Exploring the density of aluminum: the perfect combination of lightness and strength
Aluminum is a metallic element that is abundant in the earth’s crust and is widely used in modern industry and daily life due to its unique properties.
Among them, the density of aluminum is one of its many important characteristics, which has a key impact on the selection of materials and product manufacturing. This article will explore the density of aluminum in depth, revealing the factors that affect and are affected by the density of aluminum, as well as its wide application in different fields.
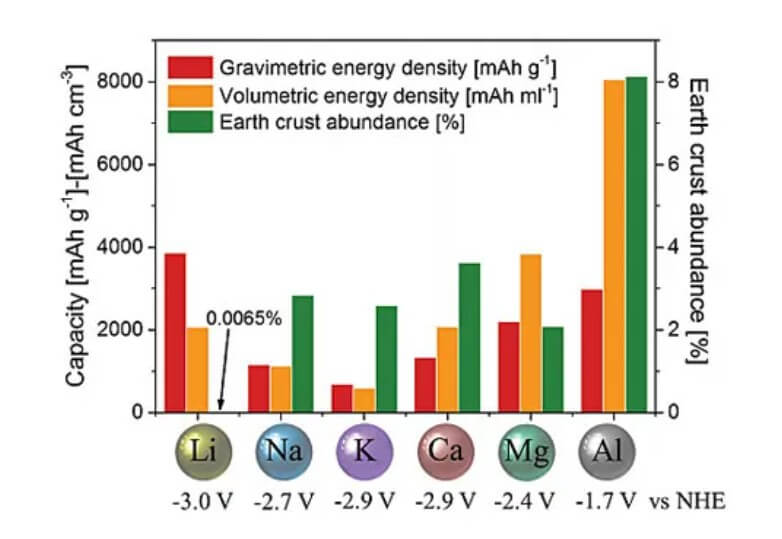
·
Comparison of aluminum resource content and volume capacity with other metals
·
1.Basic introduction to the density of aluminum and aluminum alloys
The density of aluminum is about 2.7 grams per cubic centimeter (g/cm³), which is equivalent to 2700 kilograms per cubic meter (kg/m³). This density value is relatively low, only about one-third of the density of steel. The low density of aluminum makes it an ideal material in aerospace, transportation and other fields. For example, aluminum alloys are often used in the structural components of aircraft and rockets to reduce weight, improve fuel efficiency and enhance flight performance.
The density of aluminum alloys is slightly higher than that of pure aluminum, usually between 2.5g/cm³ and 3.0g/cm³, depending on the alloy composition and processing technology. Aluminum alloys not only maintain the low density characteristics of aluminum, but also significantly improve strength and corrosion resistance by adding other elements such as copper, magnesium, silicon, etc., and are widely used in construction, automobile manufacturing, and electronic appliances.
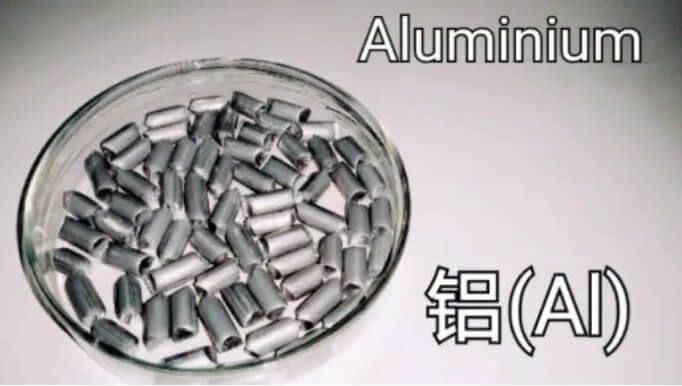
2.Detailed explanation of the formula for calculating the density of aluminum
As a widely used metal, the density of aluminum is one of the important indicators to measure its properties. Its calculation formula is:
Density (g/cm³) = total mass (g)/volume (cm³)
This means that the density of aluminum is equal to its total mass divided by the total volume. The standard density of aluminum is usually 2.7 grams per cubic centimeter (g/cm³) at room temperature, which is applicable to pure aluminum. However, the density of aluminum is affected by temperature and pressure, so it may need to be adjusted under certain conditions.
