Grinding wheels: the key to the grinding process
Grinding wheels, as the key to the grinding process, its performance is directly related to the precision, surface quality and production efficiency of the workpiece. For every manufacturing practitioner, a deep understanding of the structure, principle, production and dressing of grinding wheels is a compulsory course for improving the process level. Below we will explore the various aspects of knowledge about grinding wheels in depth.
1.Composition of grinding wheel
As a highly efficient grinding tool, the composition of grinding wheel mainly includes abrasives, binders and pores.
(1) Abrasives are the core part of the grinding wheel. Common abrasives include aluminum oxide, silicon carbide, cubic boron nitride and diamond, which determine the hardness and grinding ability of the grinding wheel.
(2) Binders are used to fix the abrasives together. Common binders include resins, ceramics and metals. The type and performance of the binder directly affect the strength and durability of the grinding wheel.
(3) Pores are distributed between the abrasive and the binder to accommodate the chips and heat generated during the grinding process, and also help with cooling and lubrication.
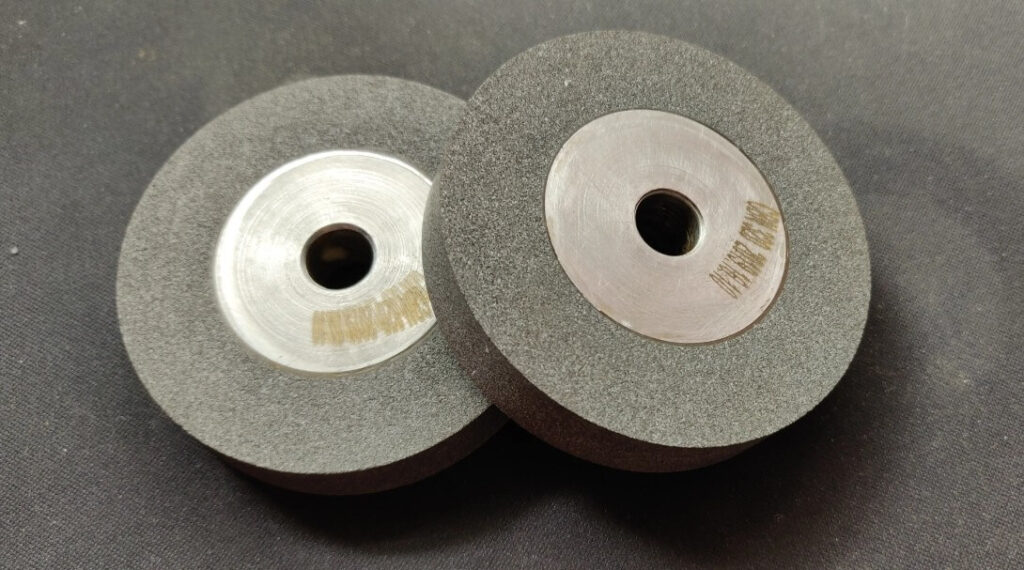
2.Types of grinding wheels
There are many types of grinding wheels. According to their shapes, they can be divided into flat grinding wheels, cup grinding wheels, bowl grinding wheels, etc.; according to abrasives, they can be divided into aluminum oxide grinding wheels, silicon carbide grinding wheels, diamond grinding wheels, etc.; according to binders, they can be divided into resin grinding wheels, ceramic grinding wheels, metal grinding wheels, etc.
Each type of grinding wheel has its specific application scenario. For example, aluminum oxide grinding wheels are suitable for grinding steel, silicon carbide grinding wheels are suitable for grinding non-metallic and non-ferrous metals, and diamond grinding wheels are suitable for grinding high-hardness materials. Different grinding wheel shapes and abrasive types enable grinding wheels to play a role in various complex grinding environments.
