Casting Techniques for Fabricating Aluminum Parts
Aluminum is a versatile and widely used material in various industries due to its excellent properties such as lightweight, high strength, and corrosion resistance.
When it comes to fabricating aluminum parts, casting techniques are commonly employed. Casting is a manufacturing process that involves pouring molten metal into a mold and allowing it to solidify. In this section, we will explore some of the casting techniques used for fabricating aluminum parts.
The most widely used casting technology for aluminum parts
One of the most widely used casting techniques for aluminum parts is sand casting. Sand casting involves creating a mold by packing sand around a pattern of the desired part. The sand mold is then filled with molten aluminum, which solidifies to form the desired shape. Sand casting is a cost-effective method that allows for the production of complex shapes and large parts. However, it may not be suitable for parts that require high dimensional accuracy.
Another casting technique commonly used for aluminum parts is die casting. Die casting involves injecting molten aluminum into a steel mold, known as a die, under high pressure. The molten metal quickly solidifies to form the desired shape. Die casting offers excellent dimensional accuracy and surface finish, making it ideal for producing parts with tight tolerances. It is also a highly efficient process, allowing for high production rates. However, die casting requires the use of specialized equipment and is more expensive than sand casting.
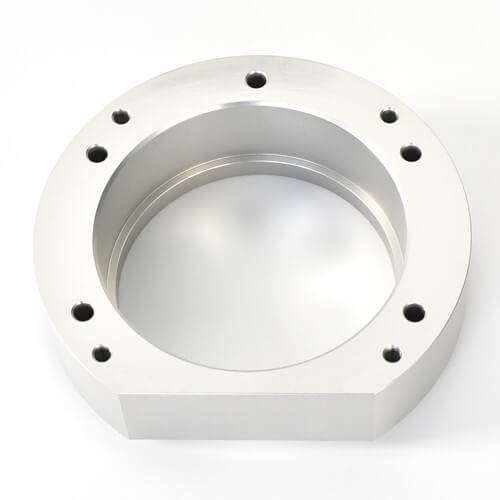
Investment casting is another casting technique used for fabricating aluminum parts. This process involves creating a wax pattern of the desired part, which is then coated with a ceramic shell. The wax is melted out, leaving behind a cavity in the ceramic shell. Molten aluminum is then poured into the cavity, filling the space left by the wax pattern. Once the aluminum solidifies, the ceramic shell is broken away, revealing the finished part. Investment casting allows for the production of highly complex and intricate parts with excellent surface finish. However, it is a time-consuming process and may not be suitable for high-volume production.
Gravity casting, also known as metal mold casting, is a casting technique that relies on gravity to fill molten aluminum into a mold. The mold in gravity casting is usually made of steel or cast iron and is preheated and coated with a release agent to facilitate removal of the solidified portion. At the same time, gravity casting is also a cost-effective method because it can produce parts with good dimensional accuracy and surface finish. However, it is not suitable for producing thin-walled or complex-shaped parts.
In conclusion, casting techniques are widely used for fabricating aluminum parts due to their versatility and cost-effectiveness. Sand casting, die casting, investment casting, and gravity casting are some of the commonly employed techniques. Each technique has its advantages and limitations, and the choice of technique depends on factors such as the desired part complexity, dimensional accuracy, surface finish, and production volume. By understanding the different casting techniques available, manufacturers can select the most suitable method for fabricating aluminum parts to meet their specific requirements.