CNC precision machining parts: advantages, types and design optimization strategies
CNC precision machining parts play an important role in the field of precision manufacturing with precise control systems and automated machining technology. In order to improve machining accuracy and production efficiency, optimizing processes and upgrading technologies have become the key directions for the development of the industry. This article will discuss the advantages, types and design optimization of CNC precision machining parts.
1.What is CNC precision machining?
CNC precision machining is an automated manufacturing technology controlled by computer programs. It uses CNC machine tools to perform high-precision turning, milling, drilling and other machining operations on materials such as metals, plastics, and composite materials to produce parts that meet strict design requirements. Compared with traditional manual or semi-automatic machining methods, CNC precision machining has higher accuracy, consistency and efficiency.
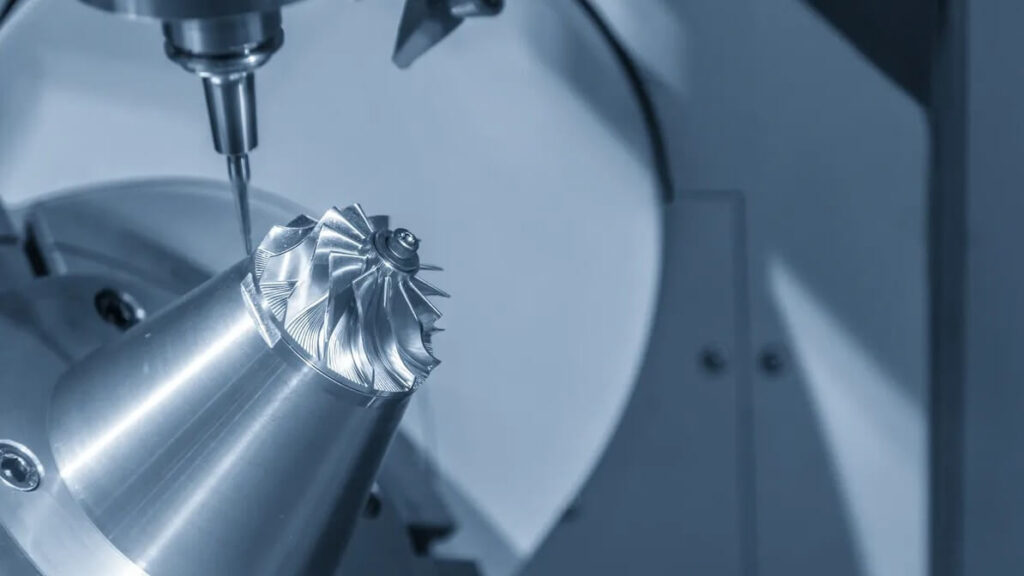
2.Advantages of CNC precision machining parts
The reason why CNC precision machining can occupy an important position in modern manufacturing is mainly due to its significant advantages in accuracy, complex geometric shape processing, efficiency and material diversity.
(1) High accuracy and repeatability
One of the core advantages of CNC precision machining is its extremely high accuracy and repeatability. Through computer program control, CNC machine tools can perform processing tasks with extremely high precision, ensuring that the size, shape and surface roughness of each part meet the design requirements.
1) Accuracy range:
The processing accuracy of CNC machine tools can usually reach ±0.001 mm or even higher.
2) Repeatability:
In mass production, CNC precision machining parts have a high degree of consistency, reducing human errors.
3) Application examples:
In the aerospace field, the processing accuracy of engine turbine blades directly affects the performance and safety of the engine. CNC precision machining parts can meet the high-precision requirements of parts in this field.
