Different Types of CNC Machine Tools: A Comprehensive Guide
1. What is a CNC machine tool?
In today’s manufacturing industry, CNC machines play a vital role. CNC machines are automated tools that use computer programming to control their movement and operation. They are widely used in the manufacturing process to produce precise and complex parts with high accuracy and efficiency. CNC stands for Computer Numerical Control, and when computers are used to control CNC machines, they are called CNC machines. In simple terms, CNC machines control the movement of tools and workpieces through computer-aided design (CAD) and computer-aided manufacturing (CAM) programs to create almost any custom shape imaginable.
This blog will take you to an in-depth understanding of the different types of CNC machines to help manufacturers make the best choice.
2. Working Principle of CNC Machine Tools
CNC machines automatically cut raw materials based on digital instructions from CAM or CAD software. First, a 3D model of the desired part is created using CAD software, which is then loaded into CAM software to generate a set of computer instructions (i.e., g-codes) that control the sequence of tool movement on the workpiece.
The g-codes contain key information such as part feature coordinates, required tools, speeds and feeds, and coolant control commands. The machine control unit (MCU) of the CNC machine converts the g-codes into specific instructions for the servo motors and spindles, allowing the CNC machine to flexibly move the tool or workpiece on multiple axes, ultimately cutting the raw material into the desired shape.
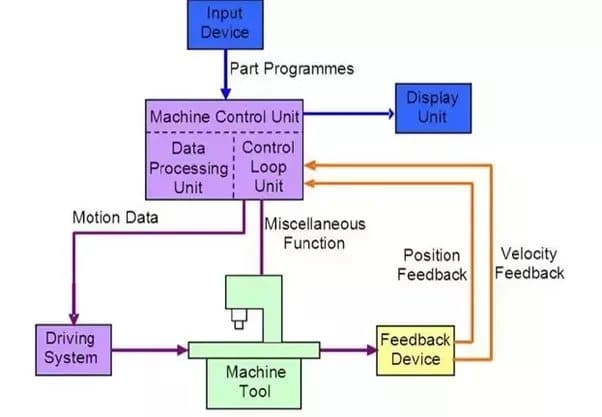
3. Composition of CNC machine tool system
CNC machine tool systems consist of several basic components that work together to achieve precise and automated machining operations:
1.Operator interface
Allows the operator to interact with the CNC system to enter commands, monitor progress and adjust parameters.
2.Input devices
Load CNC programs onto the machine tool, such as keyboards, USB flash drives, or wireless communication devices. These input devices play a key role in the programming and operation of CNC machine tools.
3.Machine tools
The physical device that performs the actual machining operations, there are different types such as lathes and milling machines, usually with slides and spindles, which are controlled in the X, Y, and Z axis directions respectively.
4.Machine control unit (MCU)
The brain of the system, receiving instructions and converting them into precise movements and actions of the machine tool, managing parameters such as motion control, spindle speed, tool change, etc.
5.Servo motors
Drive the machine tool axes, receive MCU signals, and provide precise and controlled movements.
6.Feedback devices
Such as encoders or linear scales, work with servo motors to provide position feedback to the MCU to ensure accuracy.
7.Tools
Includes a variety of cutting tools and accessories, selected according to the machining operation and material.
8.Workpiece clamping device
Fixes the workpiece in place during machining. There are many types such as vises and clamps.
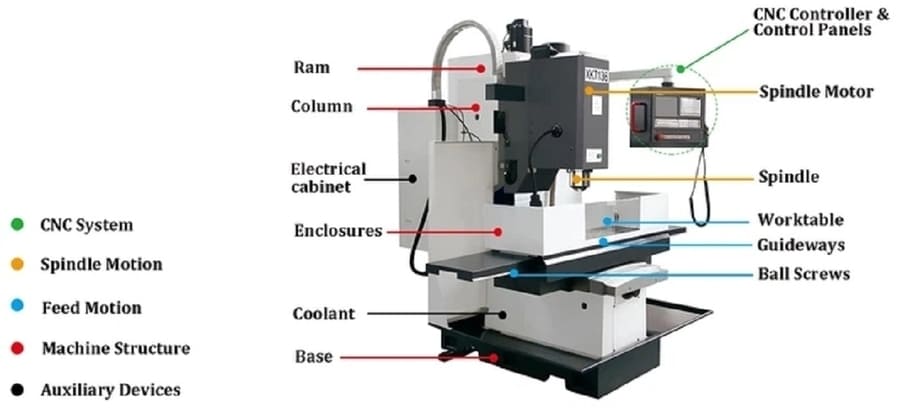
4. Different types of CNC machine tools
1.CNC milling machine
Principle: Cutting tools are used to remove material from a workpiece and accurately shape it. In a CNC milling machine, the workpiece is usually stationary while the tool rotates at high speed. CNC milling machines are available in both vertical and horizontal configurations. Vertical milling machines have a vertical spindle, while horizontal milling machines have a horizontal spindle and can accommodate larger sized workpieces.
