A Comprehensive Guide to Diamond Machining
CNC machining is traditionally considered a high-precision method. But the cutting method has its limitations. You can’t make the cutting edge perfect enough to rival a grinding wheel in terms of tolerances and surface finish. However, new technologies and equipment are constantly being developed.
So we have a fairly new solution that allows CNC machines to get closer to the precision of abrasive methods. This solution is called diamond machining.
1.Why diamond machining improves part surface quality
When machining, the hardness of the cutting tool is one of the most important parameters of machining technology, and as far as we know, there is nothing harder than diamond.
Artificial diamonds can withstand extremely high temperatures and cutting methods. They are fairly cheap, and the cutting edge is very fine, you can get a mirror-like surface with a single-pointed diamond tool, which is the only way to achieve such a fine surface finish without buying extremely expensive grinding and polishing machines.
Diamonds can be mounted on simple CNC machines, and if you adjust the technology system for maximum rigidity, you can get excellent results. You can machine the hardest metals and get a mirror-like surface finish. Diamond turning and diamond milling are among the most widespread technologies currently available for commercial use.
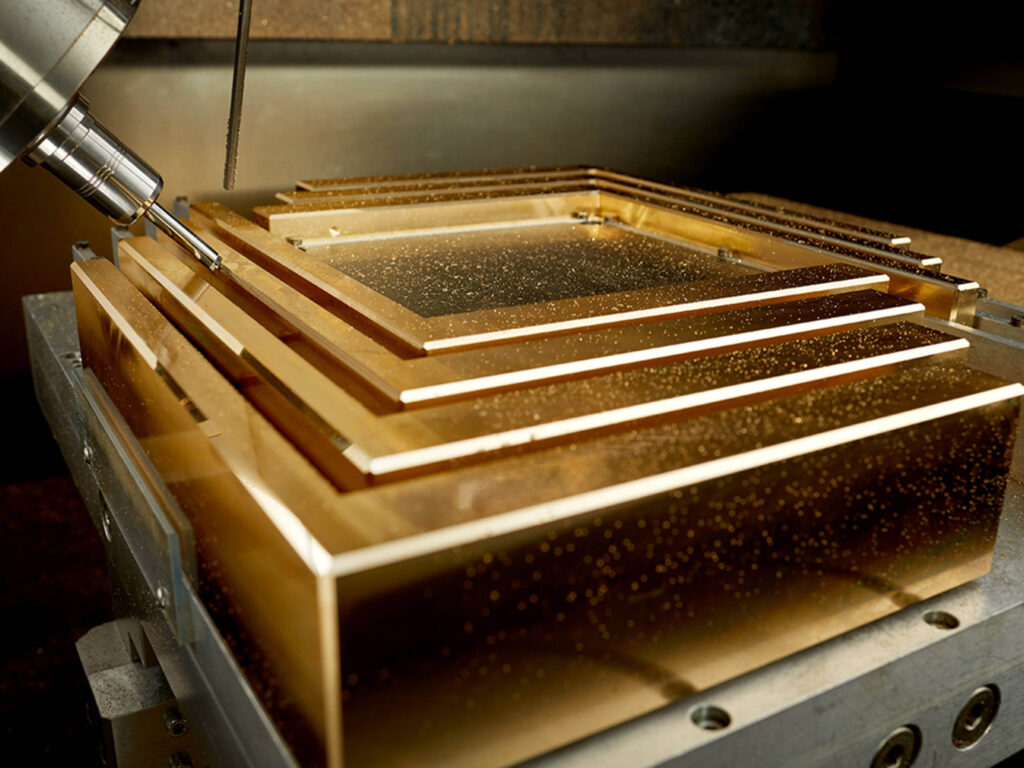
2.Advantages of using diamond machining
Diamond machining has many advantages, the main ones being:
- Excellent aluminum machining. Diamond tools are extremely good at withstanding high cutting speeds and temperatures. This is why diamond technology is often used in the mass production of aluminum parts. When machining aluminum, the service life of a single diamond blade can exceed that of many carbide tools.
- Carbide production. It is a general rule that harder materials can cut softer materials. Since there is no material harder than diamond, they are ideal for machining carbide, ceramics, and other materials with high hardness parameters.
- Diamond polishing. Some diamond tools are used to polish transparent materials such as glass, polycarbonate, PMMA. This is because of the very fine diamond particles at the tip of the tool.
