CNC Precision Machining: Best Tolerances, Equipment, and Applications
Every industry pursues high-quality machining. Generally, CNC machining processes are precise and highly complex. The demand for CNC precision machining is growing, so we have compiled this guide to explain CNC precision machining in detail so that you don’t have to go anywhere else.
1.What is CNC precision machining?
CNC precision machining is a production process in which a blank or workpiece is turned into a finished product through subtractive machining using a machine tool controlled by a CNC machine and guided by a computer-aided design of the desired shape. Subtractive machining here refers to the removal of material from the workpiece.
CNC precision machining relies on computer-aided design (CAD) for product design and computer-aided manufacturing (CAM) to turn parts into machinable processes and issue instructions to the CNC equipment. Despite the automation of manufacturing instructions, CNC machining still requires skilled machinists at some stage.
CNC precision machining is popular because it can produce standardized parts that are almost identical, with little deviation from the required diameter, length, and size. Precision machining services are utilized by automotive companies, the defense industry that manufactures aerospace vehicles and landing gear ports, and for developing prototypes and custom CNC machined parts.
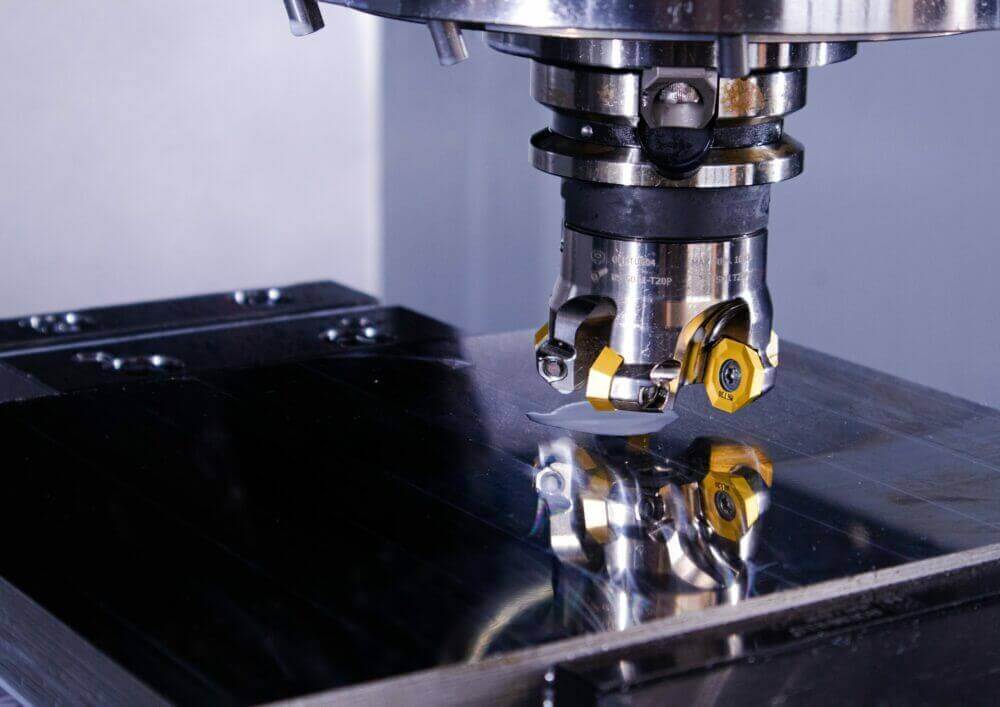
2.Tolerances of CNC Precision Machining
CNC precision machining tolerances define the CNC technology that is best suited to machining a part. CNC precision machining equipment can achieve extremely tight tolerances up to 0.0025 mm. However, CNC machining of this tolerance is expensive, time-consuming, and often unnecessary.
Most CNC precision machining services offer tolerances of ± 0.051 mm to ± 0.005 mm. CNC precision machining processes are able to maintain this tolerance, or achieve closer tolerances for tiny parts depending on the desired shape and raw material.
There is no specific tolerance for precision machining processes, the variations come from the type of manufacturing process, CNC machine tool, and tolerance measurement system.
