CNC rapid prototyping: innovative development
Rapid prototyping technology (abbreviated as RP). It can quickly manufacture new product samples, molds or models directly based on product design (CAD) data without preparing any molds, tooling and fixtures. In short, rapid prototyping is a technology that specializes in making high-quality physical models with three-dimensional design concepts. Rapid prototyping technology is another major revolution in the manufacturing industry after CNC technology.
The integration of CNC machining and rapid prototyping technology: CNC rapid prototypingCNC Rapid Prototyping: Trends and Innovations Transforming the Industry
So, what effect will it have if these two technological innovations are combined and developed? CNC machining rapid prototyping technology has become the implementation point of this idea, enabling designers and engineers to quickly and accurately transform virtual designs into real prototypes. CNC rapid prototyping technology combines the speed and agility of rapid prototyping with the complexity and accuracy of computer numerical control (CNC) machining.
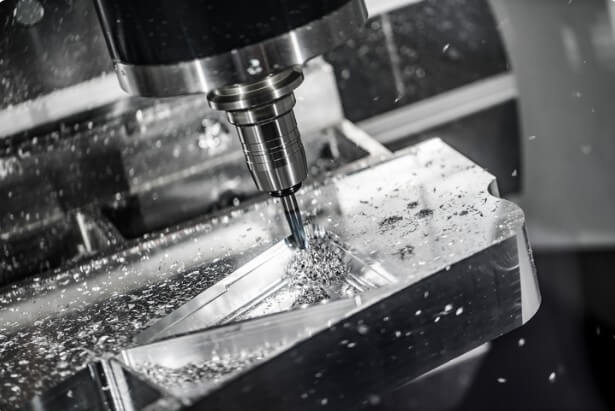
When a company or enterprise develops a new product, it always needs to prototype the designed parts or systems before investing in large-scale production facilities or assembly lines. Prototyping will greatly shorten the processing cycle of the enterprise and reduce product development costs. In addition, prototyping is very useful in the design development and improvement process, and is an important basis for production or engineering testing.
This guide will introduce all the knowledge about CNC rapid prototyping. Whether you are engaged in processing services or want to customize products, this article will be helpful to you.
1.What is rapid prototyping technology?
(1) Rapid prototyping technology
Rapid prototyping technology is a comprehensive development based on modern CAD/CAM technology, laser technology, computer numerical control technology, precision servo drive technology and new materials. It is the crystallization of multidisciplinary cross-technology.
(2) Rapid prototyping
Rapid prototyping is a technology that uses the CAD process of “holographic printer” to realize prototyping automation. CNC rapid prototyping allows designers to transform intangible ideas into tangible prototypes. When the design prototype meets customer needs and successfully completes the new product testing, it can be put into mass production. The prototyping process greatly shortens the processing cycle and reduces product development costs, which has a positive role in promoting corporate product innovation and improving product competitiveness.
2.The basic principle of CNC rapid prototyping
(1) The basic principle of RP
The basic principle of RP is to use three-dimensional technology to produce solid parts. First, the three-dimensional solid model data (STL file) is layered into layer model data (CLI file) in a certain direction. Then, the rapid prototyping machine uses specific materials based on these data to form a series of thin sheet entities.
(2) Subsequent production process
Then, through sintering, polymerization, bonding and other methods, the layers are stacked together to form a new product sample, model or mold until the entire entity is created. After making a layer of cross-section, another layer is added on it, and so on and so forth until the entire part is built layer by layer from bottom to top.
(3) The difference between CNC rapid prototyping and 3D printing
CNC rapid prototyping is an additive manufacturing technology similar to 3D printing, but the rapid prototyping method also includes rapid processing procedures such as CNC machining, injection molding, stamping, and vacuum casting. Rapid prototyping can be used at any stage of the product development process, from creative improvement to final trial production, to continuously improve the design concept.
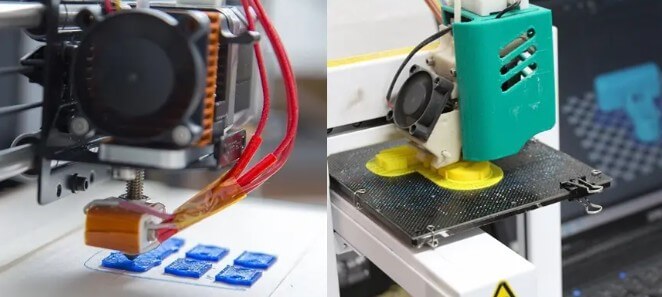
3.Process characteristics of CNC rapid prototyping:
RP uses a layer-by-layer material accumulation method to process solid models, also known as additive manufacturing (MIM) or layered manufacturing technology (LMT). This special processing method determines that it has the following technical characteristics that are completely different from traditional processing methods.
