Comprehensive understanding of cutting fluid – a powerful assistant for metal processing
Cutting fluid plays a vital role in the metal processing process. It can not only improve processing efficiency, but also extend tool life and improve workpiece surface quality. However, there are many types of cutting fluids with different performances. How to choose the right cutting fluid and use it correctly is an important issue that every metal processing company must face.
This article will discuss in detail the key role of cutting fluids in improving metal processing efficiency from the aspects of classification, function, selection basis, application skills and maintenance management.
1.Classification and characteristics of cutting fluids
It is mainly divided into two categories: oil-based cutting fluids and water-based cutting fluids. Each category has different subdivisions and each has unique performance characteristics.
(1) Oil-based cutting fluids
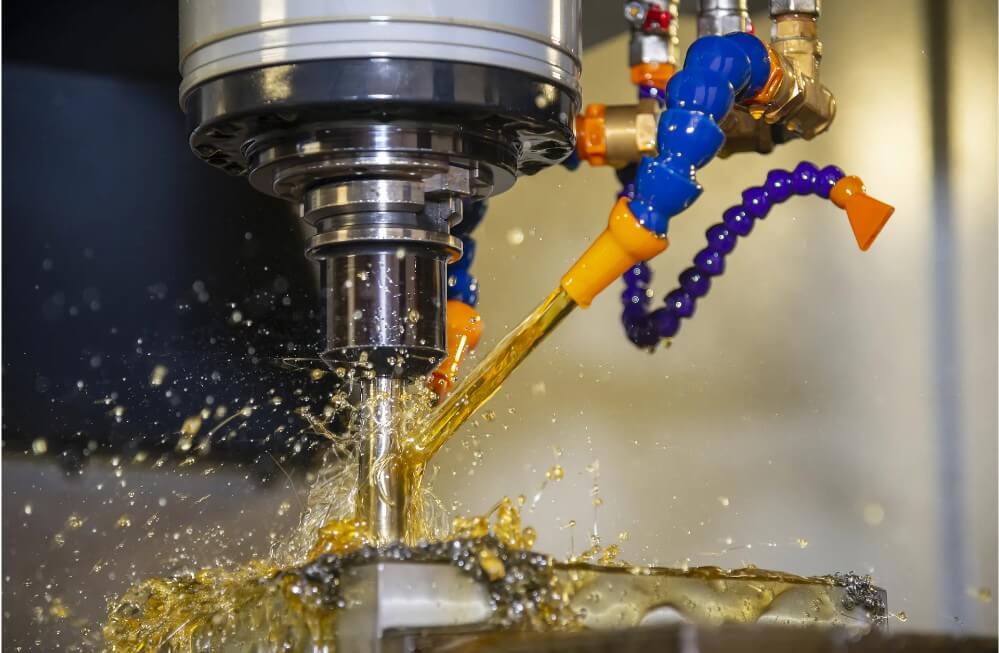
It is based on mineral oil and has good lubricity and rust resistance. It is suitable for heavy-load processing and cutting of difficult-to-process materials.
Oil-based cutting fluids can be divided into low-viscosity cutting oils and high-viscosity cutting oils according to their viscosity.
Low-viscosity cutting oil is mainly used for flushing cutting, such as deep hole drilling. It has good cooling effect and can effectively remove cutting heat.
High-viscosity cutting oil is used for intermittent cutting, such as gear cutting and heavy turning. It has excellent lubrication performance and can effectively reduce tool wear.
(2) Water-based cutting fluid
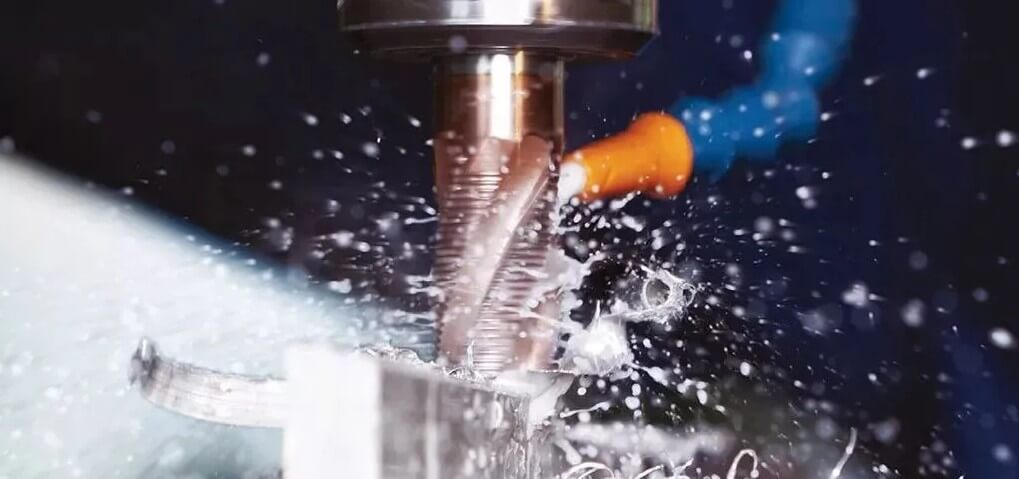
Water-based cutting fluids are divided into three types: emulsified, microemulsified and fully synthetic.
