Applications and industries that benefit from cold forming
Cold forming, also known as cold working or cold forging, is a manufacturing process that shapes metal at room temperature. The process has become popular across industries due to its many benefits. American Flowform and Machining is a global leader in advanced cold metal forming of precision components for military, aerospace, oil and gas, and other applications.
In this article, we will explore some of the applications and industries that benefit from cold forming.
1.Automotive Industry
One of the major industries that makes extensive use of cold forming is the automotive industry. Cold-formed parts are used in a wide range of vehicles, from simple fasteners to complex engine parts, and its ability to produce high-strength parts with tight tolerances makes it ideal for automotive manufacturers.
In addition, cold formed parts are lightweight, which helps improve fuel efficiency and reduce overall vehicle weight.
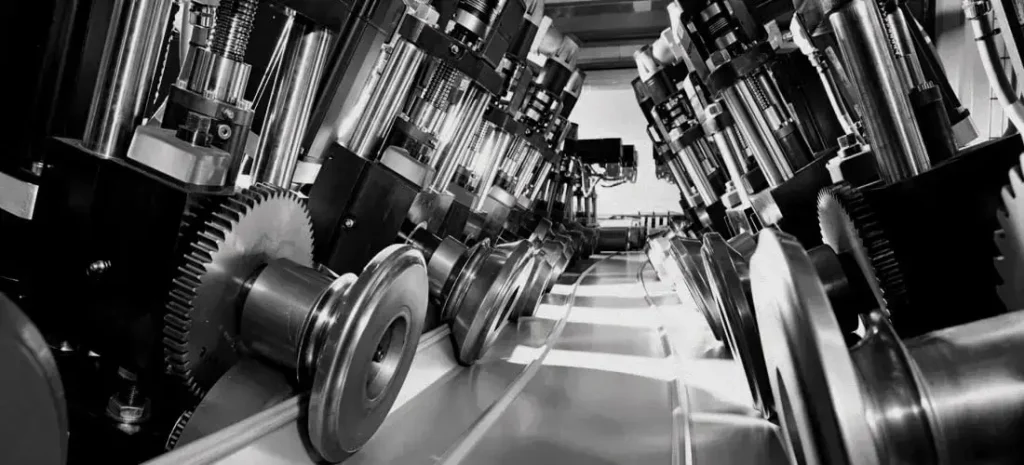
2.Aerospace Industry
The need for lightweight, high-strength components in aircraft has led to an increase in the use of cold-formed parts. The process can produce complex shapes and complex geometry capabilities, which are critical in aerospace applications.
In addition, the excellent fatigue resistance of cold formed parts ensures their reliability and longevity in harsh aerospace environments.
3.Electronics Industry
The electronics industry is another industry that has adopted cold forming. As electronic devices become miniaturized, the demand for small, precision components has grown significantly.
The process is capable of producing complex connectors, terminals, and other electronic parts with high dimensional accuracy. The ability to produce these parts in large quantities at a low cost makes it an attractive option for electronics manufacturers.
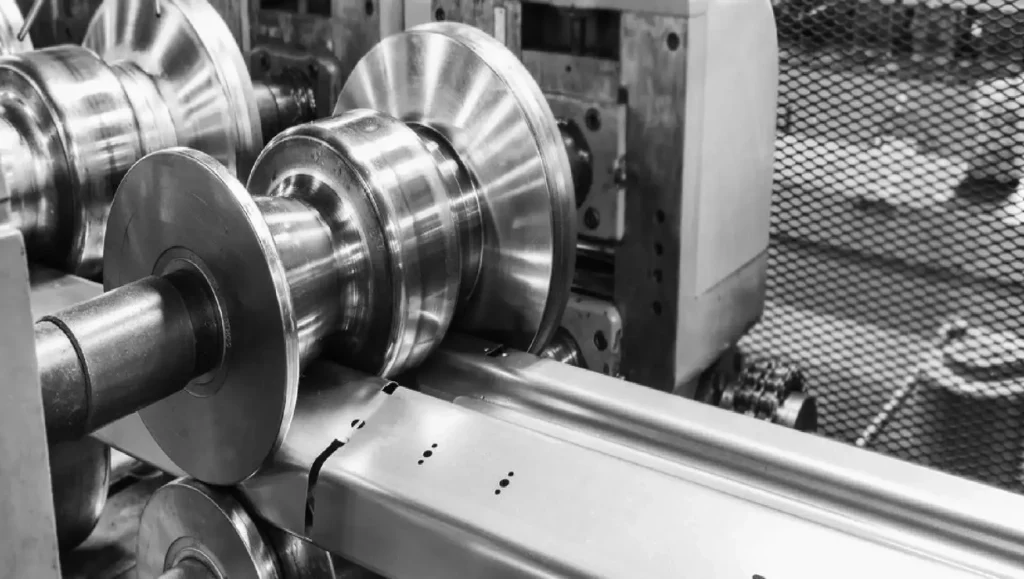
4.Medical Industry
Cold-formed parts are widely used in medical devices and implants due to their biocompatibility and corrosion resistance. Cold forming also produces complex shapes with tight tolerances, ensuring a precise fit and improving the performance of medical devices.
