CNC Robotics: Innovations in Automation and Machining Robotics
In the manufacturing industry, automation has become an important tool for improving productivity and efficiency. One of the most important advancements in automation is the use of CNC robots in machining processes. CNC (Computer Numerical Control) refers to the use of computers to control machine tools. It is able to produce many types of parts such as part exchange sewing machines, part of the washing machine, parts for slush machine and parts of a ct scan machine.
This technology has revolutionized the manufacturing industry by enabling precise and efficient machining operations. For example, part exchange sewing machines, part of the washing machine, parts for slush machine and parts of a ct scan machine.
The history of CNC robotics can be traced back to the 1940s when the first numerical control machines were developed. These early machines used punched cards to control the movement of the machine tools. While this was a significant step forward in automation, it was limited in its capabilities and required a high level of expertise to operate.
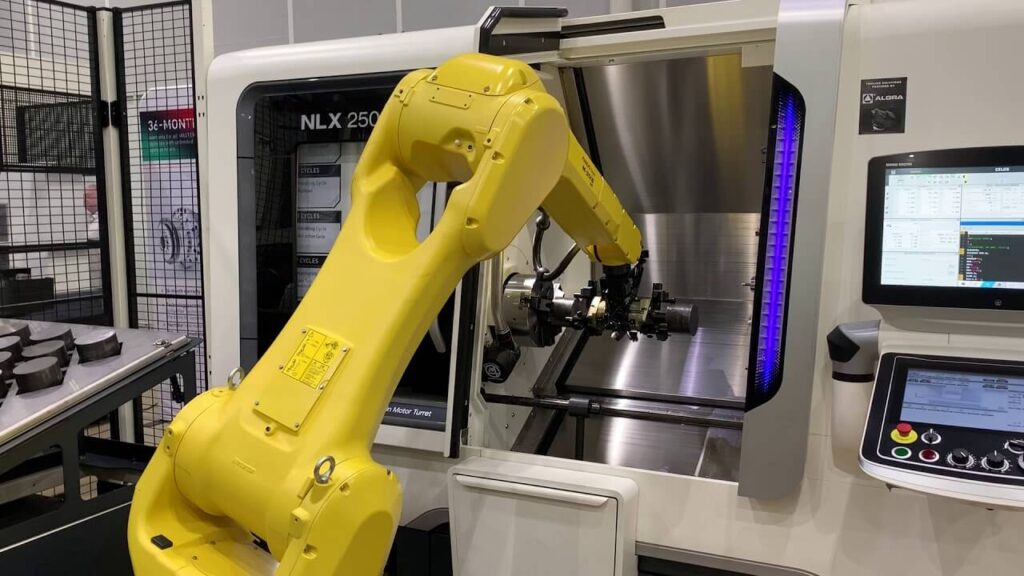
Over the years, advances in computer technology and software have greatly improved the capabilities of CNC robots. As a result, today’s CNC machine tools can already perform complex machining operations with high precision and repeatability. This advancement has increased productivity and reduced costs for manufacturers to a great extent.
One of the key benefits of CNC robotics is the ability to automate repetitive tasks. In traditional machining processes, operators would manually control the movement of the machine tools. This was not only time-consuming but also prone to human error. With CNC robotics, these tasks can be programmed into the machine, allowing for consistent and precise machining operations.
Another significant advancement in CNC robotics is the integration of sensors and feedback systems. These systems allow the machine to monitor and adjust its operations in real-time. For example, if a tool becomes dull or breaks during machining, the machine can automatically stop and alert the operator. This not only reduces downtime but also prevents costly damage to the workpiece.
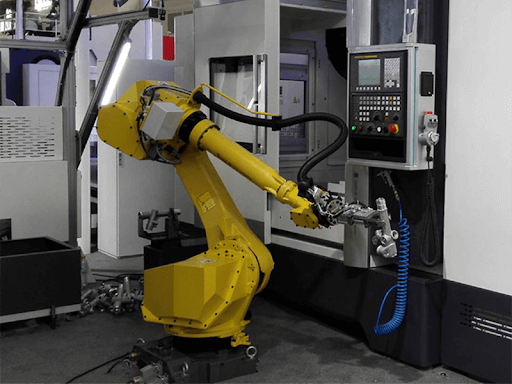
Furthermore, CNC robotics has enabled manufacturers to produce more complex and intricate parts. With traditional machining methods, certain shapes and features were difficult or impossible to achieve. CNC machines, on the other hand, can easily create complex geometries with high precision. This has opened up new possibilities for designers and engineers, allowing for the creation of innovative and unique products.
In recent years, there has been a growing trend towards the integration of CNC robotics with other automation technologies. For example, robots can be used to load and unload workpieces from the CNC machine, further reducing the need for human intervention. This not only increases productivity but also improves worker safety by reducing the risk of accidents.
Looking to the future, the evolution of CNC robotics is expected to continue. Advancements in artificial intelligence and machine learning are likely to further enhance the capabilities of these machines. For example, AI algorithms can be used to optimize machining processes, reducing cycle times and improving efficiency.
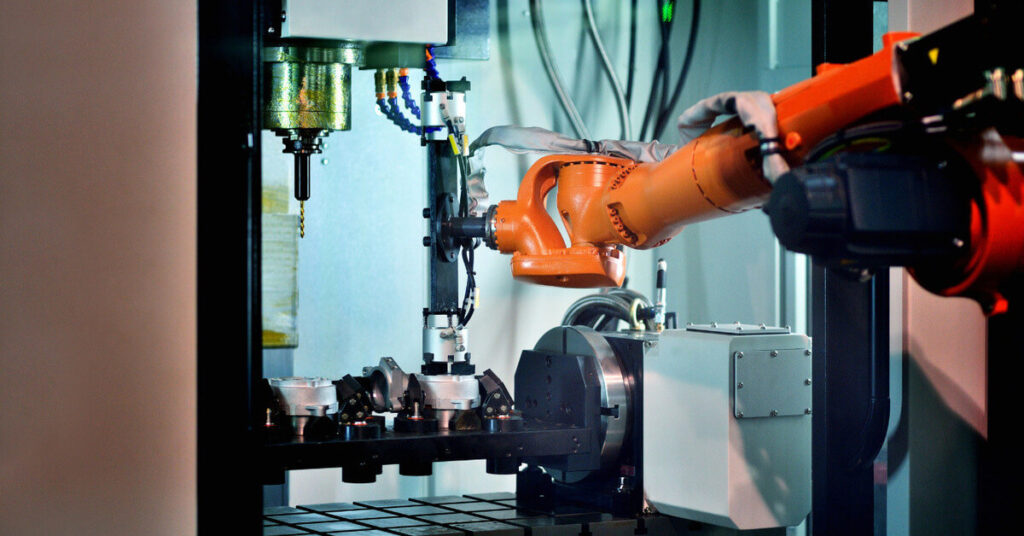
In conclusion, CNC robotics has come a long way since its inception in the 1940s. The integration of computers, sensors, and automation technologies has transformed the manufacturing industry. CNC machines now offer unparalleled precision, efficiency, and flexibility. As technology continues to advance, we can expect even greater innovations in automation and robotic machining.