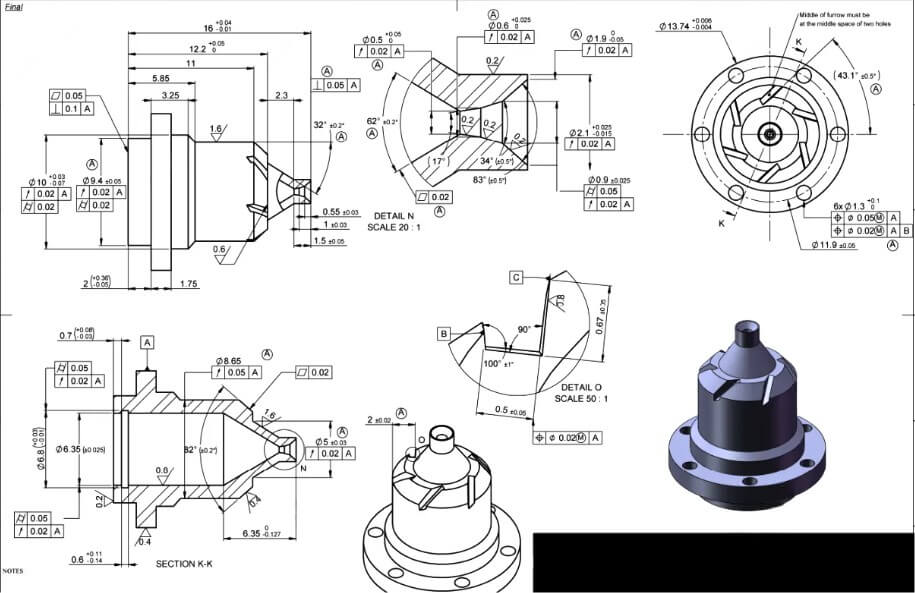
3.Main factors affecting CNC precision
(1) The precision of the machine tool itself
The precision of the machine tool itself is the basis for determining CNC precision, including the following aspects:
Guide rail precision: The straightness and parallelism of the guide rail determine the motion precision.
Spindle precision: The rotation precision, coaxiality and thermal stability of the spindle directly affect the processing precision.
Machine tool rigidity: Insufficient machine tool rigidity will cause vibration and deformation during cutting, affecting precision.
(2) Tools and process parameters
Tool wear: The tool will gradually wear during the processing, resulting in dimensional deviation.
Cutting force: Excessive cutting force will cause workpiece deformation and affect processing precision.
Cutting speed and feed rate: Improper parameter selection will affect surface quality and dimensional accuracy.
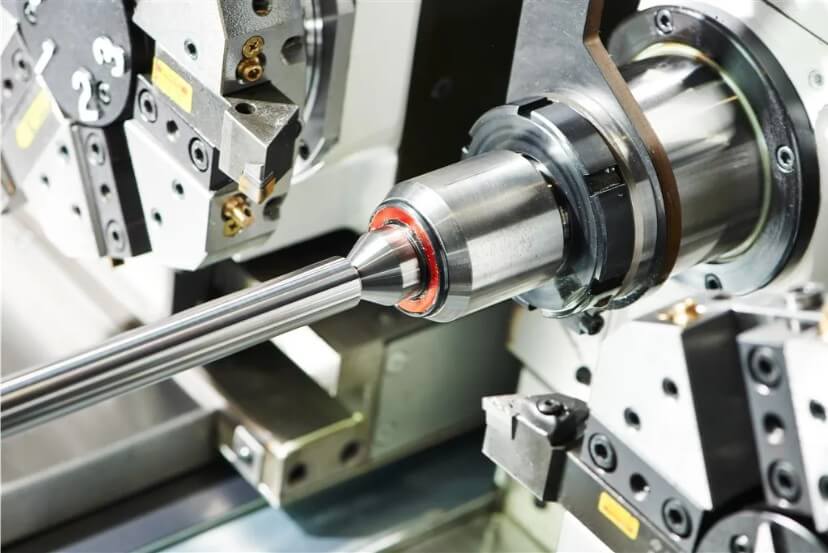
(3) Servo system and control precision
Interpolation algorithm: High-precision interpolation algorithm can reduce trajectory error and improve CNC precision.
Servo error: The control accuracy of the servo motor determines the motion error.
Feedback system: High-precision grating ruler, encoder and other feedback devices can improve position accuracy.
(4) Fixture and workpiece positioning error
Fixture accuracy: Fixture positioning error will directly affect the dimensional accuracy of workpiece processing.
Clamping method: Uneven clamping force or repeated clamping error will lead to dimensional deviation.
