Broaching machining processes, methods, benefits and applications
Broaching machining is a machining process that uses a specialized tool called a broach to remove material. A broach can cut grooves, slots, or other complex shapes because it has a series of progressively sharper cutting teeth.
During broaching machining, the broach is pushed or pulled into the workpiece to produce a final product with high precision and surface finish.
The process of removing metal from a workpiece by cutting a defined path is called broaching, which involves pushing or dragging the broach. This involves moving multiple cutting tools while holding the workpiece stationary or moving the workpiece while holding the tool stationary.
There may be some relative rotation between the tool and the workpiece, and the broaching tool can broach from the focal point of the workpiece inward or from the outer layer of the workpiece outward.
Did you know? Broaching is one of the fastest metal removal processes, capable of removing material quickly. Broaching can effectively produce complex shapes and contours in a shorter time than other machining techniques.
1.What is Broaching?
Broaching is a metalworking technique that uses a sharp, hardened, grooved tool to continuously, continuously, and precisely remove material from a workpiece. The broaching process involves using a tool with convex teeth of varying sizes to remove a precise amount of material each time it slides over the workpiece.
Broaching occurs when a multi-edged tool rotates while the workpiece remains stationary, or when the workpiece moves while the tool remains stationary. In rare cases, the tool and workpiece may rotate relative to each other. Broaching can be done from the center of the workpiece inward or from the surface of the workpiece outward.
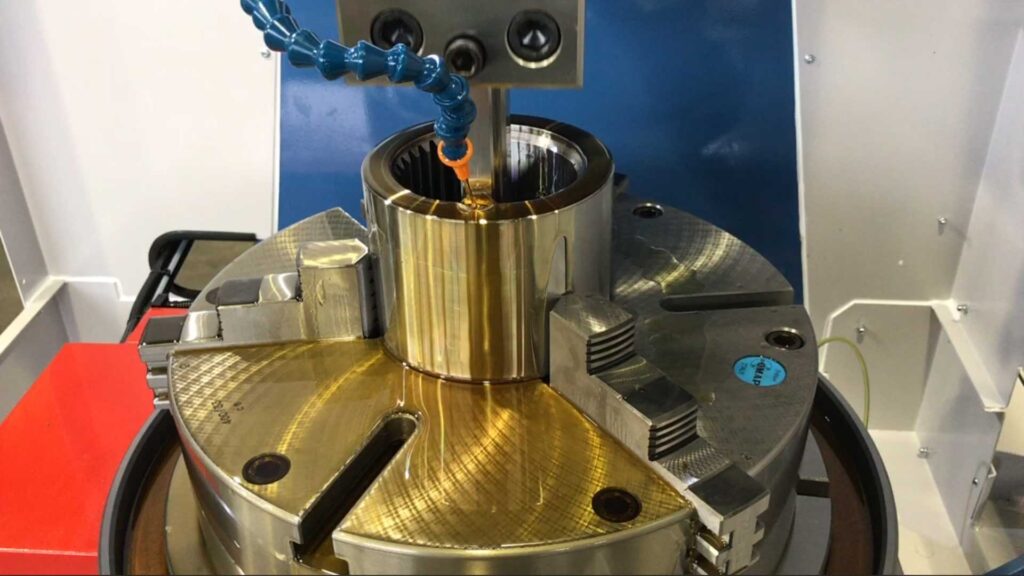
2.Types of Broaching Machining
Broaching is used when precise cuts are required, especially for unusual shapes. Commonly machined surfaces include spherical and non-circular gaps, spirals, keyways, and flat surfaces. The type of tool used in broaching machines is a toothed tool called a broach.
There are two types of broaching machining:
- Linear: In linear broaching machining, the broach runs in a linear direction over the workpiece surface to complete the cut, which is a more common procedure.
- Rotary: Rotary broaching machining involves rotating and pressing the broach into the workpiece to cut axisymmetric shapes. Rotary broaches are tools used on lathes or screw machines.
Both techniques require only one pass of the broach to complete the cut, making them extremely efficient.
3.Broaching Machining Methods
The broaching machining process is completed in the following ways:
1) Internal broaching machining
Internal broaching machining is mainly used to increase the size of the hole. This process usually uses a pull broaching tool, but for lighter workpieces, a push broaching tool can also be used.
