Understanding the Basics of CNC Machining
CNC machining, or computer numerical control machining, is a manufacturing process that uses computer controls and machine tools to produce precise and complex parts. It has revolutionized the manufacturing industry by increasing efficiency, accuracy and productivity. These include parts of an espresso machine, parts slot machine and pinball machine parts uk.
For anyone wanting to design CNC machined parts, such as parts of an espresso machine, parts slot machine and pinball machine parts uk, it is vital to understand the basics of CNC machining.
At its core, CNC machining involves the use of computer programs to control the movement and operation of machine tools. These programs, often referred to as G-code, are created using CAD (Computer-Aided Design) software. The G-code contains instructions that tell the machine how to move, what tools to use, and at what speed and depth to cut.
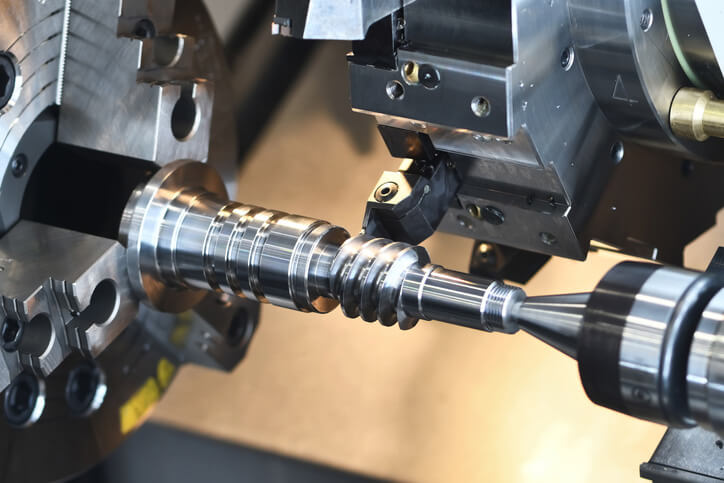
Key Benefits and Considerations of CNC Machining
One of the key advantages of CNC machining is its ability to produce highly accurate and consistent parts. The computerized controls ensure that each part is manufactured to the exact specifications defined in the CAD design. This level of precision is particularly important in industries such as aerospace and medical, where even the smallest deviation can have significant consequences.
To design parts for CNC machining, it is crucial to have a good understanding of the capabilities and limitations of the process. CNC machines can work with a wide range of materials, including metals, plastics, and composites. However, the choice of material can affect the machining parameters, such as cutting speed and tool selection. It is important to consider the material properties and consult machining guidelines to ensure optimal results.

Another important consideration is the design of the part itself. While CNC machines can produce complex shapes and features, certain design elements can still present challenges. For example, sharp internal corners or thin walls can be difficult to machine accurately, so rounded corners or radii are recommended to avoid stress concentrations and improve machinability. Additionally, designing parts with appropriate tolerances is critical to ensuring good fit and functionality.
When designing parts for CNC machining, it is also important to consider the tooling requirements. Different tools, such as end mills, drills, and taps, are used for various machining operations. The selection of the right tool depends on factors such as material, part geometry, and desired surface finish. It is essential to consult tooling catalogs and guidelines to choose the appropriate tools for the job.
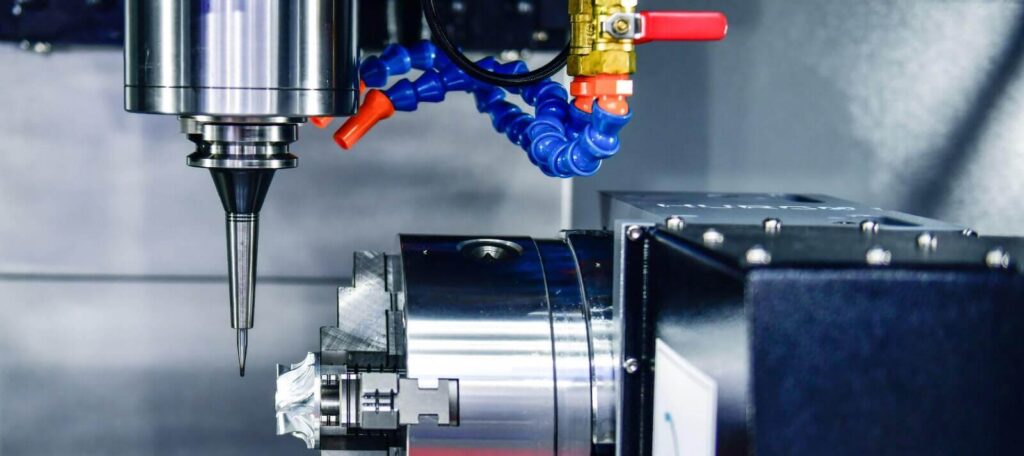
Furthermore, understanding the machining process itself is essential for designing parts for CNC machining. The process typically involves several operations, such as roughing, semi-finishing, and finishing. Each operation removes material at different rates and requires specific tooling and cutting parameters. By understanding the process, designers can optimize the part design and machining strategy to minimize cycle time and maximize efficiency.
In conclusion, understanding the basics of CNC machining is crucial for designing parts for this manufacturing process. CNC machining offers high precision and consistency, but it is important to consider material properties, part design, tooling requirements, and the machining process itself. By taking these factors into account, designers can create parts that are optimized for CNC machining, resulting in efficient and accurate production.