The most common tolerance measurement systems for machined parts are:
- Single-sided tolerance: The tolerance is specified for only one side of the dimension. This means that one side can exceed the nominal size, but the other side remains within the exact tolerance.
- Bilateral Tolerance: This is the most common tolerance, and you will see a value with a ± sign. The dimension can deviate on both sides.
- Limit Tolerance: The limit tolerance specifies the range of values that a dimension can take. Usually between two numbers, the accuracy is defined by the decimal places.
3.Common Types of CNC Precision Machining Equipment
CNC precision machining is not a new process, but not all machines can do it. The most common precision machining equipment relies on CAM software to control computer numerical control (CNC) machines.
Although these machines are capable of completing most processes, some tasks are better done with certain machines from a cost minimization and productivity perspective.
1) CNC Milling Machines
CNC milling machines have a spindle that holds a cylindrical tool that moves along the axis of the machine. CNC milling machines have a variety of cutting tools with multiple teeth. CNC milling machines are used to machine rectangular blanks and can be used for a variety of operations from drilling holes to carving slots. They are also used to shape surface features and match common tolerances prior to surface finishing processes.
Milling machines are generally used to machine flat surfaces. CNC milling machines can do face milling or perimeter milling. Perimeter milling features are cut by placing the tool parallel to the workpiece.
2) CNC Lathes and Turning Machines
CNC lathes are able to shape cylindrical blanks by rotating the part at high speed and driving it on a predetermined axis. The tool remains stationary and the chuck rotates.
Another type of CNC lathe is the Swiss-type lathe. A relatively modern type of CNC machine tool, the CNC Swiss-type lathe uses a sliding headstock and guide bushings to support long cylindrical parts. In addition to this, Swiss-type lathes also have milling capabilities.
CNC lathes are specialized to provide some standard turning operations such as reaming, drilling, balling, pinning, grooving or tapping and taper. Keep in mind that CNC lathes are strictly used to produce machined parts from cylindrical parts.
3) CNC Drilling Machines
Drilling holes does not usually require high precision, and most vertical drill presses are manually operated. However, when producing holes with close tolerances and uniform size, it is important to have an automated CNC machine. In addition to cylindrical holes of the required diameter, CNC drilling also includes broaching, drilling, screw machine drilling, and collet reamer.
These holes are usually drilled for screws, automotive parts, and plastic components. For example, the speaker holes in the metal chassis of mobile phones are drilled by precision CNC drilling machines.
4) Electrical Discharge Machines (EDM)
EDM machines remove metal by continuously generating sparks and generating heat on the metal. The process is called spark machining, and it works by applying a direct current to an electrode and the metal part below, forming an electric field.
Tiny metal parts suspended in the electrode are formed at the center of this field, and because they are conductive, these tiny metal impurities heat up, and the plasma burns the material and removes the metal.EDM uses metal wire or sinker dies. Wire EDM uses the principle of burning away material with an electrode wire, while sinker die EDM uses an electrode that is a positive image of the desired cavity.
4.Why are CNC machines so precise?
Precision refers to consistency and repeatability. Expanding this definition to CNC precision machining work, we can say that the precision of a CNC machine refers to the variation in similarity of the parts produced. Remember, for most CNCs, this variation is less than 0.1 mm.
This means that if you were to take two parts made by the same CNC machine, there would likely be a 0.1 mm difference in some dimensions. For precision CNC machines, this difference is even smaller, and the parts can be assumed to be identical.
The reason CNC machines are so precise is that they are primarily operated by digital code. The instructions direct the machine to move x mm vertically, x mm horizontally, and rotate the cutting tool at a certain speed. With guidance like this, it is difficult to make mistakes.
In addition to this, the movement on the axes is measured in real time by linear encoders. In addition, there are built-in calibrators to account for any mechanical deviations and calibrate the machine. In addition, for extreme tolerance situations, temperature and humidity levels are controlled to achieve optimal performance.