2) External broaching machining
It is mainly used to flatten surfaces and cut keyways, slots, and grooves on the outside of objects such as shafts. This method is also used in gear manufacturing.
3) Pull broaching machining
Pull broaching machining is broaching that is subjected to tensile forces during processing. The type of broaching operation performed by pull broaching machining is called pull broaching. This process avoids misalignment and cracking. This type of broaching machining has high productivity. Pull broaching machining is usually constructed of a single piece and is used for internal broaching machining. The number of teeth in the tool is large and it is widely used.
4) Push broaching machining
Push broaches are often subjected to compressive forces during processing. Push broaches are shorter than pull broaches and are usually used for external broaching. Push-type broaches have fewer teeth and a higher tool failure rate. Due to limited applications, productivity will be reduced.
5) Ordinary cutting broaching machining
Ordinary cutting broaching machining uses an ordinary broach, and the height of the teeth gradually increases from one tooth to another throughout the length of the broach.
6) Progressive cutting broaching machining
The teeth in progressive cutting broaching machining increase along the length of the broach, increasing in width rather than height.
7) Integral, segmented and modular broaching machining
Integral broaching machining is a single-piece tool used mainly for internal broaching. Segmented broaching is made by connecting different parts of the broaching. Modular broaching is made by combining multiple modules into a single part. It is used for external broaching.
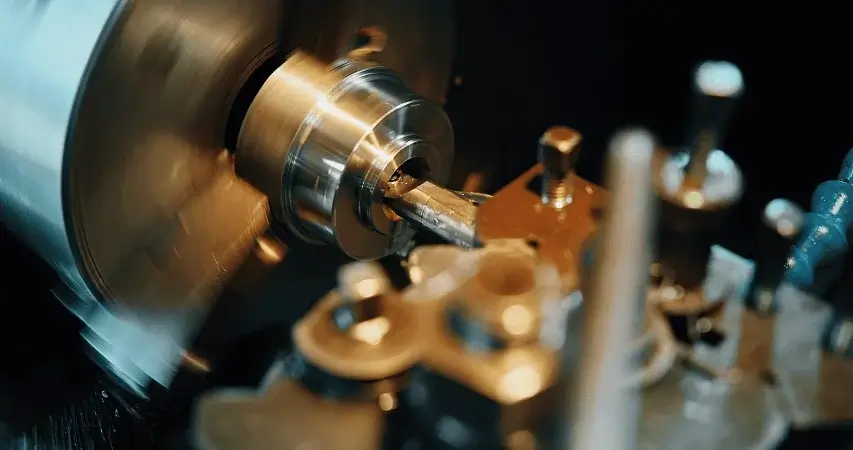
4.Broaching Machines
Broaching machines obtain polished flat or curved surfaces by broaching or pushing the surface of the workpiece. It can be used for both internal and external surfaces.
The tool of a broaching machine is pulled or pushed across the surface to complete the machining. The broaching operation is very simple. It is used to provide linear motion to the tool and keep the workpiece immobile. The broaching tool can move vertically or horizontally.
Therefore, there are two types of machines, namely vertical machines and horizontal machines. Horizontal machines are typically used for internal machining, while vertical machines are used for external and surface machining.
5.Broaching Machining Process
Broaching machining is a high-speed manufacturing method used to create unique, precision components. Broaching machines come in a variety of shapes and sizes. But they always use tools to remove a certain amount of material from an unfinished or manufactured component.
Depending on the broach used, the process can produce round holes, uneven external shapes, keyways, or a number of irregular shapes.
Broaching machining, like drilling, casting, and grinding, is a highly specialized, precise production operation. Each broaching machine is designed to machine a single hole with optimal precision, speed, and accuracy.
In this regard, the broaching machining operation is a very efficient machining method, primarily used when working with delicate metal and plastic components.
However, in some cases, broaching machines can be inefficient. Particularly hard metals may require frequent tool refurbishment; a new tool is required for each specialized cut.
This can be a problem if your organization does not have the ability to refurbish and manufacture old broaching tools. Fortunately, certified broaching companies can help you with all of your customization and maintenance needs.