- Durability. Diamond tool blades are 30 to 50 times more durable than carbide blades.
- Surface finish. With high-quality machining with diamond machining, you can achieve a better surface finish than any conventional tool. Basically, diamond tools bring a little grinding to the machining.
3.Diamond Machining Technology
Most machining methods that utilize diamond to some extent are considered grinding and polishing techniques, but there are two methods that can be used with CNC equipment and are closer to cutting than abrasive machining.
1) Single Point Diamond Turning
SPDT is a method that is very similar to simple turning, but the tool used is a diamond tool. In addition, the rigidity of the manufacturing system must be much greater. This means shorter lengths between fixtures, shorter tool holders, and minimizing vibrations.
SPDT is particularly suitable for manufacturing optical lenses because they are mostly rotating parts, and it is very convenient to fix them on a lathe and use a single-point diamond blade to obtain a clear and transparent surface.
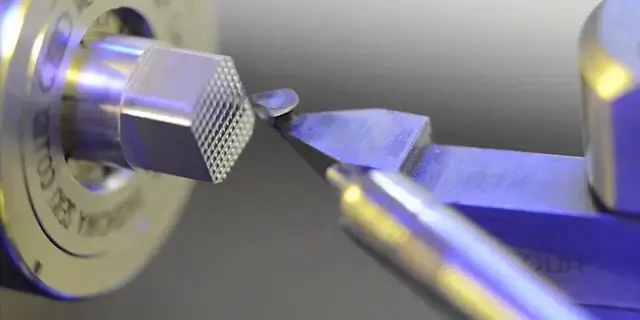
2) Single Point Diamond Milling Cutter
Single Point Diamond Milling is similar to conventional milling, but the main difference lies in the cutting tool and machining parameters. The tool is a milling cutter with a diamond blade. Mounted on a 5-axis machining center, this milling cutter is very suitable for machining complex surfaces made of glass, PMMA, and polycarbonate.
Extremely fast spinning diamond milling cutters with minimal cutting feed and ample lubrication can create the best surface finish for automotive light lenses, light guides and custom window glass.
However, it is important to always keep in mind vibration, as it will immediately destroy any surface quality. To improve the quality of the workpiece, some SPDM techniques involve machining in only one direction (the milling cutter makes a path and then returns to the initial side of the workpiece for a stepping motion, so that the cutting force is always in one direction.
4.What tools are used for diamond machining
The diamond tool used for machining is basically the same as any other cutting tool, but the blade is different. The base material of the blade is made of tungsten or carbide, and a thin film of diamond is visible at its tip.
The film is very hard and can last 50 times longer than conventional tools. It is very sharp and cuts very cleanly, achieving an excellent surface finish.
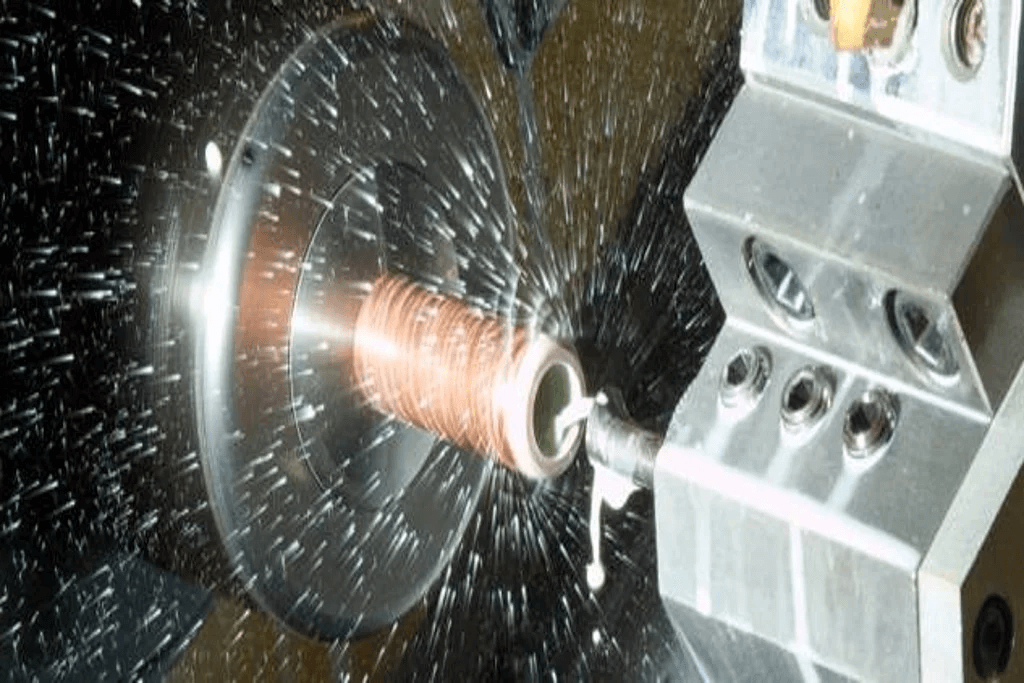
5.What materials can be cut with diamonds
Diamond tools can machine many different materials, including ceramics, silicone, polycarbonate, plexiglass (PMMA), non-ferrous alloys such as aluminum, copper, bronze, titanium, glass, different polymers such as ABS, polyethylene, and highly abrasive materials such as concrete, granite, stone.
