Importance of Material Selection for Cylindrical Parts
Cylindrical parts are commonly used in various industries, from automotive to aerospace, due to their versatility and efficiency. When designing cylindrical parts, there are several important considerations to keep in mind to ensure optimal performance and functionality. One of the most crucial aspects of designing cylindrical parts is the selection of the appropriate material.
The choice of material for cylindrical parts is of utmost importance as it directly affects the part’s strength, durability, and overall performance. Different materials have varying properties, such as tensile strength, hardness, and resistance to corrosion, which can significantly impact the functionality and lifespan of the cylindrical part.
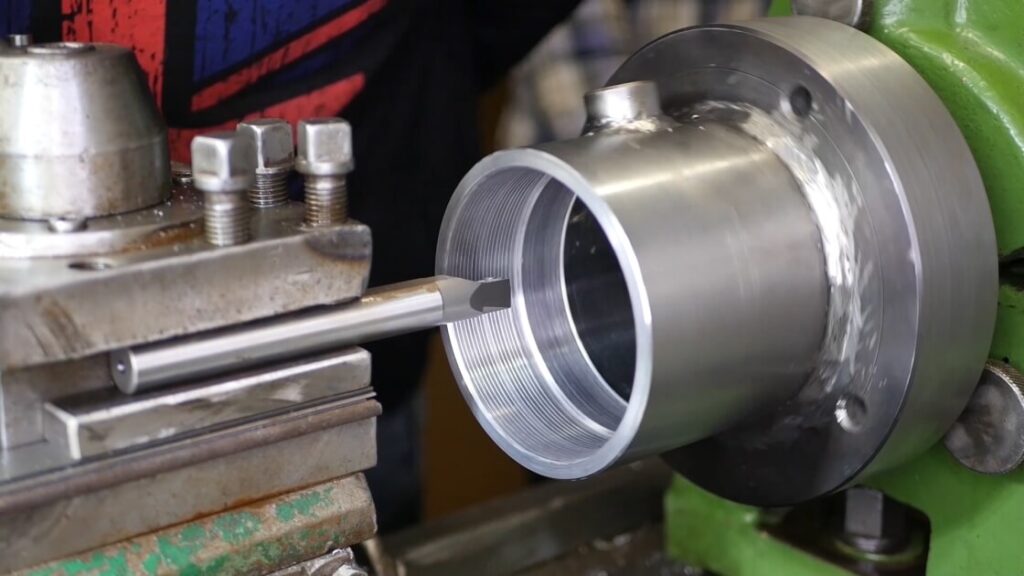
Important factors to consider when selecting materials for cylindrical parts
One key consideration when selecting a material for cylindrical parts is the intended application and the specific requirements it entails. For example, if the cylindrical part will be subjected to high temperatures or extreme pressure, a material with excellent heat resistance and high strength, such as stainless steel or titanium, would be a suitable choice. On the other hand, if the cylindrical part will be exposed to corrosive environments, a material with good corrosion resistance, such as aluminum or certain types of plastics, would be more appropriate.
Another important factor to consider when selecting a material for cylindrical parts is the manufacturing process. Different materials have varying machinability and formability, which can affect the ease and cost of production. For instance, materials like aluminum and brass are known for their excellent machinability, making them ideal choices for cylindrical parts that require intricate designs or tight tolerances. On the other hand, materials like hardened steel may be more challenging to machine, requiring specialized tools and techniques.