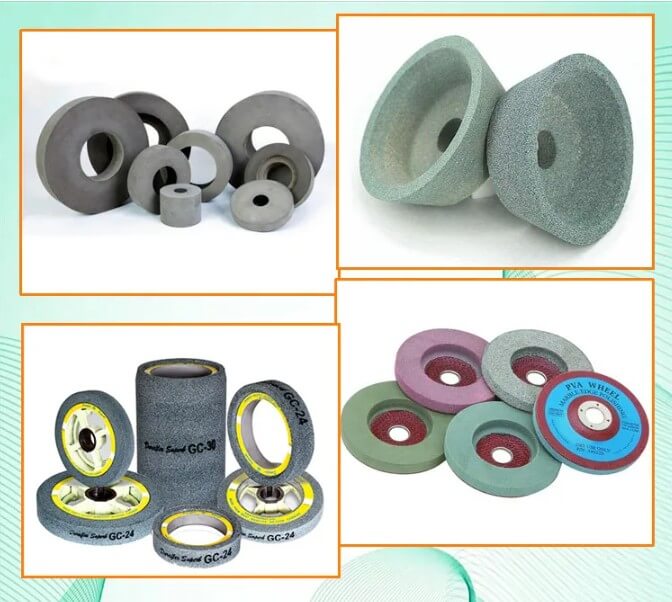
3.Working principle and characteristics of grinding wheels
(1) Grinding principle of grinding wheels
The grinding principle of grinding wheel is based on the abrasive on its surface performing a tiny cutting action on the workpiece. During the grinding process, the grinding wheel rotates at high speed, and the abrasive grains on its surface cut the surface of the workpiece. Since the hardness and sharpness of the abrasive grains are higher than the workpiece material, they can effectively remove the material on the workpiece surface.
The grinding effect of a grinding wheel is affected by many factors, such as the type of abrasive, particle size, hardness, and grinding wheel speed. The grinding speed of a grinding wheel is very high. The linear speed of a general grinding wheel can reach 15 to 80 m/s, which is higher than the cutting speed of a lathe, while the linear speed of an ultra-high-speed grinding wheel can reach 150 to 300 m/s.
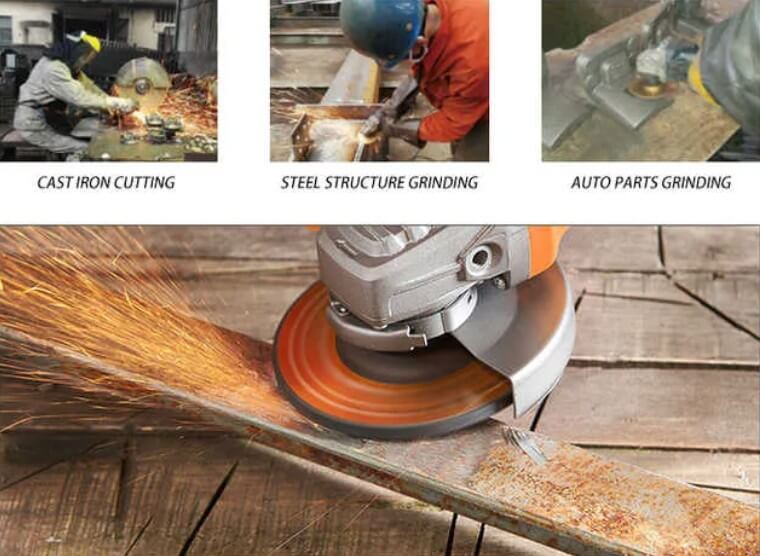
(2) Heat pipe cooling technology for grinding wheels
Heat pipe cooling technology is an efficient cooling method. By setting a heat pipe inside the grinding wheel, the phase change of the working fluid is used to quickly transfer heat, thereby effectively reducing the temperature of the grinding area. This technology is particularly suitable for high-precision and high-efficiency grinding operations, and can significantly improve the surface quality of the workpiece and the service life of the grinding wheel. The design and production of heat pipe grinding wheels need to consider the selection of working fluids, the amount of liquid filled, and the optimization of the heat pipe structure to ensure that its heat exchange performance reaches the best state.
4.Application fields and selection of grinding wheels
(1) Application of grinding wheels in industry
1) Classification by industry field
Grinding wheels are widely used in many industries such as machinery manufacturing, automobiles, aerospace, building materials, and electronics. For example, in the automotive manufacturing industry, grinding wheels are used for high-precision grinding of engine parts and gearbox parts; in the aerospace field, high-performance grinding wheels are used to process difficult-to-process materials such as high-temperature alloys and titanium alloys. In addition, grinding wheels are used to process stone and ceramics in the building materials industry and semiconductor materials in the electronics industry.
