cut aluminum composite material |
A comprehensive guide to A comprehensive guide to cut aluminum composite material
Cut aluminum composite material is one of the common processes in modern manufacturing. It is widely used in aviation, automobiles, construction and other fields due to its light weight, high strength and excellent processing performance. However, cut aluminum composite material is not an easy task. It requires choosing the right cutting technology and paying attention to some key matters. This article will provide you with a comprehensive guide to help you master the core points of cut aluminum composite material.
1.Definition and Importance of Aluminum Composites
Aluminum composites are an advanced engineering material composed of an aluminum matrix and reinforcing materials (such as fibers, particles, etc.). This material combines the light weight of aluminum and the high strength of reinforcing materials, and has higher strength, stiffness and wear resistance than single aluminum. In modern industry, aluminum composites are widely used in aviation, aerospace, automobiles, construction and other fields due to their excellent performance. They are an indispensable and important material in modern industry and high-tech industries.
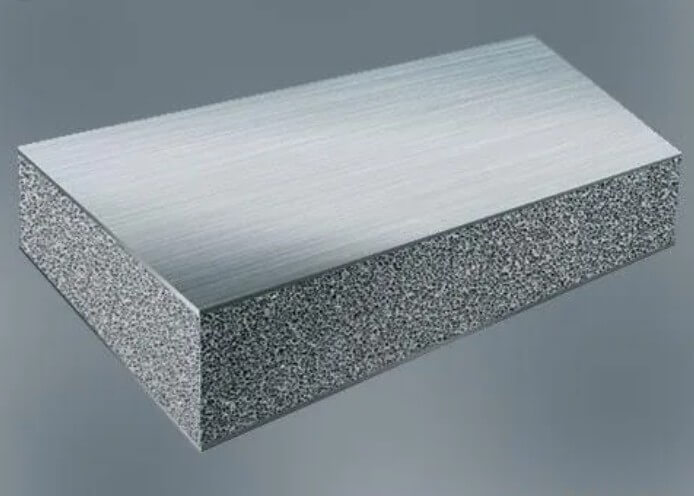
2.Types and characteristics of aluminum composites
Aluminum composites are a multiphase material composed of aluminum and other materials. They are compounded by physical or chemical methods. They have many excellent properties and are widely used in various fields of modern industry. The following are the main types of aluminum composite materials and their characteristics:
(1) Aluminum-based composite materials:
This type of material uses aluminum as the matrix and adds reinforcing materials such as silicon carbide (SiC), aluminum oxide (Al2O3) and other particles or fibers. Aluminum-based composite materials have high strength, high stiffness, good wear resistance and good dimensional stability, and are suitable for aerospace, automotive and electronic equipment.
(2) Aluminum honeycomb composite materials:
This material uses aluminum honeycomb core as the base material and other materials such as PVC, PET film, solid wood veneer on the surface. Aluminum honeycomb composite materials have the characteristics of light weight and high strength and are widely used in building decoration, furniture manufacturing and transportation.
(3) Aluminum-plastic composite materials:
Aluminum-plastic composite materials are made of aluminum plate and plastic core material. They have both the strength of aluminum and the corrosion resistance of plastic. They are often used in building exterior walls, roofs and interior decoration materials.
(4) Aluminum laminated composite materials:
This material is made of multiple layers of aluminum and other materials alternately laminated, such as aluminum-steel laminates, aluminum-titanium laminates, etc. Aluminum laminated composites combine the advantages of each component, have excellent mechanical properties and corrosion resistance, and are suitable for applications in special environments.
