A Comprehensive Look at CNC Swiss Precision Machining
I know you are wondering, why is it called CNC Swiss precision machining? Most people are fascinated by the name of this type of machining before they know the basics of the process.
Yes, the name of the machine is related to the country of Switzerland. Apart from that, the machine offers a lot of features, so it is widely used all over the world.
For a long time, Swiss machines have been considered to be made exclusively for Swiss watchmakers. It is a versatile machine that can produce small and complex parts.
In this post, we will focus on the characteristics of CNC Swiss precision machining.
1.What is CNC Swiss precision machining
CNC Swiss precision machining is usually a machining performed by operators on CNC lathes, whose original design comes from Switzerland. It is a specialized process that usually focuses on producing complex and delicate parts. The products of CNC Swiss precision machining are also known for their tight tolerances.
It all started in the 19th century when Swiss engineers designed a machine that could manufacture small parts. The main mechanism of this machine is a guide bushing and a headstock with a sliding function. Based on this setup, the workpiece and the cutting tool can be close to each other. This improves tolerance and precision. Since the 70s, Swiss machines have replaced their automation with CNC.
CNC Swiss precision machining has one of the most impressive range of capabilities you can get. Some of the processes that can be performed in CNC Swiss precision machining include turning, drilling, tapping, and milling.
CNC Swiss precision machining is faster and more efficient in part production than conventional CNC machining. It can deliver 30 parts per hour that are ready for shipment or delivery – without secondary operations.
Therefore, for smaller parts with thin walls and all other complex components, this is the preferred CNC machining process for producing small complex parts.
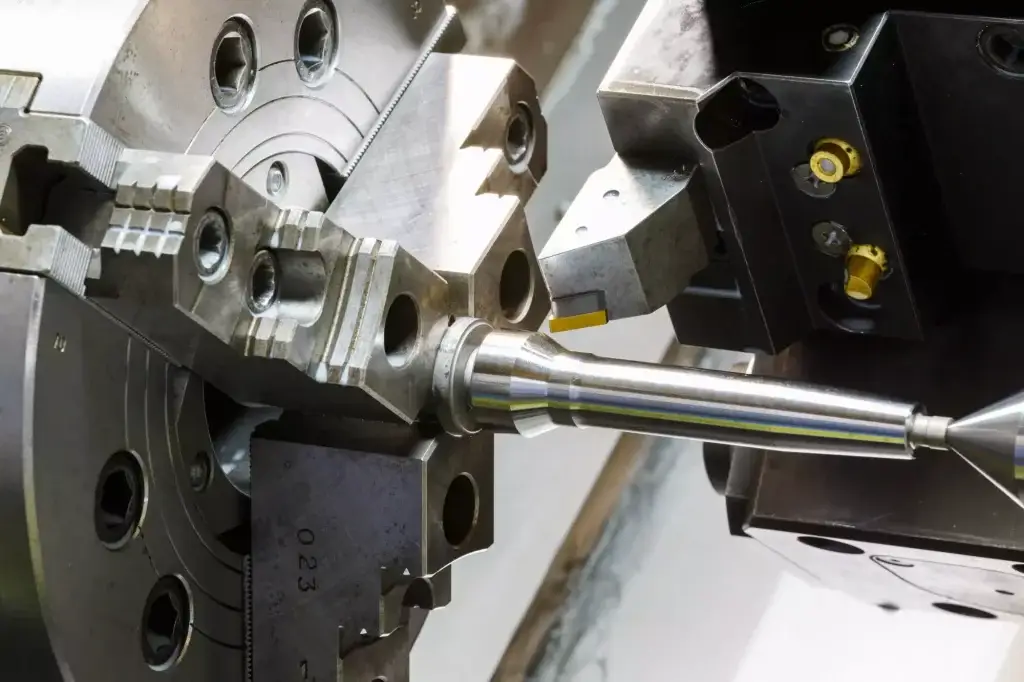
2.CNC Swiss precision machining vs. CNC machining, what is the difference?