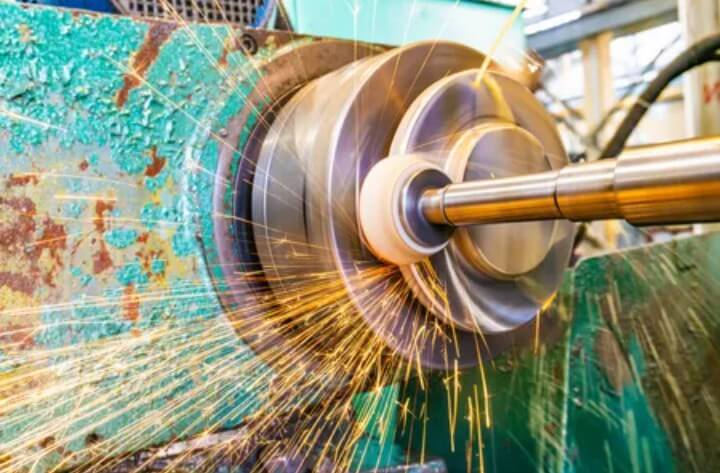
2) Classification by processing materials
Grinding wheels are widely used in industry, covering multiple material processing such as metal processing, wood processing, stone processing and ceramic processing. In metal processing, grinding wheels are used to grind various metal materials such as steel, aluminum, copper, etc. to obtain workpieces with high precision and low surface roughness. In wood processing, grinding wheels are used to grind and polish the surface of wood to improve the gloss and beauty of wood. In stone processing, grinding wheels are used to cut and grind stone to make various stone products. In ceramic processing, grinding wheels are used to grind and polish ceramic materials to improve the surface quality and precision of ceramic products.
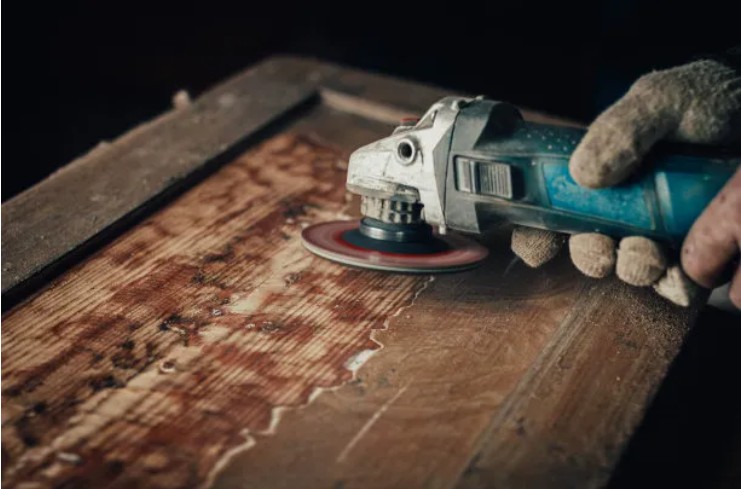
(2) Selection and use of grinding wheels
Selecting the right grinding wheel is the key to ensuring grinding quality and efficiency. When selecting a grinding wheel, it is necessary to consider the material properties, hardness, grinding requirements of the workpiece, and the abrasive, particle size, hardness, and binder type of the grinding wheel. For example, when grinding soft materials, a harder grinding wheel should be selected to keep the cutting edge sharp; when grinding hard materials, a softer grinding wheel should be selected to avoid excessive wear of the abrasive.
In addition, the operator should also master the correct use of the grinding wheel, including the installation, balancing, adjustment, and setting of grinding parameters of the grinding wheel, to ensure the stability and safety of the grinding process.
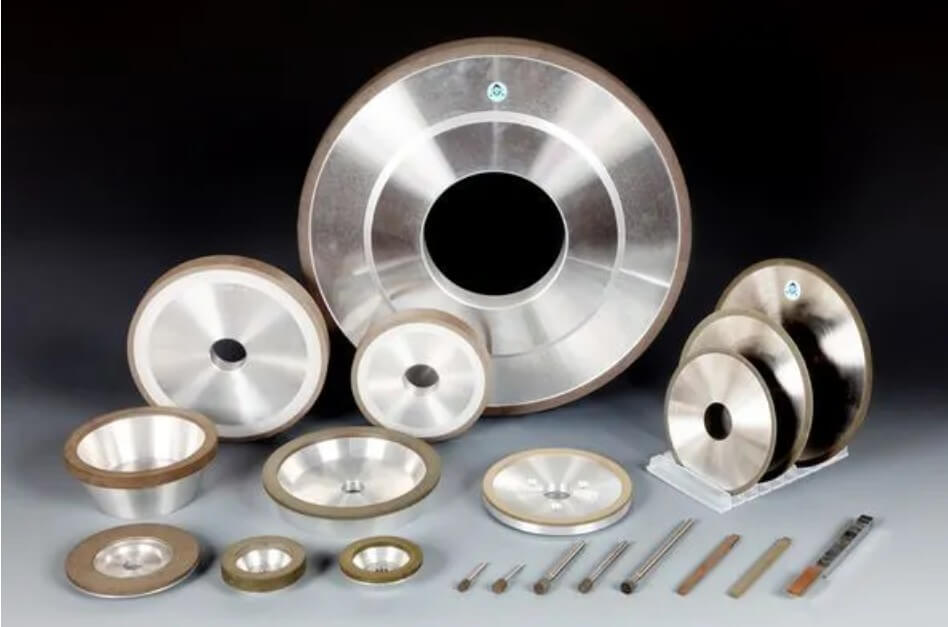
5.Manufacturing process and quality control of grinding wheels
(1) Manufacturing process
1) Raw material preparation:
The main raw materials of the grinding wheel include abrasives and binders. Abrasives include aluminum oxide, silicon carbide, etc., which are used for grinding; binders include ceramics, resins, etc., which are used to bond the abrasives together. Before production, the abrasives and binders need to be mixed in a certain proportion.
