Glass CNC machining: What are the different machining technologies used?
Glass CNC machining uses a variety of specialized techniques to achieve precision and detail that cannot be matched by hand machining, and machining g10 is one of them. Each technique has specific applications and inherent limitations that make it suitable for specific tasks in the glass machining industry. Through machining training or cnc machining training near me, you will learn that glass machining is also very versatile.
1.Glass CNC Machining Techniques
- Milling: Involves the removal of glass material to create features such as grooves and channels. It is well suited to creating complex geometries in glass with high precision.
- Drilling: Used to create holes of various diameters, which are essential in many glass applications, from simple water jet holes to complex optical components.
- Boring: Used to enlarge pre-drilled holes to precise dimensions, improving the finish and tolerance of the holes.
- Engraving: Allows for complex designs on the surface of glass, often used in decorative and artistic applications.
- Grooving: A technique for cutting narrow grooves in glass, often used to install seals and other components.
- Grooving: Similar to grooving, but involves cutting grooves in the glass for assembly purposes or stress relief.
- Grooving: involves removing material from a larger area to create a groove in the glass, allowing for the placement of other components.
- Grinding: This process adjusts the surface finish of the glass, removes minor flaws, and prepares the surface for further processing.
- Water jet cutting: Cuts glass using a high-pressure water jet with mixed abrasive particles, characterized by its ability to cut shapes with minimal material waste and without inducing thermal stress.
- Polishing and grinding: These finishing processes enhance the surface smoothness of the glass, improving its clarity and quality for optical applications.
- Edge grinding and polishing: This technology is essential for safety and aesthetic reasons to ensure that the edges of glass parts are smooth and well-processed.
- Thermal and chemical strengthening: Processes that enhance the durability and resistance of glass to thermal and physical stress by changing the chemical structure or surface state of the glass.
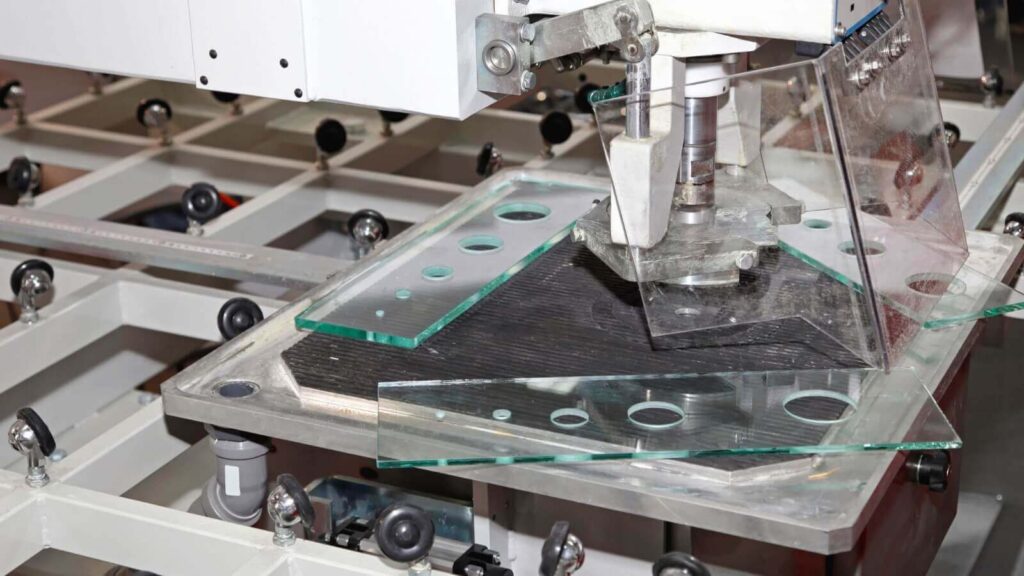
2.What types of glass are suitable for CNC machining?
Choosing the type of glass suitable for CNC machining is crucial because each glass has unique characteristics and applications that make it suitable for specific machining tasks.
