Efficient aluminum metal cutting: Improving productivity in the manufacturing industry
Aluminum metal cutting is an indispensable part of modern manufacturing and is widely used in aerospace, automobile, construction and other fields. With the continuous advancement of technology, aluminum metal cutting processes are also constantly innovating and improving. This article will introduce in detail several commonly used aluminum metal cutting technologies and their optimization methods to help manufacturing companies improve production efficiency and reduce costs.
1.The importance of aluminum metal cutting technology
Due to its advantages such as light weight, high strength and good corrosion resistance, aluminum alloys are increasingly widely used in modern industry, covering aerospace, automobile manufacturing, architectural decoration and other fields. With the continuous advancement of industrial technology and the growth of market demand, efficient and accurate aluminum metal cutting technology has become a key factor in improving product quality and reducing production costs. Therefore, the continuous development of advanced aluminum metal cutting technology will not only help promote technological innovation in related industries, but also promote the high-quality development of the entire manufacturing industry.
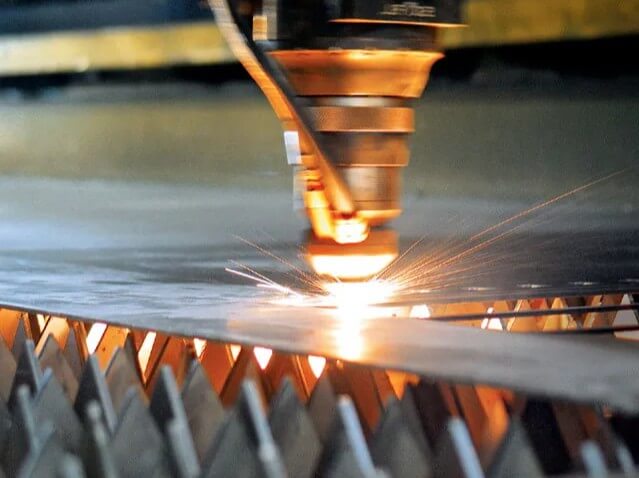
2.Characteristics and cutting difficulties of aluminum alloys
(1) Physical and chemical properties of aluminum alloys
Aluminum alloys have the characteristics of low density, high strength, good electrical conductivity, thermal conductivity and corrosion resistance, which make them the preferred material for many important industrial applications. However, the high reflectivity and high thermal conductivity of aluminum alloys also bring challenges to the cutting process.
(2) Technical difficulties in cutting aluminum alloys
1) High reflectivity:
The high reflectivity of aluminum alloys to lasers makes it difficult to absorb energy during laser cutting, affecting cutting efficiency and quality.
2) High thermal conductivity:
The good thermal conductivity of aluminum alloys will cause heat to diffuse rapidly during cutting, increasing the difficulty of cutting.
3) Easy to generate built-up edge:
In traditional mechanical cutting, aluminum alloys are prone to generate built-up edge, which not only affects cutting accuracy but may also damage the tool.

Summary:
These characteristics require that when cutting aluminum metal, appropriate cutting methods and parameters must be selected to overcome the challenges brought by material properties and ensure cutting quality and efficiency.
3.Analysis of the main cutting technologies for aluminum metal cutting
(1) Laser cutting
1) Process principle:
Laser cutting uses a high-energy-density laser beam to irradiate the surface of the material, rapidly heating the material to a molten or vaporized state, thereby achieving cutting. This technology can process parts of various complex shapes with high cutting accuracy and smooth cuts.
2) Advantages and limitations of laser aluminum metal cutting technology:
Laser cutting of aluminum alloy has the advantages of fast cutting speed, high precision, and non-contact processing. However, the high reflectivity of aluminum alloy has low absorption rate of laser, which affects cutting efficiency. In addition, the initial investment of laser cutting equipment is large, and the operation and maintenance costs are high.
3) Key factors affecting cutting quality:
Parameters such as laser power, wavelength, and cutting speed have a significant impact on cutting quality. Appropriate process parameter selection can significantly improve cutting efficiency and cut quality.