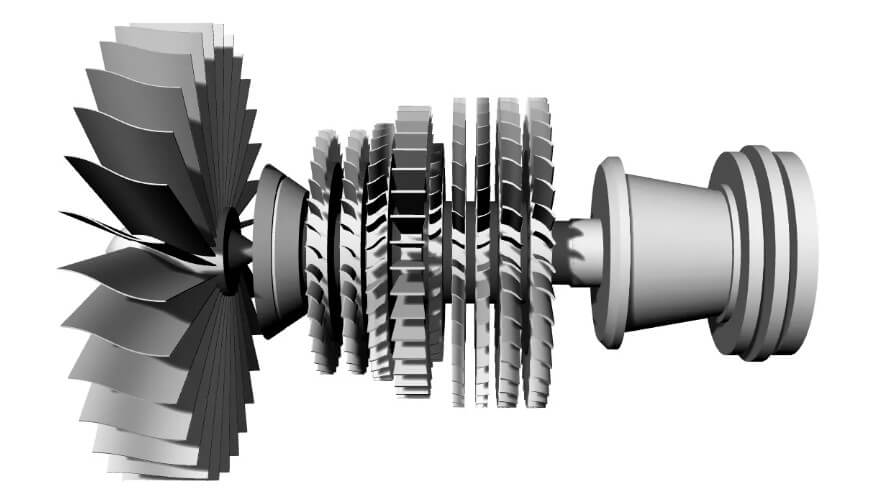
(2) Processing capability of complex geometric shapes
CNC precision machining can easily cope with the processing needs of complex geometric shapes, which is difficult to achieve with traditional processing methods.
1) Multi-axis machining:
Modern CNC machine tools are usually equipped with multi-axis (such as 3-axis, 4-axis, 5-axis) functions, which can process in multiple directions simultaneously, thereby completing the processing of complex shapes.
2) Surface processing:
CNC machine tools can accurately process various surfaces, such as spiral surfaces, spherical surfaces, etc., to meet the design requirements of high-end products.
3) Application examples:
In the field of medical devices, the complex surface design of artificial joints needs to be achieved through CNC precision processing to ensure that they perfectly match the human skeleton.
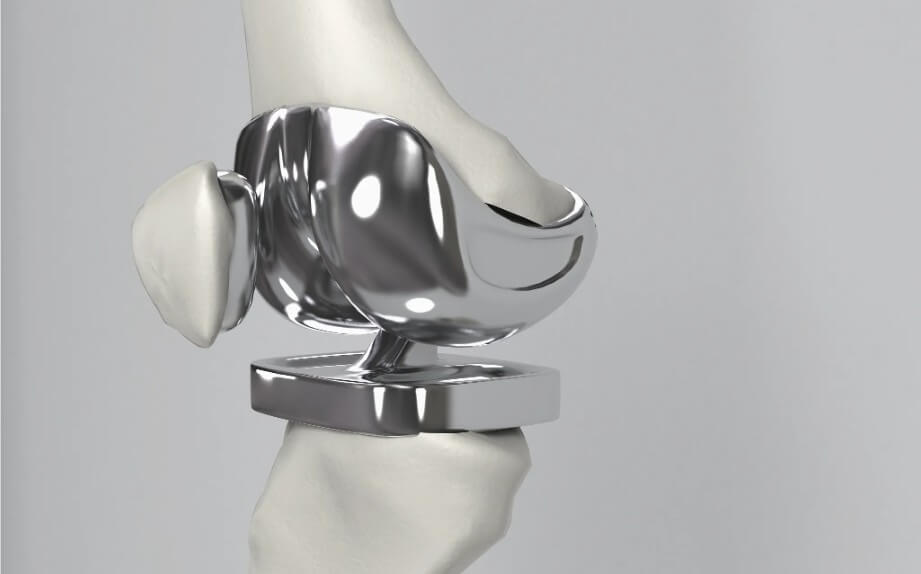
(3) High efficiency and high output
CNC precision processing is not only highly accurate, but also very efficient, and is particularly suitable for mass production.
1) Automated production:
CNC machine tools can work continuously for 24 hours, reducing manual intervention and significantly improving production efficiency.
2) Fast tool change:
Modern CNC machine tools are equipped with automatic tool change systems that can complete tool changes in seconds, reducing downtime.
