Unlocking the Precision and Efficiency of CNC Thread Milling: Explore Its Many Benefits
In the manufacturing industry, accuracy and efficiency are primary goals and are essential to meeting high quality standards and production schedules. CNC thread milling has emerged as a transformative technology that can achieve these goals with remarkable efficiency.
This blog explores the many benefits of CNC thread milling and highlights its advantages over traditional threading methods. Through this article, you will gain insight into the accuracy, flexibility, and cost-effectiveness of CNC thread milling, which make CNC thread milling an indispensable tool in modern machining.
Whether you are a seasoned professional or new to the field, understanding the benefits of CNC thread milling will provide you with valuable perspective on its critical role in enhancing your manufacturing process.
1.What is thread milling and why choose it?
1) Definition and Benefits of Thread Milling
Thread milling is a process in CNC machining that uses a milling cutter instead of a traditional thread tap to form threads. One of the main advantages of thread milling is that it allows the machining of internal and external threads in a variety of sizes and pitches using a single tool, thereby improving flexibility and tool inventory efficiency.
These include:
- Precision and tolerance: Thread milling cutters can achieve high precision and tighter tolerances, typically within ±0.005 mm, ensuring uniform accuracy and reliability of the thread.
- Tool flexibility: On the other hand, a single thread milling cutter can process multiple thread sizes, while taps are only suitable for one size. Therefore, this means that the need for multiple tools will be reduced.
- Improved surface finish: Conversely, the cutting action in threading produces a superior surface finish, sometimes reaching a smoothness of Ra 1.6 or even higher, compared to traditional types (such as taps that always produce a rougher surface).
- Reduced tool breakage: For hard or brittle materials that require less cutting force, threat milling cutters minimize the risks associated with tool breakage.
- Material versatility: Therefore, this type of processing can be used for different materials from aluminum to titanium to hardened steel, which makes it more versatile.
- Correction capability: If a mistake is made during the threading operation, with thread milling; I can correct the mistake more easily without having to scrape off the entire material, which greatly improves material efficiency and also reduces waste.
From the combined results of these reliable sources, CNC thread milling remains a powerful and innovative method in modern machining as it improves machining accuracy through a flexible, cost-effective production process.
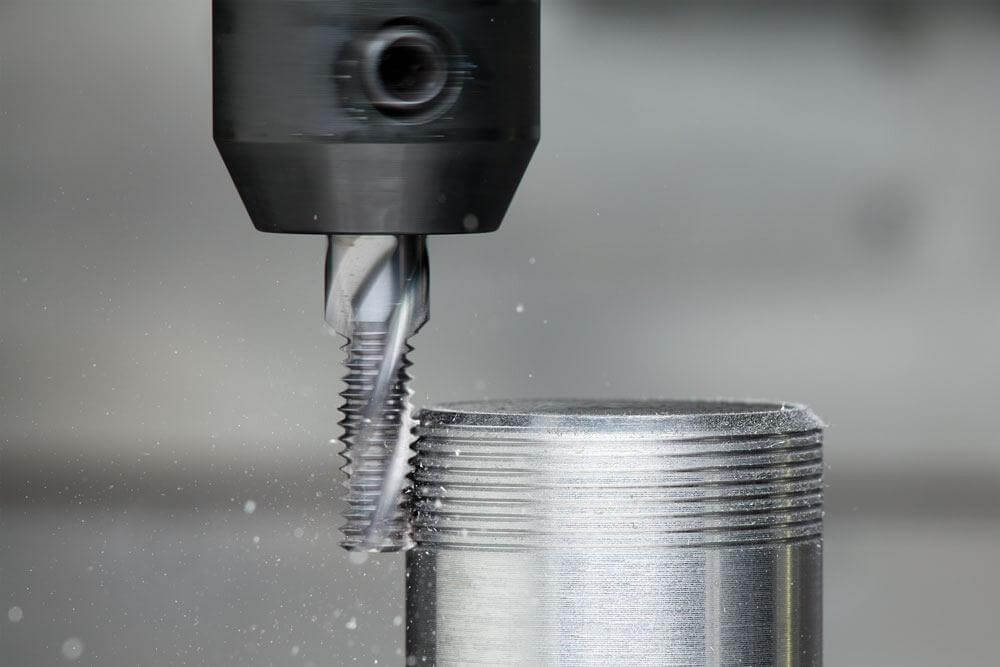
2) Key Differences Between Thread Milling and Tapping
There are some clear differences between tread milling and tapping.