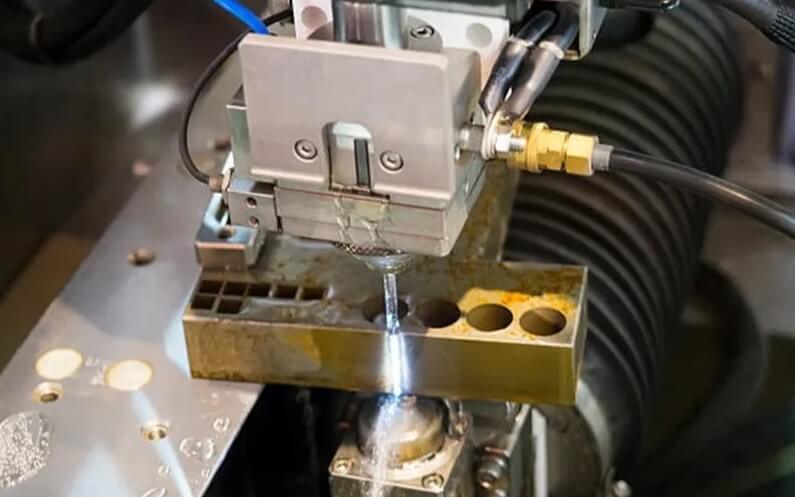
(2) Water jet cutting
1) Process principle:
Water jet cutting uses high-pressure water flow or high-pressure water flow with abrasive added to cut materials. This cutting method is suitable for almost all materials, especially heat-sensitive materials such as aluminum alloy.
2) Advantages and limitations of water jet aluminum metal cutting technology:
Water jet cutting has no heat-affected zone and is suitable for cutting complex shapes and thin plate materials. However, the speed of water jet cutting is relatively slow and the equipment maintenance cost is high.
(3) Plasma cutting
1) Process principle:
Plasma cutting uses high-temperature plasma to heat and melt the material, and blows away the molten material through high-speed plasma flow to form a cutting mouth.
2) Advantages and limitations of plasma aluminum metal cutting technology:
Plasma cutting has a fast speed and is suitable for cutting thicker materials. However, the cutting accuracy and cutting quality are relatively low, which is not suitable for occasions with high precision requirements.
(4) Laser water-cooled cutting
1) Process principle:
Laser water-cooled cutting is a new cutting method that combines laser cutting and water-cooled technology. By introducing water flow cooling during the laser cutting process, the heat-affected zone is effectively reduced and the cutting accuracy is improved.
2) Advantages and application prospects of laser water-cooled aluminum metal cutting technology:
This cutting method significantly reduces the thermal deformation of the material while maintaining the high precision of laser cutting. It is suitable for aluminum alloy cutting with high precision and high quality requirements. Especially in the fields of aerospace and automobile manufacturing, laser water-cooled cutting technology shows great application potential.
(5) Turning
1) Process principle
Turning is a method of cutting aluminum metal by rotating a tool. The workpiece is fixed on the rotating spindle, and the tool moves along the workpiece surface in a straight or curved line. Through the cutting action of the tool, the excess material on the workpiece surface is removed to obtain the desired shape and size. Turning is suitable for processing rotating parts, such as shafts, discs, etc.
2) Advantages and limitations of turning aluminum metal cutting technology:
Turning can produce circular products with high dimensional accuracy, is easy to automate, and has high production efficiency. However, the tool replacement frequency is high, the operator’s technical requirements are high, and it is not suitable for processing products with complex shapes.
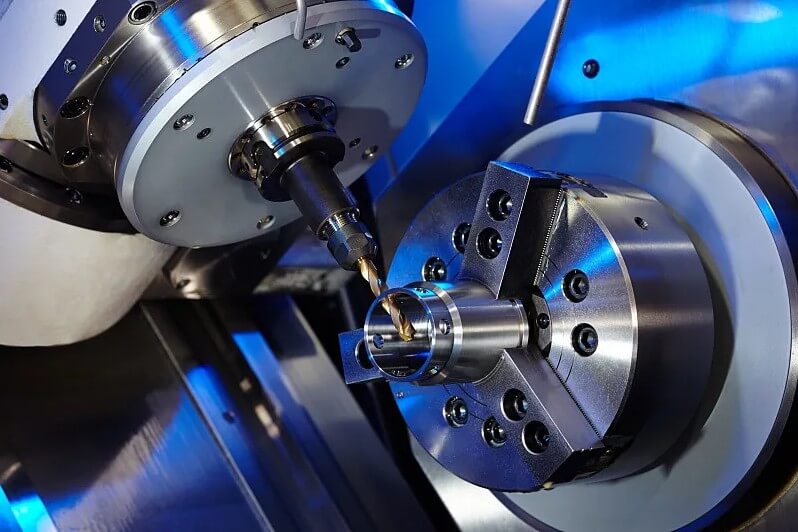
(6) Milling:
1) Process principle
Milling is a process of cutting aluminum metal using a rotating multi-blade tool. When the tool rotates, the workpiece is fed along the X, Y, and Z axes, and the workpiece is continuously cut by the tool’s multiple cutting edges. Milling can process a variety of shapes such as planes, grooves, and formed surfaces, with high processing efficiency and accuracy.
