CNC turned parts: the use of digital machining program
CNC programming is the key link to complete the processing of CNC turned parts, which guides the machine tool to complete the processing of the workpiece. Reasonable CNC program can not only improve the processing efficiency, but also ensure the quality of parts processing. This paper will discuss the application of CNC programming and its importance in accomplishing the machining of CNC turned parts.
1.Overview of CNC turning technology
(1) The origin and development of CNC technology
CNC technology, that is, computer numerical control technology, originated in the 1950s, initially developed by the Massachusetts Institute of Technology, aimed at solving the problem of processing complex military parts. With the development of computer technology, CNC technology has been rapidly popularized and applied to various manufacturing fields, becoming an integral part of modern manufacturing. CNC technology through digital programs to control the movement of mechanical tools to achieve high precision, high efficiency automated processing, greatly promoting the modernization of the manufacturing industry.
(2) The status of CNC turning in the modern manufacturing industry
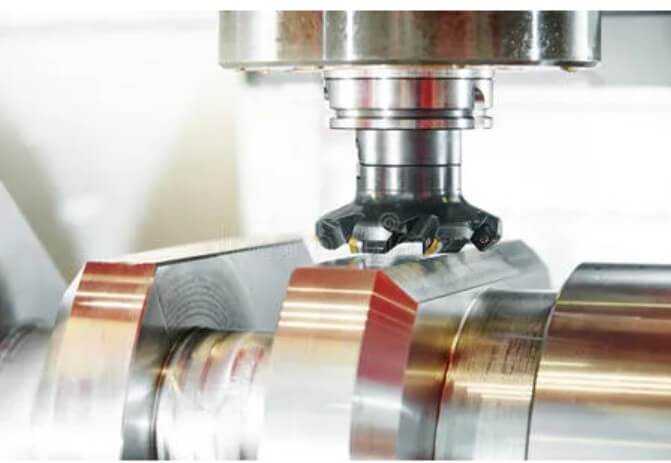
CNC turning technology, as an important branch of CNC technology, is mainly applied to the processing of rotating parts, such as shafts and disk parts. It is characterized by its high precision and high efficiency, and occupies an extremely important position in the modern manufacturing industry, especially in the automobile, aerospace and precision instruments and other industries that require very high precision of parts. CNC turning technology can process the traditional lathe is difficult to process the complex shape of the parts, greatly improving the production flexibility and product quality, is one of the key technologies indispensable to the modern manufacturing industry.
(3) Digital machining program
Digital machining program through the computer numerical control (CNC) system, the design drawings into machine-recognizable instructions to achieve precise control of CNC machine tools. Compared with the traditional manual programming, digital machining program can significantly improve programming efficiency, reduce human error and ensure the stability and consistency of the machining process. Common automated programming software such as MasterCAM, UG, etc., provides a wealth of machining strategies and simulation functions, making programming easier and more efficient.
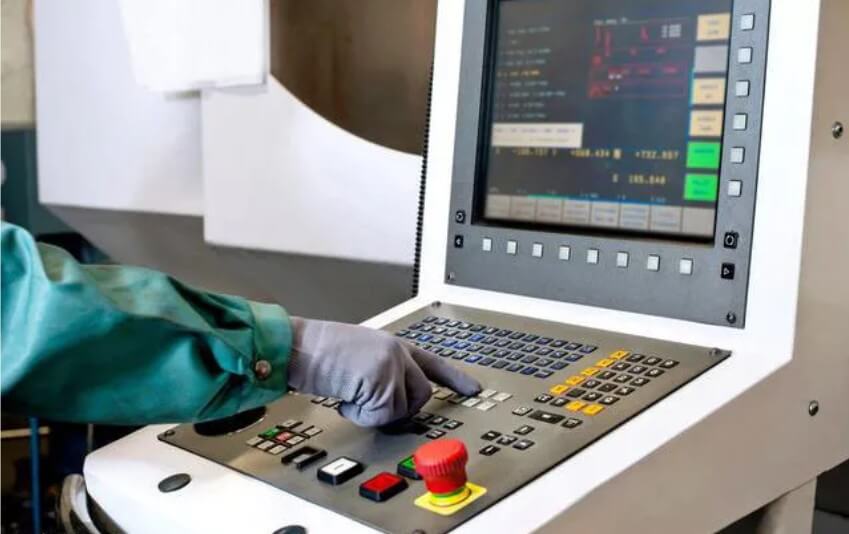
2.How is CNC turned parts utilized in the machining process?
