Analysis of the components and manufacturing process of electric valves
As a vital component of industrial automation control systems, the stable and reliable performance of electric valves is inseparable from the precise coordination of various components. This article will analyze the components of electric valves in detail and explore the manufacturing process of these components.
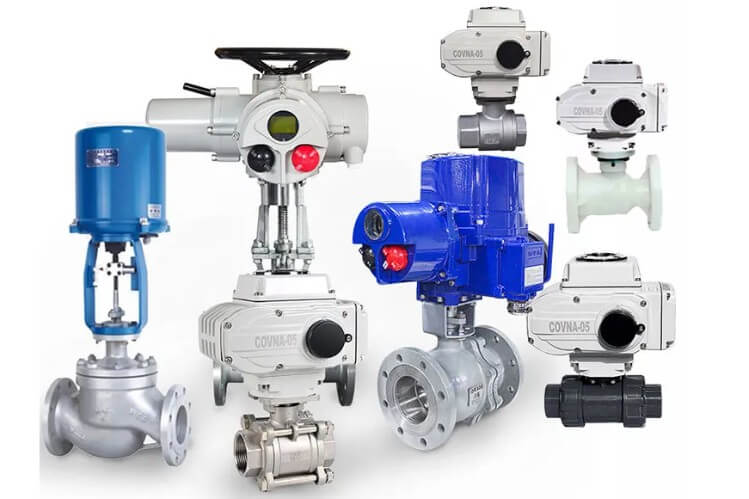
1.Components of electric valves
(1) Electric device
The electric device is the core part of the electric valve, mainly composed of electric actuators, reducers, valve stems, valve cores and other components:
1) Electric actuator:
Through the motor drive, it converts electrical energy into mechanical energy, drives the valve core to move, and realizes the opening and closing of the valve.
2) Reducer:
Reduces the speed of the motor output and increases the output torque to meet the force and speed requirements for the opening and closing of the valve.
3) Valve stem:
Connects the electric actuator and the valve core, transmits power, and makes the valve core move linearly or rotationally in the valve body.
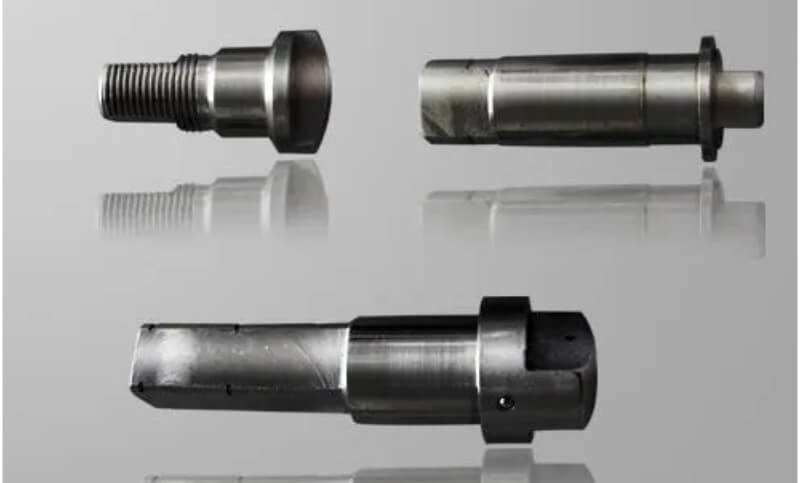
4) Valve core:
Directly controls the on-off and flow of the fluid, and is one of the key components of the valve.
(2) Valve body
The valve body is the main part of the electric valve, usually made of the following materials and includes the following components:
1) Material:
Cast iron, cast steel, stainless steel, etc., select the appropriate material according to the working medium, pressure and temperature.
2) Sealing ring:
Used to ensure the sealing inside the valve and prevent medium leakage.
3) Valve seat:
Cooperates with the valve core to form a sealing pair to control the flow of fluid.
4) Valve disc:
Moves between the valve seat and the valve core to achieve fluid regulation.
(3) Accessories
The accessories of the electric valve mainly include the following parts:
1) Positioner:
Used to accurately control the opening of the valve and improve control accuracy.
2) Handwheel mechanism:
When the electric device fails, the valve can be manually operated.
3) Limit switch:
Detect the opening and closing position of the valve and feedback the signal to the control system.
4) Filter:
Filter impurities in the medium and protect the internal components of the valve.