3) Mass production:
CNC machine tools can quickly replicate the same parts, ensuring consistency and efficiency in mass production.
4) Application examples:
In automobile manufacturing, the processing of engine blocks requires high efficiency and high consistency, and CNC precision processing can meet these requirements.
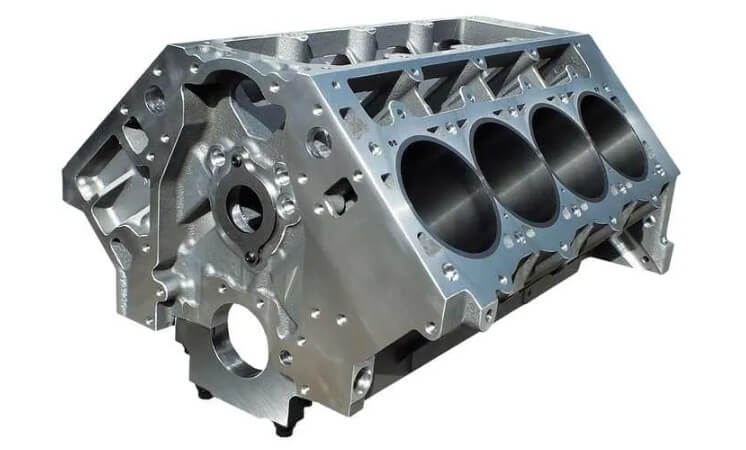
(4) Material diversity
CNC precision machining is suitable for the processing of a variety of materials, including metals, plastics, ceramics and composite materials.
1) Metal materials:
Such as aluminum alloys, stainless steel, titanium alloys, etc., are widely used in aerospace and automobile manufacturing.
2) Plastic materials:
Such as PEEK, nylon, etc., are often used in medical devices and electronic products.
3) Composite materials:
Such as carbon fiber composite materials, used in high-end sports equipment and aerospace fields.
4) Application examples:
In electronic products, CNC precision machining can be used to process aluminum alloy shells and plastic connectors to meet the processing needs of different materials.
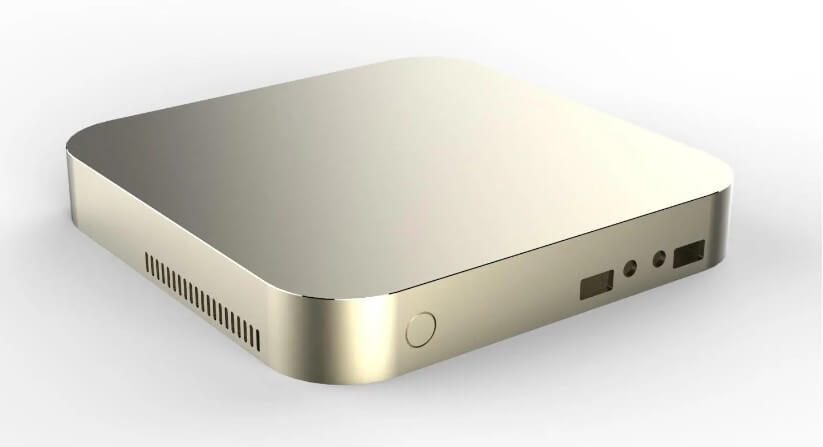
3.Types of CNC precision machining parts
The types of CNC precision machining parts can be classified according to industry, materials and processing technology.
(1) Classification by industry
●Aerospace: engine parts, fuselage structural parts, turbine blades, etc.
●Automobile manufacturing: engine parts, gearbox parts, chassis components, etc.
●Medical devices: surgical instruments, implants, diagnostic equipment, etc.
●Electronic products: precision connectors, heat sinks, housings, etc.
●Energy industry: turbine blades, nuclear reactor components, etc.
(2) Classification by material
●Metal materials: aluminum alloy, stainless steel, titanium alloy, etc.
●Plastic materials: PEEK, nylon, etc.
●Composites: carbon fiber composites, etc.