In addition, the density of aluminum alloys varies, depending on the alloying elements added. Common aluminum alloy densities are usually between 2.5 and 2.9 g/cm³. For example, the density of aluminum-copper alloys may be 2.8 to 2.9 g/cm³, while the density of aluminum-zinc alloys may be 2.6 to 2.7 g/cm³.
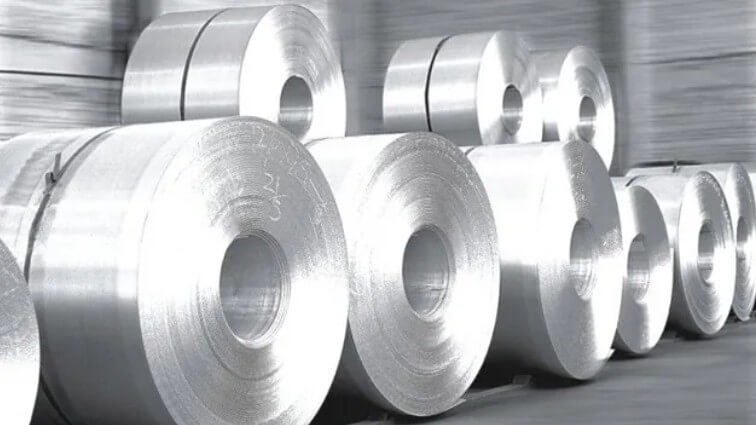
Through this formula, we can easily calculate the mass or volume of aluminum or aluminum alloy, which is particularly important for material selection and design in engineering and manufacturing applications.
3.Common aluminum alloy types and their density
Aluminum alloys are formed into many types due to the addition of different elements, and each type has different density and properties. For example, the density of aluminum-copper alloys may be higher than that of pure aluminum, while aluminum-magnesium alloys may have lower density. Common aluminum alloys include 2000 series, 5000 series and 6000 series, which are widely used in the automotive, aviation and construction fields.
(1) 2000 series aluminum alloy
2000 series aluminum alloy is a high-strength aluminum alloy containing copper, magnesium, manganese and other elements, and is widely used in the aerospace field. For example, 2024 aluminum alloy is widely used in the manufacture of aircraft fuselages and wings due to its high strength and high hardness. 2014 aluminum alloy is widely used in the manufacture of mechanical parts and molds due to its good cutting performance.
(2) 5000 series aluminum alloy
5000 series aluminum alloy is a medium-strength aluminum alloy containing magnesium and is widely used in shipbuilding and construction. For example, 5052 aluminum alloy is widely used in shipbuilding and marine engineering due to its good corrosion resistance and welding performance. 5083 aluminum alloy is widely used in the automotive and rail transportation fields due to its good fatigue resistance.
(3) 6000 series aluminum alloy
6000 series aluminum alloy is a high-strength aluminum alloy containing magnesium and silicon and is widely used in the construction and automobile manufacturing fields. For example, 6061 aluminum alloy is widely used in the manufacture of building structures and automobile parts due to its good comprehensive performance and processing performance. 6082 aluminum alloy is widely used in the manufacture of mechanical parts and molds due to its good mechanical properties and corrosion resistance.
Aluminum alloys with different densities
The addition of different alloying metals can cause the density of different aluminum alloys to change. For example:
1xxx alloys have a density close to that of pure aluminum, up to 99%. However, some 7xxx or 8xxx alloys have a density of up to 2.9 g/cm3. Meanwhile, some 4xxx alloys have a slightly lower density.
These subtle changes have a profound impact on the versatility and usability of aluminum alloys, which not only reflect the role of the alloy material, but also determine the range of mechanical properties available.