The following is a detailed look at the main types of glass used in CNC glass processing and their respective specifications:
- Borosilicate Glass: Borosilicate glass is known for its excellent resistance to thermal shock and chemical corrosion and is often used in applications that require high temperature resistance and durability. Its low coefficient of expansion makes it ideal for high-precision optical components and laboratory glassware.
- Soda-lime glass: Soda-lime glass is the most common type of glass and is mainly used for windows, bottles, and general glassware. This glass type is easier to process, but is less resistant to heat and chemical stress than borosilicate glass.
- Fused quartz: This glass has high optical clarity and excellent thermal stability, making it ideal for demanding environments such as aerospace and telecommunications. Fused quartz is often used to make mirrors and lenses, which require high precision and minimal thermal expansion.
- Aluminosilicate Glass: Aluminosilicate glass has a high strength-to-weight ratio and good heat resistance and is used in smartphone screens and other high-strength display applications. Its processing requires precise control to maintain its structural integrity.
- Lead Glass: Lead glass has a high refractive index and high density, making it an ideal choice for optical components such as lenses and prisms that require enhanced light scattering. Due to the lead content, special handling and processing techniques are required.
- Quartz Glass: Quartz glass is known for its high purity, thermal stability and chemical stability, and is used in semiconductor manufacturing and UV lighting systems. It requires highly specialized CNC machining technology to handle its hardness and brittleness.
3.What are the advantages of glass CNC machining?
Glass CNC machining has several key advantages that are essential in high-stakes manufacturing and artistic environments:
- Precision: CNC machine tools operate with high precision and can produce glass parts with precise specifications. This precision is critical to industries such as aerospace and electronics, as even the smallest deviation can affect the function of the final product.
- Customization: One of the outstanding advantages of CNC machining is its ability to accommodate complex designs. This customization capability allows manufacturers to produce unique and complex shapes that are difficult or impossible to achieve with traditional glass forming methods.
- Repeatability: CNC machining ensures that every part produced is of the same specifications and quality, regardless of quantity. This repeatability is essential to maintaining quality control in a mass production environment.
- Speed: Compared to manual machining, CNC machining significantly reduces the time required to go from design to production. This efficiency is essential to meeting tight deadlines and increasing productivity.
- Efficiency: CNC machining allows glass to be precisely cut to preset specifications, minimizing waste. This efficient use of materials not only reduces costs but also reduces environmental impact.
- Repeatability: In mass production, the ability to accurately replicate glass parts is essential. CNC technology ensures that each product is a perfect match to the prototype, maintaining batch-to-batch consistency.
- Versatility: CNC machines can handle a wide range of glass types and designs, making them a versatile tool for the glass manufacturing industry. This versatility allows for the exploration of new products and applications.
- Reduced Waste: Precision machining means less material is wasted during the cutting and forming process. This efficiency not only has economic benefits, but also meets sustainability goals by reducing waste.
- Clean Cuts: CNC machines produce clean and smooth cuts, reducing the need for additional finishing steps. This cleanliness is particularly important in the production of medical devices and other applications where surface smoothness is critical.
- Safety: Automated CNC processes improve safety by reducing the need for direct human interaction with cutting equipment. This is particularly important in glass processing, where handling and cutting can pose a risk of injury.
