A Comprehensive Guide to CNC Turning
CNC turning is a basic manufacturing method that revolves around the high-speed rotation of a bar of raw material. As the material rotates, a cutting tool precisely shapes it, removing excess material to achieve the desired shape. Unlike other cutting methods where the tool itself moves and rotates, in CNC turning it is the workpiece that rotates during the cutting operation.
The process is widely used to manufacture a variety of components, including engine parts, shafts, bushings, and gears. CNC turning offers distinct advantages over manual turning, such as greater consistency, repeatability, and efficiency. CNC turning also involves various types of machine tools, including lathes, turning centers, and Swiss-type lathes. Choosing the right machine tool and cutting tool depends on the specific workpiece requirements and the desired end product.
1.What is the turning process like?
CNC turning is a versatile machining method that is typically used to machine cylindrical workpieces. However, its application is not limited to cylindrical shapes, but also includes square or hexagonal raw materials. The workpiece is securely clamped in place using a “chuck” that rotates at an adjustable RPM (revolutions per minute).
Compared to traditional lathes, modern CNC lathes use numerical control technology to ensure precision and efficiency. Thanks to computer program monitoring, the process is constantly monitored and fine-tuned to provide meticulous and precise results.
Equipped with a variety of tools, spindles, and adjustable speed settings, these modern CNC lathes offer a wide range of machining capabilities. In addition, the diversity of cutting tool sizes and shapes allows for the creation of a wide range of geometries. In particular, tubular and circular shapes benefit the most from CNC turning technology.
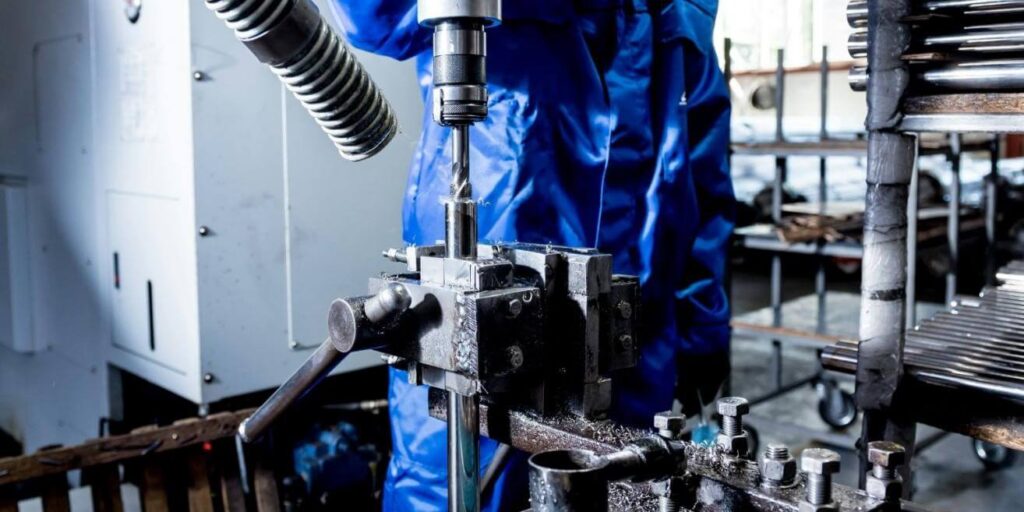
2.What is the difference between CNC milling and turning?
When delving into the world of CNC machining, it is crucial to understand the subtle differences between CNC milling and turning. The core mechanisms of these processes are different, and some tasks are better suited to milling, while others are better suited to turning.
There are several key factors that influence the choice between milling and turning:
1) Part Shape and Size
The specific contours and dimensions of the part play a key role in determining whether CNC milling or turning is a more appropriate method.
2) Material Composition
The type of material used is another key consideration that affects the selection of the most appropriate machining process.
3) Number of parts
The number of parts required is an important factor. Depending on the production volume, different machining processes may be more efficient or cost-effective.
4) Desired surface finish
The surface finish you want to achieve is critical. Whether it is a knurled finish or a specific texture, this factor will influence the choice between milling and turning.
5) Budget constraints
Financial considerations are always a crucial aspect. The available budget will influence the decision between CNC milling and turning processes.
Ultimately, determining the most suitable CNC machining process depends primarily on the shape of the part, and secondarily on the production volume requirements. Making an informed decision based on these factors ensures the best results for your manufacturing needs.
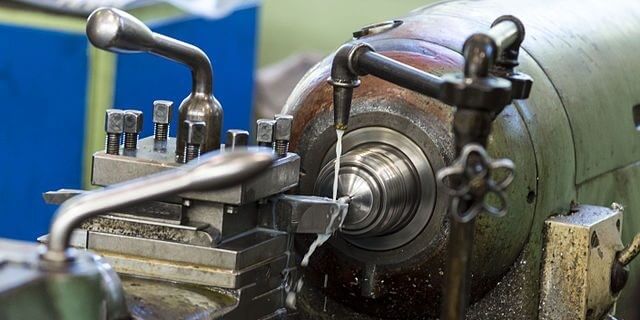
3.Benefits of CNC Turning
When the goal is to quickly and consistently produce symmetrical or cylindrical parts in large quantities, CNC turning is the preferred choice. This machining process is not only fast but also highly accurate, making it ideal for repetitive production needs. CNC turning is able to manufacture parts with excellent quality, ensuring a very smooth surface. In addition to the primary turning function, this versatile process also encompasses a variety of additional operations, including:
- Boring: This process is not limited to turning, but also includes boring, which can create precise and carefully crafted internal diameters.
- Drilling: CNC turning seamlessly integrates drilling operations, increasing its efficiency in precision manufacturing of complex parts.
- Reaming: CNC turning excels in reaming, ensuring that the final product meets the required specifications and strict standards.
- Taper turning: Taper turning is another aspect of CNC turning that demonstrates its versatility, capable of finely producing tapered components.
Whether your project requires fast production, high-quality output, or complex additional operations such as drilling, boring, reaming, and taper turning, CNC turning is an excellent comprehensive solution. Its ability to seamlessly integrate these processes makes it a reliable and efficient choice for a variety of manufacturing needs.