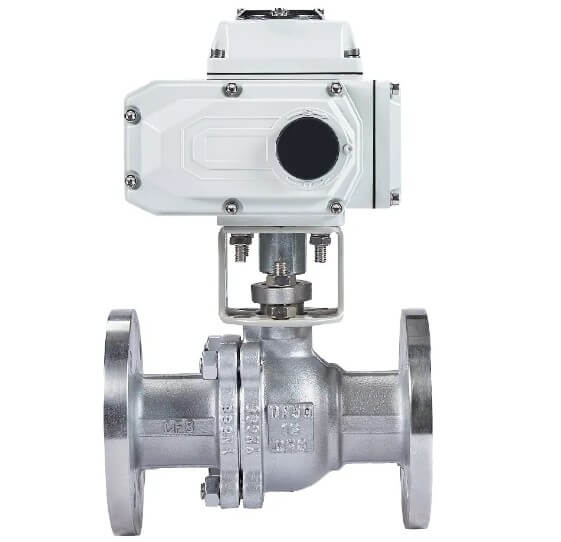
(4) Connectors
Connectors are used to connect electric valves to pipelines or other equipment, mainly including:
1) Flange:
Used to connect valves and pipelines, usually fastened with bolts.
2) Bolts and nuts:
Used to fasten flanges to ensure the sealing and stability of the connection.
(5) Transmission mechanism
The transmission mechanism connects the electric device and the valve body, converting the rotational motion of the electric device into linear motion or rotational motion of the valve core, mainly including:
1) Worm gear:
Commonly used in angular stroke electric valves to achieve 90-degree rotation.
2) Connecting rod and crank:
Convert rotational motion into linear motion to drive the valve core to move.
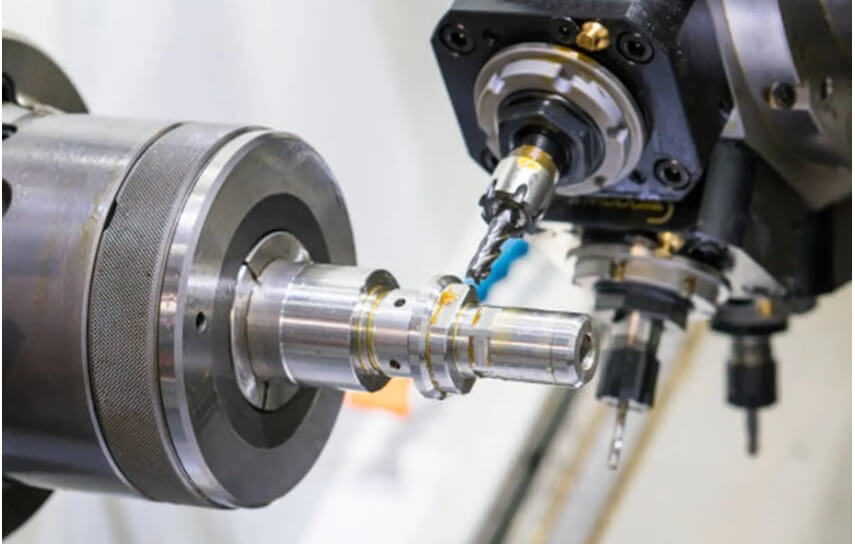
2.Manufacturing process of electric valve parts
(1) Electric device
1) Electric actuator:
The motor housing is usually manufactured by casting or stamping, the internal coil is made by winding, and the rotor, stator and other components are machined and assembled.
2) Reducer:
Gears, worm gears and other parts are processed by precision machining, such as turning, milling, grinding, etc., and then assembled and debugged.
3) Valve stem:
It is manufactured by cold drawing, forging or machining, and the surface is heat treated and finished to improve strength and wear resistance.
4) Valve core:
Depending on the material, it is manufactured by casting, forging or machining, and then surface treated and finished to ensure sealing and corrosion resistance.
(2) Valve body
1) Casting:
Applicable to large electric valve bodies, such as cast iron and cast steel valve bodies, using pressure casting, precision casting and other processes, and then machining and surface treatment.