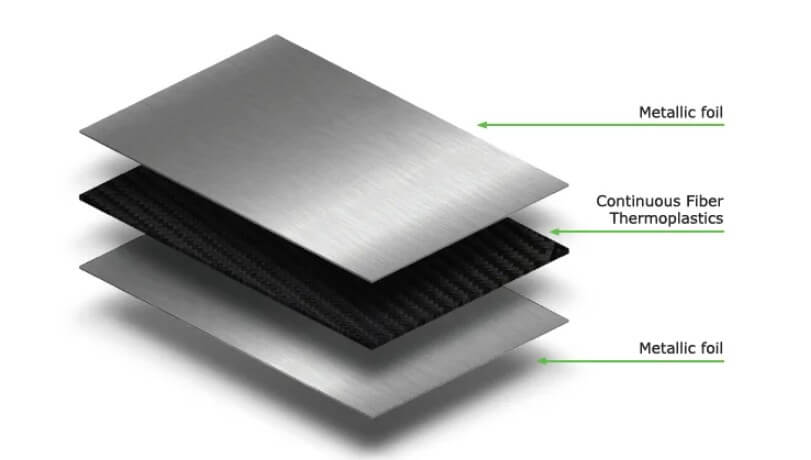
3.Common methods for cut aluminum composite material
(1) Mechanical cutting
Mechanical cutting includes methods such as sawing, turning and milling. These methods separate materials through physical contact and mechanical force and are suitable for the preliminary processing of most aluminum composites. This method is simple to operate and low in cost, but it is easy to generate burrs and heat, which may lead to a decrease in material properties.
In order to reduce thermal damage and burrs during the cutting of aluminum composites, high-precision CNC cutting machines and suitable coolants can be used. For example, when cutting aluminum honeycomb composites, CNC sawing machines and suitable coolants can be used to reduce thermal damage and burrs during the cutting process.
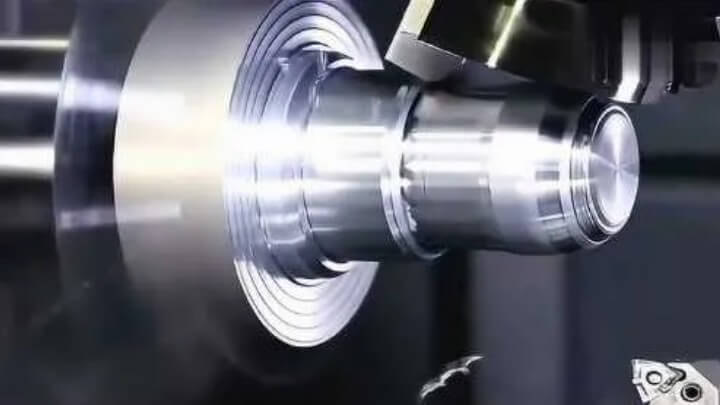
(2) Laser cutting
Laser cutting uses a high-energy-density laser beam to cut aluminum composites, which has the characteristics of high precision and high efficiency. Laser cutting can minimize the heat-affected zone and is suitable for cutting complex shapes.
However, laser cutting equipment is expensive, and smoke and harmful gases may be generated during the cutting process, requiring good ventilation and protective equipment. For example, when cut aluminum composite material, laser cutting can significantly improve cutting accuracy and efficiency, but it is necessary to pay attention to controlling cutting parameters to reduce thermal damage and smoke generation.
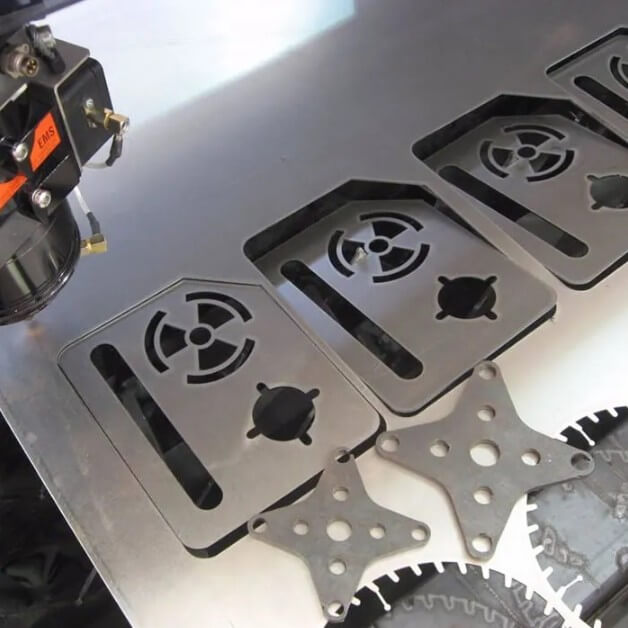
(3) Plasma cutting
Plasma cutting uses a high-temperature plasma arc to melt and blow away the material, and is suitable for thicker aluminum plates. Plasma cutting is fast and relatively low in cost, but the cutting accuracy and edge quality are not as good as laser cutting.