Given the diversity of user needs, the debate of CNC Swiss precision machining vs. CNC machining is not going away anytime soon. Conventional CNC lathes are undoubtedly revolutionary, so it has its advantages. The same is true for Swiss CNC lathes.
Swiss machine tools are known for their short cycle times. They can meet the requirements of large-scale production. The capabilities of this type of machine tool depend on the availability of multiple axes, in some cases, more than 10 axes. They cannot machine complex parts at speeds comparable to conventional lathes.
There are also differences in the bar stock sizes that the two types of CNC machines are able to handle. CNC machining on Swiss-type machines is limited to smaller bar stock (about 1.5 inches). Conventional CNC machining is capable of machining larger bar stock.
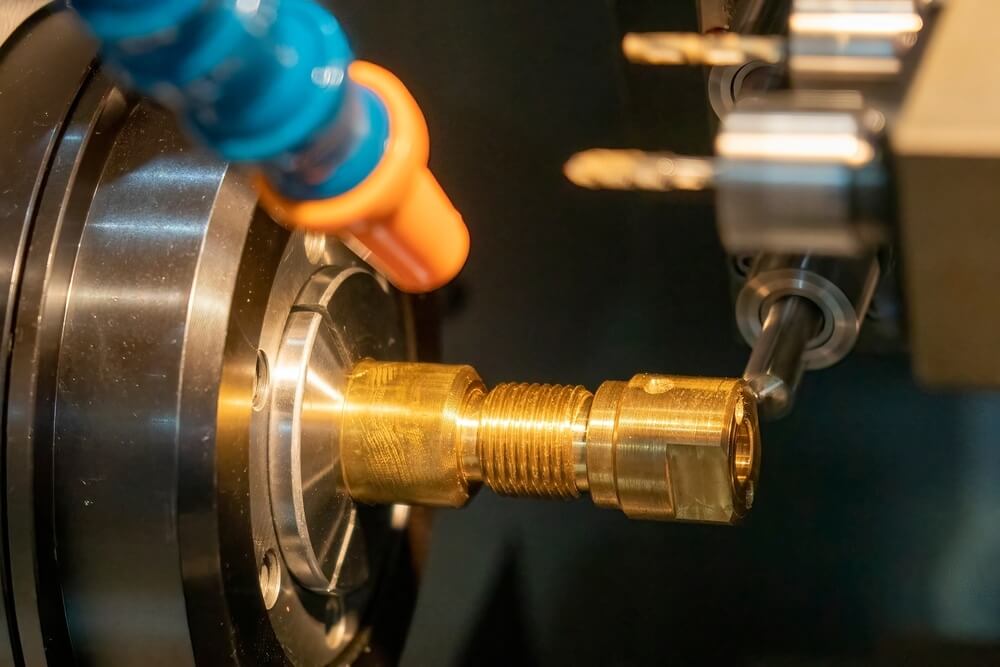
3.Advantages and Disadvantages of CNC Swiss Precision Machining
When considering whether to invest in or use a Swiss-type CNC machine, you need to understand its advantages and disadvantages. Here are the prominent advantages and disadvantages of this CNC machining method.
Advantages of Swiss Machines:
1) High Precision Machining
Swiss lathe machining technology tends to have very high precision compared to conventional lathes. While other lathes typically have a maximum of three axes, Swiss lathes can operate up to five axes. The more axes, the more precision the machine is able to provide machining operations. Swiss lathes can achieve tolerances up to 0.0002 inches.
2) High Repeatability
Swiss precision machining is synonymous with consistent performance. These interesting machines produce high-quality components with amazing repeatability. This is an irreplaceable attribute for industries where even the smallest units are important.
3) Complex Part Production
If you are looking to manufacture complex parts with extreme precision, CNC Swiss precision machining technology is the way to go. This machining technology is ideal for producing complex geometries that other machining operations may have difficulty doing.
