Copper Machining Processes, Designs, Grades and Considerations
Known for its electrical and thermal conductivity, copper plays a key role in modern manufacturing and is a commonly used material in CNC machining.
This guide delves into the world of copper machining, revealing its intricacies, techniques, and applications. It’s more than just shaping metal; it’s harnessing copper’s unique properties to create components that are vital to a variety of industries.
1.What is copper machining?
Copper machining refers to the process of cutting, shaping, or modifying copper materials using a variety of techniques to achieve the desired geometry and size. The process is essential for producing high-precision and complex copper parts for numerous applications.
Key Aspects of Copper Machining:
- Excellent electrical and thermal conductivity
- Ability to create complex shapes and precise dimensions
- Wide range of uses, covering various fields such as electronics, aerospace, etc.
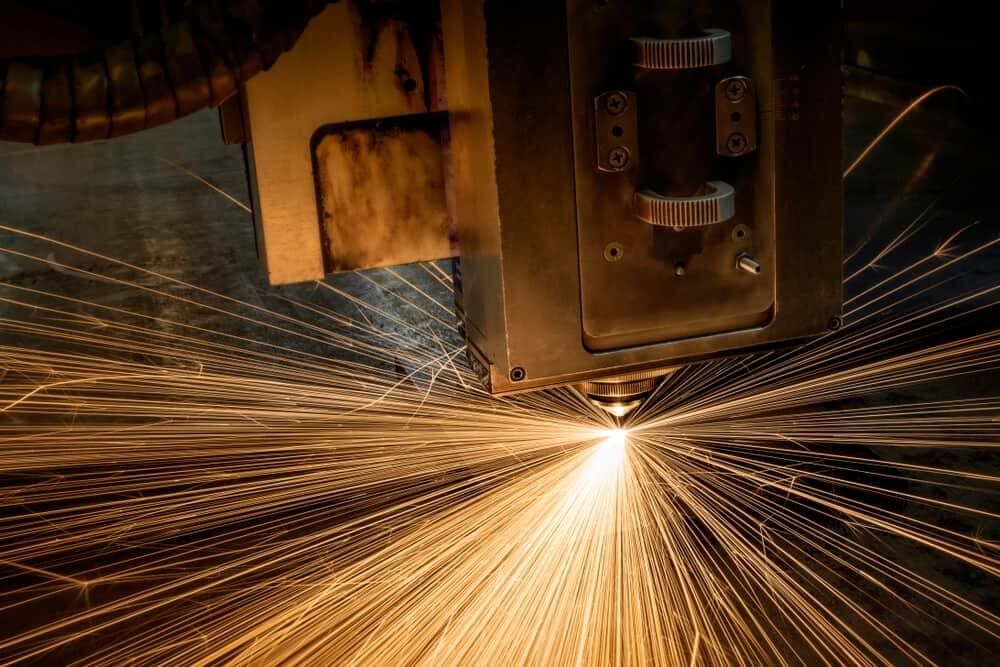
2.How is copper machining performed?
Copper machining is the removal of material from a copper workpiece to achieve the desired shape and size. This can be done through a variety of methods such as milling, turning, drilling, etc., each of which is suitable for different types of designs and requirements.
3.What are the common processes for copper machining?
Copper machining involves a variety of techniques, each of which is selected based on the specific needs of the project. These techniques cater to different design requirements and application areas.
1) CNC Milling
CNC milling is the cornerstone of copper machining, using a rotating cutting tool to carve copper. This method is unmatched in precision and is ideal for machining complex parts and fine designs.
2) CNC Turning
In CNC turning, the copper piece is rotated relative to a fixed cutting tool and is primarily used to create cylindrical parts. The technique is efficient and versatile, suitable for both internal and external machining.
3) Drilling
Drilling creates precise circular holes in copper, which is essential for parts that need to be fastened or bolted together. Both drilling and milling machines can be used for this purpose.
4) Tapping
Tapping involves cutting threads within a drilled hole so that a bolt or screw can be inserted. This process can be done manually or with a CNC drive for greater precision.
5) Grinding
Grinding uses a grinding wheel to achieve a fine surface finish and precise dimensions. The technique is often a finishing step that finishes parts that have been machined by other methods.
6) Electrical Discharge Machining (EDM)
EDM is the method of choice for copper parts that require extremely high precision. It uses electrical sparks to finely shape copper and is ideal for complex geometries.
7) Waterjet Cutting
Waterjet cutting uses a high-pressure stream of water (sometimes mixed with abrasives) to cut copper. It is particularly suitable for cutting thick copper sheets without thermal deformation.