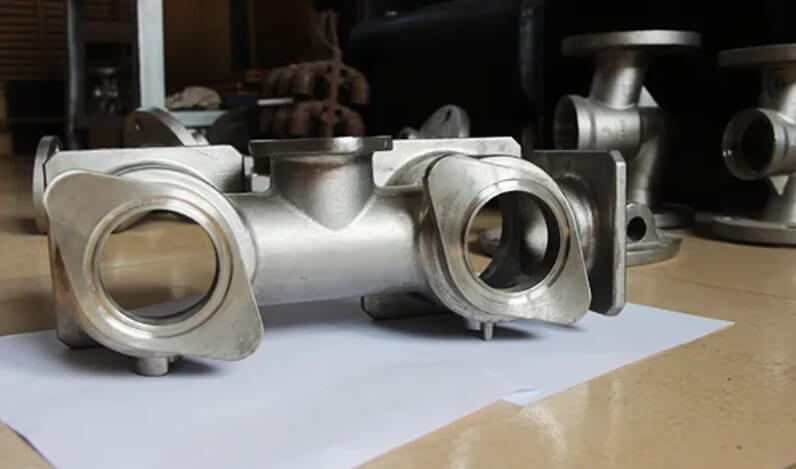
2) Forging:
Applicable to high-pressure and high-temperature valves, such as stainless steel valve bodies, using free forging or die forging processes, and then machining and heat treatment.
3) Machining:
The cast or forged valve body is finely processed, such as turning, milling, drilling, etc., to ensure the dimensional accuracy and surface roughness of the valve body.
4) Welding:
For some valve bodies with complex structures, welding can be used to connect different parts, and then post-weld heat treatment and non-destructive testing are performed.
(3) Accessories
1) Positioner:
Using precision machining and electronic assembly processes, it contains components such as sensors and controllers.
2) Handwheel mechanism:
The handwheel is usually manufactured by casting or injection molding, and the transmission parts are machined and assembled.
3) Limit switch:
The shell is manufactured by plastic injection molding or metal stamping, and the internal switch element is manufactured by electronic assembly.
4) Filter:
The filter screen is usually manufactured by stainless steel weaving or sintering, and the shell is cast or machined.
(4) Connectors
1) Flange:
It is manufactured by casting, forging or machining, and then surface treated and anti-corrosion treated.
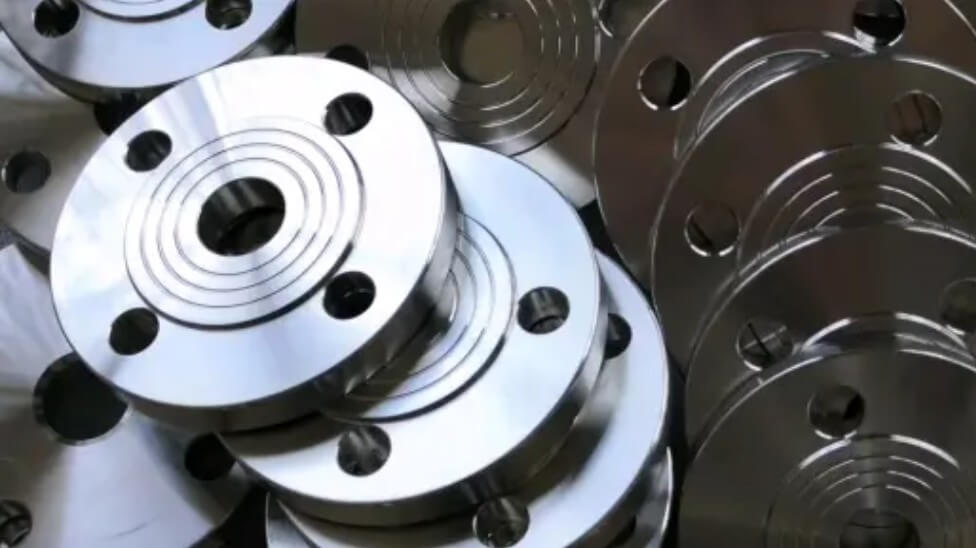
2) Bolts and nuts:
Made by cold heading, machining or heat treatment to ensure strength and corrosion resistance.
(5) Transmission mechanism
1) Worm gear:
Worm gear is usually made by casting or machining, worm gear is made by machining and heat treatment, and then assembled and debugged.
2) Connecting rod and crank:
Made by forging or machining, heat treated and finished on the surface to ensure strength and wear resistance.
Summary:
Through the above detailed analysis of the composition of electric valve components and their manufacturing process, we can see that each component of the electric valve is precisely designed and manufactured to ensure that it can operate stably and reliably under various working conditions. In practical applications, selecting appropriate materials and manufacturing processes for different components is crucial to improving the performance and service life of the electric valve.
3.Application of advanced technology in electric valve manufacturing
(1) CNC machining technology
Improve machining accuracy and efficiency, suitable for complex parts processing. CNC machining technology achieves high-precision machining through computer control systems and is suitable for machining of complex-shaped valve cores, valve bodies and other parts.