As you can see, the range of materials is very wide, from hard and brittle materials to soft and transparent materials.
6.When you cannot use diamond machining
A very important note is that diamond tools cannot be used to cut steel or iron alloys. The reason is that they both contain a large number of carbon atoms. Machining is always done at high temperatures, and since both diamond and steel contain carbon, the atoms sinter when heated. This way, the tool sticks to the part material and both parts are wasted.
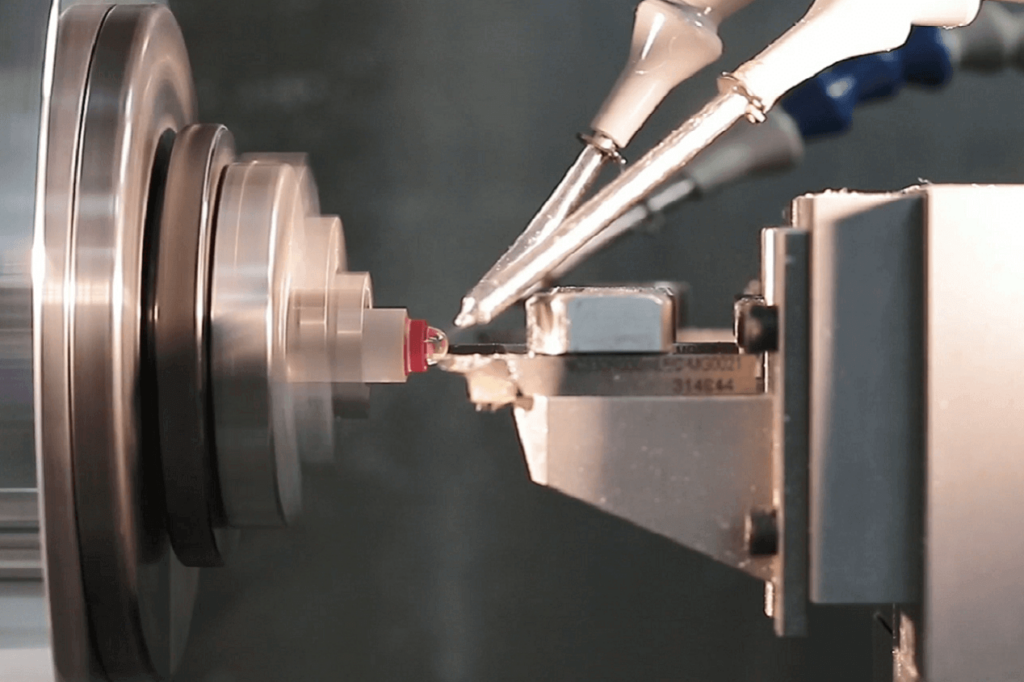
7.Where diamond machining can bring good results
1) Headlight lens prototype
As part of the CNC prototyping service, automotive headlight lens prototypes can be manufactured using diamond cutting.
The lens is too large and the geometry is too complex (it actually has to be cut into several segments and then glued together to retain its light-transmitting properties) to be milled, but a 5-axis The diamond milling cutters of a CNC machine can create a mirrored surface of just the right quality.
2) Light Guides
Light guides are a special tube and transparent component that helps illuminate certain points in a complex way.
They need to have a very fine surface finish while maintaining the complexity of their geometry. With the best 3-axis, 4-axis or even 5-axis CNC milling machines.