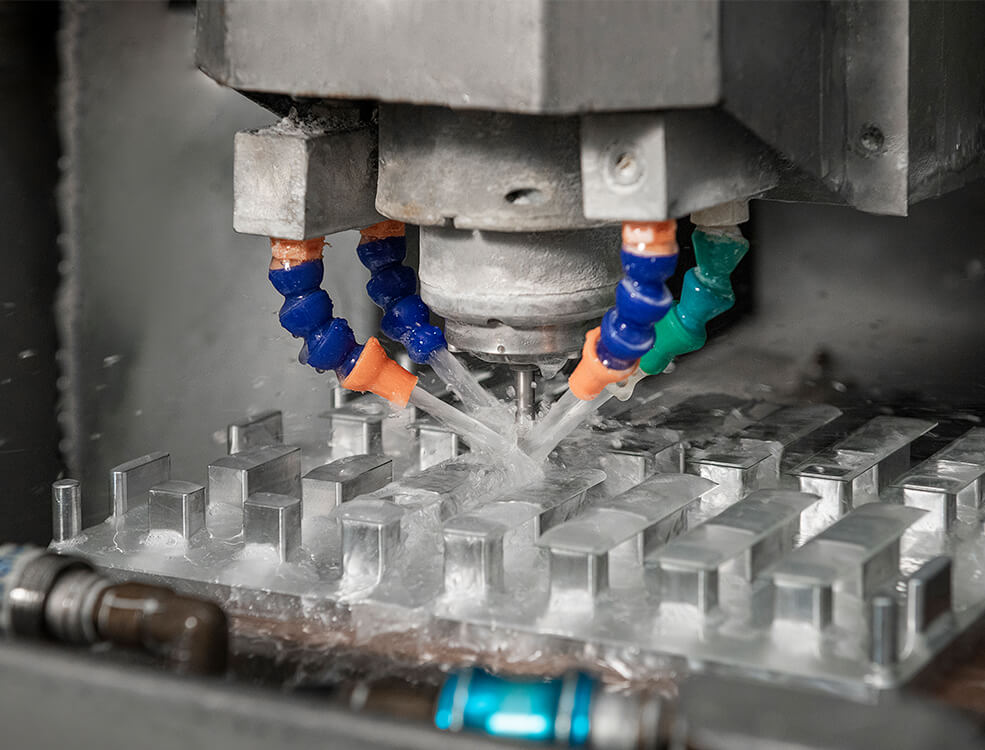
4.Are there any limitations to glass CNC machining?
While glass CNC machining offers numerous advantages, it also has certain limitations that the industry must consider before choosing this method.
Understanding these disadvantages is essential to optimizing the use of CNC technology in glass processing.
- Fragile Materials: Glass is inherently brittle, which presents challenges to the machining process. Even with advanced CNC technology, the risk of cracking or shattering cannot be completely eliminated, especially when cutting complex or thin glass sheets.
- Cost: CNC machining involves a significant initial investment, including machinery and setup costs. For smaller projects or businesses, these costs may be prohibitive, and CNC machining is less economical than other methods such as laser cutting or manual techniques.
- Operational Complexity: Operating CNC machinery requires skilled personnel who understand both the software side and the hardware side. Specialized training and knowledge are required, which adds another layer of cost and complexity to the project.
5.What are the applications of glass CNC machining?
Glass CNC machining is versatile and supports a wide range of applications across a wide range of industries. Its precision and ability to produce complex shapes make it an indispensable machining tool in many high-tech fields.
- Optical Industry: Produces precision lenses, prisms, and other components that are critical to optical clarity and performance.
- Semiconductor Industry: Used to manufacture wafers and other precision components that require precise dimensions and smooth surfaces.
- Biotechnology and Medical Devices: Essential for manufacturing complex devices used in medical diagnosis and treatment, where precision is critical to device efficacy.
- Aerospace and Defense: Provides the ability to manufacture strong yet lightweight glass components for spacecraft and military equipment.
- Automotive industry: used to manufacture durable and aesthetic glass parts such as windows, mirrors and display covers.
- Electronics and consumer goods: provides components for electronic devices, including glass screens and protective covers that require high precision and durability.
- Home appliances and decoration: CNC machining helps design decorative elements and functional parts of home appliances that combine beauty with functionality.
- Telecommunications: involves the machining of glass parts that are integral to optical fiber and other communication technologies.
- Art and design: enables artists and designers to realize complex sculptures and artworks that require precise and repeated modifications.
10 Research and development: supports experimental design and prototyping, allowing researchers to explore new applications and innovations in the use of glass.