(1) High flexibility.
It can manufacture three-dimensional entities of any complex shape. The processing process does not require production preparations such as tools, molds or fixtures. For different part models, it only needs to re-enter CAD data or adjust and set different process parameters. The production cost of a single piece is almost independent of the complexity of the product and the batch size.
(2) Highly integrated CAD/CAM.
CNC rapid prototyping technology is directly driven by CAD models. The production of different parts does not require the design and use of special tooling fixtures, which can avoid cumbersome CAPP bottlenecks. The production process is completely digitalized, truly realizing seamless connection between CAD/CAM.
(3) The speed of the entire prototyping process.
From CAD design to prototype part manufacturing, it usually only takes a few hours to dozens of hours to obtain high-precision and high-reduction products, which far exceeds the speed of traditional processing.
(4) High degree of automation.
The operation process of CNC rapid prototyping technology is fully automatic, and no human intervention is required during the processing. After the parts are loaded, the equipment can work unattended.
4.Application direction of CNC rapid prototyping technology
Since the 1980s, CNC rapid prototyping technology has developed rapidly and has been widely used in many fields such as automobiles, aerospace, medicine, and light industry. Its application directions are mainly in three aspects.
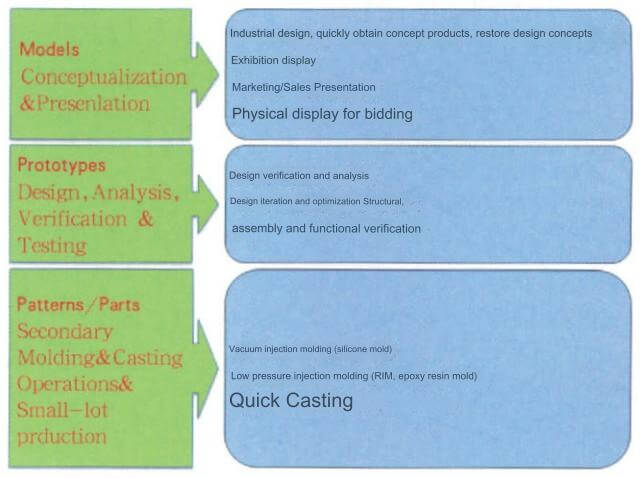
(1) Model.
CNC rapid prototyping technology has successfully solved the problem of “visible but invisible” three-dimensional modeling. Its biggest feature is that it can transform design ideas into product prototypes with certain structural functions at the fastest speed, making the design model from “visible” (three-dimensional digital model) to “visible” (physical model).
Therefore, one of the main functions of CNC rapid prototyping technology is to restore design ideas, quickly obtain conceptual products, focus on the restoration and display effect of appearance, and is usually used for sales demonstration and market promotion of new products to test market reactions, thereby improving the market reaction speed of new product development and reducing development risks.
(2) Prototype.
The rapid prototype obtained by CNC rapid prototyping technology can fully evaluate the assemblability and manufacturability of the product. Due to the high degree of CAD/CAM integration of CNC rapid prototyping technology, it can not only quickly restore the appearance of the product, but also quickly produce product parts and structural parts, thereby verifying and analyzing the structure and assembly of the product, and quickly evaluating and testing the product design, shortening the product development cycle, reducing development costs, and improving the ability to participate in market competition.
In addition, the product prototype can be quickly obtained, and on this basis, the subsequent product mold design, production process, assembly process, and even the design of mass production fixtures can be checked and evaluated to avoid production problems and huge losses caused by design defects after entering the mass production stage, so that the product can be put on the market with the fastest speed, lowest cost, and best quality.
(3) Unit manufacturing/small batch direct production.
Using the indirect molding method and combining various conversion technologies, the CNC rapid prototyping technology prototype is converted into various rapid molds, such as silicone mold technology, RIM technology, lost foam casting, etc., which can easily realize the production of single or small batch products, meeting the development trend of rapid product updates and small batches.
5.CNC rapid prototyping process
It can be divided into two stages: preliminary data processing (discrete) and subsequent physical realization (accumulation).