(3) Classification by processing technology
●Turning: used to process cylindrical parts, such as shaft parts.
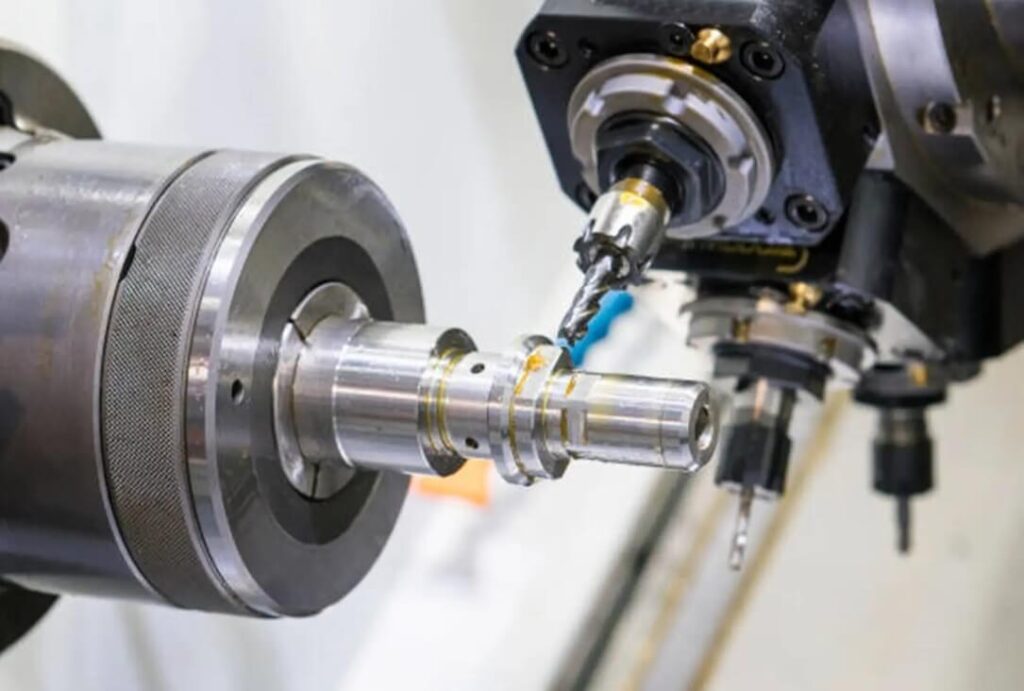
●Milling: used to process flat, curved and complex shaped parts.
●Drilling: used to process hole parts, such as bolt holes, locating holes, etc.
●Grinding: used for surface treatment of high-precision parts to improve surface finish.
4.Design optimization of CNC precision machining parts
(1) Optimize geometry
1) Simplify complex structures
●Reduce unnecessary features:
Avoid designing overly complex geometries, such as deep cavities, narrow slots or tiny holes, to reduce processing difficulty and cost.
●Merge processing steps:
Integrate multiple parts into an integral structure to reduce assembly requirements.
2) Avoid sharp angles and sharp edges
●Rounded corner design:
Add rounded corners to edges and corners to reduce stress concentration and extend tool life.
●Chamfering:
Add chamfers to holes or edges to facilitate assembly and reduce burrs.
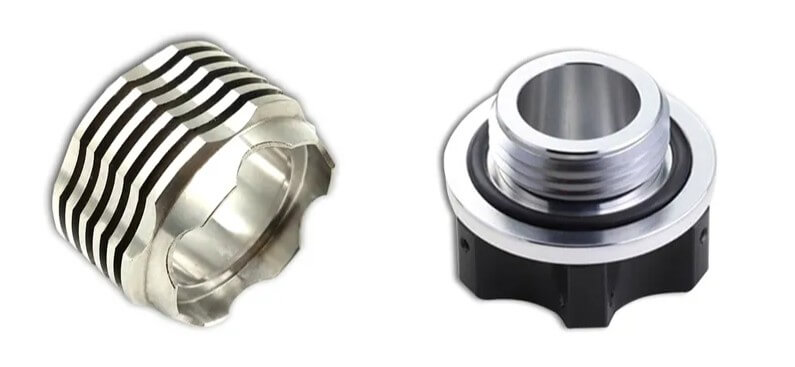
3) Optimize wall thickness
●Uniform wall thickness:
Ensure uniform wall thickness to avoid deformation or processing difficulties due to large differences.