Emulsified cutting fluids have a higher oil content, better lubricity and cutting properties, and are suitable for processing soft materials such as aluminum alloys;
Microemulsified cutting fluids have a moderate oil content and are widely applicable. Their lifespan, corrosion resistance and extreme pressure performance are better than emulsified types;
Fully synthetic cutting fluids do not contain oil and have excellent cooling performance. They are suitable for heavy-load processing such as high-speed cutting, but their lubricity is relatively low and special additives need to be added to improve their lubrication performance.
2.Functions of cutting fluid
It plays a variety of important functions in the metal processing process, mainly including lubrication, cooling, cleaning and rust prevention.
(1) Lubrication
Cutting fluid can form a lubricating film between the tool and the workpiece, and between the tool and the chips, reducing friction, cutting force and tool wear, and improving the surface processing quality of the workpiece. The quality of the lubrication directly affects the service life of the tool and the surface roughness of the workpiece.
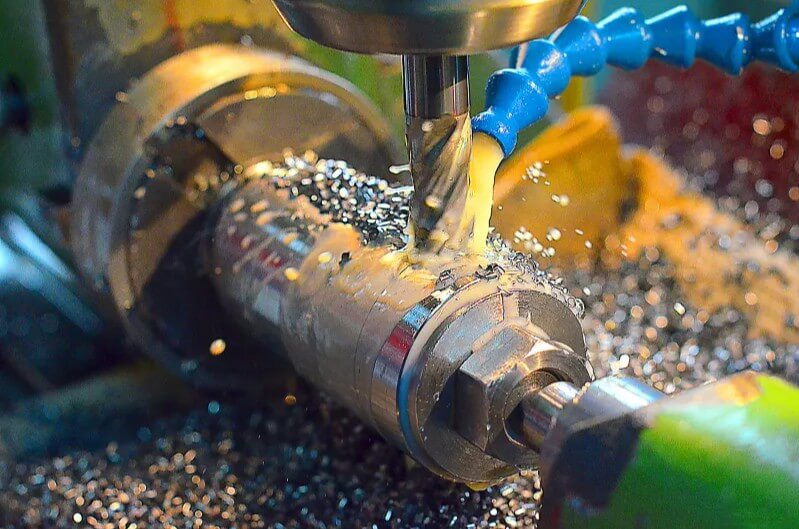
(2) Cooling
During the cutting process, the tool, chips and workpiece generate a lot of heat due to friction. The cutting fluid contacts these heat bodies to achieve convection and vaporization cooling, quickly absorbs and removes heat, and reduces the cutting temperature.
This not only prevents the hardness of the tool from decreasing and aggravating wear due to overheating, but also reduces the dimensional error of the workpiece caused by thermal deformation, ensuring the stability and accuracy of the processing process.
(3) Cleaning
If the chips, grinding chips, iron powder, oil stains, sand and other impurities generated during the cutting process are not removed in time, they will have an adverse effect on the processing process. The cutting fluid can effectively wash these impurities away from the cutting area, keep the processing environment clean, and thus ensure the smooth progress of the drilling operation.
