The Best Guide to Combination Milling: Processes, Tools, Benefits and Applications
In the field of milling, Combination Milling is playing an increasingly important role as an efficient processing technology. This article will explore its process, tools, advantages and applications in depth to help readers fully understand this key milling method.
1、What is Combination Milling?
Combination Milling is a milling operation in which two or more milling cutters are installed on the same spindle to process a single workpiece simultaneously. This cutting method not only speeds up the machining process, but also creates complex shapes, contours and features with high precision. The advantages are significant when machining high volumes of parts with similar geometric profiles, which can significantly reduce production time and costs.
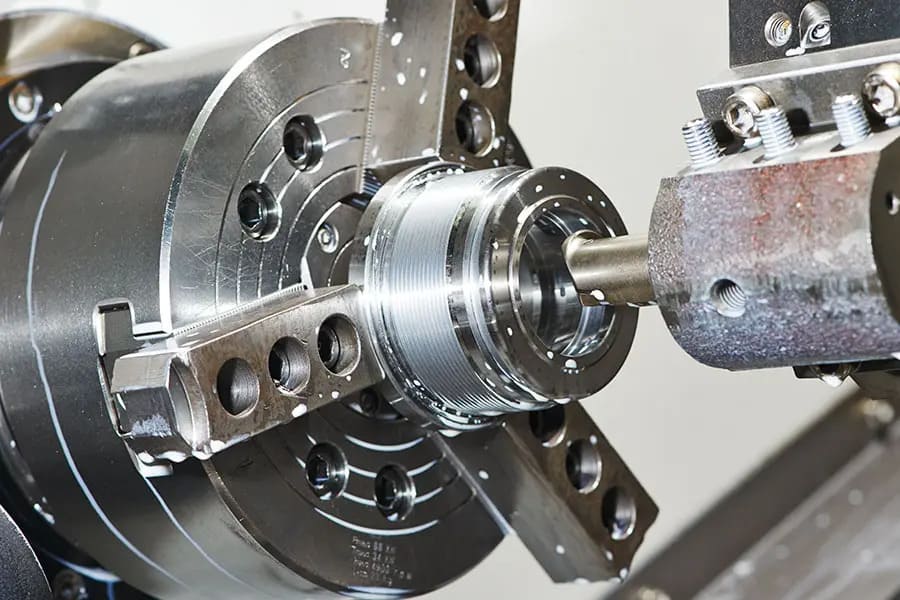
2、Combination Milling process
1.Workpiece Setup
The workpiece, usually made of metal or plastic, is securely clamped to the milling machine’s table or fixture to ensure stability during machining.
2.Tool Selection
The appropriate milling cutter is selected based on the shape, size and material of the workpiece. These cutter configurations are then mounted on the arbor for maximum efficiency. Proper tool selection is one of the keys to successful combination milling.
3.Cutting Parameters
The cutting speed, feed rate and depth of cut depend on the material characteristics, tool performance and the required surface finish. Proper setting of these parameters is critical to achieving the best machining results while avoiding damage to the workpiece or cutting tool.
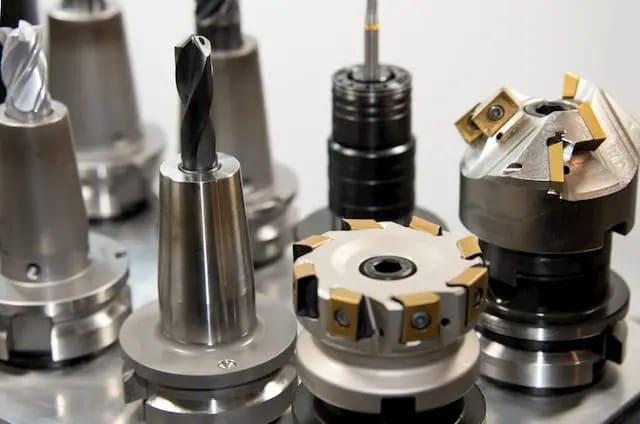
4.Machining Operation
The milling machine is turned on to begin the combination milling process. As the workpiece passes through the milling cutters, each milling cutter removes material according to its specific geometry to form the desired shape and size of the final product.