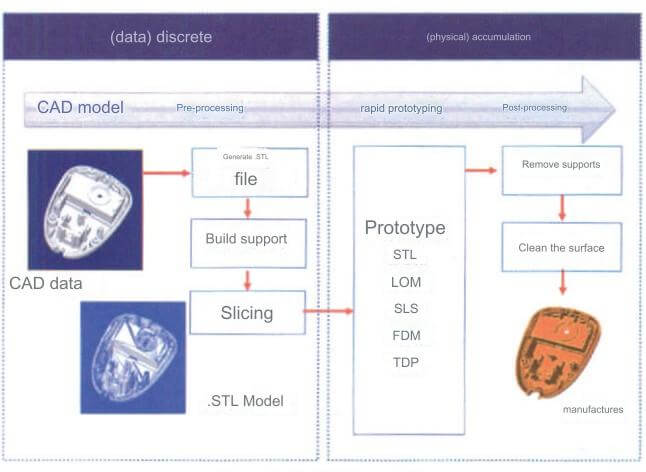
(1) Processing process
In the discrete process, CNC rapid prototyping decomposes the three-dimensional CAD model of the part along a certain direction to obtain a series of cross-sectional data, on which the motion trajectory of the forming head is obtained; in the accumulation process, the forming head processes each cross-section of the part layer by layer under the control of the motion trajectory, and the layers of cross-sections are repeatedly accumulated and connected to finally obtain the processed parts.
(2) Differences from traditional methods
Different from the subtractive principle of traditional cutting processing, this forming technology based on discrete growth obtains products in an additive manner. It can directly obtain the physical prototype (sample) of the product from the CAD file, and use it to quickly produce the physical prototype (sample) of the product.
(3) Functions and advantages
The physical prototype produced by CNC rapid prototyping can quickly verify the product appearance and the assembly relationship of the modeling parts or perform functional testing, thereby providing a measurable and touchable intuitive means to improve human-computer communication in the design process and shorten the product development cycle.
6.Principle and function of CNC rapid prototyping model
Depending on the functions of the prototype model, there are three types of prototype models:
(1) Exploratory principle
This prototype is used in the demand analysis stage of development. The purpose is to clarify user needs, determine expected features, and explore the feasibility of various solutions. It is mainly aimed at situations where the development goals are vague and both users and developers lack project experience. Through the development of prototypes, user needs are clarified.
(2) Experimental prototype
This prototype is mainly used in the design stage. Evaluate whether the experimental plan is appropriate and whether the operation is feasible. For a large system, if you are not sure about the design plan, you can use this prototype to confirm the correctness of the design plan.
(3) Evolutionary prototype
This prototype is mainly used for systems that quickly submit prototypes to users. The prototype system either contains the system framework or the main functions of the system. After being recognized by the user, the prototype system will continue to expand and evolve into the final software system. It extends the idea of CNC rapid prototyping to the entire process of software development.
7.Types of CNC rapid prototyping
(1) Rapid 3D printing prototypes
As a pioneer in the industry, different 3D printing technologies are suitable for different rapid prototyping stages. 3D printing services are generally used for model making in fields such as rapid prototyping, mold making and industrial design, and are gradually used for direct manufacturing of certain products.
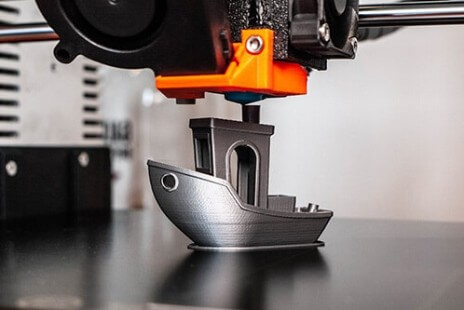
(2) Sheet metal rapid prototyping
Sheet metal processing is a subtractive manufacturing process that makes parts from thin metal sheets by cutting, bending, folding, stamping and assembling. Sheet metal parts are usually high in precision and durable, so they are particularly popular with engineers and can be used in terminal applications such as chassis, brackets and chassis.
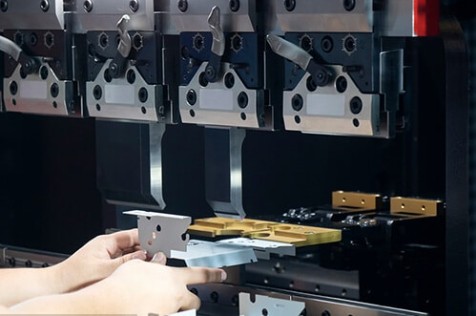
(3) Automated rapid prototyping
CNC rapid prototyping uses computer equipment to produce better designed models and prototypes with fast turnaround. It is conducive to creating high-quality end-use materials.
CNC rapid prototyping can use different programs to create actual elements. Models developed using CNC rapid prototyping are easy to change or modify. Compared with other prototyping processes, CNC rapid prototyping is faster and can design the most complex elements in the simplest way.
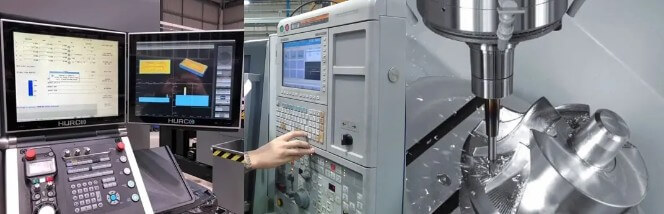
(4) Rapid injection molding
Using rapid injection molding, prototypes of injection molded parts can be made. One of the most notable advantages of rapid injection molding is the ability to make prototype models using different materials and colors.