●Minimize wall thickness:
Reduce wall thickness to reduce material cost and processing time while meeting strength requirements.
(2) Reasonable material selection
1) Material machinability
●Select easy-to-process materials:
Preferably select easy-to-cut materials such as aluminum alloys and brass to reduce tool wear and processing time.
●Consider material hardness:
High-hardness materials (such as titanium alloys) are difficult to process and require a balance between performance and processing feasibility.
2) Material cost
● Cost-effectiveness optimization:
Select materials with lower costs while meeting performance requirements.
● Material utilization rate:
Reduce material waste by optimizing design, such as using nested nesting.
(3) Optimize tolerances and surface roughness
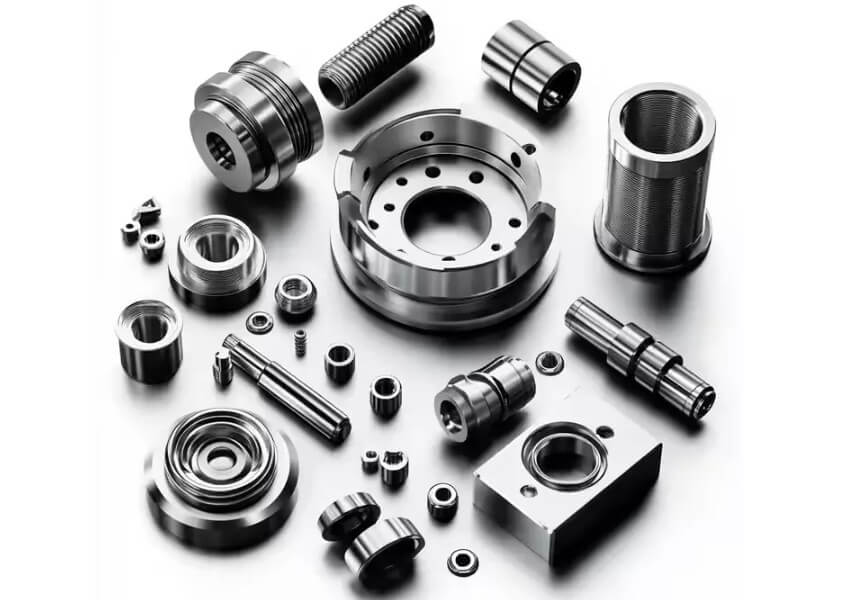
1) Reasonable tolerance setting
● Avoid too strict tolerances:
Too strict tolerance requirements will increase processing difficulty and cost, and a reasonable range should be set according to actual functional requirements.
● Critical dimensions first:
Set strict tolerances for critical dimensions that affect assembly and function, and non-critical dimensions can be appropriately relaxed.
2) Surface roughness optimization
● Function-oriented:
Set surface roughness according to the functional requirements of the parts, for example, moving parts require lower roughness to reduce friction.
● Processing process matching:
Select a suitable surface processing process (such as fine milling, grinding or polishing) to meet the roughness requirements.
(4) Design for Manufacturability
1) Reduce processing steps
●Complete multiple processes in one clamping:
By optimizing the design, parts can complete multiple processes in one clamping, reducing repeated positioning errors.
●Reduce tool changes:
Consider using the same tool to complete multiple feature processing during design to reduce the number of tool changes.
2) Standardized design
●General feature design:
Try to use standardized features such as holes, grooves, and threads to reduce the use of customized tools.