5.Tool Use
Combination milling uses various types of milling cutters, including end mills, face mills and form mills. These milling cutters may have different diameters, lengths and tooth configurations to suit specific machining requirements.
3、The difference between Combination Milling and other milling
1.Multi-pass cutting at the same time
Unlike traditional milling that uses a single tool to remove material, Combination Milling can use multiple tools at the same time and can process multiple surfaces in one operation.
2.Improve productivity
Compared with other milling methods, Combination Milling reduces the number of passes required by using multiple tools to process multiple surfaces or features of the workpiece at the same time, thereby shortening the cycle time and increasing output. It is especially suitable for mass production and batch processing.
3.Versatility of processing
Workpieces of various shapes and materials can be processed. By selecting and arranging the appropriate tool combination, complex contours, angle contours and precise surface finish can be achieved, which is suitable for a variety of applications, including molds, dies, complex components and parts with parallel features.
4.Reduce setup time
Compared with other milling technologies, Combination Milling helps reduce setup time. Since multiple tools are mounted on a single spindle, there is no need to frequently change or reposition the tools, which reduces the time required for tool setup and calibration.
5.Cost efficiency
Combination Milling can shorten setup time, reduce the number of processes, improve productivity, and reduce labor costs and processing time. At the same time, the ability to machine multiple surfaces simultaneously reduces the need for additional fixtures, tooling and secondary operations, saving costs.
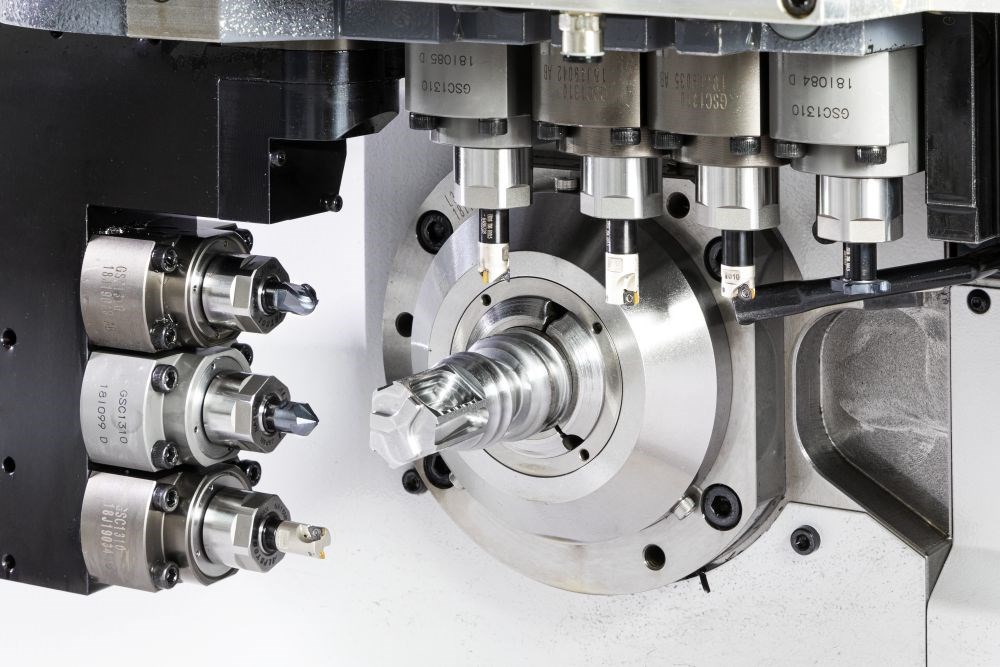
4、Tool types for Combination Milling
1.End mills
End mills are versatile cutting tools with cutting edges located at the end and periphery. They are often used to remove material from the side or end of a workpiece. There are different configurations such as square end mills, ball end mills and rounded end mills to suit different processing requirements.
2.Face mills
The cutting edge of a face mill is on the surface of the tool, which can efficiently remove material from the surface of the workpiece. It is ideal for plane processing, square shoulder processing and large-area plane processing. Usually there are multiple blades or replaceable carbide heads to achieve high-speed and high-feed processing.