CNC turning is an indispensable part of the modern manufacturing industry, the core of which lies in the realization of efficient and accurate parts processing through digital control technology. The following is the embodiment of several key aspects of CNC technology in the machining process of turned parts:
(1) high degree of automation
CNC lathe through the pre-written machining program to automatically complete the parts processing. In addition to manual loading and unloading of workpieces, the machine tool can automatically cut, feed, tool change and other operations. The increase in the degree of automation significantly reduces the labor intensity of the operator and improves the labor conditions. For example, the spindle speed of CNC lathe has reached 5000-7000r/min, greatly improving the processing efficiency.
(2) Stable machining accuracy and quality
The dimensional accuracy of CNC turning processing is usually between 0.005 ~ 0.1mm, and is not affected by the complexity of the shape of the part. The CNC system ensures that the tool moves accurately according to the preset trajectory by means of high-precision servo motors and closed-loop feedback control system, thus eliminating human error in operation, improving the consistency of the dimensions of the same batch of CNC-turned parts, and keeping the quality of the product stable.
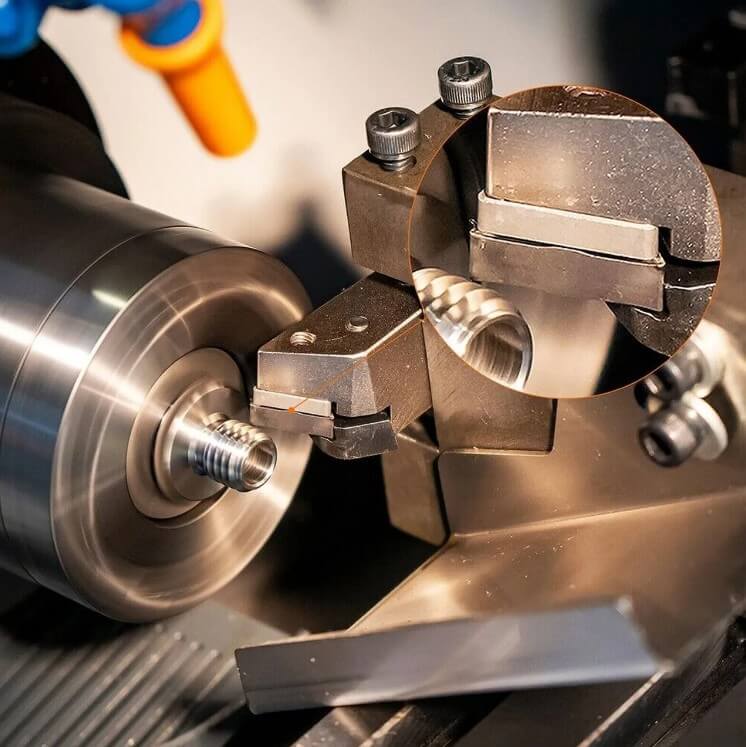
(3) Flexible adaptability
CNC lathe machining program is editable, when the processing object changes, just rewrite and enter the processing of the part of the program, you can automatically process new parts, without having to make any complex adjustments to the machine tool. This feature makes the CNC lathe in the short production preparation cycle, new product development has significant advantages.
(4) optimized machining program
The development of CNC turning machining process pays great attention to the concentration and optimization of the process. As far as possible in a clamping to complete the processing of most or even all surfaces, in order to reduce the number of clamping and tool change time, improve production efficiency. At the same time, through reasonable tool path planning and cutting parameter selection, to ensure that the machining process is efficient and stable.
(5) Computer communication and networking
CNC machine tools use digital information, easy to connect with computer-aided design and manufacturing (CAD/CAM) system to form an integrated system. Through networking technology, multiple CNC machine tools can form a flexible manufacturing system to achieve centralized management and scheduling of the production process, further enhancing productivity and flexibility.