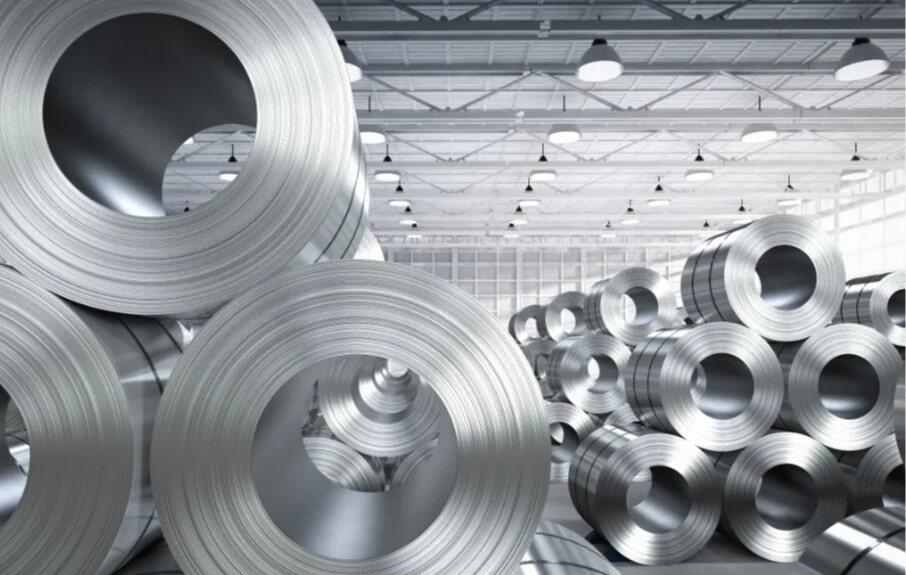
The following are the density data, main alloying elements, and characteristics or uses of some common aluminum alloy grades:
Alloy Number | Density (g/cm³) | Main Alloying Elements | Characteristics or Applications |
1050 | 2.71 | Pure aluminum (99.5%) | Excellent conductivity, used for electrical wires |
2011 | 2.83 | Al – Cu | High strength, good machinability, used for screws and rivets |
2014 | 2.8 | Al – Cu – Mg – Si | High strength and toughness, used in aerospace and military applications |
2017 | 2.8 | Al – Cu – Mg | Good strength and fatigue resistance, used for aircraft structures |
2024 | 2.78 | Al – Cu – Mg | High strength, used for aircraft structures and wheels |
3003 | 2.73 | Al – Mn | Good corrosion resistance, used for cooking utensils and building panels |
3004 | 2.73 | Al – Mn | Similar to 3003, used for beverage cans |
5052 | 2.68 | Al – Mg | Good formability and corrosion resistance, used for marine applications |
5083 | 2.66 | Al – Mg | High strength and excellent corrosion resistance, used for shipbuilding |
6061 | 2.7 | Al – Mg – Si | Good mechanical properties and weldability, used in automobile, construction, bicycle, electronics and other industries |
6063 | 2.69 | Al – Mg – Si | Excellent extrudability and corrosion resistance, used for window frames and architectural applications |
7075 | 2.8 | Al – Zn – Mg – Cu | Very high strength, used for aerospace and high – performance applications |
7050 | 2.78 | Al – Zn – Mg – Cu | High strength and toughness, used for aerospace structures |
8011 | 2.71 | Al – Mg | Good formability and corrosion resistance, used for aluminum foil |
8090 | 2.59 | Al – Li – Cu | Light weight and high strength, used for aerospace applications |
9050 | 2.6 | Al – Li – Cu – Mg – Zr | Very light weight and high strength, used for aerospace and automotive applications |
1100 | 2.71 | Pure aluminum (99.0%) | Good ductility and corrosion resistance, used for general purpose applications |
3005 | 2.73 | Al – Mn | Good corrosion resistance, used for building panels and siding |
5056 | 2.68 | Al – Mg | Good formability and corrosion resistance, used for marine applications |
6060 | 2.7 | Al – Mg – Si | Similar to 6063, used for architectural applications |
·
Please note that the density of aluminum alloys may vary slightly depending on the specific production process and alloy composition. In actual applications, it is recommended to refer to the specific material data sheet or information provided by the supplier.