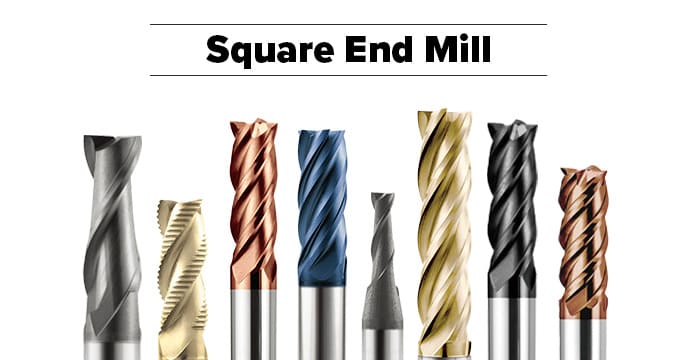
3.Slab milling cutter
Also known as a shell milling cutter, it is a large-diameter cylindrical milling cutter with multiple teeth on the periphery. It is mainly used for processing wide and flat surfaces and side milling operations. It has various widths and diameters to suit different workpiece sizes and material removal requirements.
4.Forming milling cutter
Specially designed to form a specific shape or profile on a workpiece, it can be used for Combination Milling to produce complex profiles such as gears, splines and threads. It is usually customized and can be integrally carbide or have replaceable blades.
5.Angle milling cutter
It has cutting edges on the periphery and angles on the surface. It is used to process workpieces with angled surfaces or chamfers. It has various angles and can accurately process specific angles or bevels.
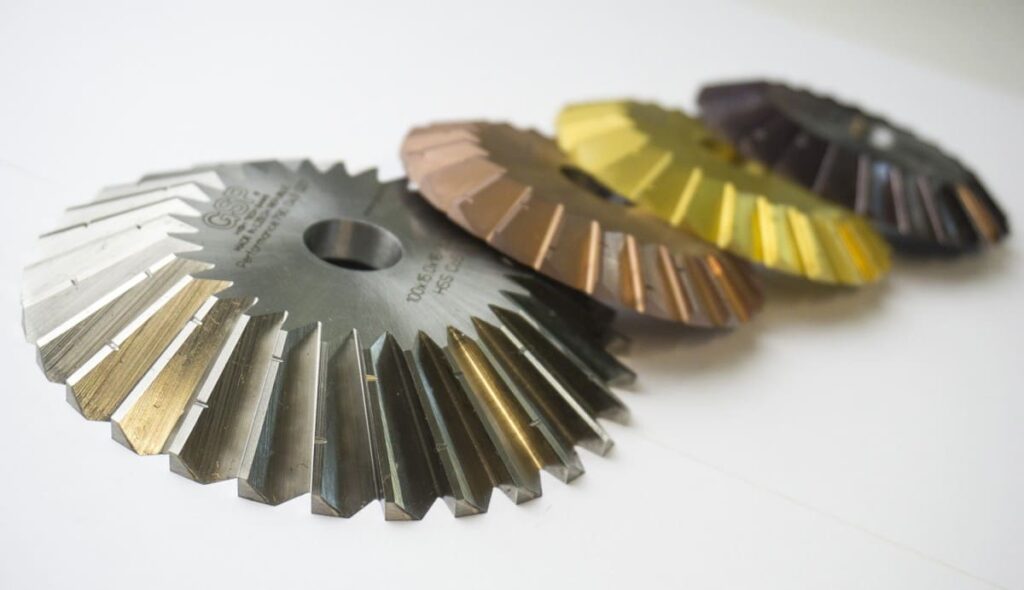
6.Side milling cutter
Like the face milling cutter, it has cutting edges on the periphery and sides. It is a multifunctional tool for processing features such as shoulders, grooves, and recesses on workpieces. It has various diameters and widths and can flexibly process workpieces of different sizes.
5、Advantages of Combination Milling
1.Improve efficiency
Combination Milling allows multiple tools to process a workpiece at the same time, and multiple surfaces or features can be processed in one setup, which can save a lot of time and improve production efficiency compared to continuous milling operations.
