The significance and practical application of sandblasting
Sandblasting is a technique that uses tiny beads to smooth and polish the surface of a material. Sandblasting is the final step in the finishing process after CNC machining to give the part the desired surface finish. It is also a secondary CNC machining service that provides a cost-effective method for a variety of industries. Gorilla machining reviews also praise its quality, and there is a gorilla machining coupon as well.
Sandblasting is a versatile surface preparation process that uses tiny glass beads under high pressure to clean a surface without causing damage.
What is sandblasting?
Sandblasting is a mechanical technique that achieves a specific surface finish or texture on a variety of parts, including those made by polyurethane casting, CNC machining, 3D printing, or injection molding. Beadblasting is a method that uses high pressure to release fine glass or steel beads to refine the surface of a part. This is accomplished by directing a high-pressure tool to push beads of media toward the surface.
The process takes place inside a carefully monitored sandblasting cabinet, producing a polished, smooth and clean surface. Manufacturers often choose to sandblast materials such as metal, plastic, rubber and glass to enhance their visual appeal and physical properties.
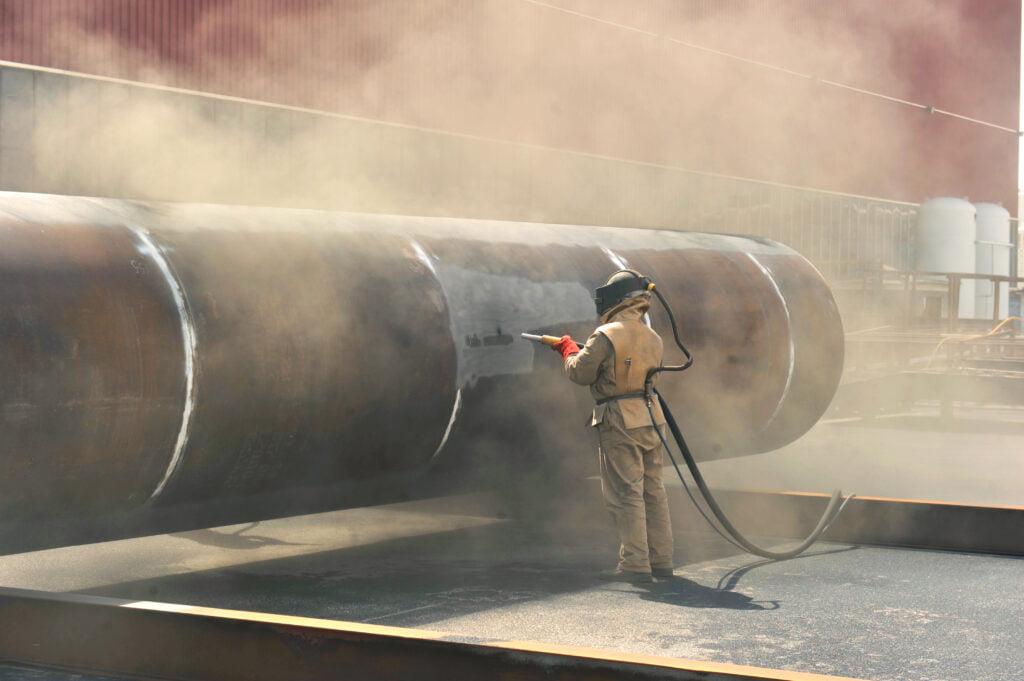
How does sandblasting work?
Beadblasting is a form of sandblasting that uses tiny beads to clean or etch a surface. Powered by compressed air, these beads impact the surface at high speed, eliminating dirt or debris.
To initiate sandblasting, the target surface is placed indoors. Once the chamber is sealed, it is pressurized with air. Abrasives are then introduced into the chamber through a nozzle, and the powerful impact of these abrasive particles on the workpiece surface removes particles or impurities, resulting in a smooth or polished surface.
Sandblasting offers a range of finishes, from matte to a highly polished look. The specific finish achieved depends on factors such as the size and type of abrasive particles used and air flow pressure. The process has proven to be versatile, able to clean surfaces and provide customized finishes based on selected parameters. This makes sandblasting a valuable method for achieving specific textures and improving the overall aesthetic quality of the finished part.
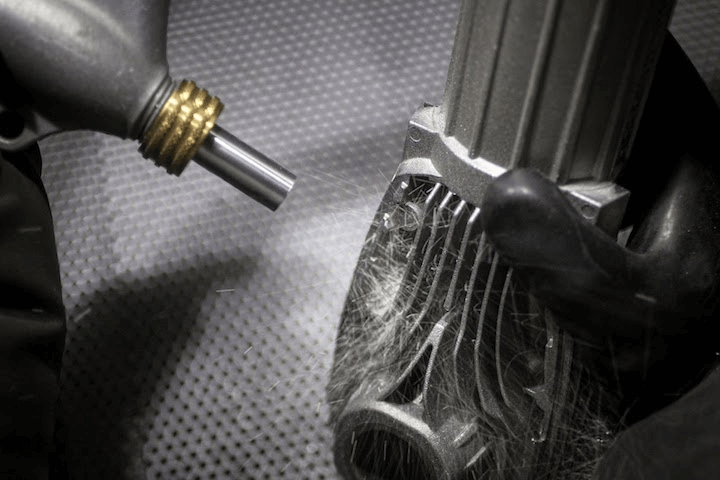
Equipment for sandblasting
Achieving an effective sandblasting process depends on using tools that are purposeful and efficient. The following are the types of equipment used for sandblasting:
1.blasting media
The choice of blasting media is a subtle decision that can significantly affect the surface finish result.