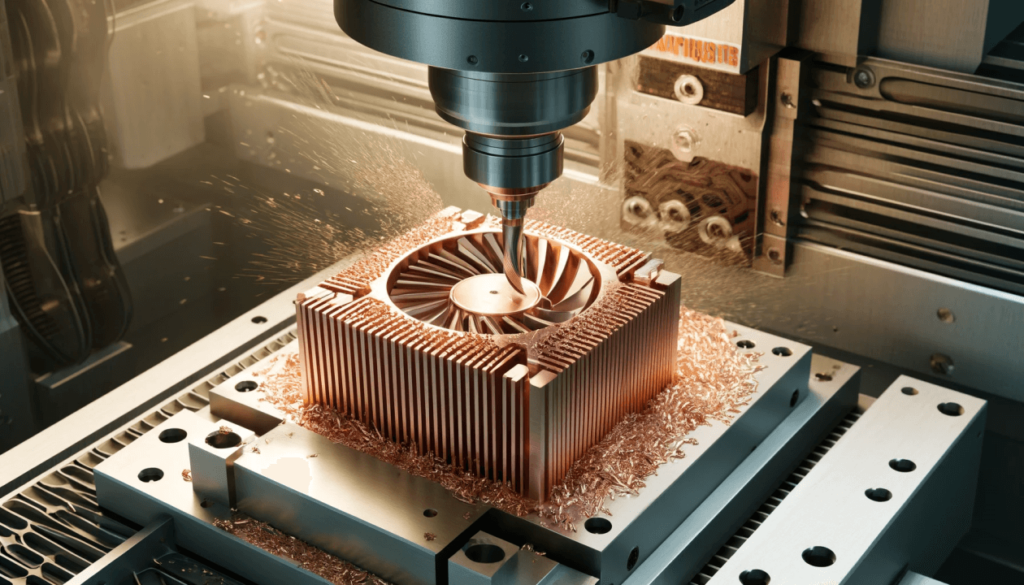
4.What are the best tools for machining copper?
In copper machining, choosing the right tool is crucial. The nature of copper is known for its plasticity and conductivity, so tools are needed that can handle its unique properties while ensuring precision and quality.
General guidelines for effective tools:
- Durability: Tools made of high-grade materials such as carbide or high-speed steel (HSS) are characterized by resistance to wear.
- Precision: Sharp, well-designed tools are suitable for complex designs and tight tolerances.
- Compatibility: Tools that work in harmony with CNC machines for optimal performance in copper CNC machining services.
5.Different grades of copper used in machining
1) Pure copper
Pure copper, also known as cathode copper, is highly conductive. It is often used in electrical applications, but can be challenging to machine due to its softness.
2) Electrolytic Copper
Electrolytic copper is a material of choice for electronic applications due to its high purity. Its electrical and thermal conductivity make it an excellent choice for heat exchangers and wires.
3) Oxygen-free Copper
Oxygen-free copper is known for its excellent electrical conductivity and ductility, making it ideal for high-quality audio-visual equipment and vacuum electronics. Its low oxygen content reduces the risk of hydrogen embrittlement.
4) Free-cutting Copper
Free-cutting copper alloys, such as those containing lead, offer improved machinability. They are often used in applications where ease of machining is important, although conductivity is slightly reduced.
5) Best Copper Grade for Machining
When it comes to machining, choosing the right copper grade is critical. Each copper grade has unique properties that affect its suitability for a particular application. For example, a free-cutting copper grade, while easier to machine, may not have the same electrical conductivity as pure copper or oxygen-free copper.
6) Copper with the Best Mechanical Strength
Among the types of copper, copper alloyed with elements such as tin or zinc generally has excellent mechanical strength. These coppers are often used to make components that require both durability and electrical conductivity.
6.Precision and Tolerances in Copper Machining
Achieving high precision and maintaining tight tolerances are key to copper machining. Factors that affect precision include:
- Machine calibration and stability
- Tool quality and suitability
- Material properties of the copper grade
- Operator skills and experience
Understanding these factors and controlling them is essential for high-quality copper machining, especially in precision-driven industries such as aerospace and electronics.
7.Applications of Copper Machining
Copper machining has a place in numerous industrial applications due to its excellent electrical and thermal conductivity.
1) Here are some notable applications:
- Electrical components: From wires to connectors, copper’s electrical conductivity makes it indispensable.
- Heat exchangers: Leverage its thermal properties for efficient heat transfer.
- Aerospace components: Require strength and electrical conductivity.