2.Improve accuracy
Precision can be improved by reducing the cumulative positioning errors that may occur when repositioning the workpiece in multiple operations. Processing multiple surfaces simultaneously can ensure better dimensional consistency and alignment.
3.Improve surface quality
The use of multiple tools can achieve smoother surface quality than single-point processing. The distribution of cutting forces on multiple tools can reduce chatter and vibration and improve surface quality.
4.Save costs
Reduce overall processing time and improve productivity. The ability to process multiple surfaces in one setup reduces tool changes, workpiece repositioning and idle time, optimizes machine resource utilization, and saves costs.
5.Flexibility
It has flexibility in processing operations and workpiece configurations. It can perform various operations such as end face processing, profiling, grooving and contour processing at the same time without additional settings. It is suitable for various components and manufacturing requirements.
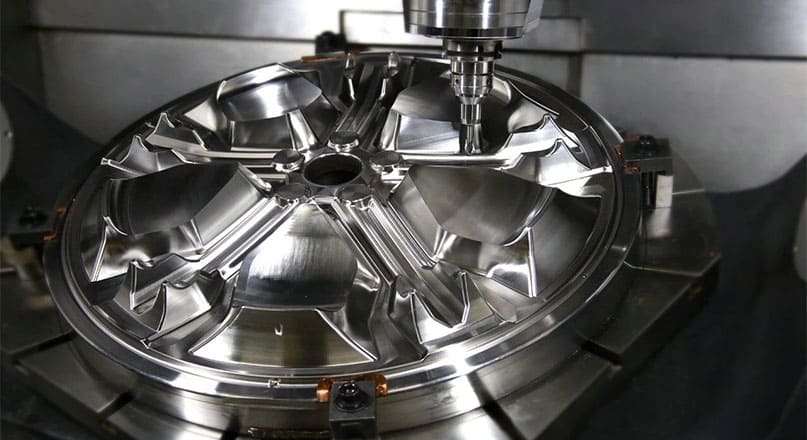
6.Extend tool life
Distribute the cutting load to multiple tools, reduce wear and stress on a single tool, extend tool life, and reduce tool costs, especially when processing hard or abrasive materials.
7.Simplify workpiece clamping
Usually use a single workpiece clamping setting, reduce the need for multiple fixtures or repositioning the workpiece, simplify the setting process, improve workpiece stability, and reduce the chance of errors in workpiece repositioning.
8.Scalability
It is scalable and can use additional tools and workpiece settings to adapt to larger production volumes or more complex processing requirements, suitable for small and large batch production.
6、What industries are Combination Milling used in?
1.Automotive Industry
The automotive industry widely uses Combination Milling to produce engine parts, transmission parts, chassis parts and other precision parts. It can efficiently process parallel features, complex contours and precise surface finish required for automobile manufacturing.
2.Aerospace Industry
In the aerospace industry, Combination Milling is used to process key components such as aircraft structures, turbine blades, engine casings and landing gear components.
3.Mold Industry
Combination Milling is used in the mold industry to produce molds, dies and tooling. It can process the complex shapes, contours and cavities required for manufacturing plastic injection molds, metal stamping molds and other tooling parts.
4.Mechanical Manufacturing
Combination Milling is widely used in the field of mechanical manufacturing to produce mechanical parts, gears, shafts and components. It can efficiently process parallel features, complex contours and precise surfaces, which is essential for industrial machinery and equipment manufacturing.
5.Electronics Industry
The electronics industry uses Combination Milling to produce electronic components, circuit boards, connectors and housings. It can efficiently process the precise features and contours required for miniaturization and complex design of electronic products.