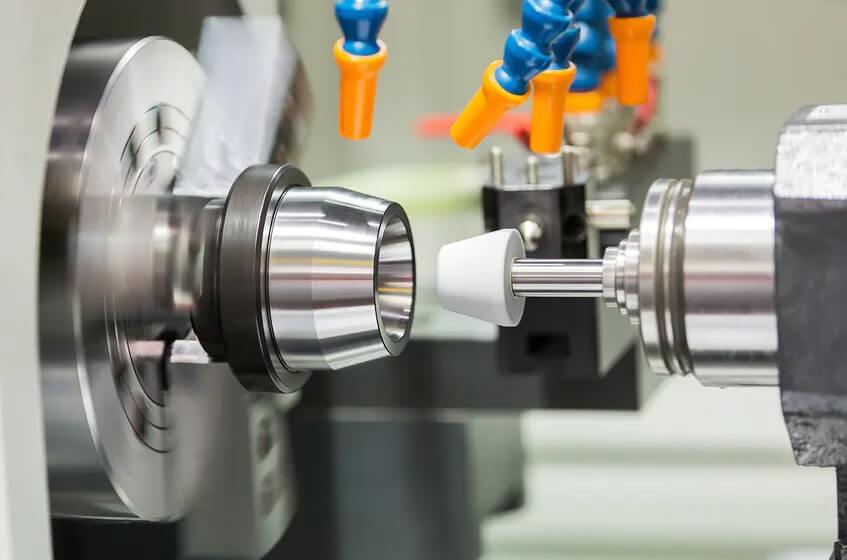
(5) Environmental factors
Temperature change: Temperature change will cause thermal expansion of the machine tool structure, thereby affecting the processing accuracy.
Vibration interference: Ground vibration, external noise, etc. will cause machine tool vibration, affecting the processing quality.
4.Main error types of CNC machine tools
(1) Geometric error
Machine tools have geometric errors during the manufacturing and assembly process, such as:
Straightness error of machine tool guide rails
Spindle rotation error
Machine tool assembly deviation
(2) Servo error
Servo system response lag or improper adjustment will cause:
Position error
Speed fluctuation error
Feed system lag
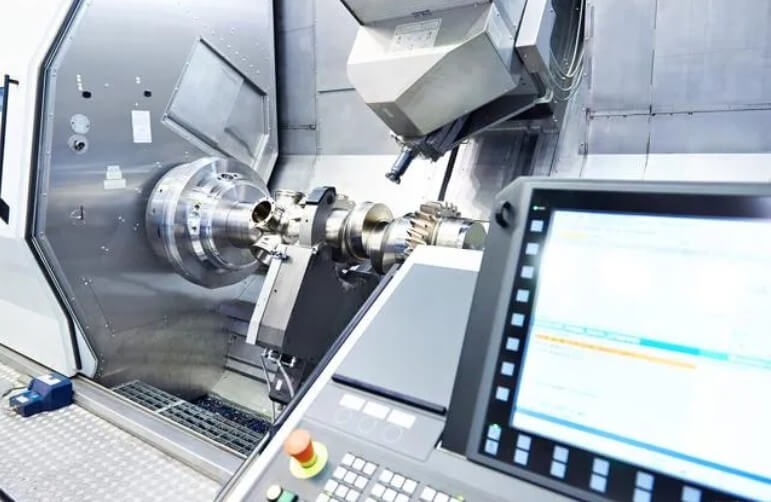
(3) Thermal error
During the operation of the machine tool, heat will cause parts to expand, resulting in processing errors. For example:
Thermal expansion caused by long-term operation of the spindle
Deformation of the machine tool bed affected by ambient temperature
(4) Reverse clearance error
Due to problems such as gear clearance and screw nut matching, the feed system will have errors during reversing.
5.Optimization methods to improve CNC precision
(1) Machine tool selection and maintenance
Select a suitable machine tool: According to the accuracy requirements of the machined parts, select a CNC machine tool with a suitable accuracy level.
Regular maintenance: Regularly cleaning, lubricating, adjusting and other maintenance work on the machine tool can effectively extend the service life of the machine tool and maintain the machine tool accuracy.