In addition, plasma cutting of aluminum composites will produce strong light radiation and harmful gases, and corresponding protective measures need to be taken. For example, when cutting thick aluminum plates, plasma cutting can significantly increase the cutting speed, but it is necessary to pay attention to controlling cutting parameters to reduce the damage of light radiation and harmful gases to operators.
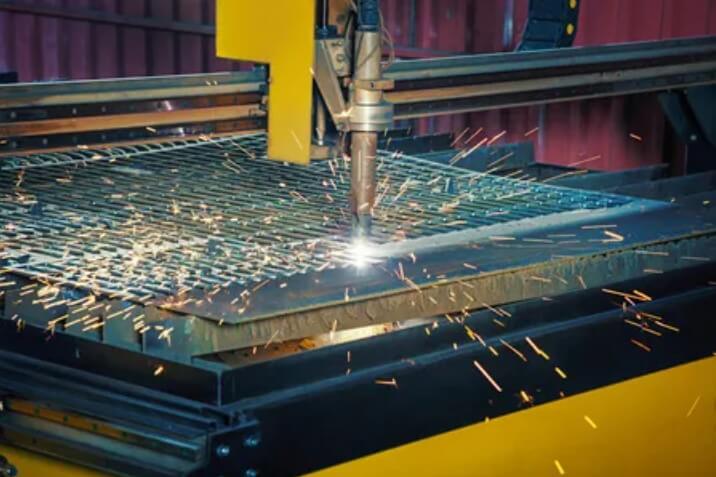
Water jet cutting uses high-pressure water flow or water flow with abrasive to cut aluminum composites, and is suitable for aluminum composites of various thicknesses. This method has no heat-affected zone and good cutting edge quality, but the cutting speed is slow and the equipment cost is high.
Water jet cutting is particularly suitable for cut aluminum composite material and sensitive materials, such as aluminum composites with fiber reinforcement. For example, when cut aluminum composite material containing fiber reinforcement, water jet cutting can significantly improve the cutting edge quality, but it is necessary to pay attention to controlling the cutting parameters to reduce the cutting speed and equipment cost.
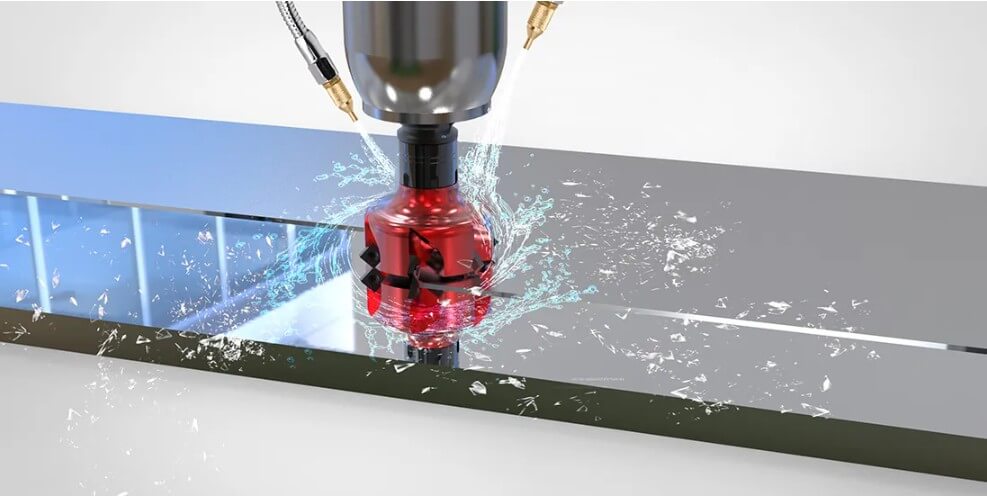
4.Technical challenges in cut aluminum composite material
There are many technical challenges when cut aluminum composite material. The following are some of the key points:
(1) Challenges brought by material properties:
Aluminum composites are usually composed of aluminum matrix and reinforcement materials (such as carbon fiber, boron fiber, etc.). This combination gives the material high specific strength, high specific stiffness and good fatigue resistance. However, these characteristics also make the cutting process difficult. The high hardness of the reinforcement material will lead to increased tool wear, affecting the cutting accuracy and surface quality.
(2) Thermal damage during cutting:
When cut aluminum composite material, due to the high thermal conductivity of the material, a large amount of heat will be generated in the cutting area. If the heat cannot be dissipated in time, it will cause oxidation and burns on the material surface, and even cause interface separation between the matrix and the reinforcement material, seriously affecting the cutting quality.