CNC machining technology can improve machining efficiency and precision, reduce manual operation errors and ensure the quality of parts.
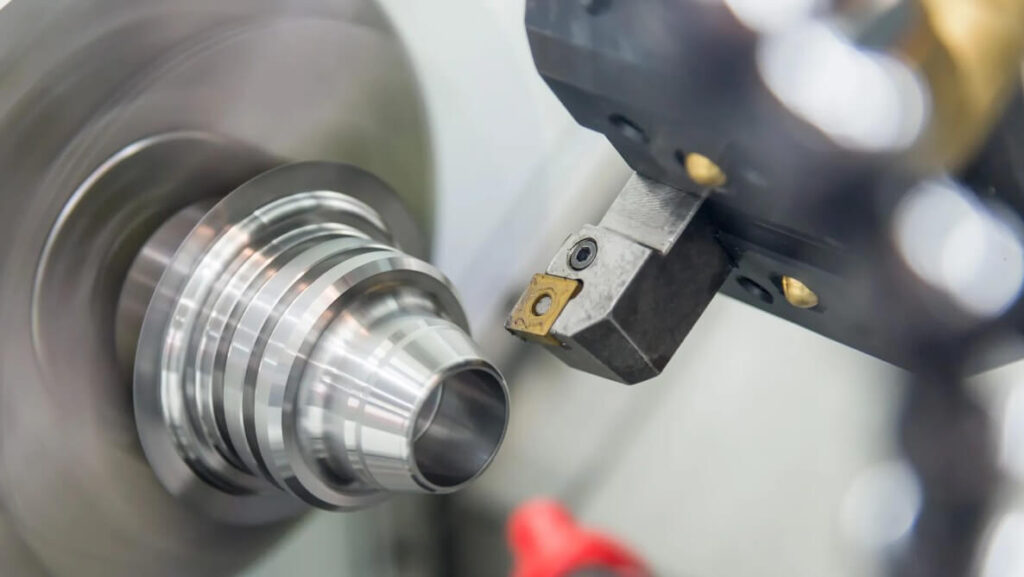
(2) Material surface treatment technology
Improve the surface performance of parts through coating. Material surface treatment technology improves the corrosion resistance, wear resistance and fatigue resistance of parts through coating processes.
For example, the corrosion resistance and wear resistance of valve stems and valve cores can be improved through nickel plating, chrome plating and other processes; the high temperature resistance of valve bodies can be improved through spraying ceramic coatings.
(3) Intelligent manufacturing technology
Automation and informatization of production processes can be achieved. Intelligent manufacturing technology realizes automation and informatization of production processes through automated equipment and information systems, and improves production efficiency and product quality.
For example, mass production and automated assembly of valves can be achieved through automated production lines; data collection and analysis of production processes can be achieved through information systems, improving the efficiency of production management and quality control levels.
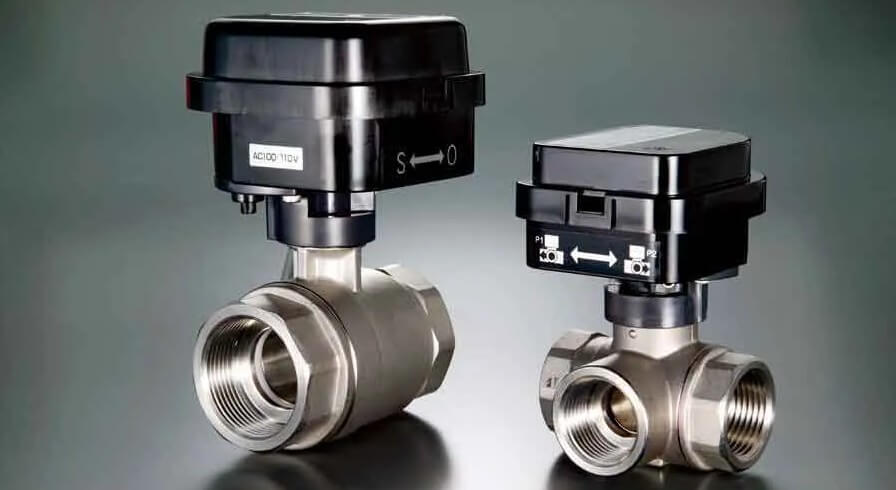
4.Summary
As an important industrial control device, the composition and manufacturing process of electric valve components directly affect its performance and use effect. Understanding the composition and manufacturing process of electric valve components will help us better select and use electric valves and improve the efficiency and reliability of industrial automation control systems.