2) Advantages and limitations of milling aluminum metal cutting technology:
Milling can process products with complex shapes, a wide processing range, high accuracy, and good surface finish. However, the machining process may produce built-up edge, which will affect the machining quality and the production efficiency is relatively low.
(7) Wire cutting
1) Working principle
Wire cutting is an electrospark machining method that uses a moving thin metal wire (electrode wire) as an electrode to perform pulse spark discharge cutting on the workpiece. A certain discharge gap is maintained between the electrode wire and the workpiece, and a working fluid medium is poured. Through continuous pulse discharge, the metal is etched and cut into shape.
2) Advantages and limitations of wire cutting aluminum metal cutting technology:
Wire cutting is mainly used to process various complex and fine workpieces with high machining accuracy, short production cycle and low manufacturing cost. However, its speed is relatively slow and is only suitable for conductive materials. In addition, the cutting thickness is limited, and the molybdenum wire is easy to break and needs to be replaced regularly.
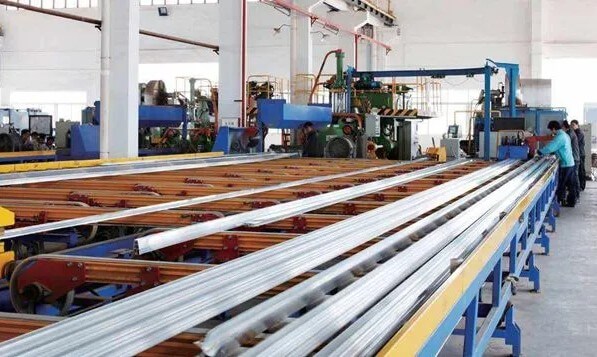
Summary:
These cutting technologies have their own characteristics and are suitable for different industrial needs and application scenarios. In practical applications, choosing the right aluminum metal cutting technology is crucial to improving production efficiency and product quality.
4.Key points of process control for aluminum metal cutting
(1) Select appropriate cutting equipment and tools:
1) Select appropriate cutting equipment
Select appropriate aluminum metal cutting equipment according to the thickness and size of the aluminum material. Commonly used equipment includes CNC cutting machines, CNC cutting machines, sawing machines, etc. CNC equipment is suitable for large-scale, high-precision cutting tasks, while CNC processing equipment is more flexible.
2) Select appropriate cutting tools
Select appropriate cutting tools, such as saw blades, blades, etc. For thicker aluminum alloy materials, special aluminum alloy cutting blades should be used to ensure cutting efficiency and accuracy.
(2) Control cutting parameters:
1) Accurately adjust cutting speed, feed speed and cutting depth.
These parameters directly affect cutting quality and efficiency. For example, high-speed cutting may cause material deformation and increased surface roughness, while low-speed cutting may reduce production efficiency.
2) Select appropriate pulse power supply parameters.
During the EDM wire cutting process, reasonably set parameters such as pulse width, pulse interval and discharge voltage to reduce the adhesion of machining chips and improve machining stability.
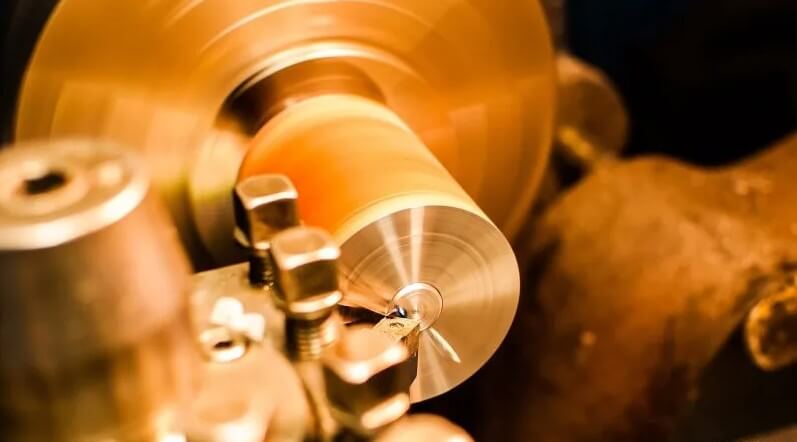
(3) Ensure that the workpiece is clamped firmly:
1) Fix the aluminum workpiece
Before cutting, the workpiece must be firmly fixed on the workbench. Loose clamping of the workpiece may cause the workpiece to move during the cutting process, thereby affecting the aluminum metal cutting accuracy and even causing safety accidents.