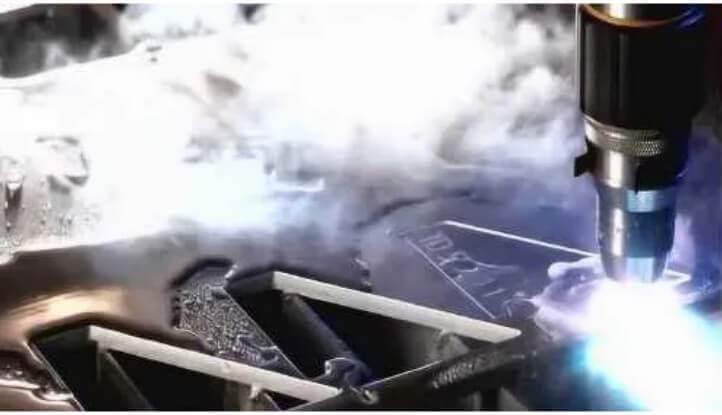
(3) Burr and delamination problems:
When cut aluminum composite material, burrs and delamination are easy to occur on the cutting edge. This is mainly due to the fact that the fracture behavior of the reinforcement material is inconsistent with that of the aluminum matrix, resulting in tearing of the material during cutting. Burrs and delamination not only affect the appearance quality of the parts, but also reduce the mechanical properties of the parts.
(4) Tool selection and cutting parameter optimization:
Selecting the right tool material and geometric parameters is crucial for the successful cutting of aluminum composites. Commonly used tool materials include superhard materials such as diamond and cubic boron nitride. However, these tools are expensive and very sensitive to cutting parameters (such as cutting speed, feed rate, and cutting depth). The selection of cutting parameters requires comprehensive consideration of factors such as cutting efficiency, surface quality, and tool life.
5.Precautions for cut aluminum composite material
When cut aluminum composite material, you need to pay attention to a number of technical points and safety precautions. The following are detailed precautions:
(1) Selecting the right cutting tool:
It is crucial to use the right cutting tool. Common cutting tools include saw blades, knives, and drill bits. When selecting, choose the appropriate tool type and specification based on the thickness and hardness of the aluminum composite. For example, using a saw blade specifically for aluminum profiles can avoid problems such as aluminum sticking and burrs.
(2) Preparation before cutting:
Before cutting, the aluminum composite material needs to be cut to a fixed length and the size needs to be checked. The fixed length should be checked especially for the first cut. At the same time, the surface quality and size of the material should be checked, the defective parts should be marked, and the defective parts should be cut off first when cutting.
(3) Keep the cutting environment clean:
The cutting saw table should be kept clean during the cutting process, and a large amount of aluminum chips should not be allowed to exist. Aluminum chips not only affect the cutting accuracy, but also may scratch the surface of the material. Avoid overlapping cutting to prevent aluminum chips from accumulating and surface damage.
(4) Control cutting parameters:
When cut aluminum composite materials, the cutting speed and feed speed should be controlled. Too fast speed may cause uneven cutting surface, and too slow speed may damage the saw blade. Adjust the feed speed according to the thickness of the material to ensure the cutting quality and the service life of the saw blade.
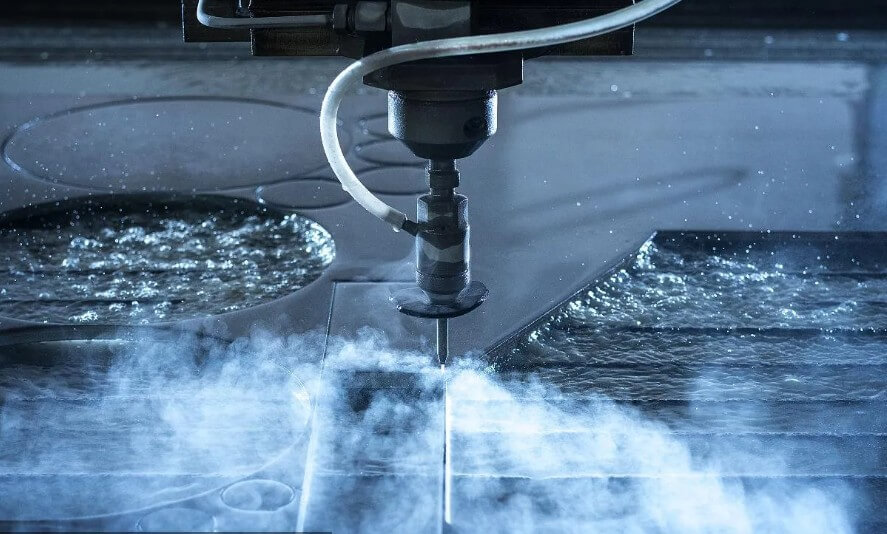
(5) Use appropriate lubrication and cooling:
When cut aluminum composite materials, appropriate lubricating oil or coolant should be used to reduce friction and heat, prevent overheating of the saw blade and extend its service life. Commonly used lubricants include saponified liquid and special cutting fluid, the latter of which is more effective and helps improve the workshop environment.
