Distributed Steps of Customized Aluminum Extrusion Process
Aluminum extrusion in China occurs in direct or indirect extrusion. Extruders here come in a variety of power levels, such as Inpol, which ranges from 12.5 to 55-MN. But before starting the extrusion process, the cast aluminum bars need to be cut into small pieces. These pieces are called billets. They determine the same length for each extruded bar. Thus, the material does not go to waste. The aluminum extrusion process can be modified according to customer needs. Here, we discuss the six stages of aluminum extrusion.
Step 1: Preheating of aluminum billets and steel dies
In this stage, the billets are first heated in a gas furnace or induction furnace. This temperature starts from room temperature up to the extrusion temperature. Moreover, its range varies according to the alloy and the final temperature. From then on, the heated billets must be ductile so that they can get the desired shape. But they must be strong and keep the shape even during transportation. Then the push rods exert pressure on these billets so that they move towards the die opening.
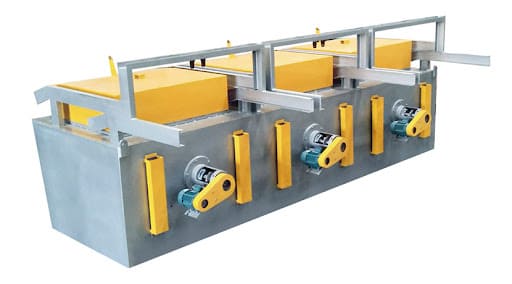
Step 2: Loading the billets into the extrusion container
In the second stage, the heated billets are then quickly transferred to the extrusion container. At this stage, the billets are ready for extrusion. After that, the punch applies pressure on them and pushes them towards the opening of the die.
Step 3: Extrusion
After passing through the die openings, the blanks enter the tool. These die openings can be changed and modified into a variety of shapes and sizes. This stage is like pressing cookies. Here, the profiled discs create a variety of cookie designs. Subsequently, the bars with the desired shape come out of the pressing container.
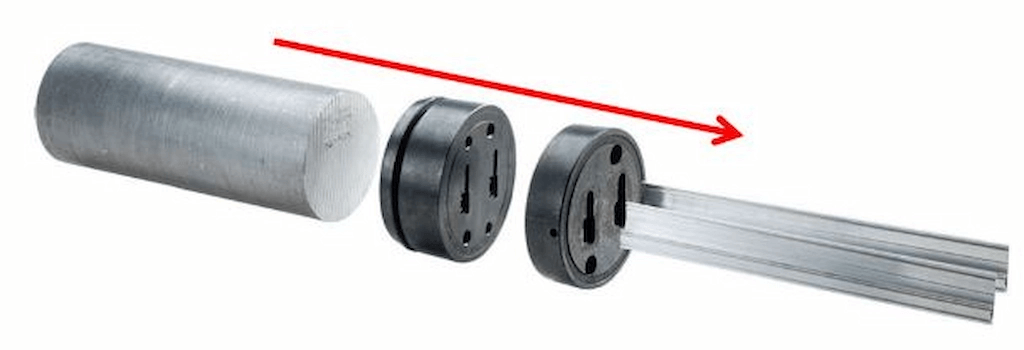
Step 4: Controlled Cooling
After extrusion, the bars, tubes or profiles are cooled rapidly. After leaving the press, the complete bars are placed in a water bath. This guarantees a uniform quenching of the heated aluminum. Moreover, this quenching process is essential for the required mechanical properties and adequate microstructure. Therefore, the cooling process is necessary to eliminate any danger of deformation of the material.
Step 5: Stretching the Bars
After cooling, the bars are cut into the required lengths. During the cutting process, pullers grab them. These pullers are usually placed on a beating table. They allow the bars to cool further. At this stage, the extruded bars undergo a strengthening process. This process stretches them and eliminates the internal tensions within the bars, ultimately ensuring their mechanical properties.
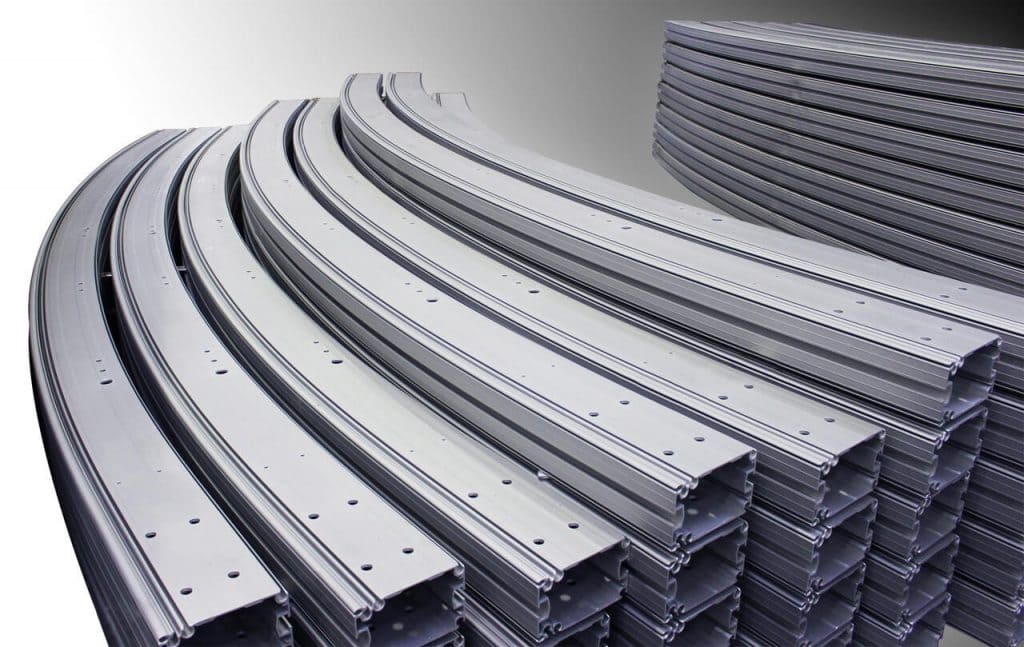
Step 6: Cutting and Final Packaging
This is the final stage of aluminum extrusion. At this stage, the reinforced bars are again cut into the required lengths specified by the customer. Thus, the aluminum bars have T1/T4 temper characteristics. However, they need to have T5/T6/T66 temper. Furthermore, this aging process strengthens the bars/profiles or tubes again until they meet the mechanical properties of the specified alloy.