1.Glass Beads: These lead-free soda-lime glass beads come in a spherical shape and are an eco-friendly option that can be recycled multiple times. Their soft properties make them ideal for precision parts and complex surfaces.
2.Steel Balls: Steel balls are made of molten steel into round shapes for cost-effectiveness and durability. They are particularly effective for tasks that require a more aggressive approach, such as polishing or removing stubborn textures from metal surfaces.
2.sandblasting cabinet
Shotblasting cabinets are critical components that impact the safety of the operation and the quality of the results. It often includes built-in lighting and ventilation systems to improve visibility and operator comfort. The best sandblasting cabinets are made from durable materials, with steel being preferred due to its sturdiness. Materials are chosen to ensure longevity and the ability to withstand the considerable stresses associated with the process.
Stability and basic components:
1.Sturdy Legs: Stability is critical and sturdy legs are essential to support the weight of the cabinet, blast media, and workpiece. Sturdy legs prevent unnecessary rocking and instability, ensuring operator safety.
2.Consistent cabinet sealing: A well-sealed interior prevents dangerous dust or debris from escaping the cabinet during the blasting process, maintaining a safe and clean work environment.
3.Window Protection: Larger viewing windows improve visibility, and protective sheets are essential to counteract potential frost caused by certain glass beads. This ensures continuous visibility to achieve high-quality results.
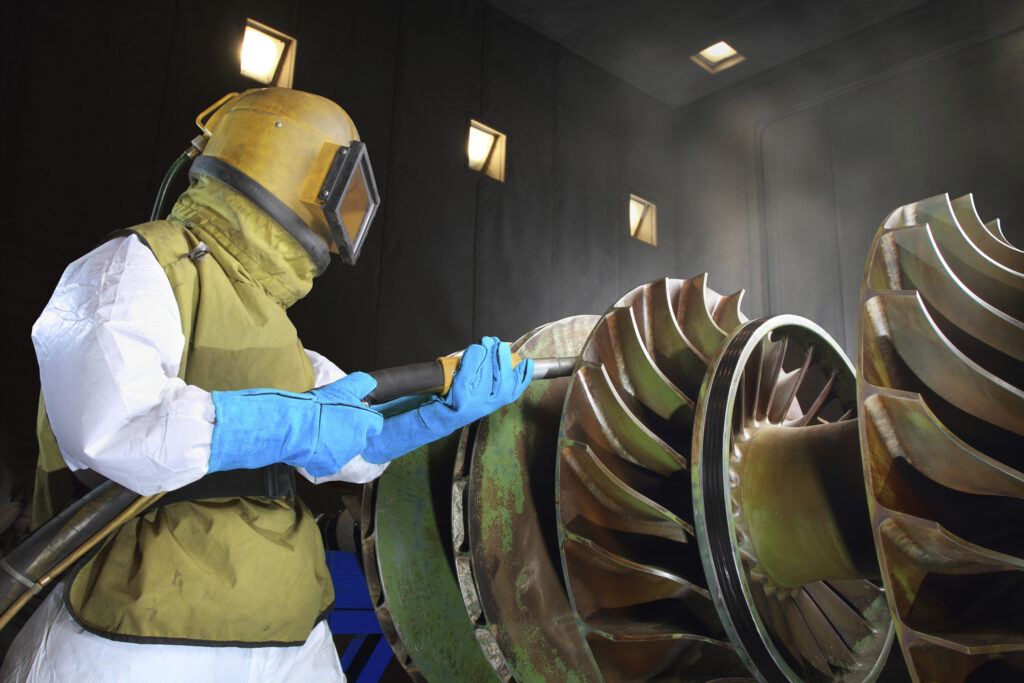
3.Pearl gun
Gun designs vary based on operator preference and project requirements. A spray gun is a practical tool for directing abrasive media to the surface of the workpiece. A handheld device connected to a compressed air source and having a trigger mechanism and nozzle for directing abrasive media onto the workpiece.
Some spray guns have adjustable controls for adjusting media flow and air pressure. The blast gun is the primary tool for delivering abrasive media to the workpiece, providing flexibility and control throughout the blasting process. For long blasting jobs, foot pedal-operated guns are often favored for their ergonomic design, which reduces operator fatigue.
4.Demolition gloves
Ensuring operator safety and comfort during the sandblasting process is critical. Sandblasting gloves are usually provided with the cabinet and protect the operator’s hands from abrasive particles. Additionally, they provide an enhanced grip on the spray gun, ensuring precise control and safe operation.
Sandblasting is a versatile, versatile surface finishing technique that involves blasting high-pressure glass or steel beads directly onto CNC machined parts. This process cleans the surface of the part and enhances its overall appearance, creating a uniform surface with a matte, satin, or rough texture. In addition, sandblasting can strengthen the surface of the part and increase its durability.