3 Key Things to Consider When Making Metal Parts
Metal part manufacturing plays a vital role in almost every industry when it comes to manufacturing mechanical components. These parts are essential to ensure that machines and tools perform as intended, and they are in increasing demand due to their durability and strength.
But how exactly do you manufacture metal parts? In this blog post, we will cover three key considerations involved in the metal parts manufacturing process, including material selection, manufacturing methods, and part requirements.
1.Selecting the Type of Material
The first consideration in metal part manufacturing is determining the material to be used for the job. A variety of metals can be used to manufacture metal parts, and these metals can be divided into two categories: hard metals and soft metals. Cost, weight, tensile strength, formability, machinability, and corrosion resistance are all important considerations when choosing a metal for a part.
Because different types of materials can affect the performance, appearance, and cost of a part, it is essential to spend some time analyzing the characteristics of each material. By choosing the right material, manufacturers can ensure that the final product meets the required specifications and performs optimally.
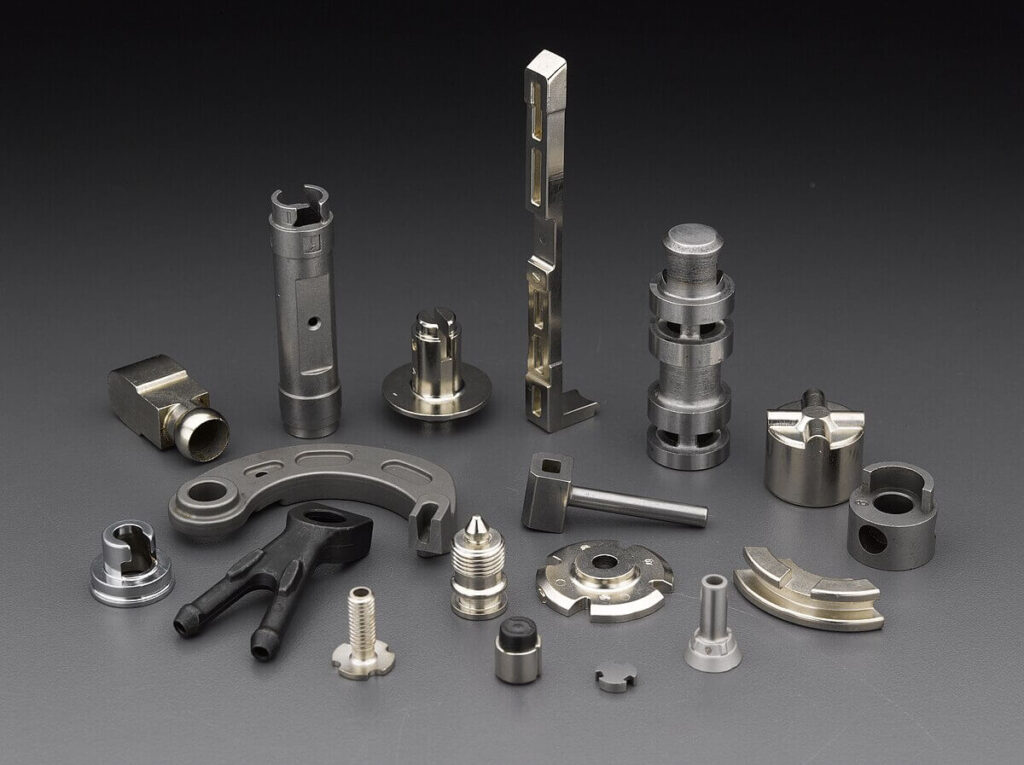
1) Soft Metals
Soft metals are prized for their malleability and lightweight properties. They are easier to machine than hard metals, making them ideal for making parts with complex shapes and tight tolerances.
- Aluminum: Because aluminum is a soft element, it is not ideal for mechanical purposes. Therefore, it is often mixed with other elements such as copper, magnesium, and zinc, and then heat-treated to improve its properties. Automobile and aircraft parts are often made of aluminum.
- Magnesium: Magnesium is a bit more expensive than aluminum, but has some unique advantages. Despite its light weight, this material has good strength and durability. It is often alloyed with aluminum and zinc and used to make parts for household electronics such as mobile phone bodies and home appliances.
- Brass: Brass is a versatile metal and is ideal for use when corrosion resistance is important. For example, many plumbing parts such as valves are made of brass. Brass is also very strong and can be used to make everything from ship parts to coins, depending on the proportion of brass used.
- Copper: Copper has a fibrous structure and is difficult to machine. However, due to its electrical conductivity, copper is an extremely important metal for power generation and is often used in wires and pipes. Like other soft metals, copper is also commonly used as an element in many different metal alloys.
2) Hard alloys
Hard metals are important functional materials in metal parts manufacturing, providing increased strength and durability. Like softer metals, hard metals also have their own unique properties and advantages.