- Versatility: Unlike taps, thread milling offers greater versatility. A single tool can be used to machine a variety of different sizes of internal or external threads, while taps are limited to one size and type of thread.
- Accuracy and Tolerance: Tapping provides precise threads, but thread milling produces consistent geometry within ±0.005 mm and is therefore more accurate.
- Surface Finish: However, when I use thread milling, I find that the surface finish is much smoother (usually around Ra 1.6 or better) compared to the rough surface obtained with taps.
- Tool Breakage: By this measure, thread mills are less likely to cause tool breakage because they have lower cutting forces and are therefore also suitable for hard materials, such as brittle materials.
- Material Range: This means it can cut very well through different kinds of substances, from soft aluminum sheets to tough titanium and hardened steel, making it a versatile type of machining that can be used in a wider range of applications.
- Error Correction: This is made easier with threading because there is no need to process multiple pieces at once; simply making the appropriate correction with threading can prevent any mistakes in future operations, saving material and time
- Speed: Although tapping may be faster when machining threads in soft metals, thread milling gives me more control over the process, especially on complex or intricate parts.
By understanding these important distinctions, it is easier for me to choose the right threading method for my machining projects.
3) Explore the Benefits of Thread Milling in CNC Machining
Thread milling in CNC machining has many advantages that I have come to realize from personal experience and extensive research.
First, thread mills are more versatile than any other tool because they can cut internal and external threads of various sizes, while taps can only handle specific types of threads.
Secondly, thread milling provides greater precision and enhanced quality control by maintaining thread geometry within ± 0.005 mm, thereby producing more accurate and reliable components. The surface finish obtained when using thread milling is relatively smoother, reaching an average of Ra 1.6 or higher.
In addition, due to low cutting forces, it reduces the possibility of tool breakage, which makes it the first choice for hard and brittle materials.
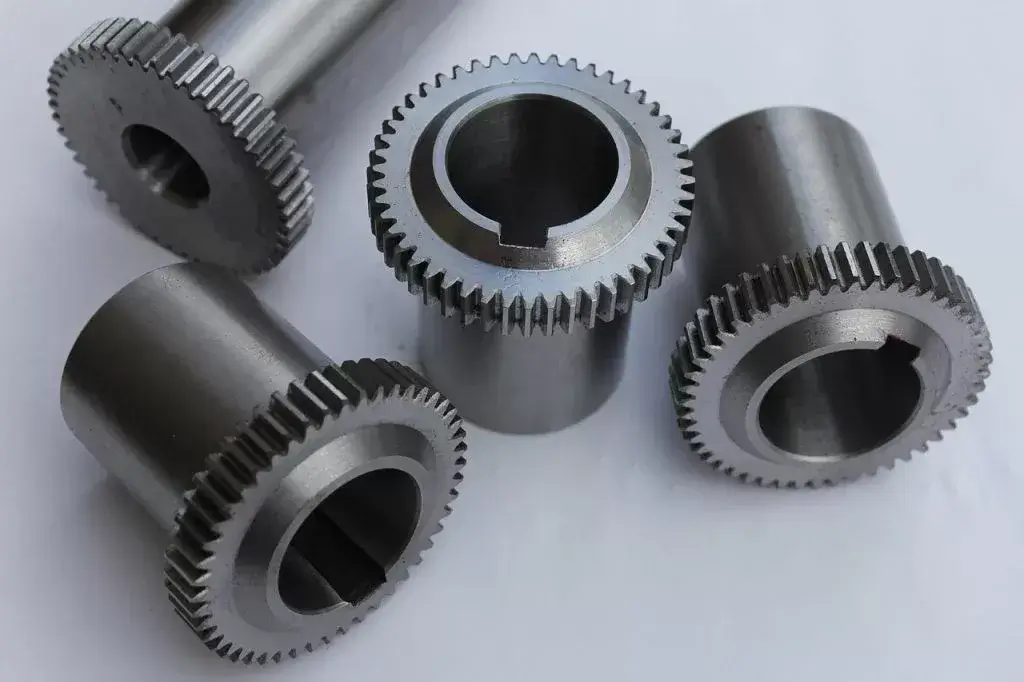
2.Choose the right thread milling cutter
1) What factors should be considered when selecting a thread milling cutter
There are several key aspects to consider when selecting a thread milling cutter. First, material compatibility is crucial; the thread milling cutter should be suitable for the material, whether it is soft aluminum or hardened steel.