(6) Intelligent tool management
Modern CNC lathe is equipped with intelligent tool management system, which can automatically identify and manage the use of tool status. According to the processing requirements, the system automatically selects and replaces the appropriate tool, reducing manual intervention and improving processing efficiency and tool life.
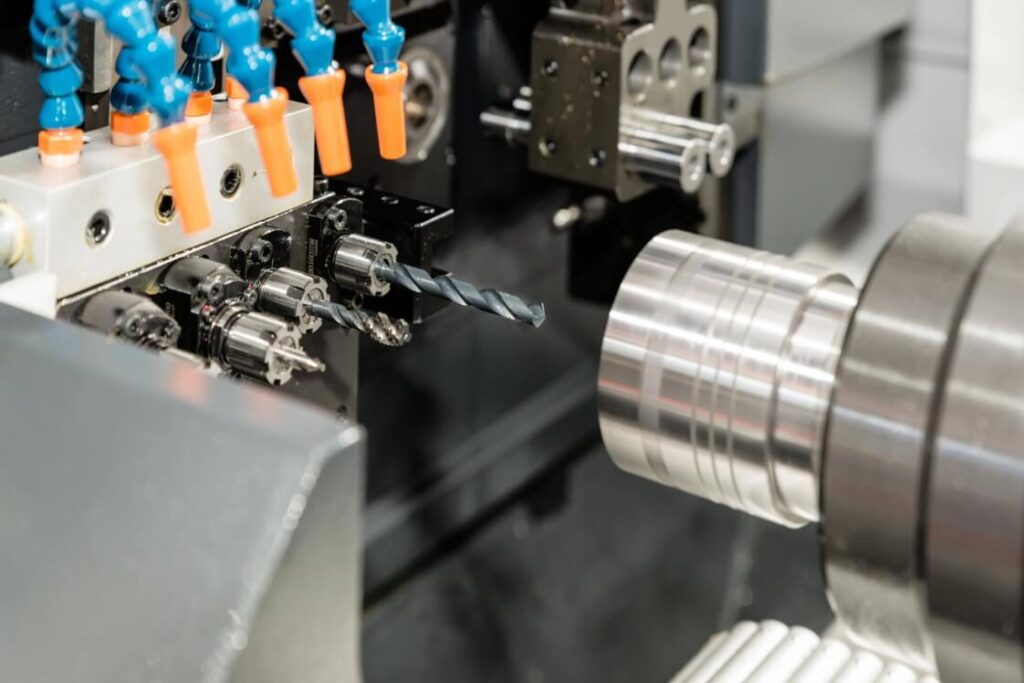
Summary:
The application of CNC technology makes the process of machining CNC turned parts more efficient, precise and flexible, providing strong support for the development of modern manufacturing.
3.Typical CNC turned parts machining cases
(1) Shaft parts CNC turning processing
Shaft parts are common processing objects in CNC turning, which are characterized by a length greater than the diameter, usually need to ensure high dimensional accuracy and surface roughness. Shaft CNC turning parts machining process, generally use a clip a top of the clamping method, that is, one end of the three-jaw chuck clamping, the other end of the top support to ensure the coaxiality and stability of the parts.
In terms of tool selection, a pointed turning tool is usually used for external turning, and a drill or reamer is used for internal hole machining. The selection of cutting parameters needs to be adjusted according to the material and size of the parts to ensure processing efficiency and accuracy.