CNC machines often facilitate rapid injection molding. The process also follows a transition-to-production approach that can produce thousands of parts.
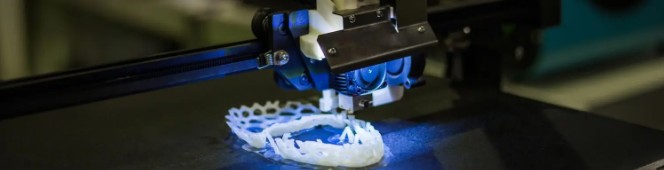
(5) Vacuum rapid prototyping casting
This method can produce parts similar to those produced in mass production, with similar mechanical properties, wall thickness, color, and surface texture. It facilitates casting of resin and silicone models and helps eliminate any potential bubbles.
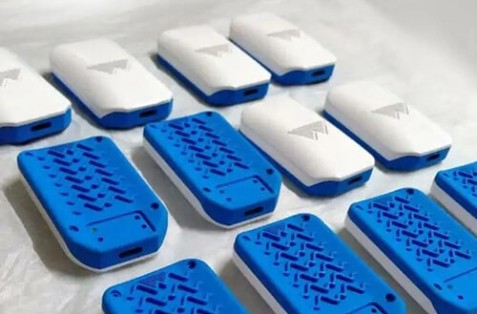
8.New Trends in CNC Rapid Prototyping
Looking ahead, CNC machining will continue to evolve and adapt to new challenges and innovations in the field of rapid prototyping.
(1) Integration of artificial intelligence
Emerging trends include the integration of artificial intelligence and machine learning to achieve more efficient and precise machining processes. This advancement can enable predictive maintenance, reduce downtime, and increase productivity.
(2) Adoption of advanced materials
A noteworthy trend in CNC rapid prototyping is the widespread adoption of advanced materials. Manufacturers are looking at a variety of materials beyond traditional metals and plastics, including composites and super alloys, which have excellent performance in specific applications. They exhibit properties similar to those used in mass production, expanding the range of possibilities for material exploration during the prototyping phase.
(3) 3+2 and 5-axis milling
The move to 3+2 and 5-axis CNC machining represents a major leap forward in machining capabilities, a development that opens up new possibilities for manufacturing unprecedented complex and precise prototypes. These advances improve the accuracy and flexibility of CNC rapid prototyping prototyping, meeting the needs of the high-precision component industry and the expanding market demand.
(4) Hybrid manufacturing
Hybrid production is a fusion of additive and subtractive methods, seamlessly integrating 3D printing and CNC machining into a single workflow. It provides a balanced solution for additive and subtractive production technologies that maximizes the advantages of both technologies. Designers can now experience the design freedom that comes with using additive strategies, while CNC rapid prototyping ensures both speed and precision.
(5) Lightweight design
Manufacturers specialize in developing prototypes that meet specific requirements and prioritize weight performance, such as in industries such as automotive and aerospace. Reducing weight can improve gas efficiency and typical performance. CNC rapid prototyping allows the creation of lightweight structures with complex geometries, which contributes to the design trend of achieving the most ideal power-to-weight ratio.
Summary:
These innovations not only enhance the capabilities of CNC machining, but also open up new possibilities for prototype development, making CNC rapid prototyping technology an even more important method in product design and testing.
9.Why is CNC machining the best choice for rapid prototyping?
CNC rapid prototyping includes CNC machining technology and rapid prototyping technology.
CNC machining is widely regarded as the most efficient and cost-effective solution for rapid prototyping. For functional prototypes that require durability, precision and a finish close to the final product, CNC machining is the first choice.
(1) Compared with other methods, CNC machining has obvious advantages in material strength and precision, which is critical for functional testing and design verification.
(2) In addition, CNC machines can process a variety of materials from metals to plastics, giving designers the flexibility to choose the most suitable material for the prototype.
(3) The speed of CNC machining also plays a vital role in shortening the time to market and enabling rapid iteration and modification based on test results or feedback.
10.Summary
So far, CNC rapid prototyping has undoubtedly simplified the way a manufacturer or company processes and works. In conclusion, CNC has had a profound impact on the field of rapid prototyping, providing precision, efficiency, and versatility. For companies that want to remain competitive in their respective markets, adopting CNC machining with expertise is a strategic step towards success.
If you are looking for an experienced CNC rapid prototyping manufacturer, Xavier is your ideal choice. The Xavier team is well equipped to provide high-quality CNC rapid prototyping solutions. If you would like to learn more or discuss your needs with us, please feel free to contact us.