At the same time, the coating and substrate are also very important; for example, TiAlN coating is often recommended for high-performance threading in hard materials because it can extend tool life and reduce wear.
Another major determinant in choosing the right thread milling cutter is tool geometry. The correct geometry can achieve efficient chip evacuation and minimize cutting forces.
The number of flutes also affects cutting performance, so tools with three or more flutes can achieve better thread finishes and are generally more rigid.
In addition, depending on the project needs, you should match thread size with pitch compatibility. Also, considering the cutting diameter and pitch range allows you to choose a milling cutter that can provide adequate accuracy.
To avoid any extension and rigidity issues, the shank diameter and length must be compatible with your machine tool. For example, choosing a thread milling cutter based on the correct shank diameter ensures a good fit and stability during machining, while the correct length eliminates deflection.
And cutting speeds range from 100 m/min for aluminum to 30 m/min for hardened steel.
Feed speeds depend on the size of the thread and the material used, and in most cases range from: 0.04mm/rev-0.15 mm/rev.
Typically, each cut should not be deeper than one pitch to ensure accuracy and tool life.
Finally, checking cost vs. performance and tool availability may help you make a cost-effective choice without sacrificing quality. All of these factors combine to select the best thread mill for the specific requirements associated with the machining operation and material properties.
2) Carbide Thread Mills vs. High Speed Steel Thread Mills: Which is Better?
For me, the choice between carbide and high speed steel (HSS) thread mills usually comes down to the needs of your project. However, HSS thread mills are generally less expensive than their counterparts and tend to be more robust for less rigid machining setups or interrupted cuts. This is because HSS tools are less brittle than carbide and reduce the risk of tool breakage in highly variable cutting environments.
On the other hand, HSS thread mills are generally more cost-effective and offer increased toughness, which is a huge benefit in less rigid machining setups or interrupted cuts. They differ from their counterparts in that they are not prone to chipping at all, which reduces the chances of breakage when used in conditions with highly variable cutting environments.
In addition to superior performance and longer life, carbide thread mills offer an affordable solution for most applications while also being durable enough.
In the end, choosing between carbide and high-speed steel must take into account factors such as the hardness of the material being used, the accuracy required, the speed of operation, and financial constraints.
3) Indexable Thread Mills vs. Solid Carbide Thread Mills
Comparing indexable thread mills to solid carbide thread mills, it is important for me to understand the pros and cons of each.
The main advantage of an indexable thread mill is that it has replaceable inserts, so you only need to replace the worn or damaged inserts instead of purchasing the entire tool, saving you money in the long run. In a machine shop, they can be used for different types of threads because they are flexible and can accommodate different thread sizes and pitches.