·
4.The influence of aluminum production process on aluminum density
(1) Aluminum refining process
The aluminum refining process mainly includes three stages: bauxite mining, alumina production and aluminum production. Bauxite is refined into alumina, which is then electrolyzed to produce aluminum liquid. During the electrolysis process, alumina decomposes in molten cryolite to produce aluminum liquid and oxygen. The density of aluminum liquid is affected by factors such as electrolysis temperature, electrolyte composition and current density. For example, too high an electrolysis temperature will cause the density of aluminum liquid to decrease, while impurities in the electrolyte may affect the purity of aluminum liquid and thus its density.
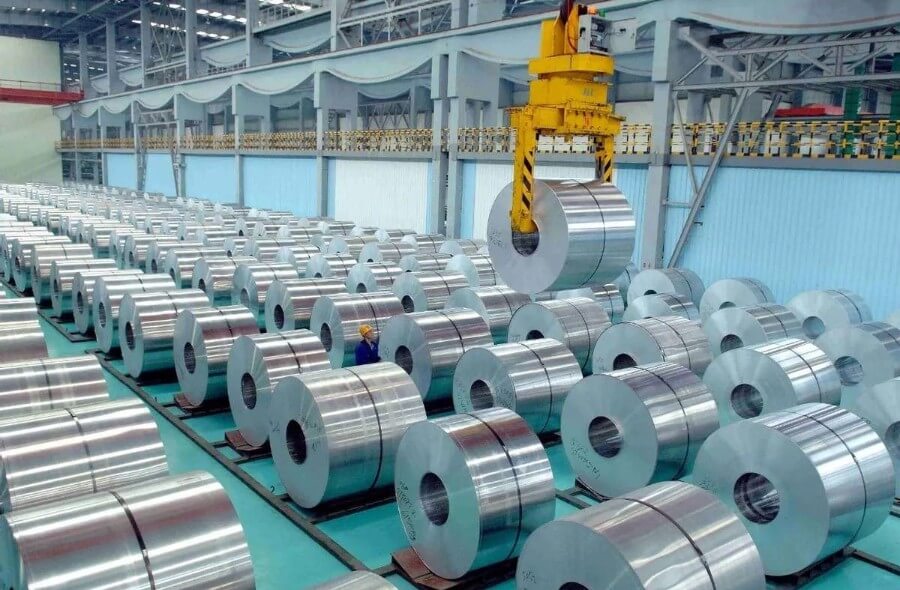
(2) Aluminum alloying
Aluminum alloying is the process of improving its properties by adding other elements. Common alloying elements include copper, magnesium, silicon, zinc, etc. The type and content of alloying elements will have a significant effect on the density of aluminum alloys. For example, the density of aluminum sodium alloy may be close to 2.64 grams per cubic centimeter, while the density of certain specific aluminum alloys may be higher or lower. In addition, during the alloying process, the uniformity of the distribution of alloying elements and the formation of solid solutions will also affect the density of aluminum alloys.
5.The influence of aluminum density on its application
The density of aluminum is 2.7 grams per cubic centimeter, which makes it widely used in many fields. The following are several aspects of how the density of aluminum affects its application:
(1) Lightweight properties and aerospace
The lightweight property of aluminum is one of its most prominent advantages. This property makes aluminum an indispensable material in the aerospace field. Due to the low density of aluminum, the fuselage of aircraft and the structural parts of rockets can be made of aluminum, which greatly reduces the overall weight. This not only improves the fuel efficiency of the aircraft, but also enhances its maneuverability and load-bearing capacity. For example, in modern commercial aircraft, the use of aluminum accounts for more than 70% of the total mass of the fuselage.
