Advantages of CNC Precision Components
CNC precision Components have become an integral part of various industries due to their numerous benefits. These parts are manufactured using computer numerical control (CNC) machines, which provide high precision and accuracy in the production process. They include but are not limited to cnc lathe machine parts, cnc machine automotive parts, and cnc milling machine parts, among others.
In this article, we will explore the benefits of CNC precision parts and why they are preferred over traditional manufacturing methods.
Advantages of CNC Precision Components
One of the main advantages of CNC precision parts is its high accuracy, such as cnc lathe machine parts, cnc machine automotive parts, and cnc milling machine parts. CNC machines are programmed to follow specific instructions, ensuring that each component is produced with the utmost precision. This level of accuracy is crucial in industries such as aerospace, automotive, and medical, where even the slightest deviation can have significant consequences. With CNC precision components, manufacturers can achieve tight tolerances and ensure that each part meets the required specifications.
Another advantage of CNC precision components is their consistency. Traditional manufacturing methods often rely on manual labor, which can lead to variations in the final product. CNC machines, on the other hand, eliminate human error and produce components with consistent quality. This consistency is particularly important in industries that require mass production, as it ensures that each component is identical to the next.
CNC precision components also offer increased efficiency in the manufacturing process. CNC machine tools can run continuously 24 hours a day without rest. This enables faster production times and higher output rates compared to traditional methods. In addition, CNC machines can be programmed to perform complex tasks such as multi-axis machining and simultaneous operations, further increasing efficiency and reducing production time.
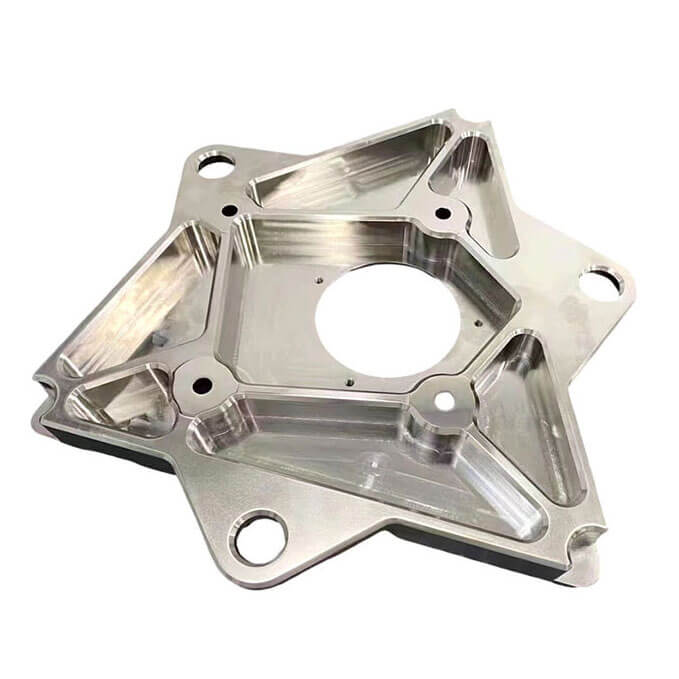
Furthermore, CNC precision components offer greater flexibility in design and customization. With CNC machines, manufacturers can easily modify the design of a component by simply changing the program. This flexibility allows for quick prototyping and iteration, reducing the time and cost associated with traditional manufacturing methods. Additionally, CNC machines can produce intricate and complex shapes that would be difficult or impossible to achieve with conventional machining techniques.
In terms of cost-effectiveness, CNC precision components offer several advantages. While the initial investment in CNC machines may be higher compared to traditional machines, the long-term benefits outweigh the costs. CNC machines require minimal human intervention, reducing labor costs and the risk of errors. Additionally, CNC machines have a longer lifespan and require less maintenance compared to traditional machines, resulting in lower operating costs over time.
Lastly, CNC precision components contribute to improved safety in the manufacturing process. With CNC machines, operators are not exposed to the same level of risk as in traditional machining methods. CNC machines are enclosed, reducing the chances of accidents and injuries. Additionally, CNC machines can be equipped with safety features such as automatic tool changers and collision detection systems, further enhancing workplace safety.
In conclusion, CNC precision components offer numerous advantages over traditional manufacturing methods. Their high level of accuracy, consistency, efficiency, flexibility, cost-effectiveness, and safety make them the preferred choice in various industries. As technology continues to advance, CNC machines will likely play an even more significant role in the manufacturing sector, revolutionizing the way components are produced.