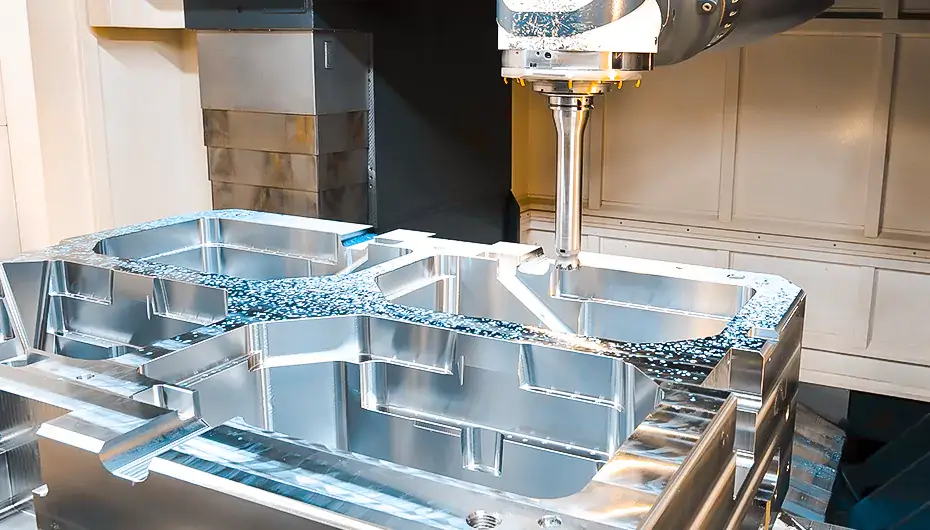
5.Applications of CNC Precision Machining
1) Aerospace
CNC precision machining is widely used in the aerospace industry to manufacture critical components with high precision and small tolerances. It is used to produce engine components, turbine blades, landing gear components, structural components, etc.
2) Automotive
CNC precision machining plays a vital role in the automotive industry and is used to manufacture engine components, transmission components, suspension systems, brake components, and other critical components. It ensures high accuracy and repeatability, thereby improving the performance and reliability of automotive systems.
4) Medical Devices
CNC precision machining produces complex components for medical devices such as surgical instruments, implants, prostheses, orthopedic devices, dental components, and diagnostic equipment. Its high accuracy ensures the safety and functionality of these devices.
5) Electronics
CNC precision machining involves the production of electronic components such as connectors, housings, heat sinks, and PCBs (printed circuit boards). CNC machines are able to create precise features, complex patterns, and fine details required by the electronics industry.
6) Defense and Military
CNC precision machining is essential for manufacturing components used in defense and military applications. It is used to produce firearms, weapon systems, optical equipment, armored vehicle components, and other defense-related equipment that requires high precision, reliability, and durability.
7) Industrial Equipment
CNC precision machining is widely used in the production of a wide range of industrial equipment, including pumps, valves, gears, bearings, shafts, and machine tool components. CNC machines are able to manufacture complex geometries, ensuring that industrial machinery operates efficiently and reliably.