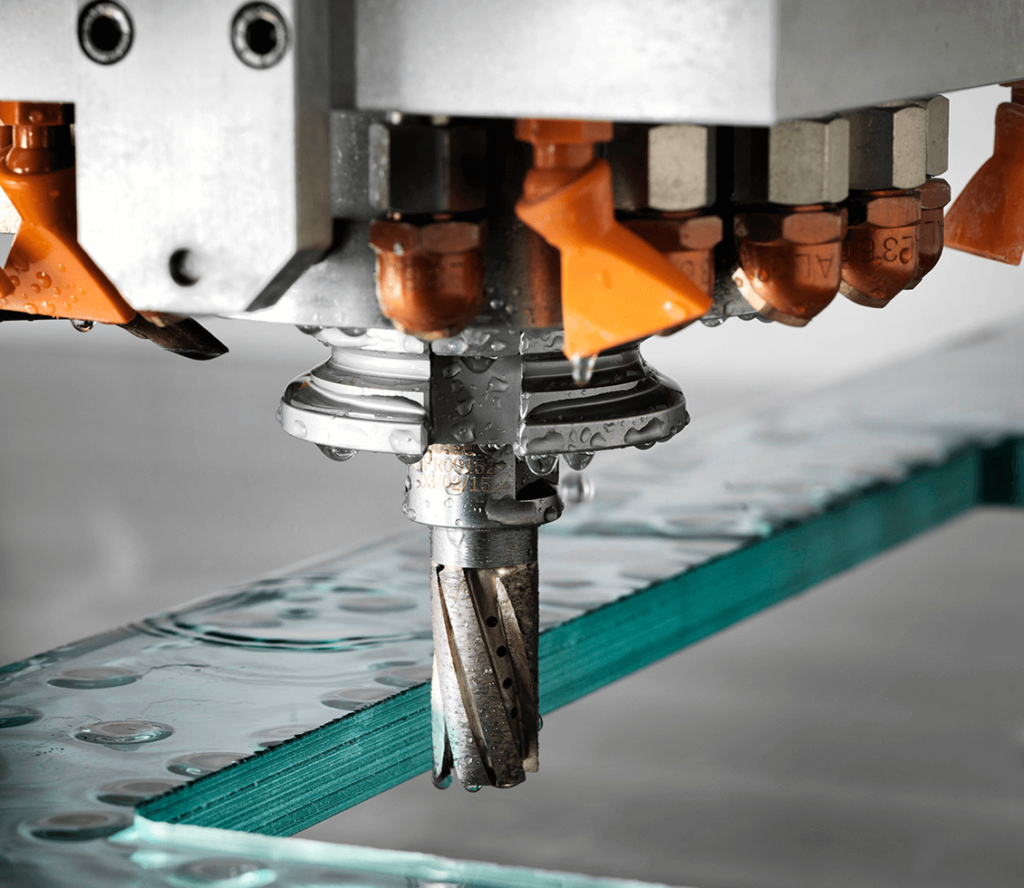
6.Is glass CNC machining expensive?
Glass CNC machining involves considerable financial expenditure, which is affected by a variety of factors that can increase the costs associated with this precision technology.
Factors affecting the cost of glass CNC machining:
- Equipment cost: The investment in CNC machine tools is huge, and advanced models cost hundreds of thousands of dollars. The precision required for glass machining requires high-end equipment, which increases the initial capital expenditure.
- Setup and Operation: Setting up a CNC machine for glass processing requires expertise and skills. Operating costs, including labor, maintenance, and machine running costs, account for a large portion of the total expense.
- Material Cost: The type of glass used varies widely in price, with specialty glasses such as borosilicate or fused quartz costing more due to the careful handling they require due to their unique properties.
- Production Volume: Higher production volumes can reduce the cost per unit through economies of scale, while small batches can be prohibitively expensive due to the time and cost of setup and teardown.
- Design Complexity: More complex designs require more machine time and more elaborate tooling, which increases costs. Complex cuts and engravings increase production time and require greater precision, which increases costs.
7.How Does Glass CNC Machining Compare to Other Glass Manufacturing Technologies?
When comparing glass CNC machining to other glass forming and cutting technologies, such as laser cutting and manual methods, several key differences emerge:
- Precision and Quality: CNC machining has superior precision, allowing for complex, three-dimensional cuts that are typically not possible with manual cutting methods and some types of laser cutting.