2) Mold making:
The mold is a key tool for forming the grinding wheel. Its shape and size determine the shape and size of the final product. The mold is generally made of metal materials such as cast iron, steel, etc., and is completed through processes such as design, processing and installation.
3) Molding:
Put the mixed abrasive and binder into the mold and shape it by vibration compaction or pressure compaction.
4) Sintering:
The molded grinding wheel needs to be heated at high temperature to cause a chemical reaction between the abrasive and the binder, thereby improving the hardness and stability of the grinding wheel.
5) Dressing:
The molded and sintered grinding wheel may have some imperfections and need to be dressed, including dressing the outer circle, dressing the hole, dressing the edge, etc.
6) Inspection, stamping and packaging:
The finished grinding wheel is strictly inspected to ensure that its appearance, size, hardness, balance, strength, etc. meet the standard requirements. Stamp the qualified products and print the certificate of conformity.
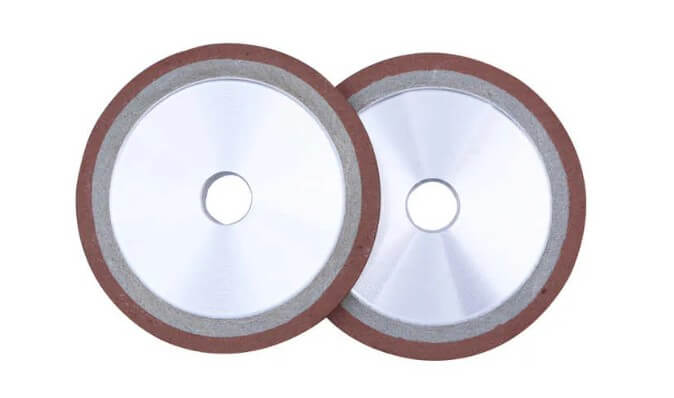
(2) Quality inspection standards
The quality inspection of the grinding wheel mainly includes the inspection of dimensional accuracy, shape accuracy, hardness, strength and balance.
1) Dimensional accuracy and shape accuracy detection
Dimensional accuracy and shape accuracy are detected by precision measuring instruments to ensure that the size and shape of the grinding wheel meet the design requirements.
2) Hardness detection
Hardness detection is carried out using a hardness tester to measure whether the hardness of the grinding wheel is within the specified range.
3) Strength detection
Strength detection is carried out through methods such as rotation tests to test the durability and safety of the grinding wheel at high speed.
4) Balance detection
Balance detection is carried out through a balancing machine to ensure the stability of the grinding wheel at high speed and avoid vibration and damage.
5) Other tests
In addition, the appearance and acoustic properties of the grinding wheel will be tested to ensure that the overall quality of the grinding wheel meets the standards.