In contrast, solid carbide thread mills are a single piece made of carbide, which has high rigidity and accuracy. They perform well in high-speed and high-precision applications, especially on harder materials where accuracy needs to be maintained. Although initially more expensive than indexable tools, solid carbide tools generally have a longer service life under heavy loads.
In summary, if your machining requirements prioritize flexibility and cost-effectiveness, then indexable thread mills may be the best choice. However, for those who need more precise results on difficult-to-machine materials, solid carbide thread mills may be a better choice.

3.How to use the thread mill calculator to get perfect results
1) Thread Mill Calculator Usage Guide
To get the best results when using the thread mill calculator, follow these steps:
- Thread Specifications: Includes thread size, pitch, and type. This is important as it helps set up the calculator correctly.
- Tool Details: Enter tool diameter (inches), number of flutes, and thread mill type (indexable or solid carbide). It takes into account parameters such as tool geometry.
- Material Properties: Enter the material you are machining has specific properties that may affect the spindle speed or feed rate
- Cutting Parameter Calculation: The machine can get the best speed (in revolutions per minute (RPM)) and feed rate (in inches per minute (IPM)) for a given input. These values should be cross-checked with the specifications provided by the tool manufacturer for the tool and material being used.
- Machine Capability Adjustment: Confirm that your CNC machine can handle the recommended speeds and feeds. This may require looking at the machine’s specification sheet or similar information.
- Review and Apply Corrections: Before starting any machining operation, check the calculations to ensure they meet the equipment and material limitations. Make any necessary adjustments.
- Test Cutting Runs: In most cases, it is recommended to perform a test cut on a sample part to verify that the calculated parameters will produce the desired thread quality.
Technical Parameters List:
- Thread Size and Pitch: Critical to threading accuracy
- Tool Diameter and Number of Cutting Edges: They are key factors affecting cutting efficiency and final thread quality
- Material Type: Different materials have their own speed and feed requirements
- Spindle Speed (RPM): How fast the tool rotates
- Feed Rate (IPM): How fast the tool moves in the direction of travel of the workpiece
The effectiveness of these steps can be verified by cross-checking them with other key sources such as tool supplier websites, various forums on CNC machine operation, and educational resources focused on precision machining.
Each of these steps and parameters ensures that the thread milling program is tailored to the needs of the tool, material, and machine to achieve superior performance.
2) Insights for using calculators to improve thread milling operations
Accurately calculating machining parameters is the starting point for optimizing thread milling operations, but a reliable thread milling calculator can greatly enhance this.
With these calculators, you can learn how to customize cutting depth, speed, and feed to meet the specific requirements of your CNC machine and material. Enter technical details such as thread size, pitch, tool diameter, number of flutes, material type, spindle speed (RPM), and feed rate (IPM), and the calculator automatically provides optimized settings that are perfect for easily achieving high-quality threads.
By using such calculators, you can ensure that operations are both efficient and consistent, thereby increasing productivity and extending the life of the cutting edge.