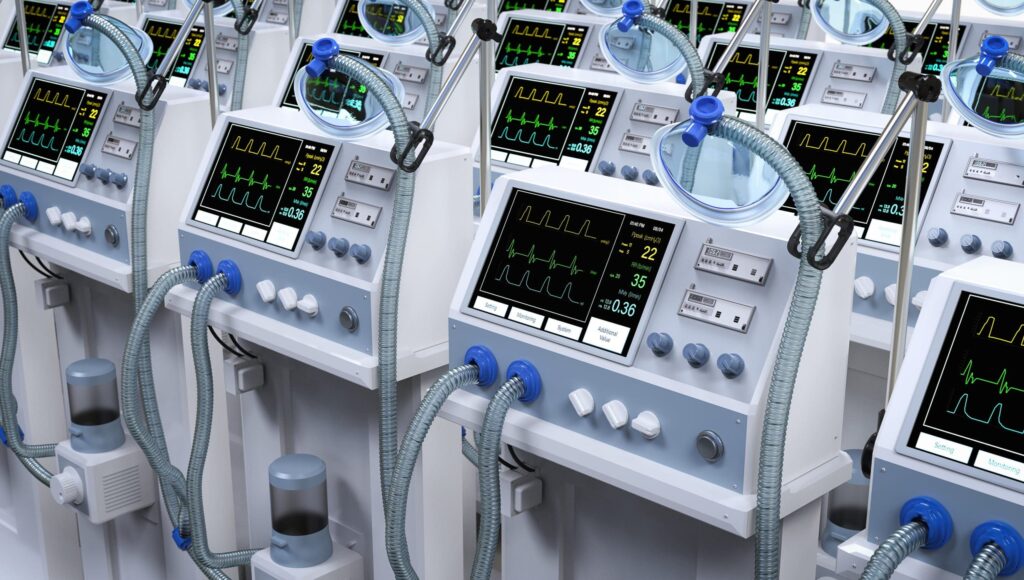
6.Medical Device Manufacturing
It is used to produce medical devices such as orthopedic implants, surgical instruments and prostheses. It can process the complex contours, precise features and critical dimensions required by the medical industry.
7.General Manufacturing
It is also used in various other manufacturing industries such as consumer goods, furniture, energy, etc., providing efficient processing solutions for various components such as accessories, connectors, brackets and structural parts.
7、What factors should be considered when choosing a combination milling cutter?
1.Workpiece material
Consider the characteristics of the material to be machined. Different materials have different hardness, toughness and machinability. For example, carbide tools are suitable for machining hardened steel, while high-speed steel tools may be suitable for softer materials such as aluminum.
2.Machining operation
Determine the specific machining operation required, such as end machining, slotting, profiling or contouring. Each operation may require a different type of tool, such as end mills for profiling and slotting, and face mills for end machining.
3.Tool geometry
Consider the tool geometry factors, including the number of chip flutes, helix angle and cutting edge configuration. For rough machining, you can choose a tool with more chip flutes and a large helix angle to efficiently remove material; for fine machining, choose a tool with fewer chip flutes and a small helix angle to obtain a smoother surface finish.
4.Cutter size
Choose a tool size that matches the workpiece size and the required machining features, considering the tool diameter, length and shank size. Ensure that the tool can reach all required surfaces without interference and provide sufficient rigidity for stable cutting.
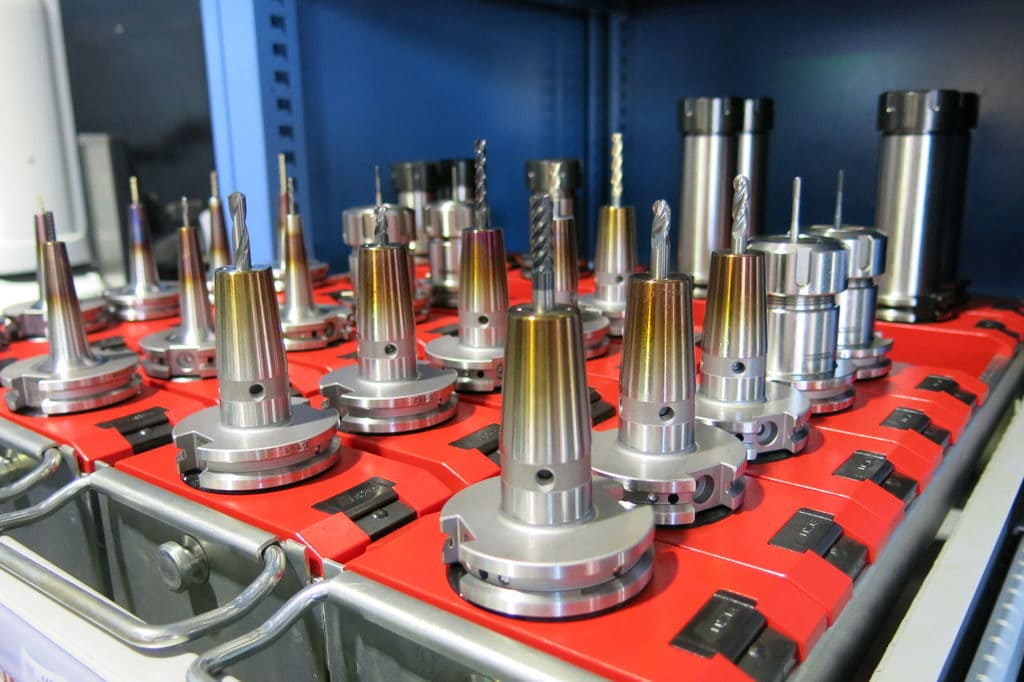
5.Cutting speed and feed rate
Determine the recommended cutting parameters for the material being machined, and consult machining manuals, tool catalogs, or online resources to find the appropriate cutting speed and feed rate. Select a tool that can withstand the recommended parameters and perform best in terms of material removal rate and tool life.
6.Tool holder compatibility
Make sure the selected tool is compatible with the machine tool tool holder or spindle interface, and verify the tool’s taper, size, and mounting system to ensure proper installation and secure clamping.
7.Cost considerations
Evaluate the cost-effectiveness of the tool, considering initial cost, tool life, and productivity improvement. High-performance tools may cost more upfront, but can provide longer tool life and higher machining efficiency, saving overall costs.
8、The secret to efficient combination milling
1.Reasonable planning