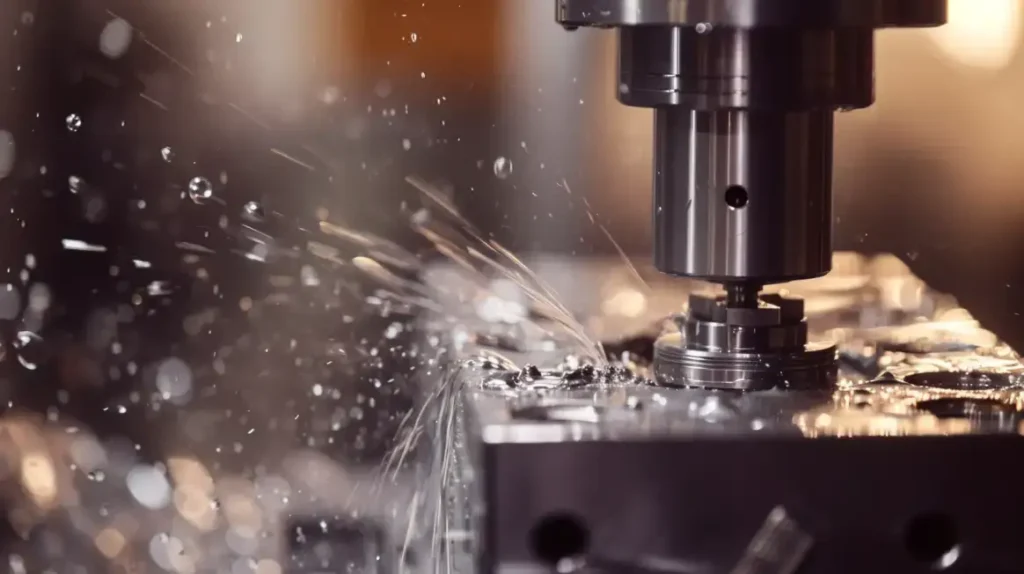
6.Advantages of CNC Precision Machining Services
1) Better Quality
The most obvious advantage of CNC precision machining is the improvement in product quality. CNC precision machines can replicate parts that appear identical to the naked eye with minor deviations. In addition to this, the surface finish is also much better than standard machined parts.
2) Tighter Tolerances
Unparalleled tolerances can be achieved through CNC precision machining. CNC precision machining operations can achieve tolerances of ± 0.00254 mm. This makes precision CNC an ideal choice for applications where assembly issues may occur.
Tighter tolerances also ensure that all parts produced will fit in assembly and will not be rejected by quality control. High precision produces identical parts.
3) Faster Production
CNC can easily process a wide range of materials, from wood to plastic and metal. Once the instructions are loaded into the CNC machine, the process is automated and labor-intensive. Faster turnaround time speeds up production and reduces costs.
4) Easy Prototyping
Most prototypes start out in a wood shop or are made from plastic. Injection molding provides a prototype solution for complex shapes, but it is costly and time-consuming.
CNC precision machining can easily form complex geometries and quickly improve designs by changing the G-code. Computer numerical control machines can process a wide range of materials at a faster rate.
5) Reliable
CNC precision machining parts rarely have quality control issues because the entire process is automated. CAD and CAM ensure that the dimensions, processes, and order of machining are correct. There are no human errors or manual processes, which increases the reliability of CNC precision machining.
7.Best Practices for CNC Precision Machining
1) Material Selection
Precision CNC machine shops use a variety of materials to produce high-precision and high-quality machine parts. The choice of material depends on the specific requirements of the part, including its function, required characteristics, and environmental considerations.
① Commonly used metals in CNC precision machining
- Aluminum (5052, 6061, 6061-T651, 7075, etc.)
- Stainless steel (201, 301, 304, 316, 410, 420, etc.)
- Steel (1008, 1020, 1045, etc.)
- Copper
- Brass
- Bronze
- Titanium
- Rare metal alloys
② Commonly used plastics in CNC precision machining
- Anti-lock brake system
- Polymethyl methacrylate
- Personal computer
- Polyoxymethylene
- PA (Nylon)
2) Programming
Programming a CNC machine tool includes determining the type of machining, sequencing tasks, adjusting parameters such as feed speed and tool number, and using CAM software to convert information into digital code (G code or M code).
3) Machining
The sequence of operations is also part of the process phase, but many times parts are transferred between CNC machines for specialized machining. These processes can be precision drilling or precision milling after a CNC turning operation.
4) Surface Treatment
Surface treatment is an essential step in the manufacturing process to ensure that the part meets the required texture, finish, and accuracy.
CNC milling can achieve tight tolerance material removal, but surface finishing processes such as grinding and lapping are often used to enhance the polish and achieve the desired surface characteristics.
Coatings such as chromate coating, anodizing, powder coating, and painting are forms of surface treatment used to improve the aesthetics and functionality of the part.