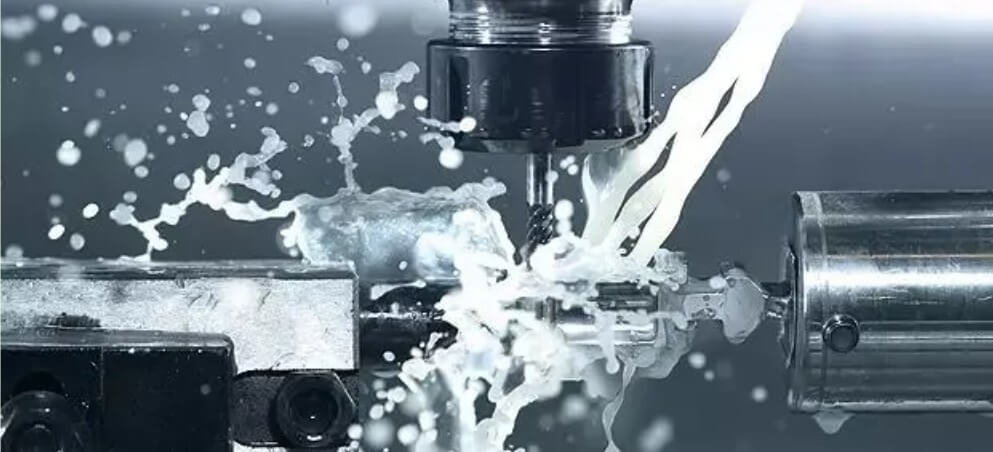
(4) Anti-rust effect
Anti-rust additives are added to the cutting fluid. These additives can form a protective film on the surface of the workpiece to prevent the workpiece from being corroded during processing, storage and transportation. The anti-rust effect is particularly important for workpieces that need to be stored for a long time or further processed.
3.Basis for the selection of cutting fluid
In selecting a suitable cutting fluid, it is necessary to comprehensively consider factors such as processing materials, processing technology, tool materials, processing accuracy requirements and economy.
(1) Processing materials
The physical and chemical properties of different materials vary greatly, and the requirements for cutting fluids are also different. For example, soft materials such as aluminum alloys have higher requirements for the lubricity of cutting fluids, and emulsified or micro-emulsified cutting fluids can be selected; while carbon steel, alloy steel and other materials with higher hardness require fully synthetic cutting fluids with better cooling performance.
(2) Processing technology
Different processing technologies also have different performance requirements for cutting fluids. For example, turning, milling, and grinding require cutting fluids with excellent cooling and chip removal properties, so fully synthetic cutting fluids can be used; broaching, tapping, and other finishing processes require high lubricity and chip removal properties of the cutting fluid, so cutting oils containing additives should be used.
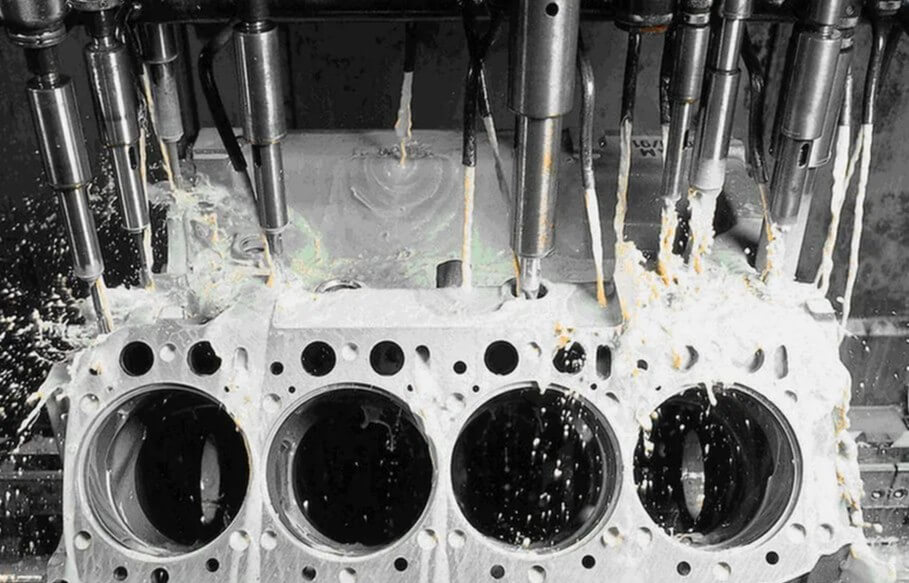
(3) Tool materials
The heat resistance and wear resistance of tool materials directly affect the selection of cutting fluids. For example, high-speed steel tools are prone to wear at high temperatures, so cutting fluids with good cooling properties should be used; carbide tools require high lubricity of the cutting fluid, so cutting fluids containing extreme pressure additives should be used.