Application: It is widely used in manufacturing fields such as cabinets, furniture, prototype models, etc. It can efficiently produce parts with complex shapes and has significant advantages such as high precision and multi-function.
2.Turning CNC machine tools
Principle: By rotating the workpiece material, cutting and shaping are performed with cutting tools. Including turret lathes, engine lathes, etc., which can perform a variety of machining operations.
Application: Suitable for manufacturing symmetrical parts such as camshafts and automotive parts.
3.EDM CNC machine tools
Principle: Using electrical sparks to remove material from conductive workpieces, there are two main types: wire cutting and sinking EDM.
Application: Manufacturing injection molds, die castings, etc., suitable for conductive materials, capable of cutting complex shapes with high precision.
4.CNC water jet cutting machine
Principle: Uses high-pressure water jets mixed with abrasives to precisely cut a variety of materials.
Application: Suitable for cutting parts in aerospace, automobile and other industries without heat damage, but the speed is slow and suitable for thick materials.
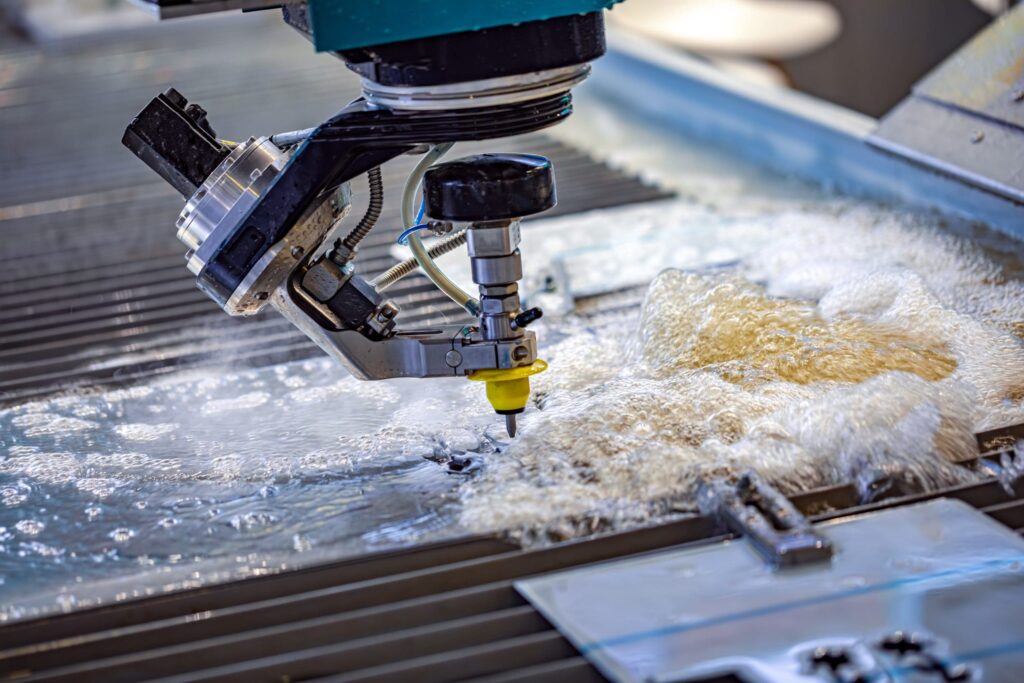
5.CNC Grinding Machine
Principle: Use a rotating grinding wheel to remove material to achieve high precision and surface finish.
Application: Used for processing parts such as camshafts and ball bearings, commonly used in industries such as automobiles and aerospace.
6.CNC Drilling Machine
Principle: Use a rotating drill bit to drill holes in the material.
Application: High efficiency, suitable for industries such as automobiles and mold manufacturing, but cannot drill deep or large holes, and specific drill bits are required for drilling holes of different diameters.