- Titanium: The biggest advantage of titanium is its high strength. At the same time, titanium is also very light, which makes it attractive and widely used in aerospace, medical industries and military fields. Because titanium is also corrosion-resistant, it is widely used in marine applications where metal parts will be exposed to water and rain.
- Steel: Steel is an iron alloy with a carbon content of about 1%. Not only is steel a high-strength metal, but it also has great flexibility because it can be machined, stamped, roll-formed, welded, etc. This makes steel a versatile material for metal parts.
- Stainless steel: Stainless steel not only has the advantages of steel, but also has the advantage of corrosion resistance, which is due to the increased chromium content (10% by weight or more). Stainless steel parts are often used in marine applications and chemical plants.
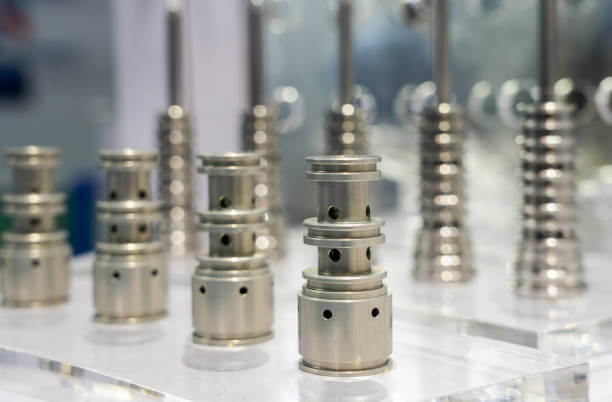
2.Determine the manufacturing method
After selecting the material, the next step is metal part manufacturing. Manufacturing methods vary depending on the type of part to be produced, and there are many factors to consider when choosing the right method for a particular job.
Various methods of part manufacturing can produce different shapes and sizes to meet the required specifications. Some common methods of part manufacturing include precision sheet metal fabrication, machining, joining, and welding. Understanding the pros and cons of each method is essential to choosing which method is best for its specific application.
The following are just a few examples. Since there are hundreds of methods for metal part manufacturing, the requirements of each part often dictate the best manufacturing process or combination of processes.
1) CNC Machining
There are many types of CNC machines. The two most common are CNC milling machines (automatic cutting machines) and CNC lathes (used for turning round or bar-shaped parts). These machining techniques are often used when manufacturing complex metal parts that require precision and detail because they are accurate and repeatable. The cost of using CNC machines can also be reduced because computer software controls many of the operations.
2) Die Casting
Die casting involves the use of molds or dies. It allows for the production of complex shapes with tight tolerances. Hardly any machining is required, and because there are no separate parts fastened together, the part can be stronger than parts made by other methods.
3) Injection Molding
Metal injection molding is another metal parts manufacturing method that requires little to no machining. With injection molding, fine metal powder is mixed with a binder material and then injected into a mold cavity. It can produce large quantities of products quickly, and it can also save costs by eliminating manufacturing steps.
4) Sheet Metal Fabrication
In sheet metal fabrication, thin sheets of metal are made into custom parts by laser cutting or bending. Compared to CNC machining, less processing time is required, and sheet metal fabrication can also handle complex projects easily because metal can be easily made into any shape.
5) Stamping
Metal stamping uses dies and stamping machines to form metal sheets into the desired shape. Stamping also often involves other metal forming techniques such as blanking and punching. Stamping is used in a variety of applications, especially those with three-dimensional designs or surface markings.
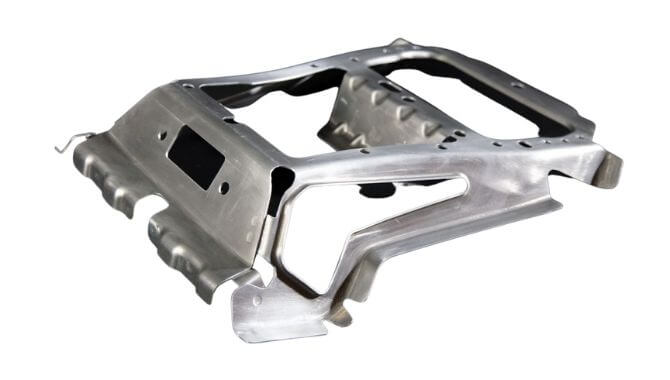
3.Understand the requirements of the part
When it comes to metal parts manufacturing, some parts are more difficult to produce than others. Simple parts can be made in a traditional machine shop using standard equipment and tools. However, custom parts with special requirements may require more complex machinery and expertise. In addition to special needs, custom parts may also require additional post-processing treatments such as surface treatment and heat treatment.
If the part features complex geometric tolerances, tight quality requirements, large overall dimensions, or tight process control, it is best to work with a professional metal fabricator with experience in manufacturing complex components.
4.Summary
Metal parts manufacturing is a complex process that involves many different considerations. If you are looking for a reliable and efficient way to manufacture metal parts, then Xavier is the right choice for you. From selecting the best material for your part to the manufacturing process itself, our team of experts takes the uncertainty out of the complex process of metal parts manufacturing – working closely with you every step of the way.