2) Choose the appropriate clamping method
Use appropriate fixtures and support structures to ensure that the workpiece remains stable during the cutting process. Especially for large or special-shaped workpieces, it is necessary to carefully consider the clamping method.
(4) Optimize the cooling and lubrication system:
1) Use appropriate coolant
Such as emulsion or special aluminum alloy cutting oil to reduce the temperature of the cutting area, reduce tool wear, and improve the finish of the cutting surface.
2) The coolant should be sufficient and uniform
Ensure that the coolant supply is sufficient and uniform to promptly remove the heat and debris generated by cutting to avoid overheating and material deformation.
5.Practical application of aluminum metal cutting technology
(1) Aerospace field
1) Application cases of aluminum alloys:
In the aerospace field, aluminum alloys are widely used in the manufacture of aircraft structures and components due to their light weight and high strength. For example, aircraft wings, fuselages and engine parts use a large amount of aluminum alloy materials.
2) Aluminum metal cutting technology requirements and standards:
The manufacturing of aerospace parts requires extremely high cutting accuracy and surface quality. Laser cutting and water jet cutting technologies are widely used in this field due to their high precision and heat-affected zone-free characteristics.
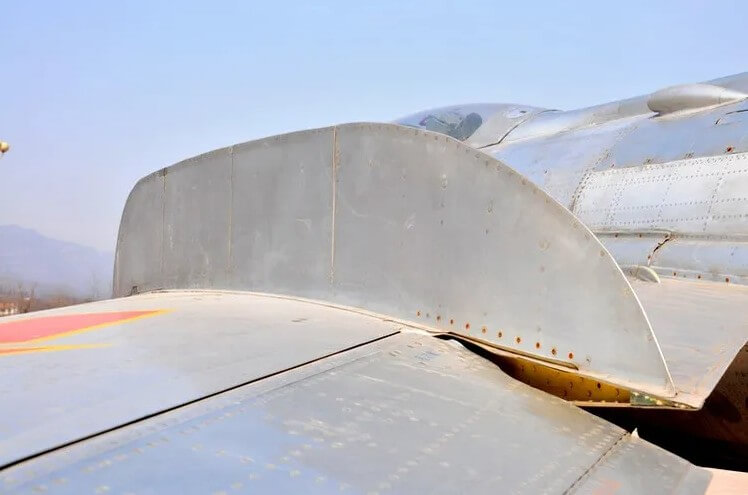
(2) Automobile manufacturing industry
1) Application trend of aluminum alloys:
With the increasing requirements for lightweight and fuel economy of automobiles, aluminum alloys are increasingly used in automobile manufacturing. In particular, the application of aluminum alloys has increased significantly in the manufacture of body structures and parts.
2) Efficiency and economic considerations of aluminum metal cutting technology:
In the automobile manufacturing industry, the efficiency and cost of cutting technology are important considerations for selecting cutting methods. Laser cutting and plasma cutting technologies are widely used in the production of automobile parts due to their high efficiency and economy.
(3) Architecture and decoration
1) Application of aluminum alloys in architecture:
Aluminum alloys are used in the construction industry to manufacture doors, windows, curtain walls, decorative panels, etc. Aluminum alloy materials are not only beautiful and durable, but also easy to process and install.
2) Balance between aluminum metal cutting accuracy and aesthetic requirements:
In architectural decoration applications, cutting accuracy and aesthetic effects are key considerations. Laser cutting and water jet cutting technologies can provide high-precision cutting and smooth cuts to meet the aesthetic requirements of architectural decoration.
Summary:
Through these practical application cases, it can be seen that the application of different aluminum metal cutting technologies in various fields not only meets specific technical requirements, but also promotes the development and innovation of related industries.
6.Summary
In summary, choosing the right cutting method and optimizing related parameters are the key to improving aluminum metal cutting efficiency and quality. Manufacturing companies should reasonably choose saw cutting, laser cutting or wire cutting technology according to their own needs and the characteristics of aluminum parts, and achieve efficient and low-cost aluminum metal cutting processing through fine parameter control and operation skills.
4 Comments