(4) Processing accuracy requirements
High-precision processing requires high lubricity and stability of the cutting fluid, so cutting fluids with stable performance should be selected, and their concentration and pH value should be strictly controlled.
(5) Economy
The selection of cutting fluids also needs to consider their use costs, including purchase costs, maintenance costs, and waste fluid treatment costs. Selecting a cost-effective one can effectively reduce processing costs and improve the economic benefits of the enterprise.
4.Tips for using cutting fluid
Proper application of cutting fluid can not only improve machining efficiency, but also extend tool life and improve workpiece surface quality. The following are some key tips for its application:
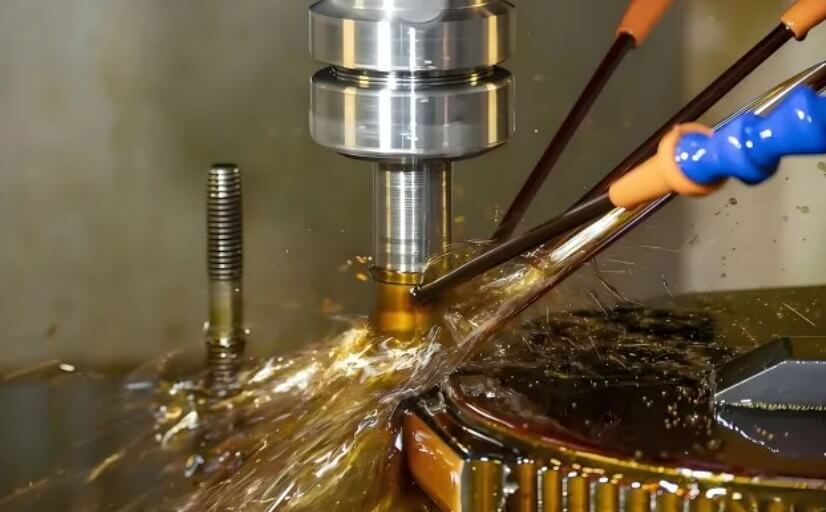
(1) Control concentration
Its concentration directly affects performance. Too high a concentration will increase costs, while too low a concentration will affect machining results. The concentration should be regularly tested and adjusted according to the supplier’s recommendations to ensure that it is in the best working condition.
(2) Control temperature
If the cutting fluid temperature is too high, it will reduce its cooling effect and accelerate tool wear; if the temperature is too low, it will affect its fluidity and chip removal effect. The cutting fluid temperature should be controlled within an appropriate range through a cooling system or a heating system.
(3) Optimize the fluid supply method
The fluid supply method directly affects its cooling and lubrication effects. According to the machining process and tool type, the appropriate fluid supply method, such as high-pressure spray, low-pressure spray, etc., should be selected to ensure that the cutting fluid can fully cover the cutting area.
(4) Clean up chips in a timely manner
The accumulation of chips will affect the cooling and lubrication effects of the cutting fluid and even cause increased tool wear. Cutting fluids should be cleaned up in time to keep the cutting fluid clean and improve processing efficiency.