●Modular design:
Decompose complex parts into multiple modular components for easy processing and assembly.
3) Consider clamping and positioning
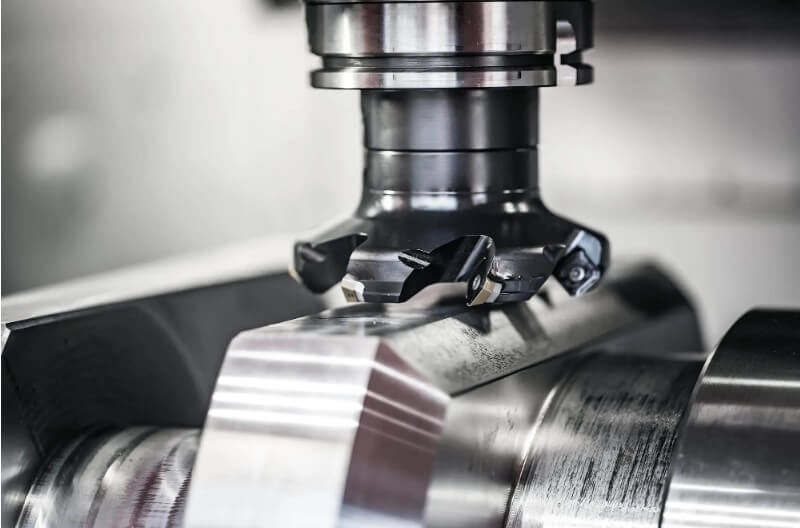
●Design clamping datum:
Design easy-to-clamp datum surfaces or holes on the parts to ensure stability and accuracy during processing.
●Avoid overhang structures:
Reduce overhangs or thin-walled structures to prevent vibration or deformation during processing.
(5) Simulation and verification
1) Use CAD/CAM software
● 3D modeling and simulation:
Use CAD software to perform 3D modeling, and use CAM software to simulate the processing process to find potential problems in advance.
● Optimize tool path:
In the process of CNC precision machining parts, it is necessary to optimize the tool path through software to reduce idle stroke and processing time.
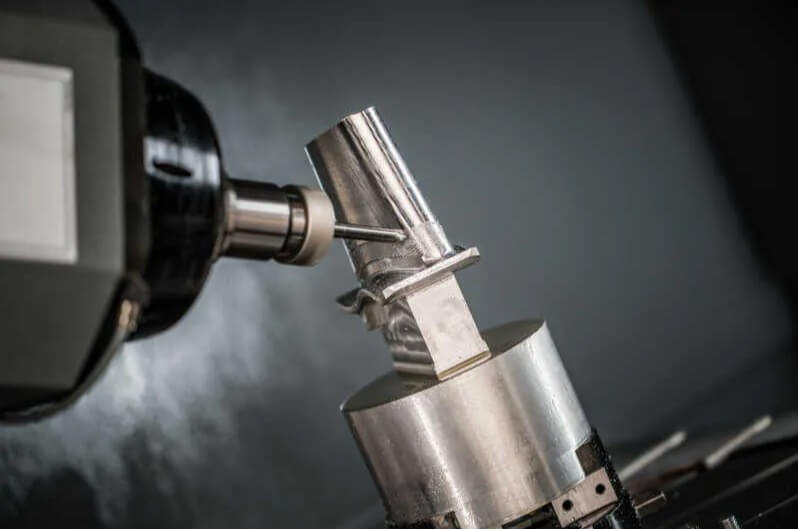
2) Prototype testin
● Rapid prototyping:
Prototypes are made through 3D printing or rapid prototyping technology to verify the feasibility and functionality of the design.
● Processing test:
Test the processing technology in small batch trial production, and further optimize the design based on the results.
5.Summary
CNC precision machining parts occupy an important position in modern manufacturing due to their high precision, high efficiency and good stability. Different types of CNC machining methods are suitable for the manufacture of various complex parts, and reasonable design optimization strategies can effectively improve machining quality and production efficiency.