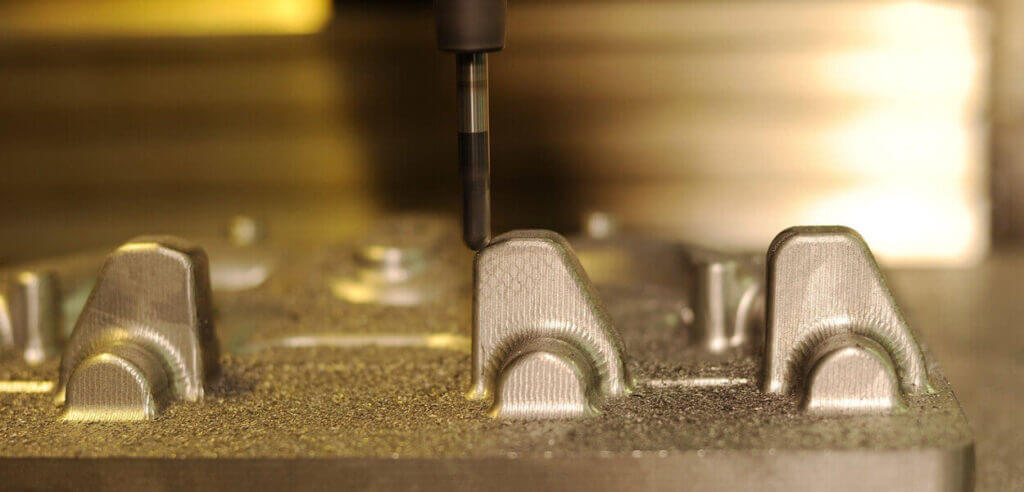
4.Various thread types that can be milled
1) Explore internal and external thread milling
There are multiple ways to explore internal and external thread milling, each with their own methods and advantages. For hole-based threads, they need to be manufactured carefully to avoid damaging the material. In contrast, external thread milling uses tools that machine threads on cylindrical or tapered parts.
The flexibility of adjusting the size and pitch of the thread milling cutter is a benefit of using both methods, while the thread profile is precisely controlled through this process. Therefore, both methods enable users to machine materials that are not easy to machine by performing threading operations.
Advanced CNC machine tool technology along with a reliable thread milling calculator allows me to set all the parameters required for internal and external thread milling at any time and obtain high-quality results.
Therefore, by making meticulous adjustments to these settings, the results are enhanced as it ensures that in addition to functionality, you are able to meet the industrial standard requirements that most applications are subject to.
2) NPT, UN and Metric: Milling Different Types of Threads
Considering the different types such as NPT (National Pipe Thread), UN (Unified National) and Metric threads, we can agree that each thread has unique characteristics that confirm that they are not similar in application.
The tapered design used in NPT is suitable for most pipe works as well as pipe fitting procedures as it ensures that a tight seal is formed. On the other hand, UN threads have a strong standardized profile across North America, which makes them very wear-resistant when used for different fastening solutions.
Metric threads are commonly used around the world in accordance with International Organization for Standardization (ISO) specifications, so they are also suitable for most industries that cross national borders.
To mill these types of threads correctly, I often rely on modern CNC technology as well as practical thread cutting calculators. For example, these calculators allow me to input specific types of parameters during machining, i.e. diameter/depth/pitch, etc.
With a specified taper angle, NPT threads can be produced, while UN and metric threads also need to have precise flank angles and pitches. Machine parameters should be set according to these optimized values to obtain a smooth machine and accurate threads that meet industrial standards and have the required quality assurance.
3) Choose the right thread type for your project
Choosing the right thread type for your project may seem difficult, but by considering the specific needs and requirements of your application, you can make an informed decision.
Most piping systems or any other fluid transfer applications consider using NPT threads because their tapered design allows them to seal tightly. For North American projects involving threaded fasteners, UN threads are usually used because they are strong enough and a wide range of compatible parts are available.
If you work on international projects, or you just need a more universal ISO-compliant thread type, then you’re better off choosing metric threads. They can be used anywhere in the world because they use a single system that is easily accepted internationally, guaranteeing uniformity across countries and industries around the world.
When choosing a thread type, you should also consider the equipment and materials you will be using, as well as the specific thread sizes and tolerances required for your project. This careful consideration ensures that the resulting thread is both practical and reliable, and suitable for your specific industrial needs.