4) Simultaneous Operations on Swiss Machines
Swiss machine tools continue to evolve. Today’s Swiss CNC lathes come with multiple tool spindles. This feature means that these lathes are capable of performing multiple operations simultaneously.
It can turn a shaft on one spindle and drill a block on another spindle. This capability can reduce cycle times. It can save a machine shop a lot of time and money compared to traditional lathes.
5) Reduced Secondary Operations
Another notable feature of Swiss machine tool operations is that the need for secondary operations is minimal or even non-existent. This is because the technology is built with tight tolerances and unmatched precision.
6) Reduced Deflection
As we all know, the distance between the workpiece and the tool can determine the degree of deflection. For Swiss lathes, the cutting tool and the workpiece are in close proximity. Due to this setup, deflection is reduced, which brings other benefits, such as higher precision machining.
7) Higher RPMs
Another feature of Swiss machines is the ability to run at relatively high revolutions per minute (RPM). There is no vibration even at such high RPMs.
As a result, Swiss machines produce products with the best surface finish. The production time for this machining process is also faster.
8) Automation of Swiss Lathes
Automation advances combine perfectly with Swiss lathe capabilities. CNC Swiss precision machining has a variety of operations, higher stability, shorter delivery times, and many other features combined with automation to great effect.
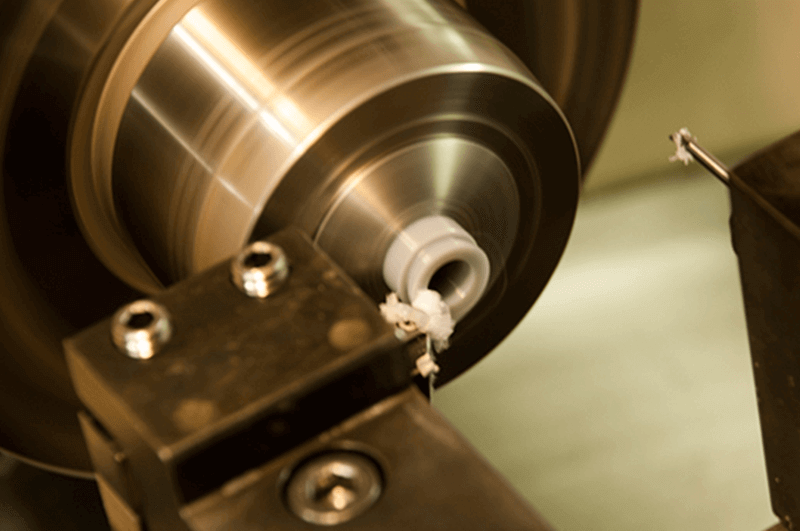
Disadvantages of Swiss Machines:
1) Bar Stock Limitations
Bar size limitations are one of the most significant disadvantages of Swiss turning centers. These CNC machines are usually limited to machining small bars, such as about 1.5 inches in diameter. For larger bars, conventional lathes are more suitable.
2) Higher Tooling Costs
Swiss machine tools tend to be more expensive than conventional lathe tools. The specialization of these tools is the main issue. Tools used to machine complex parts with tight tolerances are always more expensive than standard tools.
Add to that automatic bar feed mechanisms and high-speed machining, and it becomes even more obvious why CNC Swiss precision machining tooling is expensive.
3) Heat Dissipation Issues
The use of oil-based coolant in CNC Swiss-type machines offers several benefits. It prevents rust and tool wear while also reducing friction. However, this coolant is not completely effective in promoting heat dissipation in CNC lathes.
As a result, Swiss-type lathes can be damaged by heat buildup.
4) Longer Setup Times
Automatic Swiss lathes are powerful, so setting up can be time-consuming. Multiple tools need to be calibrated and fixed. This applies to the programming step, which can require a high level of expertise.