- Speed ​​and efficiency: CNC machining often outperforms manual methods, especially for high-volume production. Laser cutting, however, can rival it in terms of speed, but may not achieve the same level of detail and finish without additional processing.
- Versatility: Unlike laser cutters, which are limited by glass thickness and type, CNC machines can effectively process a wider range of materials and glass thicknesses.
- Cost-effectiveness: For high-volume production, CNC machining can be cost-effective because it produces less waste and is more repeatable. However, for one-off projects or prototypes, laser cutting may be more cost-effective because it takes less time to set up.
- Material limitations: CNC machines can process nearly any type of glass, while laser cutting can have issues with certain types of reflective or refractive glass unless specific parameters are carefully managed.
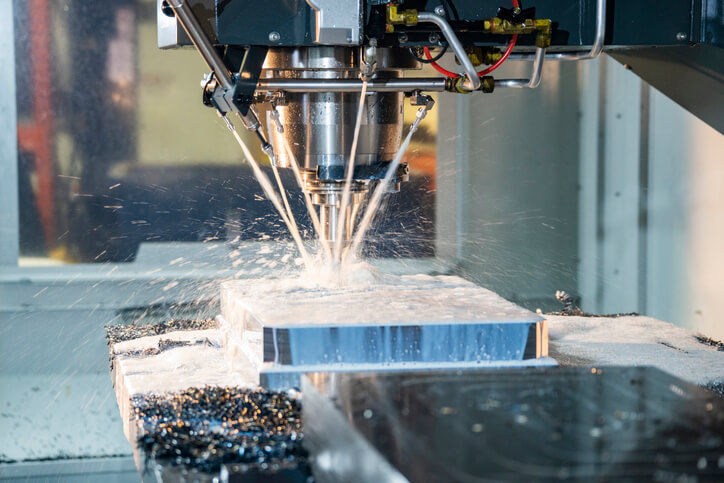
8.How to Choose the Right Glass CNC Machining Service Provider
Choosing the right CNC machining service is critical to achieving the desired results for your glass machining project.
Here are some things you need to consider to ensure you’re working with a supplier that can accurately and efficiently meet your specifications.
- Technical Capabilities: Make sure the supplier has the right CNC machines that can handle the specific type of glass and complexity of your project. Check if they have experience with advanced CNC technologies you may need, such as engraving, drilling, and milling.
- Quality Control: Look for a service provider that has strong quality control measures. They should have certifications such as ISO 9001 to demonstrate their commitment to maintaining high production standards.
- Turnaround Time: Consider how quickly the supplier can complete your project. Fast processing time without compromising quality is essential to maintaining operational efficiency.
- Cost-effectiveness: Get detailed quotes from different suppliers and compare them. Pay attention to any hidden costs, such as installation fees or additional service fees such as post-processing.
- Industry Experience: Experience is important in CNC machining. Suppliers with long-term experience are likely to have well-developed processes and a deeper understanding of how to deal with various challenges in glass machining.
- Customer Service: Good communication is key to project success. The supplier you choose should be responsive and willing to work closely with you to meet your project needs.
- Location: Consider the location of the service provider as it affects delivery time and shipping costs. Closer suppliers can offer faster delivery times and potentially lower shipping costs.
- Technology adaptability: The best suppliers keep their technology up to date. Check if they use the latest CNC machining technology and software, which can provide better precision and functionality.
- Material sourcing: Some projects require specific types of glass or custom sizes that not all suppliers can provide. Make sure your supplier is able to source the required materials.
- Post-processing capabilities: Depending on your project, you may require additional services such as surface treatment, tempering, or strengthening. Make sure the supplier can handle these post-processing tasks to save you the hassle of dealing with multiple suppliers.
9.Conclusion
CNC machining is changing the way the industry manufactures glass components, offering unparalleled precision and customization capabilities. From initial material inspection to final quality assurance, choosing the right service provider is critical.
If you are looking for an experienced CNC machining manufacturer, Xavier is your ideal choice. The Xavier team is well-equipped to provide high-quality CNC machining solutions. If you need more information or to discuss your machining needs with us, please feel free to contact us.
1 Comment