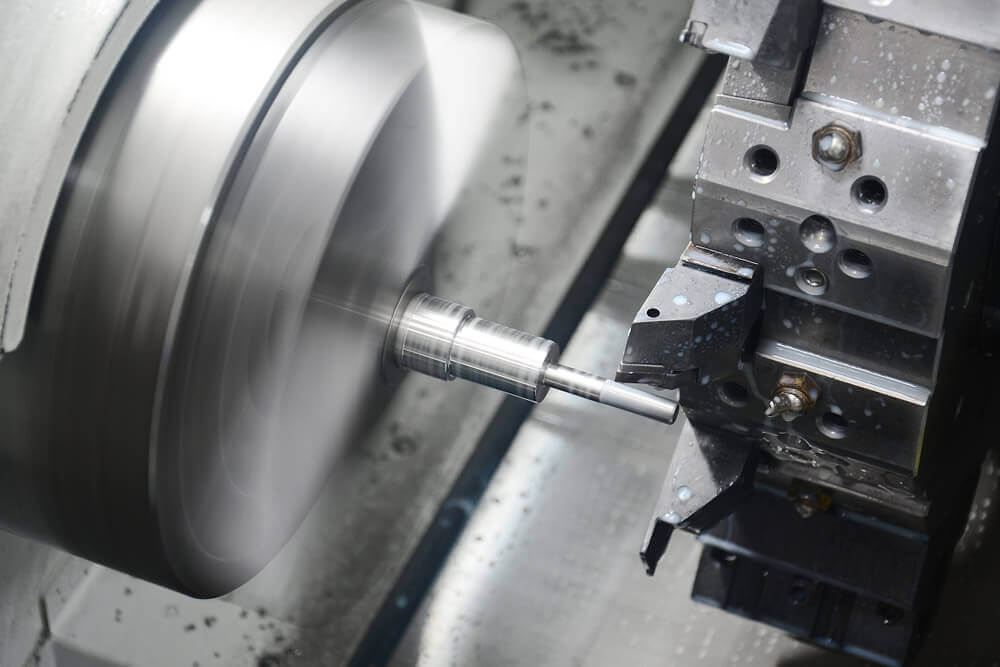
8.CNC Precision Machining Service Tips
When machining metal or plastic parts on the CNC, it is important to maximize the life of the part. This means not only choosing the right material, but also using tested methods and making the design as easy to machine as possible.
1) Simplify your design
Try to design features that are easy to machine and capable of performing the required tasks. For example, avoid using angled sides if you can use straight edges, and avoid placing holes close to each other. Many design adjustments can be made before machining.
2) Avoid Tight Tolerances
While CNC machines can produce products with very tight tolerances, the parts available to you may already be standardized. For example, you can design a camshaft to your specifications and uneven tolerances, but finding the purpose of that shaft in the engine block may be difficult.
3) Filleting
Avoid sharp edges. Inside or outside edges can act as stress concentration points. Add fillet radii to avoid stress concentrations.
4) Threading
There are a range of instructions for making threads, but the most important is to match them to the available bolts. Don’t machine threads for the entire length of the hole, which will complicate machining.
5) Avoid Thin Walls
Depending on your CNC operation, the removal rate may vary. Therefore, you should maintain the minimum wall thickness necessary to avoid stress. In most cases, the wall thickness is 0.8 mm for metal and 1.5 mm for plastic.
6) Design Parts that Can Be Manufactured with a Single Tool
The machining operation can be completed using only one tool. This is ideal because changing tools requires time and manpower, which increases production costs. Designing tools that can complete the process with minimal tool changes should be the standard.
9.Summary
CNC precision machining uses milling machines, lathes, drill presses, and some other precision machines such as EDM to machine the workpiece to the final design. The added advantage of achieving tighter tolerances in any manufacturing process makes it more premium and of a higher quality grade.
They are mainly used in applications that require high precision and small tolerances, from defense systems to casings for watch parts. The process of precision machining is similar to standard CNC, but there is a huge difference in the quality of the final CNC machined part.
If you are looking for an experienced CNC machining manufacturer, Xavier is your ideal choice. The Xavier team is well-equipped to provide high-quality CNC machining solutions. If you need more information or to discuss your machining needs with us, please feel free to contact us.