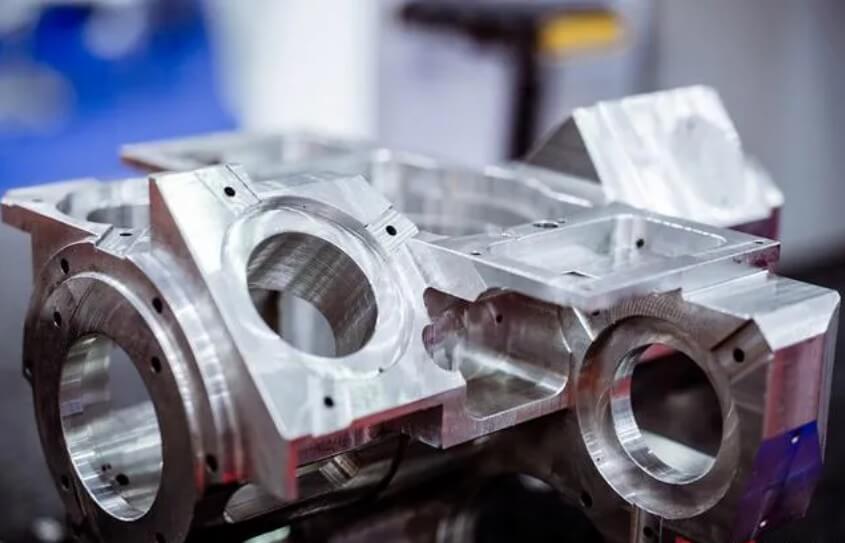
(2) Lightweight trend in the automotive industry
In the automotive industry, reducing the weight of the vehicle body is a key way to improve fuel efficiency and reduce emissions. Aluminum’s low density and light weight make it highly favored in automobile manufacturing. Using aluminum to manufacture automotive parts can significantly reduce the weight of the vehicle, thereby improving the performance and environmental protection indicators of the vehicle. For example, the all-aluminum body frame design of the Audi A8 not only reduces weight, but also enhances the rigidity and safety of the body.
(3) Aesthetics and durability in the construction field
Aluminum is also widely used in the construction field, mainly due to its lightweight, corrosion-resistant and beautiful properties. Aluminum alloy doors, windows, curtain walls and other building materials are not only stylish in appearance, but also can effectively resist the impact of harsh environments and extend their service life. In addition, the low density of aluminum also makes it more convenient during installation and transportation, reducing construction costs.
(4) Heat dissipation needs in the electronics industry
In the electronics industry, aluminum’s low density and good thermal conductivity make it an ideal material for manufacturing electronic components and radiators. For example, computer CPU radiators are generally made of aluminum because aluminum can quickly conduct heat away, keep electronic components running stably, and extend their service life.
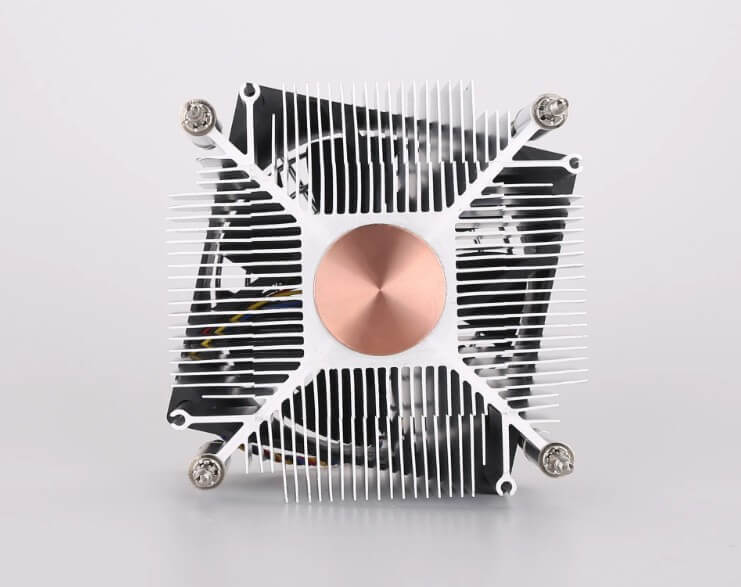
6.The impact of aluminum density on material design and machining processes
Aluminum is a lightweight metal with many excellent properties. These properties make aluminum widely used in material design and machining processes. The following are the impacts of aluminum density on these two aspects:
(1) Impact on material design
1) Lightweight structure
The density of aluminum is about one-third of that of steel, which makes it an ideal material for achieving lightweight structure. In the automotive, aerospace and other fields, reducing weight means reducing energy consumption, improving fuel efficiency and carrying capacity.