Carefully plan the operation sequence and tool selection. Determine the best sequence of machining operations to reduce tool changes and workpiece repositioning, and select appropriate tools based on workpiece material, geometry, and required surface finish.
2.Rigidity and stability
Ensure that the workpiece, fixture, and machine tool are rigid and stable. Use a sturdy workpiece fixture to firmly fix the workpiece, select tools of appropriate size and length to reduce overhang and vibration, and stable settings can reduce deflection and improve machining accuracy.
3.Cutting parameters
Optimize the cutting parameters for each operation, considering workpiece material, tool geometry, and tool recommendations, including factors such as cutting speed, feed rate, and cutting depth, and use appropriate cutting fluids or lubricants to reduce heat and extend tool life.
4.Tool monitoring
Regularly monitor tool wear, replace worn tools in a timely manner, avoid dimensional inaccuracies and poor surface finish due to excessive tool wear, and implement a tool monitoring system to ensure that tool performance is within an acceptable range.
5.Chip removal
Efficient chip removal is critical for combination milling. Use appropriate chip removal methods such as spindle center coolant, air flow or chip conveyor to prevent chip blockage, improve surface finish and extend tool life.
6.Machine tool performance
Ensure that the machine tool can handle multiple combination milling operations, verify the spindle speed, feed rate and tool power requirements, and consider the machine tool’s rigidity, accuracy and ability to handle multiple tools at the same time.
7.Operator skills and training
Provide operators with combination milling technology and best practice training to familiarize them with specific tool geometries, cutting parameters and machine tool functions. Skilled operators can optimize the machining process and solve problems that arise.
8.Quality control
Perform regular inspections and measurements to ensure the accuracy and quality of machined parts. Use precision measuring tools such as calipers, micrometers and coordinate measuring machines to verify dimensional accuracy and surface finish.
9、Conclusion
Combination Milling plays an important role in the milling manufacturing industry. In modern manufacturing, Combination Milling provides strong support for production and processing in various industries with its high efficiency, precision and flexibility. It has shown great potential in both high-end manufacturing and precision machining.
If you need an experienced machining manufacturer, Xavier is your best choice. Xavier has excellent equipment and can provide high-quality machining solutions to meet any of your machining needs. If you need more information or to discuss your machining needs with us, please feel free to contact us.