A Comprehensive Guide to Gas Welding: Technology, Benefits, Applications
Gas welding is an effective way to connect metal parts and is widely used in many industries. This article will analyze various aspects of gas welding in depth, including its working principle, advantages, common applications, as well as its limitations and safety risks, to provide users with a comprehensive reference when choosing welding.
1、What is gas welding?
Gas welding is a process that uses a manually driven flame to melt and weld metal workpieces. The flame is created by a fuel gas (usually acetylene) mixed with oxygen and can reach temperatures as high as 3200°C (5792°F). The solder paste filler is surrounded by the molten metal edge and can weld a variety of metals, as well as cutting and brazing.
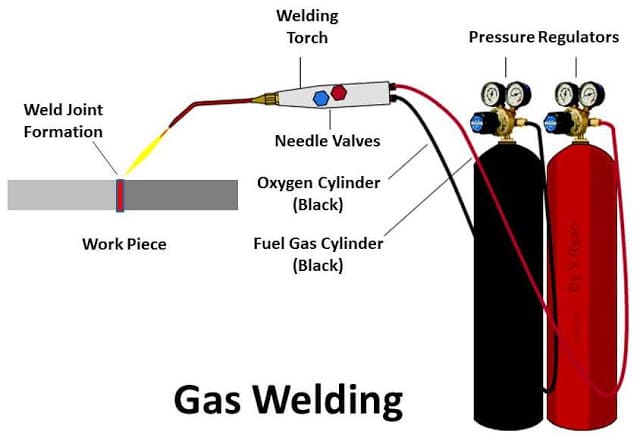
2、The role of gas welding torch
The gas welding torch is the key equipment for gas welding, which mixes oxygen with fuel gas to produce flame. It consists of a body, a mixing chamber, and a nozzle, which can adjust the ratio of oxygen and acetylene, control the flame size and temperature to adapt to different base materials and achieve a firm connection.
3、Commonly used gas welding technology types
1.Oxyacetylene welding
It is one of the most popular welding methods. It uses acetylene gas and oxygen to react to produce flames. It can melt a variety of metals and the maximum temperature can reach about 3500 degrees Celsius. Professional welders can use different flame lengths or patterns to meet welding requirements.
2.Oxy-fuel welding process
Propylene welding: Propylene is used instead of acetylene gas, which burns cleaner and is suitable for applications that limit smoke generation.
Natural gas welding: It uses gas fuel and oxygen, which is less used and suitable for light welding operations.
Oxyhydrogen welding: It uses oxygen and hydrogen as fuel, produces obvious flames when burning, and the welding process needs to be precisely controlled to avoid carbon contamination.
3.Other gas welding methods
TIG (tungsten inert gas) welding: It uses non-consumable tungsten electrodes and inert gases such as argon to protect the weld. It is suitable for welding thinner materials and is widely used in the aerospace and automotive industries.
MIG (metal inert gas) welding: Continuously feed the wire into the welding pool and is covered by inert gas. It is suitable for welding various metals. It is popular in manufacturing plants and metal processing projects and is simple and fast to operate.
Plasma arc (PAW) welding: An arc is established between the electrode tip and the workpiece to generate plasma, providing a narrow heat concentration area, low heat input, and no thermal deformation.
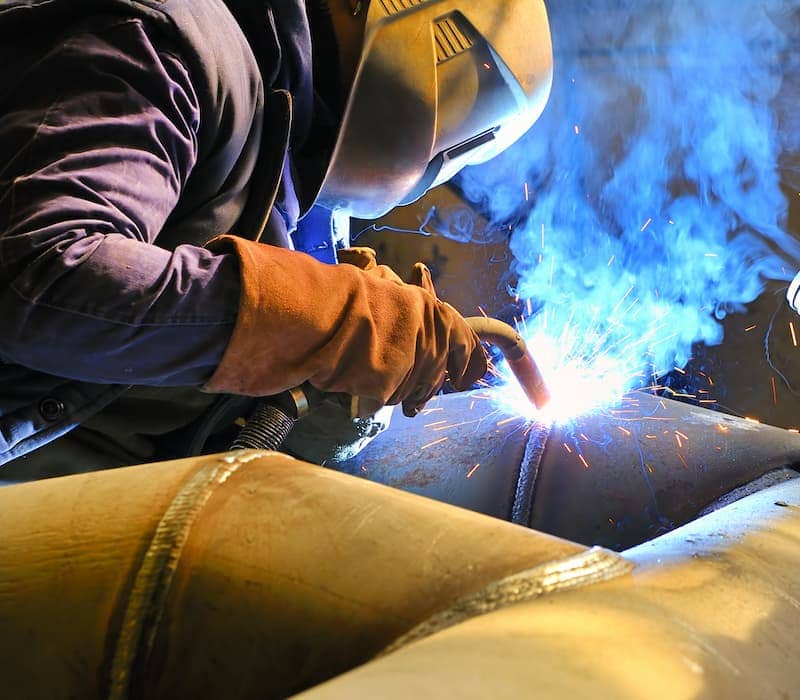
4、Equipment required for gas welding
1.Gas cylinders
High-pressure cylinders used to store welding gases such as oxygen, acetylene or propane are key equipment. Each cylinder is equipped with a regulator to control the gas flow.