2) Balance between stiffness and strength
While maintaining a low density, aluminum can significantly improve its strength and stiffness through alloying and heat treatment. During the processing, it is necessary to weigh the density, strength and stiffness of aluminum according to the specific application scenario and select the appropriate aluminum alloy material. For example, aircraft structural parts often use high-strength aluminum alloys to ensure that the strength and stiffness requirements are met while reducing weight.
3) Impact resistance
Aluminum has a low density and relatively good impact resistance. This makes aluminum advantageous in manufacturing high-speed mechanical equipment or structural parts that bear impact loads. For example, aluminum bicycle frames can withstand more impact during collisions, improving riding safety.
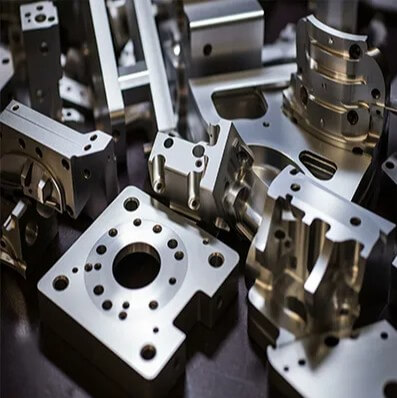
(2) Impact on the machining process
1) Cutting force and cutting heat
Due to the low density of aluminum, its cutting force is relatively small and the cutting heat is also less. This makes aluminum less prone to tool wear during machining, and higher cutting speeds and feed rates can be used to improve machining efficiency. At the same time, less cutting heat also helps to reduce workpiece deformation and improve machining accuracy.
We at Xavier have extensive experience in aluminum processing and a deep understanding of the performance characteristics of aluminum materials. As a result, we are able to reasonably select processing parameters and process strategies during CNC machining to ensure that the parts have excellent dimensional accuracy, surface quality, and mechanical properties, which are highly recognized and praised by customers. If you also have aluminum processing needs, then choosing Xavier is definitely the right choice.
2) Surface quality
Aluminum can easily obtain a good surface finish during machining. This is because aluminum has good plasticity and is not prone to burrs and edge collapse during cutting. This is very important for applications that require high surface finish, such as precision instruments, optical devices, etc.
3) Processing waste treatment
The low density of aluminum makes its processing waste larger in volume but lighter in weight. This reduces the cost of transportation and processing to a certain extent. In addition, aluminum waste has a high recycling value and can be recycled and reused to reduce resource waste and environmental pollution.
7.Summary
The density of aluminum, as one of its core characteristics, not only determines the lightweight and high-strength characteristics of aluminum, but also enables it to show excellent performance in many fields. From aerospace to transportation, from building structures to electronic devices, the wide application of aluminum is closely related to its density characteristics. In the future, with the further development of materials science, the density characteristics of aluminum will be further optimized, and its application prospects will be broader.
Regarding the characteristics of aluminum, in addition to its density, is aluminum ductile? Will brittleness destroy aluminum? What is the boiling point of molten aluminum? Does aluminum conduct electricity? Will aluminum parts rust? What is the melting temperature of molten aluminum? These are the questions that the public wants to know most, and they also show from the side that the application range of aluminum parts is very wide. Xavier’s engineers are particularly familiar with these characteristics of aluminum. By making reasonable use of these characteristics and combining them with precise manufacturing processes, they can produce high-quality parts.
5 Comments