2) Selecting the right copper alloy for a specific application
Selecting the right copper alloy is a critical decision in a machining project. Factors to consider include:
- Required electrical or thermal conductivity
- Required mechanical strength
- Specific application requirements such as corrosion resistance or machinability
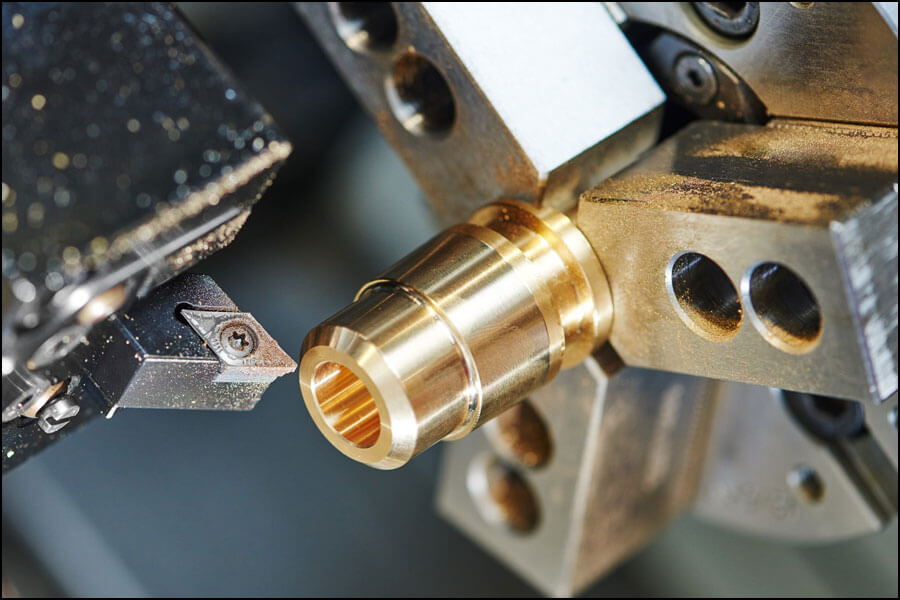
8.Key benefits and challenges of copper machining
1) Advantages of copper machining
- Excellent conductivity: Electrical and thermal conductivity.
- Versatility: Suitable for a wide range of applications.
- Recyclability: Copper can be recycled without losing its properties.
2) Challenges in copper machining
- Work hardening: Copper hardens during machining, affecting tool life.
- Thermal expansion: Managing heat generation during machining.
9.What factors need to be considered when machining copper?
1) Select the right copper material grade
Material grade affects machinability, strength and conductivity.
2) Design for manufacturability
Optimize the design to take full advantage of copper’s properties while ensuring efficient machining.
3) Set the right feed rate
Balance speed and accuracy to minimize tool wear and achieve the desired effect.
4) Choose the right tool material
Tools that can withstand the unique properties of copper ensure longevity and precision.
10.Design Considerations for Efficient Copper Machining
When designing for copper machining, consider:
- Complexity of the part: Make sure the design is feasible with available machining technologies.
- Material properties: Consider the physical properties of copper during the design phase.
- Tolerances and surface finish: Balance precision requirements with the machinability of copper.
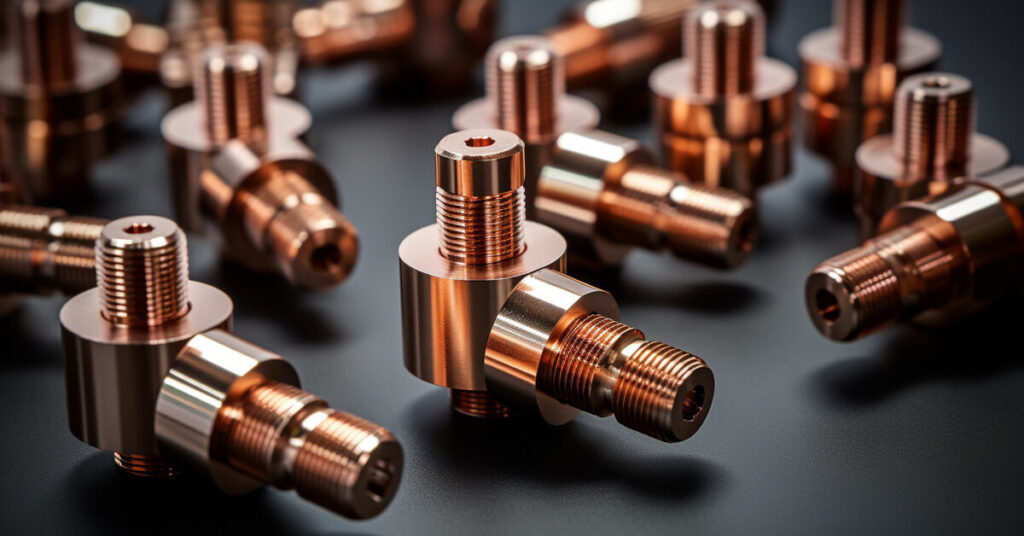
11.Key Safety Tips for Copper Machining
Safety is paramount in copper machining. Key practices include:
- Proper ventilation: Deal with copper particles and dust.