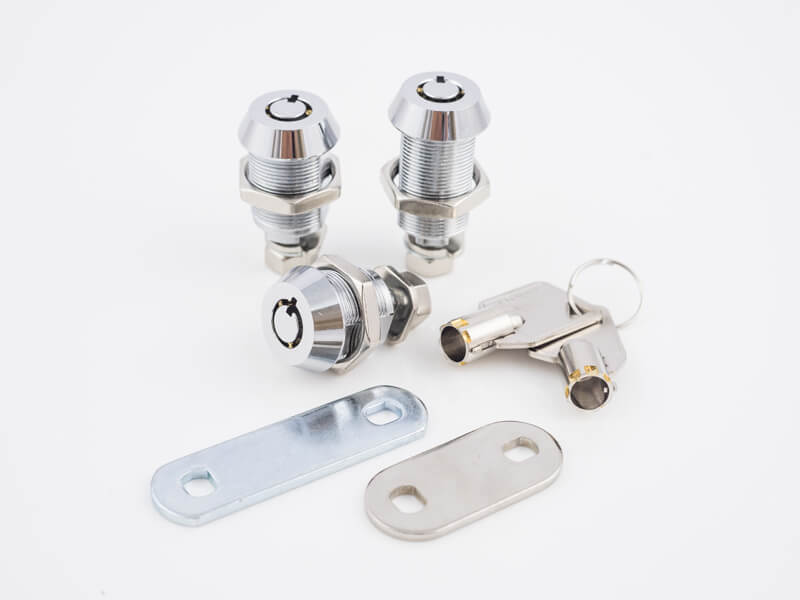
Additionally, the cost of materials should also be considered. Because materials such as special alloys or high-performance plastics are likely to be much more expensive than other materials. While these materials can provide excellent performance, actual production work must be considered and benefits and costs must be weighed to ensure that the selected material is economically viable for the intended application.
In addition to the characteristics of the material, it is also important to consider the material’s availability and delivery time. Because some materials may be easily available in large quantities, others may require longer lead times or have limited availability. This consideration is particularly important in industries with tight production schedules or tight deadlines, as delays in material procurement can have a significant impact on project timelines and costs.
Lastly, it is essential to consider any regulatory or industry standards that may dictate the choice of material for cylindrical parts. Certain industries, such as aerospace or medical, have stringent requirements for material selection to ensure compliance with safety and performance standards. It is crucial to thoroughly research and understand these standards to ensure that the chosen material meets all necessary requirements.
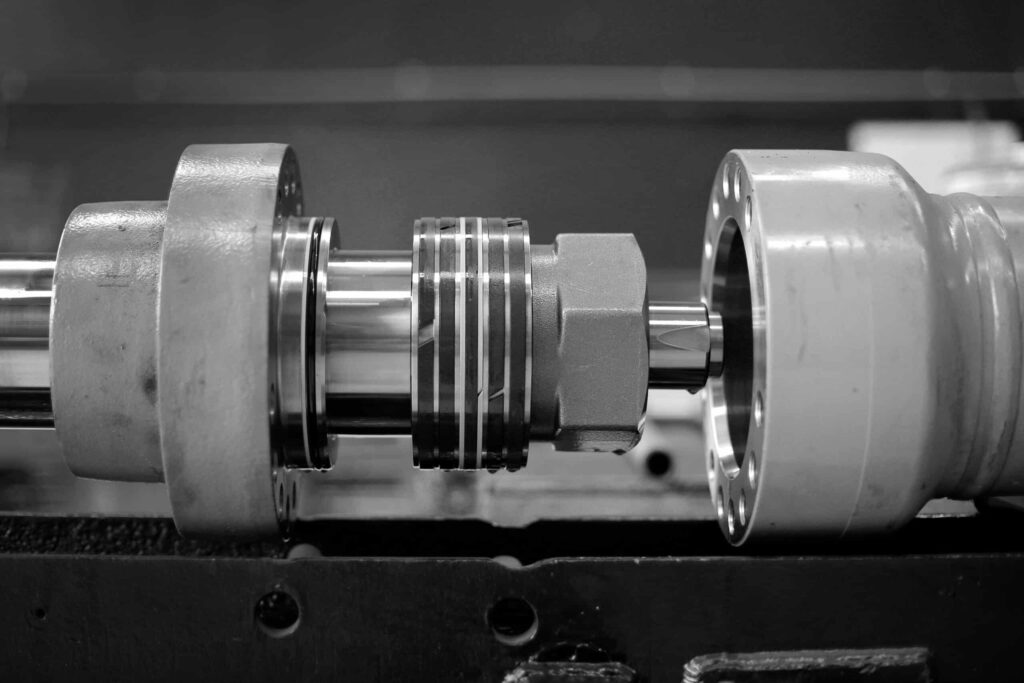
In conclusion, the selection of the appropriate material is a critical aspect of designing cylindrical parts. The material’s properties, such as strength, durability, and resistance to corrosion, directly impact the part’s performance and functionality. Factors such as the intended application, manufacturing process, cost, availability, and regulatory standards should all be carefully considered when choosing a material for cylindrical parts. By taking these considerations into account, designers can ensure that their cylindrical parts meet the desired specifications and perform optimally in their intended applications.