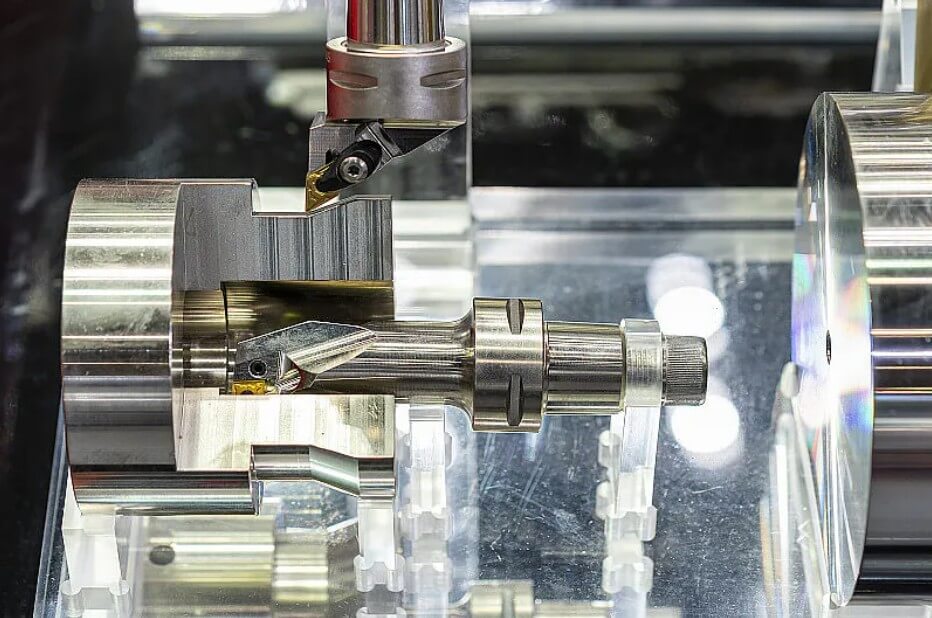
(2) disk parts CNC turning processing
Disk CNC turned parts are characterized by the opposite of shaft parts, its diameter is greater than the length, usually need to process the end face and external round.Disk parts are relatively simple to clamp, generally use three-jaw chuck clamping can be.
In terms of tool selection, disk parts end face machining usually use end face turning tool, external round machining using external turning tool. The choice of cutting parameters also need to be adjusted according to the material and size of the parts to ensure processing efficiency and accuracy.
(3) sets of parts of CNC turning processing
Sets of CNC turned parts with hollow thin-walled structure, often play a supporting or guiding role. Its characteristics include high borehole and external coaxial requirements, thin wall deformation, processing needs special attention to rigidity and chip removal problems. Clamping commonly used three-jaw self-centering chuck or four-jaw single-action chuck to ensure coaxiality and perpendicularity.
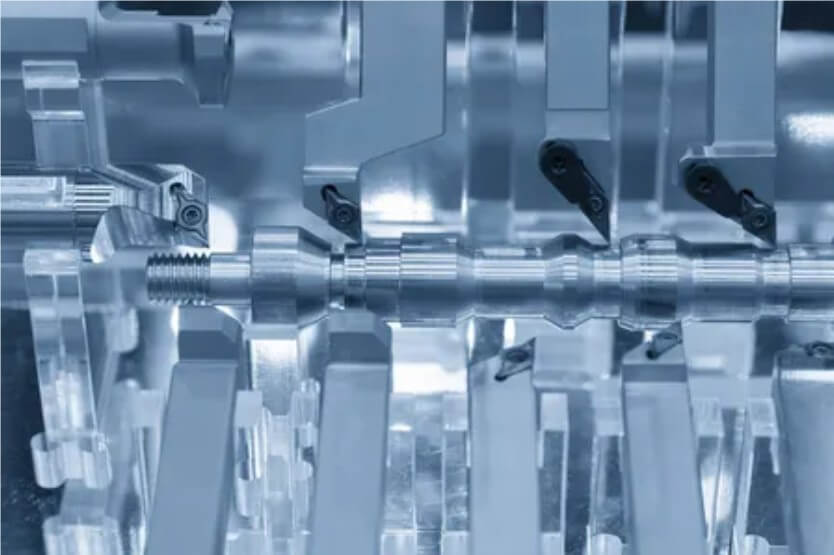
Tool selection, drilling commonly used twist drill, turning holes with internal turning tool, reaming holes with appropriate tolerance reamer, to ensure machining accuracy and surface quality. Cooling and lubrication, according to the material characteristics of the cutting fluid selection, in order to improve tool life and processing results.