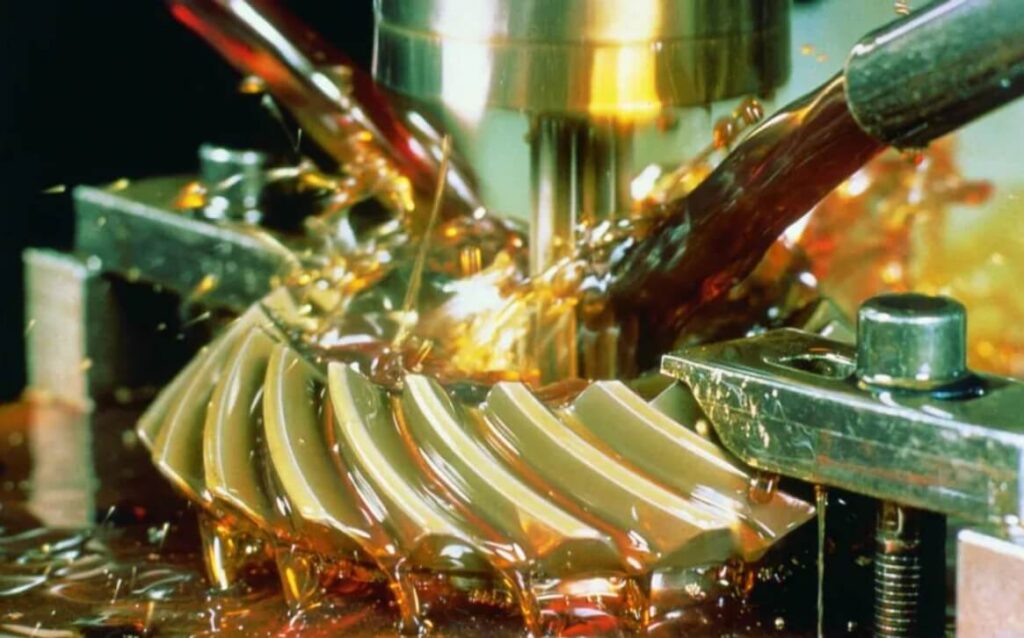
5.Cutting fluid maintenance and management
Maintenance and management of cutting fluids are the key to ensuring stable performance and extending service life. The following are some important measures for their maintenance and management:
(1) Regularly test cutting fluid performance
The concentration, pH value, colony count and other indicators of cutting fluids should be tested regularly to detect and deal with problems in a timely manner to ensure that the cutting fluid is in the best working condition.
(2) Control water quality
Water quality has a great influence on the performance of cutting fluids. Hard water will affect the stability and anti-rust performance of cutting fluids. Softened water or deionized water should be used for preparation, and water quality should be tested regularly to ensure that it meets the requirements for use.
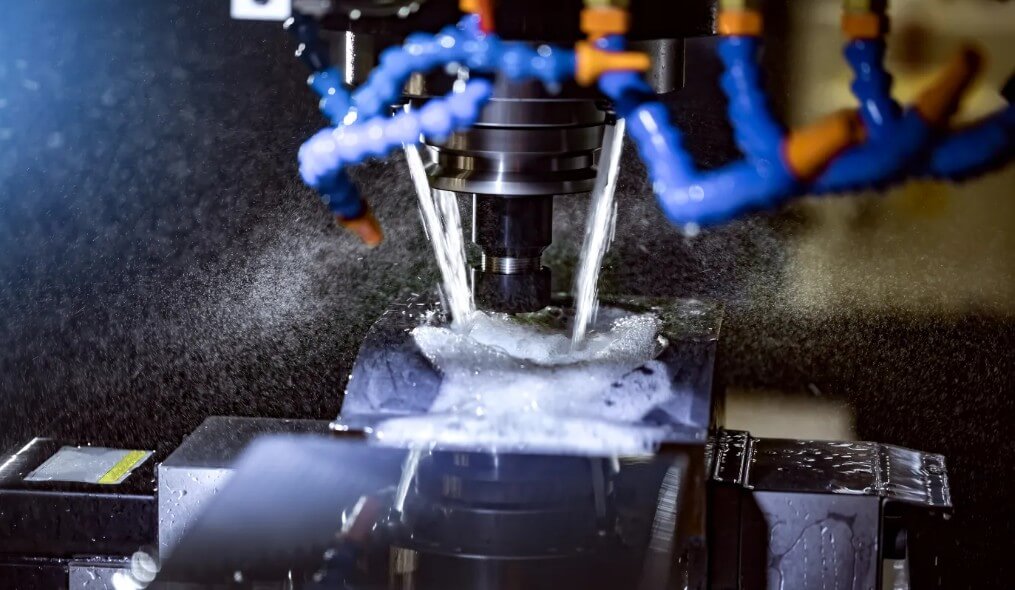
(3) Prevent pollution
The pollution of cutting fluids mainly comes from cuttings, oil stains, microorganisms, etc. Effective measures should be taken, such as installing filtering devices, regularly cleaning oil tanks, and controlling the workshop environment, to prevent cutting fluid pollution and extend its service life.
(4) Regular replacement
Cutting fluids will gradually age and their performance will decline during use. It should be replaced regularly according to its usage and the supplier’s recommendation to ensure its stable performance.
6.Conclusion
As a powerful assistant for metal processing, the selection and application of cutting fluid is the key to improving metal processing efficiency. Choosing the right cutting fluid and using and maintaining it correctly can not only improve processing efficiency, extend tool life, and improve workpiece surface quality, but also reduce processing costs and improve enterprise economic benefits.
2 Comments