(2) Error compensation technology
Error compensation is an important means to improve CNC accuracy, including:
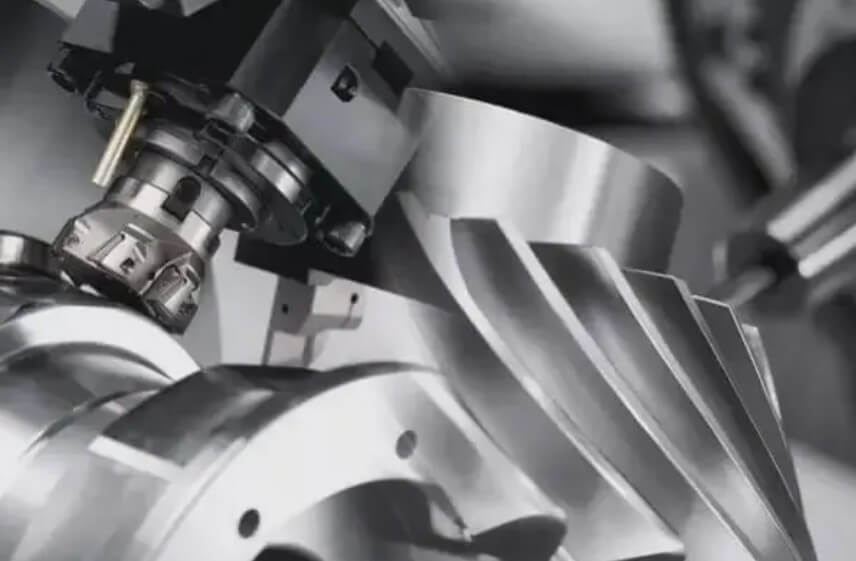
Thermal error compensation: Monitor the thermal deformation of the machine tool through a temperature sensor and perform real-time compensation.
Reverse clearance compensation: Compensate the feed amount during reversing to reduce the impact of clearance.
Geometric error compensation: Use high-precision measurement tools such as laser interferometers to compensate for errors.
(3) High-precision measurement and feedback system
Laser interferometer: used to measure machine tool geometric errors and make corrections.
Grating ruler: high-precision displacement measurement device to improve positioning accuracy.
Online detection system: through real-time measurement of workpiece errors, dynamic adjustment can be made.
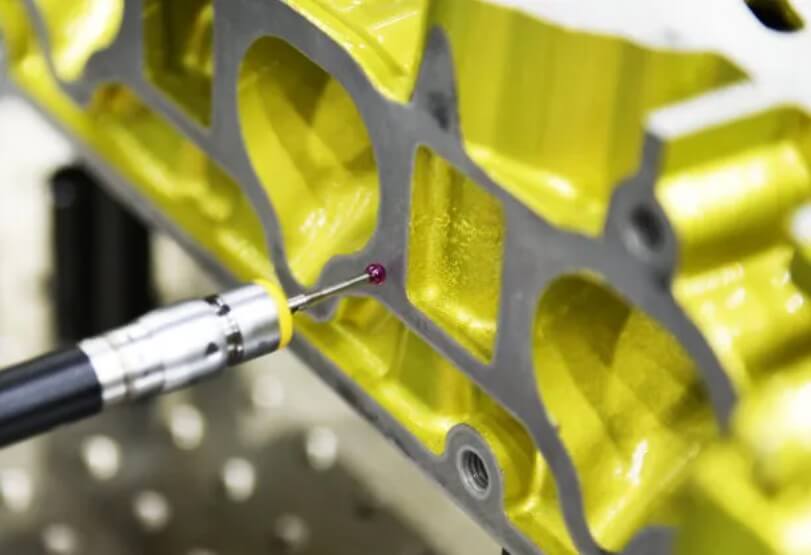
(4) Select appropriate processing parameters and optimize process paths
Optimize feed speed: Reasonable setting of feed speed can reduce vibration and improve surface quality.
Reduce the number of tool changes: try to use the same tool to process multiple features to reduce tool change errors.
Optimize processing sequence: try to perform rough processing first, then fine processing to reduce the impact of workpiece deformation.
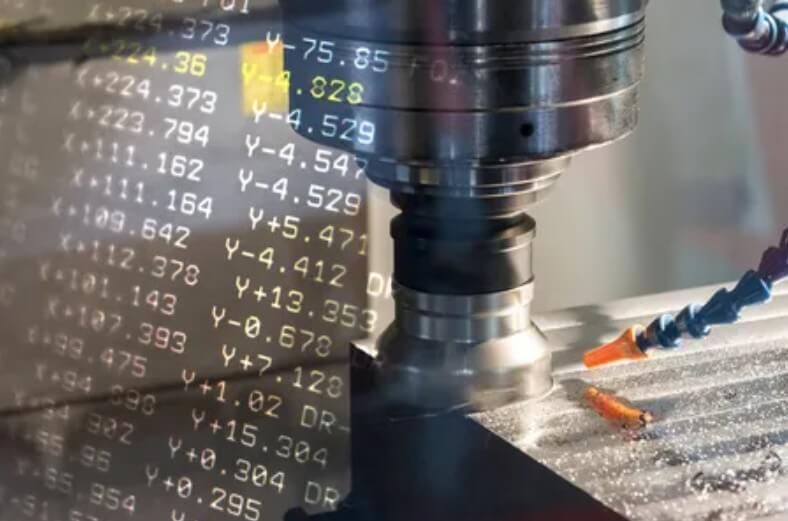
6.Application cases
(1) High-precision parts processing cases
Aerospace field: aircraft engine blades, rocket engine nozzles and other parts have extremely high precision requirements and need to be processed by high-precision CNC machine tools.
