The Importance of Quality Control in Custom Metal Parts Manufacturing
Custom metal parts is a complex and sophisticated field that requires precision and attention to detail. Special care is required during the production process, and even the smallest mistakes can have serious consequences. To ensure excellence in custom metal parts manufacturing, quality control is critical. Strip processing is a common process used in many industries, including industrial machinery, electronics, and consumer products.
Implementing an Effective Quality Control System in Custom Metal Parts
Quality control is the process of monitoring and inspecting products to ensure that they meet specified requirements and standards. In custom metal part manufacturing, quality control involves a series of inspections and tests at each stage of the production process. These inspections are designed to identify any defects or deviations from the required specifications so that they can be promptly corrected and adjusted to avoid unnecessary cost.
One of the primary reasons why quality control is crucial in custom metal parts manufacturing is the need for precision. Custom metal parts are often used in critical applications where accuracy is paramount. Whether it is in aerospace, automotive, or medical industries, any deviation from the required specifications can lead to catastrophic consequences. By implementing rigorous quality control measures, manufacturers can minimize the risk of producing faulty parts and ensure that their products meet the highest standards of precision.
Another reason why quality control is essential in custom metal parts manufacturing is the need for consistency. Customers rely on manufacturers to deliver products that are consistent in terms of quality and performance. Inconsistencies in the manufacturing process can result in variations in the finished products, leading to compatibility issues or failures in the field. Quality control helps to identify and rectify any inconsistencies, ensuring that every custom metal part produced is of the same high quality.
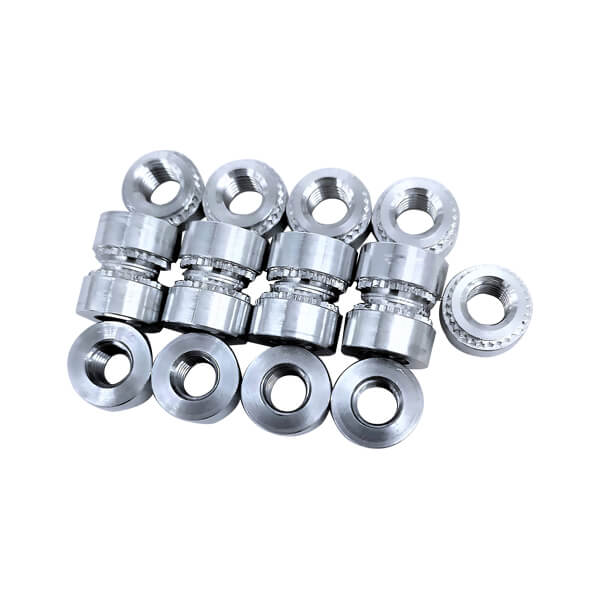
Furthermore, quality control plays a vital role in reducing waste and improving efficiency. Defective or non-conforming parts not only result in customer dissatisfaction but also lead to increased costs for manufacturers. By implementing quality control measures, manufacturers can identify and eliminate the root causes of defects, reducing waste and improving overall efficiency. This, in turn, leads to cost savings and increased profitability.
Implementing an effective quality control system in custom metal parts manufacturing requires a combination of tools, techniques, and skilled personnel. Advanced inspection equipment, such as coordinate measuring machines and non-destructive testing methods, can help identify even the smallest deviations from the desired specifications. Additionally, trained quality control personnel who are knowledgeable about the manufacturing process and the specific requirements of the custom metal parts can ensure that the necessary checks and tests are conducted accurately and efficiently.
In conclusion, quality control is of utmost importance in custom metal parts manufacturing. It ensures precision, consistency, and efficiency, while also reducing waste and improving profitability. By implementing rigorous quality control measures and utilizing advanced inspection equipment, manufacturers can deliver custom metal parts that meet the highest standards of quality and performance. In an industry where precision and accuracy are paramount, quality control is the key to ensuring excellence in custom metal parts manufacturing.