In addition, cold forming can produce parts with smooth surfaces, which reduces the risk of bacterial growth and is easy to clean.
5.Construction Industry
Cold-formed steel is commonly used in building structures such as beams, columns, and trusses. The high strength-to-weight ratio of cold-formed steel makes it ideal for construction projects. In addition, the ability to produce custom shapes and sizes through cold forming allows for efficient use of materials and reduces waste.
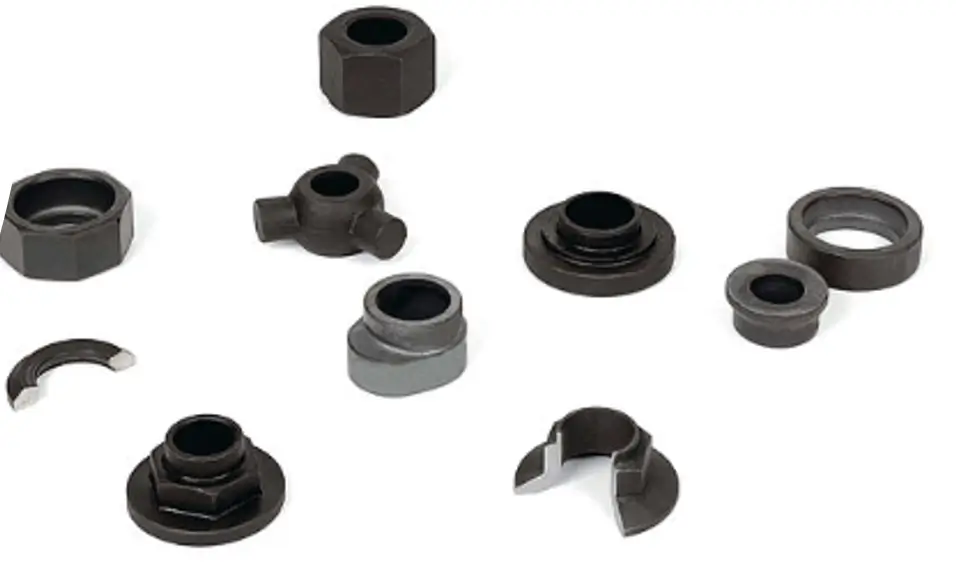
6.Energy Industry
The energy industry is another industry that benefits from cold forming. Cold-formed parts are used in renewable energy systems such as wind turbines and solar panels.
The lightweight and high-strength properties of cold-formed parts help improve the efficiency and durability of these energy systems. In addition, cold forming can produce the complex shapes required for efficient energy conversion.
7.In summary
Cold forming is used in various industries due to its many advantages, including the automotive, aerospace, electronics, medical, construction and energy industries, which benefit from the high-strength parts produced with tight tolerances.
The lightweight properties of the parts help improve fuel efficiency and reduce the overall weight of vehicles and aircraft, and precise dimensional accuracy is essential in the electronics and medical industries. The construction industry benefits from the efficient use of cold-formed materials, while the energy industry relies on cold-formed parts to build renewable energy systems.
As technology continues to advance, the scope of cold forming applications is expected to expand further, making it an indispensable manufacturing process in various industries.