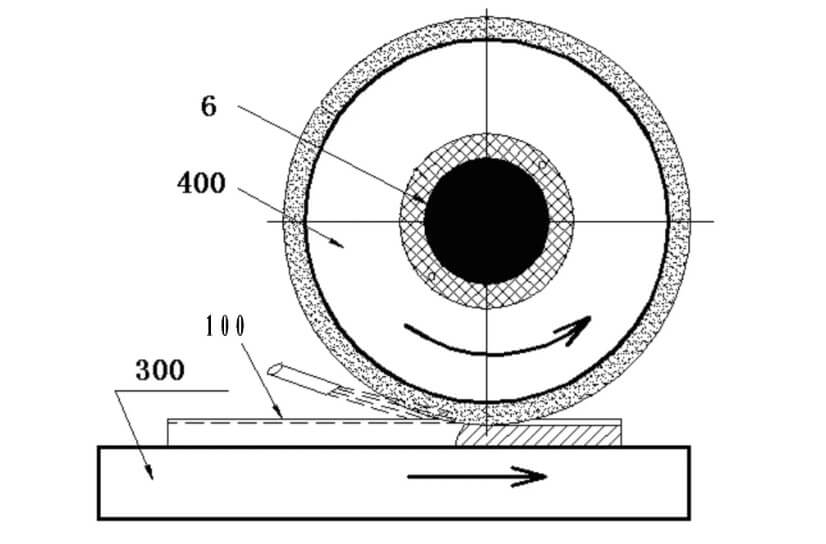
6.Wear and dressing of grinding wheels
Grinding wheels play a vital role in grinding processing, but their wear and dressing problems are often overlooked. Understanding the wear mechanism and dressing methods of grinding wheel is of great significance to improving processing efficiency and quality.
(1) Wear mode
There are three main types of wear of grinding wheels: mechanical wear, chemical wear and adhesive wear.
Mechanical wear is usually caused by hard particles in the workpiece material. For example, when grinding cast iron, hard particles such as silicon carbide will cause the grinding wheel to wear rapidly. Chemical wear occurs in a high-temperature and high-pressure grinding environment, where the grinding wheel reacts chemically with the workpiece material, further exacerbating the wear. Adhesion wear refers to the situation when grinding certain metal materials, where the chips adhere to the abrasive particles, causing the abrasive particles to break or fall off.
(2) Dressing methods
In order to deal with these wear problems, the grinding wheel needs to be regularly dressed. There are many dressing methods, including turning, rolling and diamond pen turning.
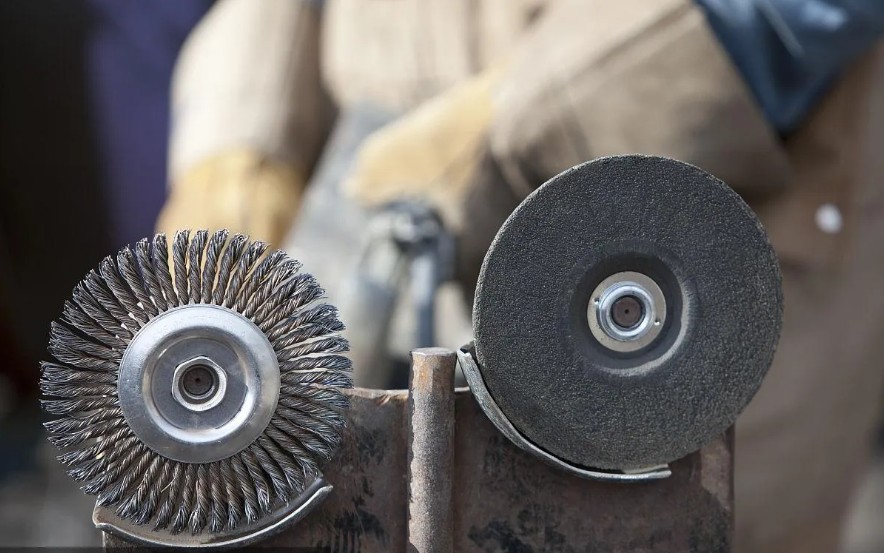
The turning method uses a high-hardness particle head to turn the surface of the grinding wheel to restore its sharpness. The rolling method uses a high-hardness material roller to roll with the grinding wheel to remove the dull layer. The diamond pen turning method uses a diamond pen for dressing, which can effectively maintain the cutting ability of the grinding wheel.
During the dressing process, attention should be paid to the balance of the grinding wheel. An unbalanced grinding wheel can cause vibration and noise, and even damage the machine tool. Static balancing is a common solution. By adjusting the balance blocks on both sides of the grinding wheel on the balance frame, the grinding wheel can be balanced.
7.Summary
Through the above detailed introduction to the basic knowledge, working principle and application, manufacturing process and quality control, as well as wear and dressing of grinding wheels, we can fully understand the importance and application skills of grinding wheels in industrial production. I hope this article can provide you with useful reference and help.
1 Comment