7.3D Printer
Principle: Print objects layer by layer, and designs and drawings are created through CAD and CAM processes.
Application: Commonly used in prototyping, providing a convenient means for product development.
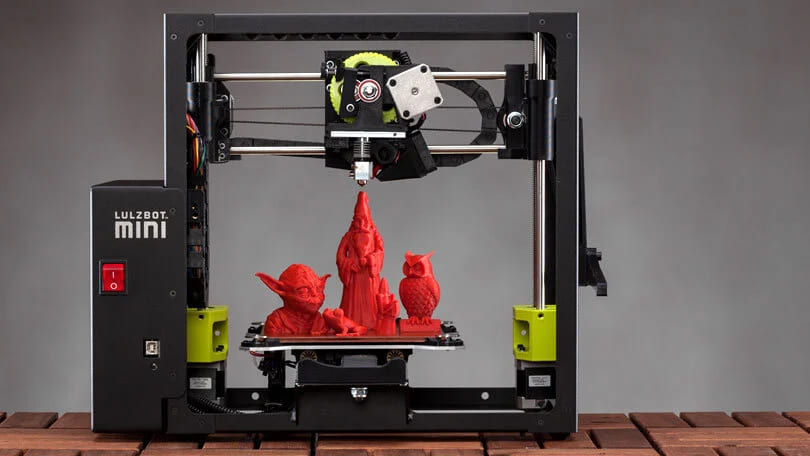
8.Multi-axis CNC Machine Tools
Multi-axis CNC machine tools are more precise and can produce more accurate parts, providing machinists with more processing options.
9.Automatic Tool Changing CNC Machine Tools
Tools can be automatically changed to improve production efficiency and reduce downtime.
5. Types of CNC machine tools by number of axes
2-axis CNC machine
The most basic CNC system, with two moving axes, usually performs basic cutting or drilling, and is suitable for machining fixed workpieces.
3-axis CNC machine
The most common form, capable of manufacturing 2.5-dimensional parts, has three moving axes, can operate on six surfaces of a traditional block of material, but requires repositioning the workpiece.
4-axis CNC machine
In addition to the X, Y, and Z axes, a rotation axis A is added to create arc cuts, increasing machining flexibility.
5-axis CNC machine
There is a rotary motion axis C of the tool or table, which can operate the workpiece on five surfaces without repositioning, producing complex and precise parts.

6-axis CNC machine
A third rotation direction B axis is added to the five-axis, capable of manufacturing parts of various complex shapes.
7-axis CNC machine
With three moving tool axes, three rotating workpiece axes, and a seventh axis E, it can manufacture parts of extremely high complexity.
9-axis CNC machine
Composed of a 5-axis milling machine and a 4-axis lathe, it can produce internal and external features of parts.
12-axis CNC machine
The most sophisticated equipment, with two cutting heads that can move along six axes, greatly improving precision and productivity.
6. Advantages and disadvantages of CNC machine tools
1.Advantages
It can realize unmanned operation and improve production efficiency.
It has high productivity and can complete processing tasks quickly.
It has high precision and repeatability, ensuring the stability of product quality.
It can produce parts with small dimensional deviations and meet high precision requirements.
It can manufacture parts with complex features, expanding the possibility of processing.
The CNC program is easy to modify, which is convenient for product adjustment.
It reduces the risk of human error and improves production safety.
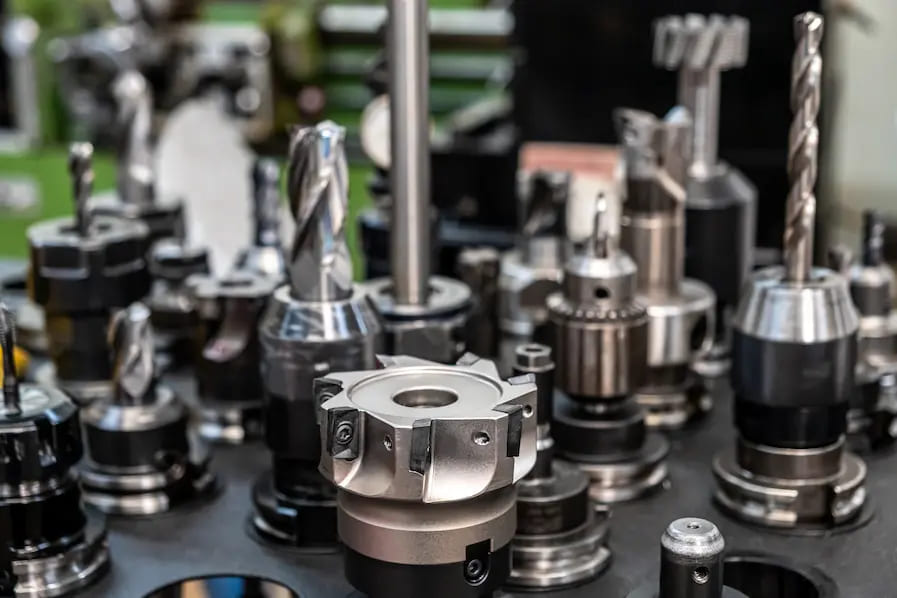
2.Disadvantages
The cost is higher than that of manual machine tools, and the initial investment is large.
