the Basics of Dynamic Milling
Dynamic milling is a cutting-edge machining technology that has revolutionized the manufacturing industry. It offers many advantages over traditional milling methods, making it a popular choice for many applications.
In this article, we will dive into the basics of dynamic milling, explore how it works and its various applications.
1.How Dynamic Milling Works
At its core, dynamic milling is a high-speed machining process that involves constantly changing the tool path during the milling operation. Unlike traditional milling where the tool follows a fixed path, the process adjusts the tool path based on the material being cut and the desired outcome.
This adaptability can increase efficiency and improve the surface finish of parts such as coffee machine parts, sewing machine parts, hot spot washing machine parts, and washing machine gasket parts.
The key to dynamic milling is its ability to maintain a constant chip load throughout the cutting process. By adjusting the tool path, the cutting forces are evenly distributed, preventing excessive tool wear and reducing the likelihood of tool breakage. This not only extends tool life, but also increases the overall productivity of the machining operation.
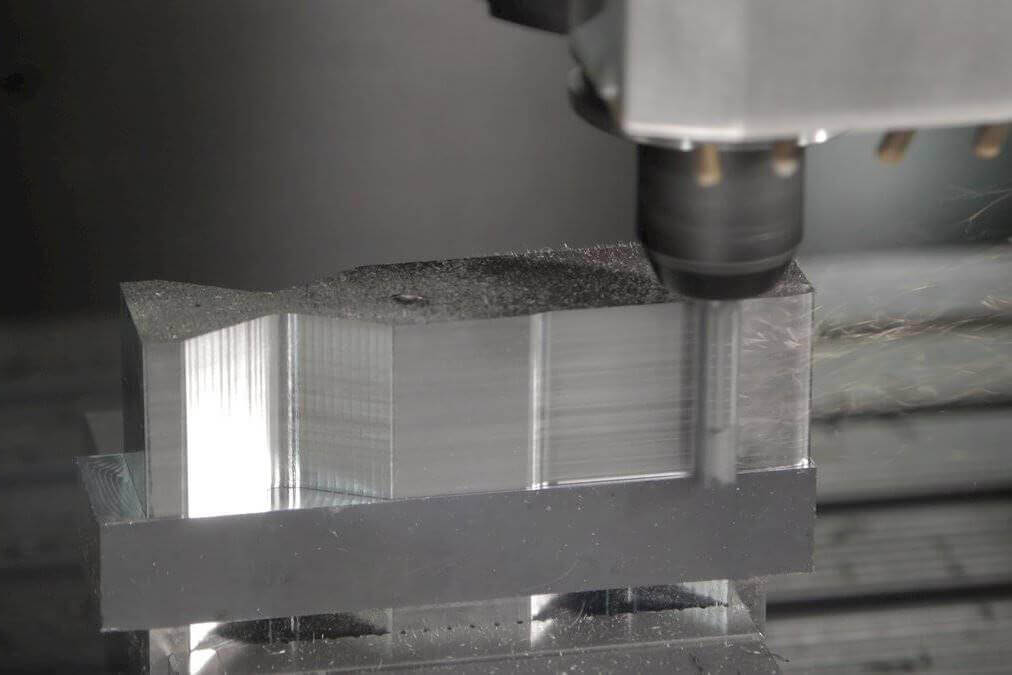
2.Advantages of Dynamic Milling
1) Reduced Cutting Forces
By constantly changing the tool path, the cutting forces are spread over a larger area, minimizing the impact on the tool and workpiece. This reduces vibration and improves stability, which increases machining speed and accuracy.
2) Time Savings
Dynamic milling also offers significant time savings compared to conventional milling methods. This is because by optimizing the tool path, cutting time can be significantly reduced, thereby increasing productivity. In addition, a constant chip load ensures that the tool is always in contact with the material, eliminating the need for multiple passes and reducing overall machining time.
3) Wide Range of Applications
The range of applications for dynamic milling is wide and varied. It is particularly suitable for machining complex geometries and hard materials. The adaptability of the tool path allows for efficient machining of complex shapes such as grooves, slots and contours.
In addition, the process excels in cutting hard materials such as titanium and hardened steel, which are often difficult for conventional milling methods.