2.Welding torches
The welding torch is responsible for mixing and delivering gases to the flame generator. It usually includes controls to adjust the flame characteristics and a nozzle to direct the flame to the workpiece.
3.Filler rods
Consumable rods used to add material to the weld joint. The choice of filler rod depends on the base metal to be welded.
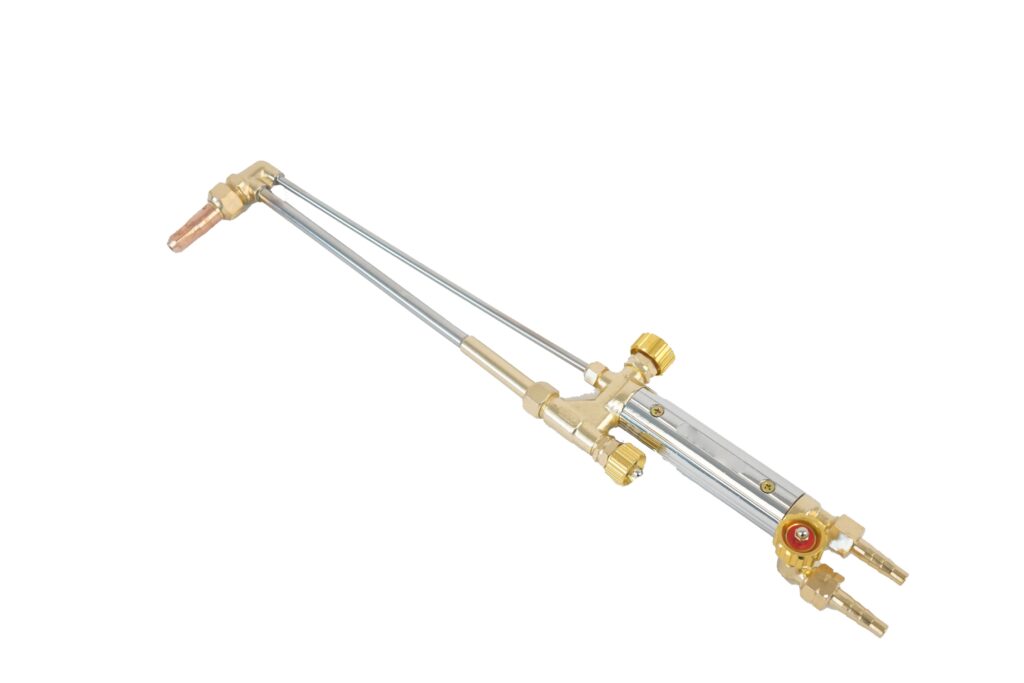
4.Protective equipment
Basic personal protective equipment includes welding masks, diffuser filters, welding gloves and other flame-resistant clothing to protect the body from sparks and high temperature burns.
Welding masks are key safety equipment that protects the eyes and head from the high levels of ultraviolet and infrared radiation generated by the welding arc.
Welding gloves protect against heat, flames and molten materials. High-quality gloves are made of durable materials such as leather to provide thermal protection and control of the hands.
5.Welding equipment carts
Mobile carts can help collect, transport and store gas cylinders and welding guns, improving convenience in the work environment.
5、What metals can be welded with gas?
1.Mild steel
Mild steel is one of the most commonly used steels because it is easily available and has good gas weldability. Gas welding techniques such as oxyacetylene welding can produce strong joints on mild steel, which is suitable for repairing and manufacturing structural parts.
2.Cast iron
Cast iron is often fixed by gas welding. Through reasonable heat distribution and suitable flux materials, crack treatment and drying can be achieved, which helps to evenly distribute heat.
3.Aluminum
Aluminum is easy to deform at high temperatures, but gas welding with aluminum-containing electrodes can achieve good results. The temperature stability of the steel needs to be well controlled to prevent deformation.
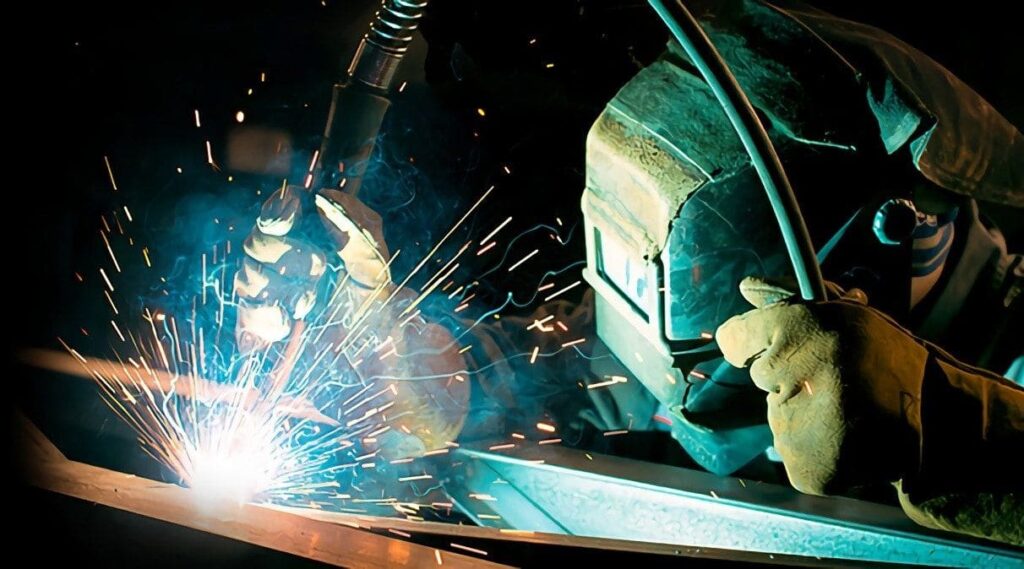
6、Technical advantages of gas welding
1.Strong mobility
Gas welding equipment is more portable than electric welding systems and can be used in remote areas or on-site.