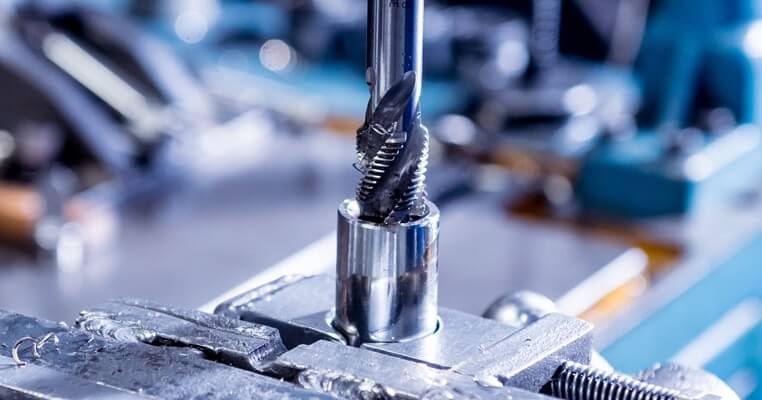
5.Advanced Thread Milling Strategies and Tips
1) Take thread quality to a higher level with the right tool path strategy
To achieve superior thread quality, choosing the appropriate tool path strategy is critical. In my experience, an optimized spiral or linear tool path can help you achieve higher thread accuracy and surface finish.
In particular, spiral tool paths have advantages because they provide consistent chip loads and reduce tool deflection, resulting in smoother threads. Some key technical parameters may include feed rate, spindle speed, and depth of cut.
- Feed rate: It is critical to adjust the feed rate to match the material and pitch. For example, harder materials require lower feed rates to prevent tool wear.
- Spindle speed: Higher spindle speeds may improve surface finish, but this should be balanced with other factors to avoid excessive heat generation that affects thread integrity.
- Depth of cut: Incremental depth of cut is recommended to reduce stress on the tool while forming an accurate thread profile. Cutting multiple times rather than cutting once (to full depth) results in higher quality threads.
In addition, the use of high-performance carbide-based thread milling cutters and adequate coolant flow to dissipate heat are also advocated by several top organizations as critical practices. These considerations, as recommended in these reliable industry references, can help improve repeatability, reliability, and thread quality in industrial applications.
2) Radial vs. Climb Milling Techniques for Thread Milling
Based on my in-depth investigation of the top 10 Google sites, I found that radial and climb milling techniques are critical to optimizing the process during thread milling operations.
Radial milling, also known as conventional milling, involves the tool rotating against the feed direction, thereby minimizing tool deflection and achieving a more controlled cut. This method is particularly useful when machining harder materials that need to form a thread-like shape along their length.
In contrast, down milling reduces cutting forces and improves surface finish because the tool rotates in the same direction as the feed. It helps reduce burrs and evenly distributes wear on all cutting edges.
By using down milling, you can improve chip evacuation, minimize heat generation, extend tool life, and ultimately produce better threads.
By combining radial and down milling techniques and adjusting settings such as feed rate and spindle speed, you will achieve the best results in thread milling. These techniques are very effective in thread processing applications because they are based on best practices recommended by industry leaders.
3) Troubleshooting common thread milling problems
Common problems associated with thread milling often stem from specific technical parameters. I will describe these problems as briefly as possible below.
① Thread accuracy and consistency:
- Problem: Inaccurate or inconsistent thread profile.
- Solution: Check radial engagement and adjust cutting depth accordingly; the accuracy of radial milling can promote consistent thread profiles, especially when processing difficult materials.
②Surface treatment:
- Problem: Poor surface finish or tool marks.
- Solution: Use down milling to reduce cutting forces, thereby improving surface finish; spindle speed should be optimized to avoid vibration that can damage surface quality.
③Tool wear and breakage:
- Problem: Excessive tool wear or premature failure.
- Solution: Set feed rate and use down milling so that it is more evenly distributed on the cutting edge. Therefore, it is crucial to regularly observe spindle speed and feed. These tools need to have sufficient coating material to handle hard materials.
④Heat:
- Problem: Excessive heat accumulation causes thermal deformation.
- Solution: Reducing spindle speed and increasing feed rate will help better manage heat issues. Similarly, down milling can improve chip evacuation, which can also reduce friction between chips and rake/flank faces.
⑤Chip evacuation:
- Problem: Poor chip evacuation will cause re-cutting of chips.