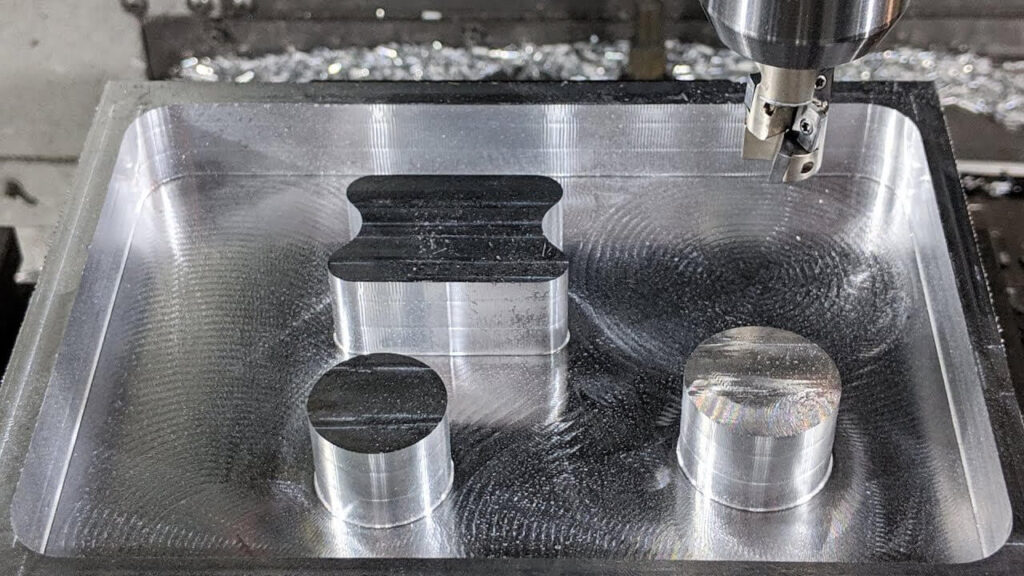
4) Molds and Dies
Another highlight of dynamic milling is the production of molds and dies. Its ability to maintain a constant chip load and reduce cutting forces is ideal for machining complex mold cavities and complex die shapes.
The improved surface finish achieved by the process also eliminates the need for additional finishing operations, saving time and resources.
3.Applications of Dynamic Milling
In the aerospace industry, dynamic milling has become the technology of choice for machining turbine blades and other critical components. High-speed machining capabilities combined with the ability to maintain a constant chip load allow these complex parts to be machined efficiently and accurately. The process saves time and money, making it an attractive option for aerospace manufacturers.
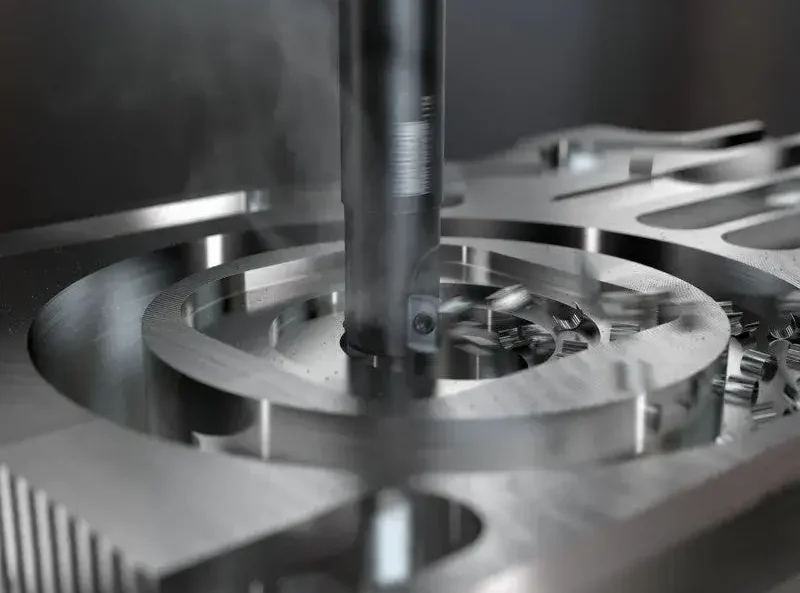
4.In summary
Dynamic milling is a cutting-edge machining technology that offers many advantages over traditional milling methods. By continuously adjusting the tool path, the process ensures a constant chip load, reduces cutting forces and improves stability. This can increase efficiency, improve surface finish and save a lot of time.
With a wide range of applications, dynamic milling has become an indispensable tool in the manufacturing industry, especially for machining complex geometries and hard materials. As the technology continues to advance, the process will play an even more important role in shaping the future of manufacturing.