2.Wide applicability
It can be used with a variety of metals (such as steel and aluminum), expanding the scope of application.
3.High flame concentration
Welders can control the direction of the flame well and heat fragile parts without causing deformation.
4.Adapt to bad weather
It can be carried out in adverse weather conditions, which may be difficult or impossible for electric welding methods.
5.Low investment cost
The initial purchase expenditure of equipment and consumables is low, suitable for small businesses and hobbyists.
7、Gas welding applications
1.Manufacturing
Used for the manufacture and repair of metal components, producing complex geometries and strong structures.
2.Automotive Industry
In the automotive industry, gas welding helps to join car frames and some area panels, achieving lightweight and strong structures.
3.Construction Industry
The construction industry uses gas welding to join pipes or structural steel components used in building or infrastructure construction.
4.Aviation Industry
Used for the manufacture of aircraft components with great attention to detail and safety measures.
8、Disadvantages and limitations of gas welding
Common Disadvantages
1.Low Heat Concentration
Gas welding uses a gas flame, which has a lower heat concentration than arc welding. This will result in longer operation time, which is inefficient and impractical for high-speed production lines.
2.External Force Influence
It is susceptible to interference from wind and other external forces, which may blow out the flame and is limited in external operations.
3.Difficult Operation
It is difficult for the operator to accurately control the flame, and when handling thin and fragile objects, problems such as burn-through or excessive deformation are prone to occur.
4.Hardware and Gas Safety Issues
Due to the high gas content, a series of precautions must be taken to ensure safety, which increases the complexity of the work.
Limitations in materials and thickness
1.Influence of metal properties
For metals such as high-strength steels containing nickel or titanium alloys and aluminum that require process control to avoid warping or insufficient melting. The conductivity of the material will also affect the feasibility of gas welding, and materials with good conductivity may not be able to fully penetrate the weld.
2.Limited scope of application
Generally applicable to metals with a thickness of less than 1/4 inch. In contrast, the heat generated by the arc is more advantageous when welding thicker materials, while the heat treatment capacity of the water-gas flame is relatively weak.
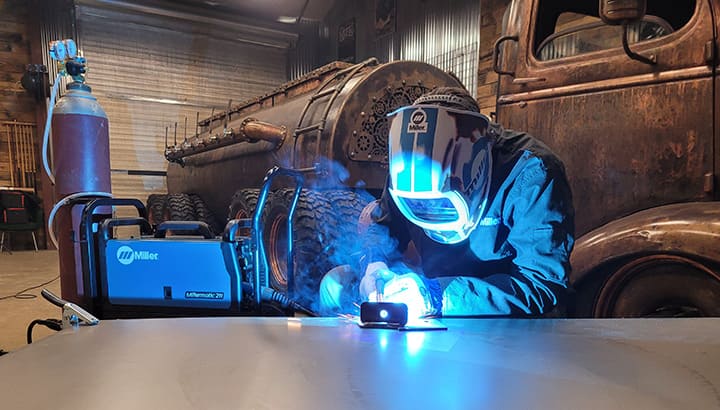
Health and safety risks
1.Smoke hazards
Operators are exposed to smoke, which may cause neurasthenia, and effective ventilation measures need to be maintained.
2.Explosion and fire risks
Due to the use of open flames and pressurized gas cylinders, the possibility of explosions and fires is higher, especially when flammable materials enter the conveying system. Measures such as avoiding the use of flammable materials and safely handling and storing gas cylinders should be taken.
3.Physical injury risks
Burns, high-temperature equipment injuries and cuts are also risks faced by workers. Wearing protective equipment can reduce such risks.
9、Conclusion
Gas welding is an important welding technology that plays an important role in many industries and has certain advantages and characteristics. However, it also has disadvantages, limitations and health and safety risks. Despite this, gas welding is still an indispensable welding technology that contributes to industrial development.
If you are looking for an experienced machine fabricator, Xavier is undoubtedly your best choice. The Xavier team has excellent equipment and is good at all types of machining to fully meet your machining needs. If you need more information or want to discuss your machining needs with us, please feel free to contact us.
1 Comment