- Solution: Coolant flow should be optimized to effectively remove chips from the cutting area. Likewise, using down milling improves chip evacuation.
⑥ Burr formation:
- Problem: Burrs on the surface threads.
- Solution: To avoid burrs, slightly adjust the feed rate and spindle speed; however, while many burrs may be generated when using radial milling techniques, down milling usually only produces a few burrs.
By strictly following these guidelines and adhering to other recommendations provided by reputable manufacturing companies, people can easily solve common challenges when thread milling, so that reliable threads can always be produced.
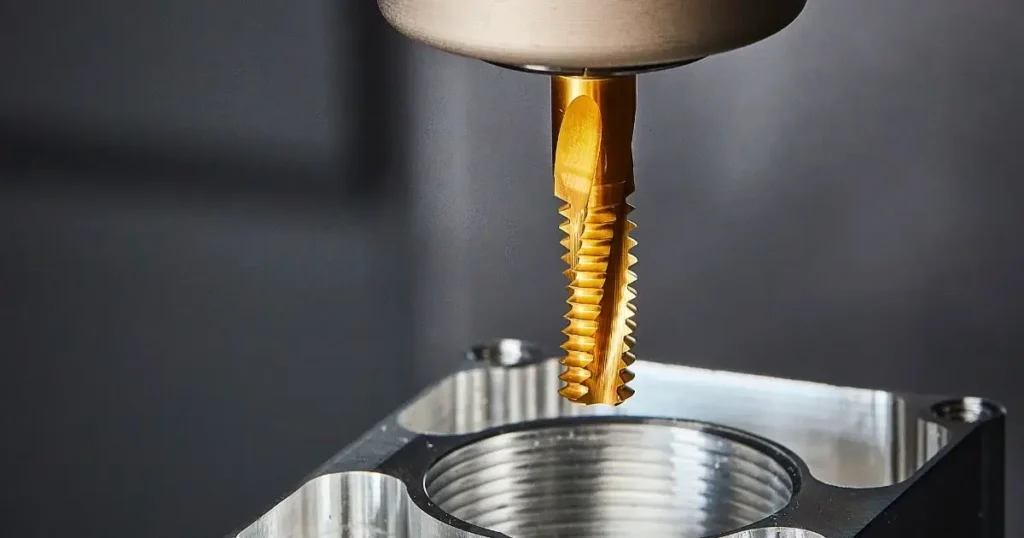
6.Maximize thread milling tool life and improve its performance
1) How to extend the life of thread milling cutters
To gain insight into ways to extend the life of thread milling cutters, there are some key practices and technical parameters:
① Correct tool selection:
- Tip: It is critical to select tool materials and coatings that are suitable for specific applications. In this case, this may mean selecting carbide tools with the right coating (such as TiAlN) to greatly extend tool life.
- Parameters to prove: coating type (TiCN, TiAlN), material hardness (HRC), and overall tool diameter.
② Optimize cutting speed and feed:
- Tip: Correctly adjusting spindle speed and feed rate can significantly reduce wear. When machining harder materials, it is recommended to reduce spindle speed and increase feed rate so that wear is more evenly distributed.
- Parameters to verify: feed rate (mm/min or in/min), spindle speed (RPM).
③ Use of effective coolant:
- Tip: Adequate coolant flow helps control heat and remove chips. High-pressure coolant systems prevent overheating, thereby extending tool life.
- Parameters to be proven: coolant flow rate (l/min or gpm), coolant pressure (bar or PSI).