(6) Safety protection measures:
Operators should wear appropriate personal protective equipment, such as safety glasses, gloves and earmuffs, to prevent metal chips, noise and other hazards generated during the cutting process from causing harm to personal safety.
(7) Post-cutting treatment:
After cutting, the cutting area should be cleaned in time, the cut workpiece should be taken out and necessary subsequent treatment should be carried out, such as deburring and surface cleaning. When framing, the ends should be aligned, each layer should be separated by horizontal bars, and information such as specifications, length and number of roots should be indicated.
6.Application industry analysis of cutting aluminum composite materials
(1) Application in the aviation industry
In the aviation industry, the technology of cut aluminum composite materials is particularly critical. For example, the use of laser cutting technology can accurately cut complex aviation parts such as wings and tail fins without compromising the material properties. This high-precision cutting technology can ensure the lightweight and high strength of aviation parts, meeting the strict requirements of the aviation industry for safety and efficiency.
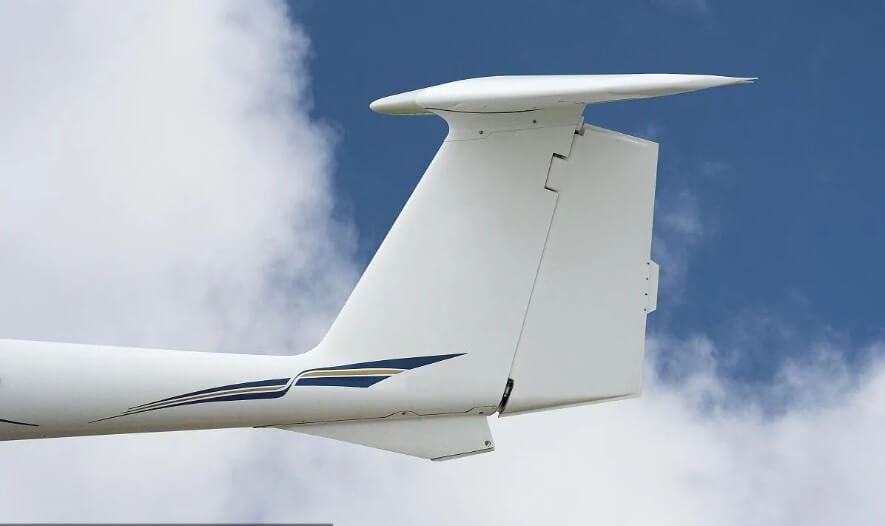
(2) Application in the construction industry
In the construction industry, cut aluminum composite materials is mainly used to process curtain walls, doors and windows and other components. Plasma cutting and water jet cutting technologies are widely used in the construction industry. These technologies can provide efficient cutting solutions and meet the requirements of the construction industry for material processing accuracy and efficiency.
(3) Application in automobile manufacturing
In the automobile manufacturing industry, cut aluminum composite material is mainly used for the manufacture of body structures. Mechanical cutting and laser cutting technologies are widely used in the automobile manufacturing industry. These technologies can provide high-precision cutting and good surface quality, meeting the requirements of the automobile manufacturing industry for material processing accuracy and efficiency.
7.Summary
In summary, cut aluminum composite material requires comprehensive consideration of multiple factors such as the selection of cutting technology, the setting of cutting parameters, and operating skills. Through reasonable selection and meticulous operation, the cutting quality and efficiency can be significantly improved to meet the needs of aluminum composite material processing in different fields.