4.CNC turning processing in the CNC technology analysis
(1) Tool management
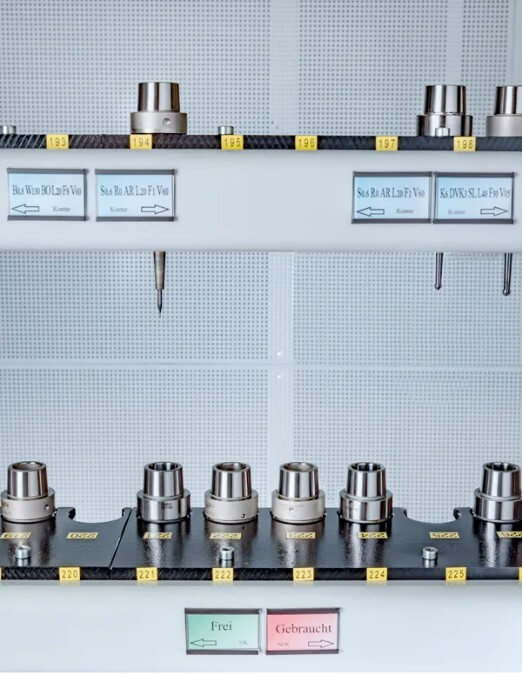
1) Tool selection
Tool management is a crucial part of CNC turning processing, reasonable tool management can not only extend tool life, but also improve processing efficiency. First of all, the tool selection needs to be based on the characteristics of the processed material, the shape of the workpiece and the processing requirements to determine. For example, the processing of high hardness materials should be selected when the good wear resistance of the tool, while the processing of precision parts need to choose high-precision tools.
2) Tool installation
Secondly, the tool installation and tool setting must be carried out accurately to ensure that the position and angle of the tool meets the process requirements. Commonly used tool setting methods include mechanical tool setting, optical tool setting and automatic tool setting, etc., of which the automatic tool setting technology is widely used in modern CNC turning machining due to its high efficiency and accuracy.
3) Tool wear monitoring and replacement
In addition, tool wear monitoring and replacement is also an important part of tool management. By real-time monitoring of tool wear and timely replacement of badly worn tools, machining quality problems caused by tool problems can be effectively avoided.
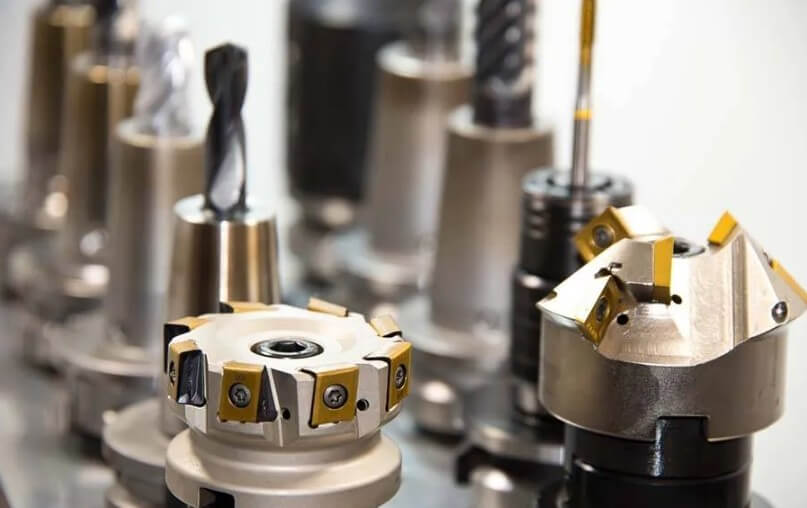
(2) Writing of machining program
Machining program is the core of CNC turning processing, and its preparation and optimization directly affects the processing efficiency and product quality.
When writing the machining program, first of all, according to the parts drawings and process requirements to determine the processing route and process parameters. Then, the use of CNC programming language (such as G code, M code, etc.) will be transformed into a machine-recognizable instruction sequence. Program writing process needs to pay attention to the setting of the coordinate system, tool path planning, cutting parameter settings and other key elements.