Medical device field: artificial joints, heart stents and other medical devices have extremely high precision and surface quality requirements and need to be processed by high-precision CNC machine tools.
(2) Application of CNC precision in intelligent manufacturing
Adaptive processing: By real-time monitoring of various parameters in the processing process, the processing parameters are automatically adjusted to ensure processing accuracy.
Online detection: During the processing process, the processed parts are detected in real time to detect and correct errors in time.
Intelligent compensation: According to the detection results, the machine tool errors are automatically compensated to improve the processing accuracy.
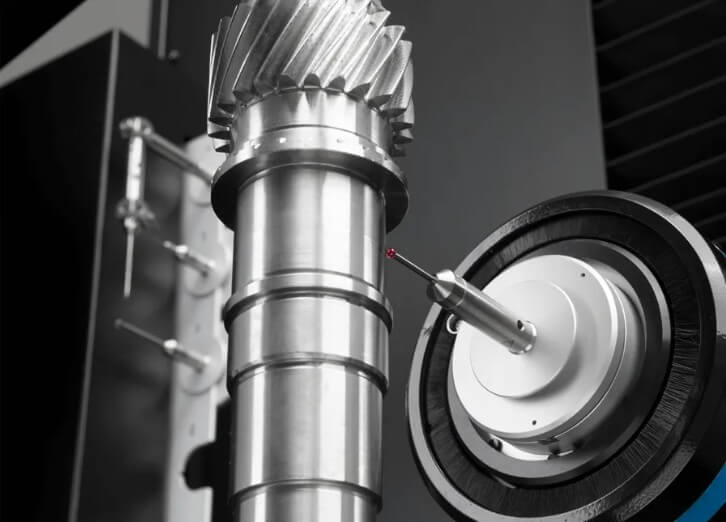
7.Conclusion and Prospect
(1) Conclusion
The processing accuracy of CNC machine tools is affected by many factors, including the structural accuracy of the machine tool itself, the tool status, the servo system, environmental factors, etc. By adopting error compensation technology, high-precision measurement system, advanced control algorithm and optimizing process path, the CNC accuracy can be effectively improved.
(2) Prospect
In the future, with the development of artificial intelligence, big data and Internet of Things technology, CNC machine tools will develop in the direction of intelligence and automation, further improving processing accuracy and production efficiency. For example:
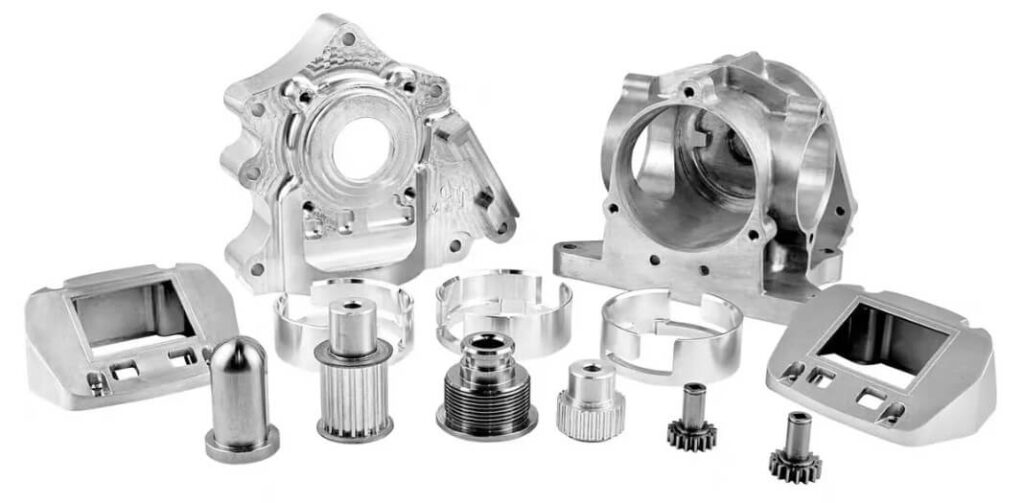
1) Adopt AI-driven intelligent error compensation system to improve real-time adjustment capabilities.
2) Realize remote monitoring and accurate diagnosis through industrial Internet technology.
3) Develop ultra-high precision processing technology to meet more precise manufacturing needs.
In summary, improving CNC precision requires not only advanced equipment, but also reasonable optimization strategies and intelligent control technologies.
Xavier has been committed to the field of CNC machining for many years, providing high-quality CNC machining services to many customers. Our production services can help you achieve the strictest tolerances required for non-standard custom CNC machining parts. If you need, please feel free to contact us!