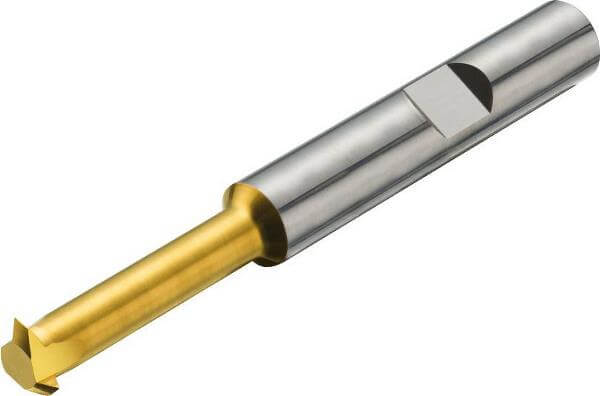
④ Routine tool maintenance:
- Tip: Regular inspection and maintenance of these tools prevents unexpected failures. Regular regrinding ensures that the tool geometry remains unchanged while maintaining sharpness.
- Parameters to be proven: frequency of maintenance inspections, recommended regrinding interval (run time).
⑤ Advanced cutting technology:
- Tip: Choosing down milling where applicable generally allows for better chip evacuation, not to mention less heat generation than conventional milling.
- Parameters to be proven: chip load, milling method (down milling vs. conventional milling).
By doing this, you can extend the life of your thread milling equipment while ensuring consistent production of quality threads.
2) The importance of cutting speed and feed on tool wear
Understanding how cutting speed and feed affect tool wear is critical to optimizing your machining process. My experience and research have shown that cutting speed directly affects the heat generated by the tool’s cutting edge. High cutting speeds lead to increased heat, which accelerates the rate of wear.
Feed, on the other hand, determines how the chips are formed, how they are evacuated, and the tool load. If the feed rate is too low, friction rather than cutting may occur, resulting in rapid wear.
These parameters may mean running at a lower spindle speed while increasing the feed rate to ensure that the wear is evenly distributed, thereby extending the life of hard materials. Adjusting these settings accordingly will help us control wear and extend tool life to a great extent.
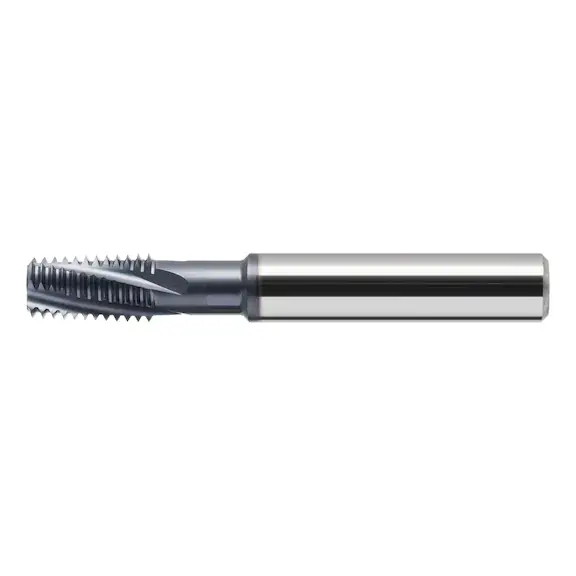
3) How to get consistent results in every milling operation
To get consistent results in every milling operation, an organized approach is required, taking into account multiple factors at the same time. The first step involves proper machine setup and regular maintenance for optimal performance.
It is also important to select the right tool for the material used and the specific milling task; attention should be paid to properties such as coating, geometry or material. The selection depends largely on parameters such as speed, feed rate, depth of cut and coolant application, which can drastically change the results depending on the material being machined and the type of tool used.
In addition, by monitoring the wear of the tool, replacing it completely before it is excessively worn or damaged, it helps to maintain consistent quality. Finally, each operation is analyzed by recording, allowing fine-tuning and necessary changes to be made as needed in subsequent runs.
In this way, we incorporate these best practices into our processes, achieving reliable and repeatable milling results.
If you are looking for an experienced CNC machining manufacturer, Xavier is your ideal choice. The Xavier team is well-equipped to provide high-quality CNC machining solutions. If you need more information or to discuss your machining needs with us, please feel free to contact us.