4.Applications of CNC Swiss Precision Machining
The Swiss watchmaking industry may be the origin of Swiss machining, but today the technology has a variety of applications.
Popular industries that benefit from this solution include:
1) Aerospace
If there is one industry that has benefited greatly from this type of machining of complex parts, it has to be the aerospace industry. Aerospace components are extensively manufactured using Swiss machine tools.
The most notable metals among them are aluminum alloys and steel. Some of the components are fans and fasteners.
2) Medical Devices
The medical industry also makes extensive use of Swiss-type lathe products to machine precision parts. Medical devices manufactured using this machining method offer the high precision required by the industry. Surgical instruments and implants are perfect examples of the impact Swiss-type lathes have made in the medical field.
3) Electronics
Modern electronics are smaller and more complex than ever before. Traditional lathes are increasingly struggling to achieve the desired results. Manufacturers have turned to advanced solutions such as CNC Swiss precision machining.
These powerful CNC machines are ideal for producing connectors, pins, and many other electronic components.
4) Automotive
CNC Swiss precision machining solutions are also widely used in the automotive industry. The technology is behind some of the latest mechanical advancements we have seen in the automotive industry recently. It helps in manufacturing smaller and more complex parts in the automotive industry.
Automotive manufacturers are using this technology to manufacture suspension components, carburetor covers, and engine parts. The industry has benefited greatly in terms of reducing costs, streamlining the manufacturing process, and increasing production speeds.
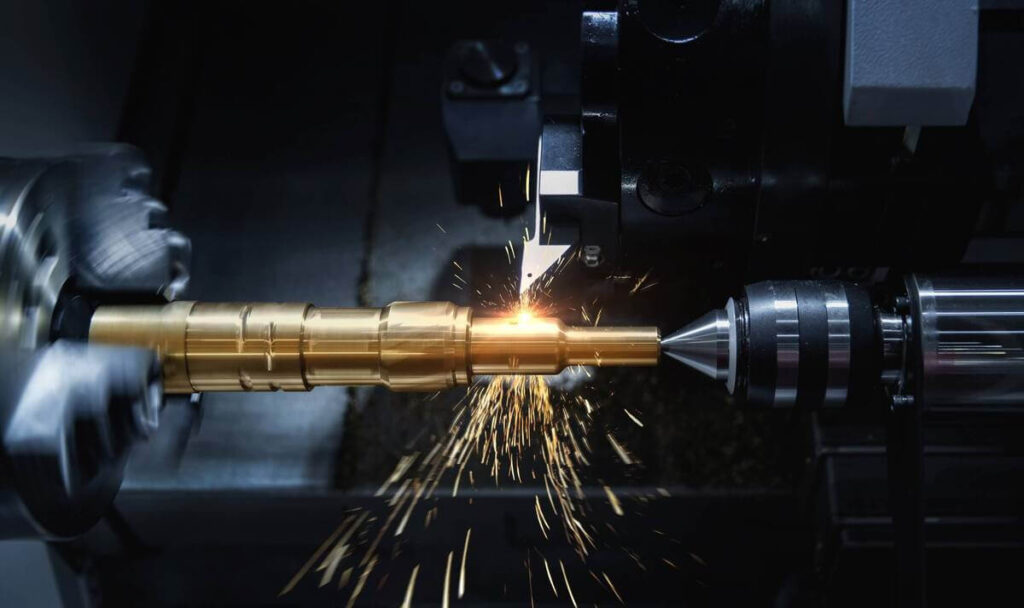
5.Conclusion
CNC Swiss precision machining plays an important role in the operations of many manufacturing plants. Its versatility, reliability, and cost-effectiveness in producing small, complex parts are unmatched by traditional machining. Its capabilities in jobs with very tight tolerances are exceptional.
We have detailed the intricacies of CNC Swiss precision machining and outlined the advantages and uses of the process. We hope that with these insights, you are ready to use this amazing technology on your next project.