It requires expensive skilled labor for operation and maintenance.
It needs regular maintenance, which increases the cost of use.
Maintenance downtime may disrupt production plans and increase costs.
7.Tips for choosing the best CNC machine type
- Identify the application requirements and manufacturing process requirements and determine the required functions.
- Take full account of the part size and ensure that the machine’s working range can accommodate it.
- Determine the required level of accuracy and select a machine with high rigidity and precision components.
- Ensure that the machine can process the materials planned to be used.
- Evaluate the output requirements and select appropriate functions such as fast traversal and automatic tool change.
- Consider whether multi-axis processing of complex three-dimensional shapes is required.
- Choose a reliable and high-precision brand to ensure the quality of the equipment.
- Prioritize easy-to-use control interfaces and compatible software to improve operational convenience.
- Look for suppliers who can provide training and technical support.
- Ensure that technicians can perform repairs and spare parts are easily accessible.
- Check the power requirements of the machine and adjust the workplace to accommodate the equipment.
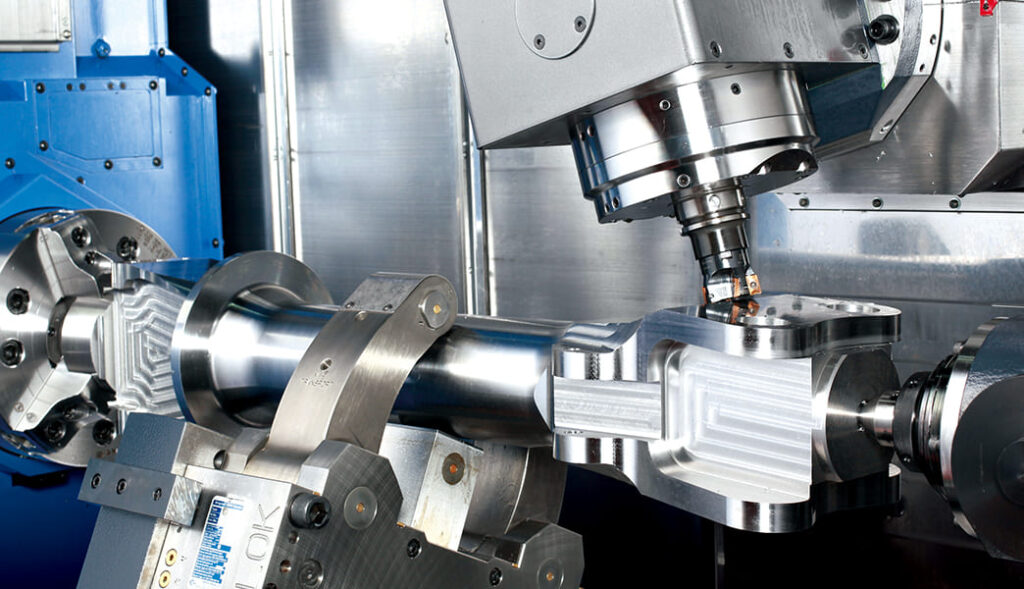
7. Conclusion
As a key equipment in modern manufacturing, CNC machine tools have greatly improved production efficiency and product quality with their computer-controlled accuracy and automation. They can automate many manufacturing operations that were originally completed manually, increase production while reducing waste, and effectively reduce the possibility of human error.
If you are looking for an experienced CNC machining manufacturer, Xavier is your ideal choice. The Xavier team is well-equipped to provide high-quality CNC machining solutions. If you need more information or to discuss your machining needs with us, please feel free to contact us.