CNC Swiss Lathe vs CNC Lathe: Which Should You Choose?
In the field of precision machining, CNC Swiss lathes and CNC lathes are two common methods, each with its own advantages and application scenarios. But for users, choosing which CNC service to use may be confusing. This blog will deeply analyze the characteristics, advantages, and applicable scenarios of these two devices to help you make a more appropriate choice.
What is a CNC Swiss Lathe?
1.Definition
A CNC Swiss lathe, also known as a Swiss-style automatic lathe or Swiss-style turning center, is a high-precision CNC machining equipment specially designed to produce small and complex parts. Originating in the Swiss watch industry, it now plays an indispensable role in many industries.
2.Working principle
Guide Bushings: The hallmark of Swiss machining is the guide bushing, which supports the workpiece close to the tool.
Moving headstock: The headstock moves axially and feeds materials through guide bushings, unlike traditional lathes.
Tool positioning: Tools are arranged around the workpiece and can be operated on multiple surfaces simultaneously.
Synchronization: The CNC system precisely coordinates the movements of the spindle box, guide bushings and cutting tools.
Continuous machining: After the part is finished cutting, the bar is advanced and the process repeats seamlessly.
Multi-axis control: usually has multiple linear and rotary axes for complex machining operations.
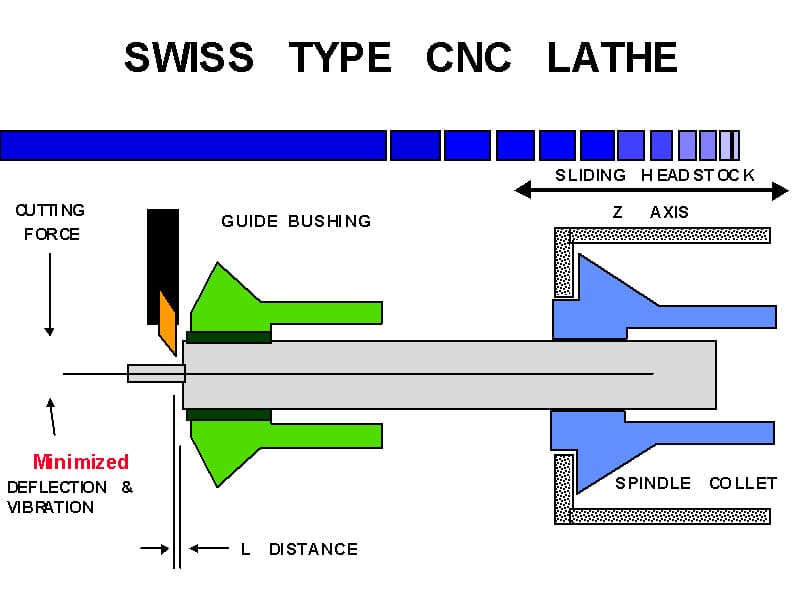
3.Advantages
High precision: Known for extremely high precision and strict tolerances, it is suitable for medical, aerospace and other industries.
High Repeatability: Consistently produces high-quality parts.
Complex parts production: Unique guide bushing system can effectively handle long, slender parts and complex details.
Simultaneous operation: multiple tool paths, turning, drilling, milling and other operations can be performed at the same time to reduce production cycle.
Less secondary processing: The completion of one-time processing is high, reducing the need for secondary processing.
Reduce Deflection: The guide bushing is positioned close to the cutting tool, reducing deflection and improving surface finish and dimensional consistency.
Higher speed: It can operate without vibration at higher speed, shorten processing time and improve surface finish.
Automation: High degree of automation, automatic rod feeding, multi-axis motion and cam programming, precision machining of complex parts without manual intervention.
4.Disadvantages
Bar stock size is limited: usually between 2mm – 38mm and needs to be of consistent diameter.
High tooling costs: Specialized tools are expensive and limited in size and geometry.
Heat dissipation problem: Using oil as a lubricant has poor heat dissipation effect.
Long installation time: Calibrating and changing tools increase preparation, and programming requires significant time and staff training.
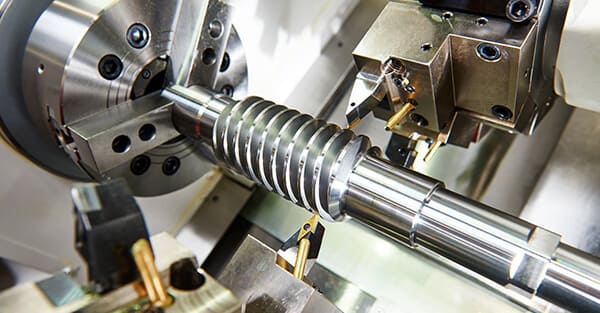
5.Application scenarios
Miniature components for medical devices that meet high demands.
Aerospace precision parts ensure aircraft safety.
Small and complex automotive parts improve vehicle performance.
The clock mechanism highlights the advantages of origin.
Dental implants and surgical instruments ensure medical quality.
High-precision electronic connectors ensure stable device connection.
Optical industrial components to meet high-precision needs.