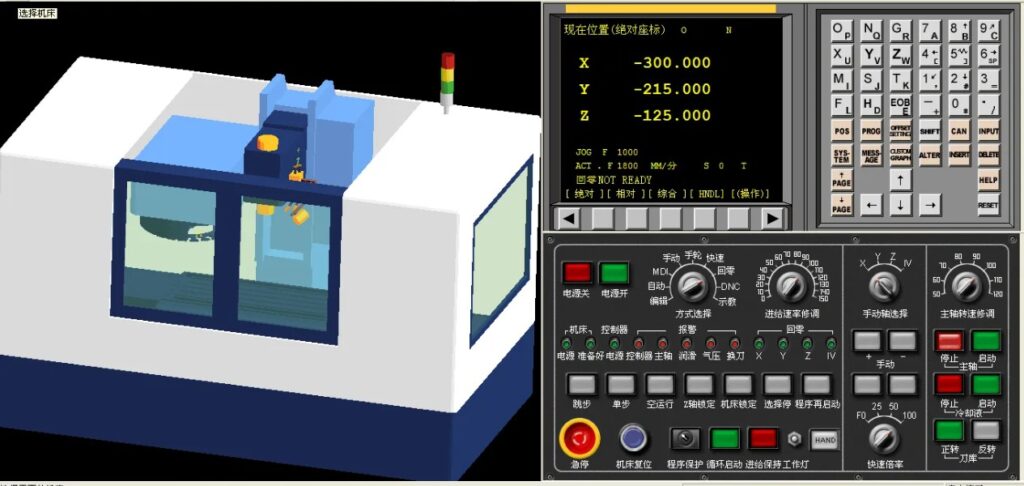
(3) Optimization of the machining program
Optimizing the machining program is an important measure to improve machining efficiency and quality. Common optimization methods include:
1) Simplify the program structure:
By reasonably planning the tool path, reduce unnecessary empty strokes and repetitive actions, simplify the program structure and improve machining efficiency.
2) Optimize cutting parameters:
According to the machining material and tool characteristics, reasonably select the cutting speed, feed and depth of cut and other parameters to obtain the best machining results.
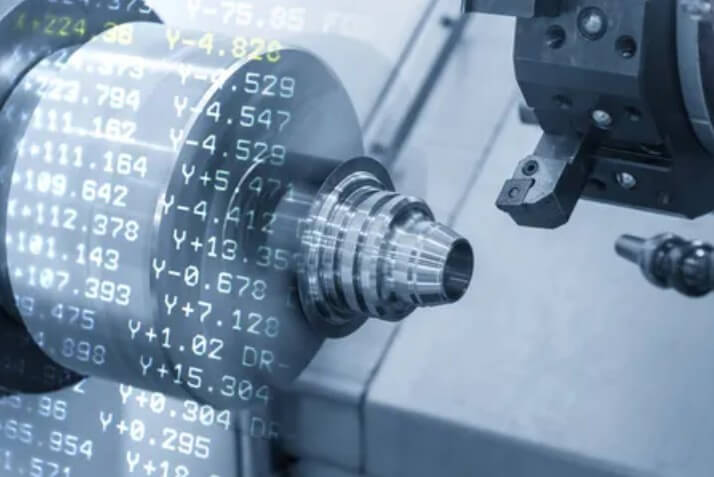
3) Application of macro programs:
Macro program is a parametric programming method that can realize the machining of complex shapes and the automation of the process. By applying macro programs, the programming work can be greatly simplified and the machining efficiency can be improved.
4) Application of post-processing technology:
Post-processing technology can convert the tool position file generated by general-purpose CAM software into a machining program for a specific machine tool. By optimizing the post-processing program, the adaptability and machining accuracy of the program can be improved.
Summary:
In summary, tool management and machining program writing and optimization are indispensable CNC technology links in CNC turning parts processing. Only by continuously strengthening the technical research and application of these aspects can we push to provide more efficient and precise CNC turned parts for the modern manufacturing industry.
5.Summarize
CNC programming plays a vital role in machining CNC turned parts. By continuously optimizing the CNC program, the processing efficiency and part quality can be significantly improved. In the future, with the continuous progress of CNC technology, CNC programming will be more intelligent, bringing more convenience for processing CNC turned parts.