The Importance of Precision in CNC Component Manufacturing
Precision is a critical aspect of CNC component manufacturing. Whether it is for aerospace, automotive, or medical applications, precision is essential to ensure the functionality and reliability of the final product. In this article, we will explore the significance of precision in CNC component manufacturing and how it is achieved.
Precision in CNC component manufacturing refers to the ability to produce parts with extremely tight tolerances. Tolerance is the allowable deviation from a specified dimension, and it is measured in thousandths of an inch or micrometers. Achieving tight tolerances is crucial because it ensures that the components fit together perfectly and perform their intended functions accurately.
The Main Reasons Why Precision Is So Important in CNC Component Manufacturing
One of the main reasons why precision is so important in CNC component manufacturing is the need for interchangeability. In many industries, such as automotive and aerospace, components need to be interchangeable to facilitate repairs and replacements. If a component is not manufactured with precision, it may not fit properly, leading to performance issues or even catastrophic failures. Therefore, precision is vital to ensure the compatibility and reliability of the final product.
Another reason why precision is crucial in CNC component manufacturing is the impact it has on performance. Many components, such as gears, bearings, and valves, rely on precise dimensions and tolerances to function optimally. Even the slightest deviation can result in increased friction, reduced efficiency, or premature wear. By manufacturing components with precision, manufacturers can ensure that their products perform at their best, delivering the desired performance and longevity.
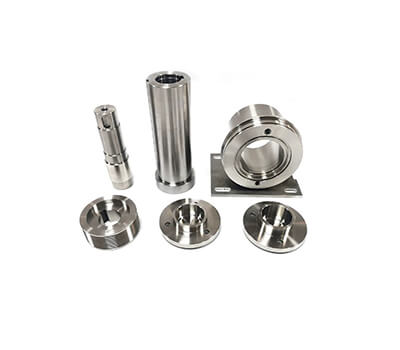
Achieving precision in CNC component manufacturing requires a combination of advanced technology, skilled operators, and meticulous quality control processes. CNC machines, or computer numerical control machines, are at the heart of precision manufacturing. These machines use computer programs to control the movement of cutting tools with incredible accuracy. They can repeat the same operation multiple times, ensuring consistent results and tight tolerances.
Skilled operators play a vital role in achieving precision in CNC part manufacturing. Their expertise and attention to detail are important because they are responsible for programming CNC machines, selecting appropriate cutting tools and monitoring the manufacturing process, which is critical to ensuring components are produced to the required precision. necessary.
Quality control processes are also integral to achieving precision in CNC component manufacturing. These processes involve inspecting the components at various stages of production to ensure that they meet the specified tolerances. Advanced measurement tools, such as coordinate measuring machines and optical comparators, are used to verify the dimensions and tolerances of the components. Any deviations from the required specifications are identified and corrected promptly to maintain the desired level of precision.
In conclusion, precision is of utmost importance in CNC component manufacturing. It ensures the compatibility, reliability, and performance of the final product. Achieving precision requires advanced technology, skilled operators, and meticulous quality control processes. By prioritizing precision, manufacturers can deliver high-quality components that meet the stringent requirements of various industries.