Small hydraulic and pneumatic valves ensure system operation.
Provide equipment support for complex components of scientific instruments.
Mass production of small turned parts is efficient and stable.
What is a CNC lathe?
1.Definition
A CNC lathe, also known as a CNC turning center, is a computer-controlled machine tool that produces cylindrical parts by rotating the workpiece. It is the foundation of modern manufacturing and can produce a variety of turned parts with high precision and efficiency.
2.Working Principle
Workpiece Rotation: Clamped in a collet or chuck, it rotates at high speed.
Tool Movement: Mounted on a turret or tool holder, it moves along a programmed path to remove material.
CNC Control: The computer numerical control system interprets program instructions and coordinates tool movement and cutting parameters.
Axis Control: There are two spindles (X and Z), and more advanced models have additional axes.
Turret Indexing: Multi-station turrets allow for rapid tool changes and multiple operations in one installation.
Seat Support: Long workpieces are provided with additional support by the tailstock to prevent deflection.
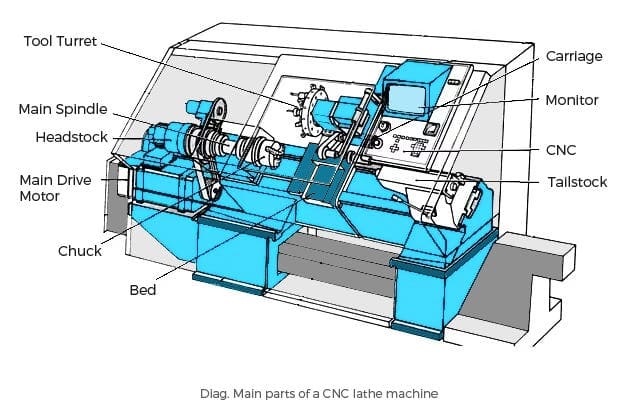
3.Advantages
Can produce a variety of round and cylindrical parts.
Can accommodate larger diameter workpieces.
Programming and operation are generally more straightforward.
Generally more affordable than Swiss lathes.
Can process a variety of material forms, including castings and forgings.
4.Disadvantages
Lack of guide bushing support can easily lead to deflection of certain geometric shapes.
Complex parts may require multiple setups or operations.
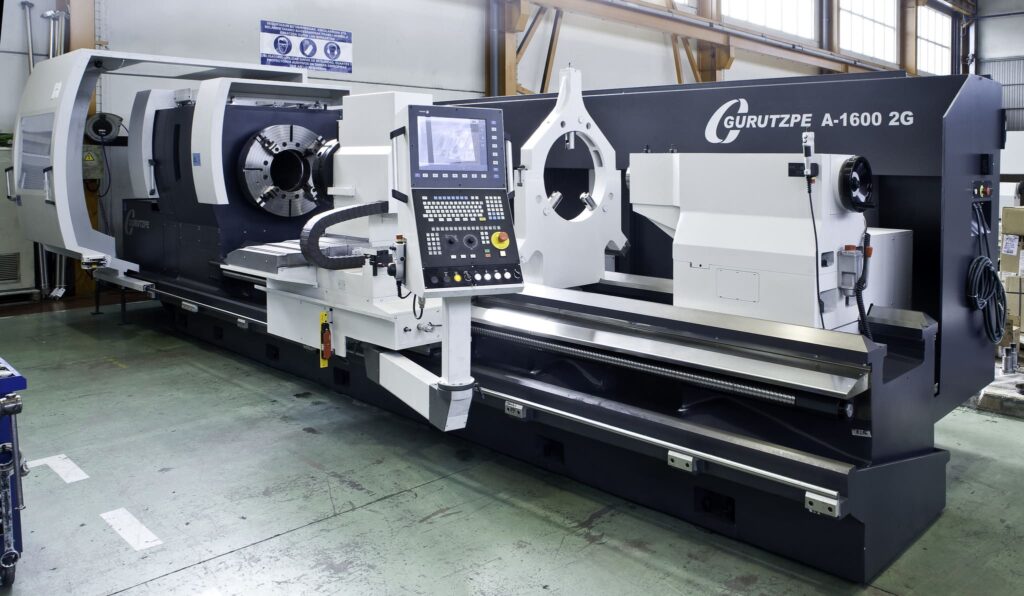
5.Applicable scenarios
General turning operations, rough machining and fine surface treatment can be performed to ensure stable and consistent machining quality.
Production of shafts, pulleys and cylindrical parts, high-precision machining to ensure dimensional accuracy and surface quality, and improve production efficiency.
Thread cutting and grooving, precise control of tools to achieve various specifications of thread cutting and different shapes of grooving.
Front and chamfering of cylindrical parts, fast and accurate completion, improve the appearance quality and assembly performance of parts.
Can manufacture large diameter parts to meet specific industry needs, ensuring machining accuracy and stability.
For prototypes and small to medium-sized production runs, quickly process samples to verify designs and efficiently complete production tasks.
Rework and repair of existing parts, accurate measurement and programming control to repair parts.
Play a role in mechanical processing training and education, helping students and novices master programming and operation skills.