- Regular tool maintenance: Ensure tools are in optimal condition.
- Follow safety protocols: Follow guidelines for machine operation and material handling.
12.Common Problems and Solutions for Copper Machining
While copper machining offers many benefits, it also has its own challenges, such as burr formation, work hardening, and tool wear. Addressing these issues is critical to maintaining the quality and efficiency of the machining process.
- Burr formation: Often caused by improper tooling or machining parameters. Solutions include using sharp tools, optimizing feed rates, and employing proper cooling techniques.
- Work Hardening: Copper can unexpectedly harden during machining. Countermeasures include using lower cutting speeds and ensuring continuous, uninterrupted cutting.
- Tool Wear: Because copper is soft and has high thermal conductivity, tools wear quickly. Using carbide or polycrystalline diamond (PCD) tools can help extend tool life.
1) What are the costs involved in copper machining?
The cost of copper machining depends on several factors:
- Material grade: Different grades of copper, such as oxygen-free copper or electrolytic copper, have different prices.
- Complexity of machining: More complex designs require more time and precision, which increases costs.
- Tools and equipment: Advanced tools and machines increase overall expenses.
For simple tasks, the cost may be moderate; for complex or high-precision machining, the cost may be much higher.
2) Comparison of costs of different copper machining technologies
Each machining technology has its own cost impact:
- CNC milling and turning: Generally more cost-effective for large-scale production.
- EDM and water jet cutting: Costly due to the precision and equipment involved.
- Drilling and tapping: Relatively low cost and suitable for simpler operations.
3) How to ensure the quality of copper machining process?
The quality of copper machining cannot be compromised. Key quality control measures include:
- Regular inspection: Frequent inspection during machining to ensure that tolerances and specifications are met.
- Tool maintenance: Ensure that tools are sharp and well maintained to avoid defects.
- Process optimization: Continuously optimize machining parameters to achieve the best results.
- 3D printing integration: Supplement traditional machining with additive manufacturing to achieve complex designs.
4) Economic impact of copper machining
Copper machining has great economic significance. Its application in key industries such as electronics, aerospace and automotive highlights its economic value. The cost-effectiveness of machining copper, especially compared to other materials, contributes to its widespread use and industrial significance.
5) Why is copper machining so important in modern manufacturing?
Copper machining is an integral part of modern manufacturing because of its:
- Versatility: Suitable for a variety of products from electrical components to decorative items.
- Electrical conductivity: Critical in electrical and thermal applications.
- Machinability: A balance between machinability and durability makes it a top choice in many fields.
6) Alternatives to CNC machining of copper
While CNC machining is common, alternatives include:
- Manual machining: For simpler or one-off projects.
- Laser cutting: For precise, non-contact cutting of thinner copper sheets.
- Stamping and forming: Cost-effective for mass-producing copper parts.
7) Environmental and health considerations in copper machining
Like any industrial process, copper machining presents environmental and health concerns. Proper handling of copper shavings and coolants is essential to minimize environmental impact. Health aspects include ensuring adequate ventilation and protective equipment to protect against copper dust and particles.
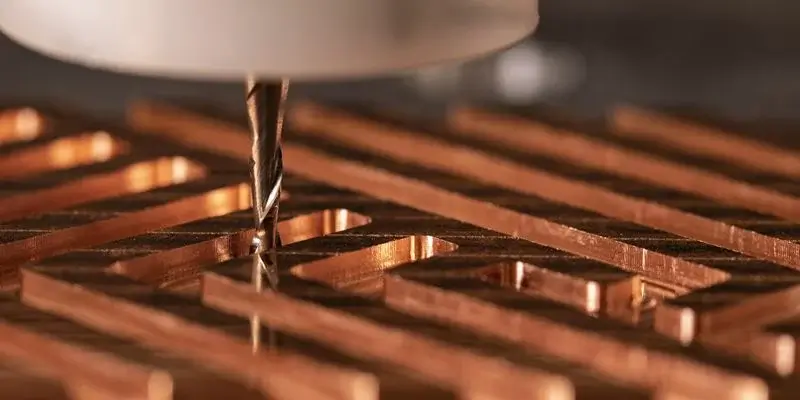
13.Conclusion
In summary, copper machining is a complex and essential part of modern manufacturing. Its versatility, conductivity, and machinability make it a valuable material across industries. Despite the challenges, advances in machining technology continue to improve its applications and efficiency.
Xavier is a leading copper machining service provider, capable of producing parts with a variety of coatings and surface treatments to suit your project requirements. We produce corrosion resistant copper machined parts and can process CNC turning or milling of solid copper rod, copper-nickel alloy and copper alloy materials.