CNC Swiss Lathe VS CNC Lathe
1.Part size and geometry
CNC Swiss lathes excel at producing small, precise parts and are suitable for long, slender parts; CNC lathes are more flexible in part size and can process small and large diameter workpieces, but are more limited when producing extremely long, slender parts.
2.Precision and surface finish
CNC Swiss lathes have higher precision and surface finish, and the guide sleeve support system reduces part deflection; CNC lathes can achieve good precision and surface finish, but may have difficulty achieving very tight tolerances on long, slender parts.
3.Output
CNC Swiss lathes are optimized for large-scale production of small parts and have strong automation capabilities; CNC lathes are suitable for small and medium-sized production and may require more frequent setups and operator attention.
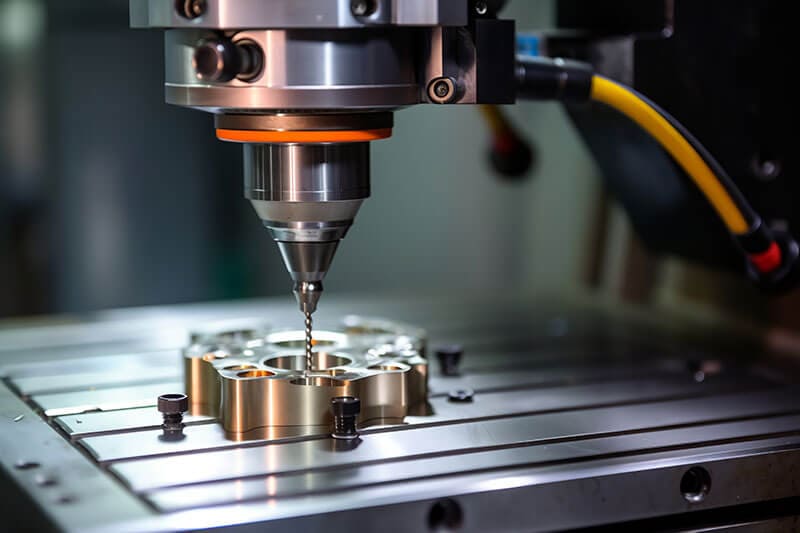
4.Part complexity
CNC Swiss lathes can produce complex parts in a single setup and perform multi-faceted operations simultaneously; CNC lathes may require multiple setups or secondary operations to produce complex parts.
5.Material Utilization
CNC Swiss lathes excel in material utilization, especially for long, slender parts; CNC lathes have lower material utilization, especially for small parts.
6.Flexibility and Adaptability
CNC Swiss lathes are efficient for specific parts, but have limited adaptability; CNC lathes are more versatile and can handle a wider range of part geometries and sizes.
7.Initial Investment and Operating Costs
CNC Swiss lathes have a high initial investment, but are low cost in high-volume production; CNC lathes have a low initial investment.
8.Programming and Operation Complexity
CNC Swiss lathes are more complex to program and operate, requiring a deep understanding of the principles and programming; CNC lathes are generally easier to program and operate.
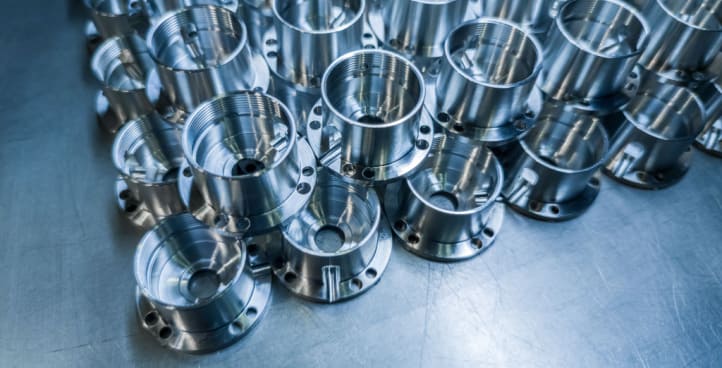
9.Secondary Operations
CNC Swiss lathes generally do not require secondary operations; CNC lathes may require multiple setups or additional secondary operations.
10.Automation Potential
CNC Swiss lathes are naturally suited for automation, with built-in bar and part collection systems for lights-out manufacturing; CNC lathes generally require more complex material handling solutions to achieve fully automated systems, and continuous operation may require complex workpiece loading and unloading devices.
In conclusion
Choosing between a CNC Swiss Lathe and a CNC Lathe requires a comprehensive consideration of project requirements, production scale, precision requirements, and cost-effectiveness. For precision parts machining that requires extreme accuracy, high automation, and mass production, a CNC Swiss Lathe is undoubtedly the ideal choice. For occasions that require flexibility to cope with multiple part sizes, moderate production scale, and cost sensitivity, a CNC Lathe is more advantageous. The final choice should be based on specific production needs to achieve the best production efficiency and cost control.
If you are looking for an experienced CNC machining manufacturer, Xavier is undoubtedly your ideal choice. The Xavier team is well-equipped to provide high-quality CNC machining solutions. For more information or to discuss your machining needs with us, please feel free to contact us.