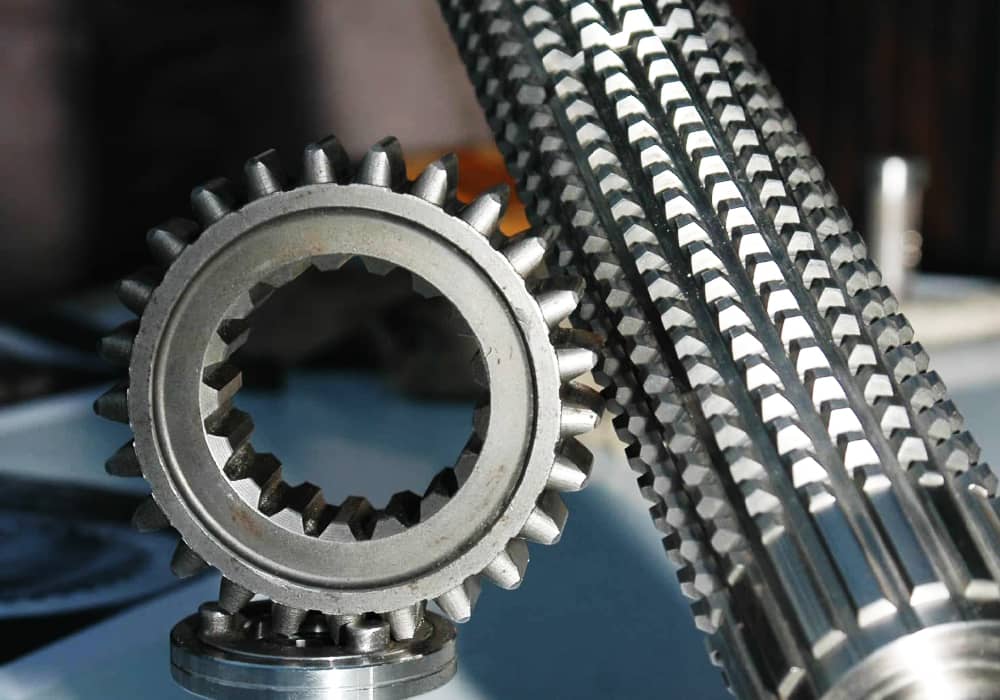
6.Broaching Operation
The metal removal process in broaching machining is similar to forming, except that it uses a set of progressive teeth to remove more material in one operation. The broaching machining operation is best described by the term “precision machinery”.
The forming process requires multiple strokes to cut the required width of the workpiece. Each stroke removes a small layer of metal.
This method is time-consuming and inefficient. Broaching machining can eliminate this limitation, which uses a series of cutting edges on a rod or bar tool.
7.Cutting Principle
The cutting principle combines the relationship between force, tension and surface. When a given force acts on a smaller area, the pressure applied is greater. Therefore, a sharp cutting tool may remove metal from the body.
8.Broaching Machining Tool
Broaching machining uses a multi-point perforation device with a continuous cutting edge. The broaching machining tool is durable, hard, fast cutting speed and wear-resistant. It is made of extremely strong tool materials such as high-speed stainless steel and carbide. The tool is an accessory for broaching machines.
The design of broaches is characterized by structure, configuration, metal material and blade geometry. The broach is designed with multiple progressive cutting edges that work in a push or pull motion on the workpiece surface. Material is removed from the narrow end of the taper to the wide end. This results in a complete product with less stress on each tooth.
The height of each tooth of the broach is customized to the cut or groove requirements of the specific machine or workpiece.
9.Advantages of the Broaching machining Process
Due to the high productivity when using the broaching process, manufacturing machines prefer this process because of the following advantages.
- The broaching machining operation achieves extremely high precision in just one stage or step. Multiple effects such as cutting and finishing can be achieved in one operation.
- The broaching machining method achieves excellent surface quality and reduces the need for surface polishing operations.
- Complex holes can be drilled inside the workpiece, and internal keyways can be machined using the high precision of the broaching machine.
- The broach is highly resilient, not prone to degradation, and has high dimensional accuracy and large tolerances.
- The temperature during the process remains constant, which reduces errors due to thermal stress.
- Highly trained operators are not required, as a semi-skilled operator can operate a broaching machine.
- Lubricant application is simple and quick.
- It is a cost-effective method for mass production of machine parts.
10.Disadvantages of Broaching machining Process
Broaching machining has some disadvantages.
- The initial cost of broaches is high. The initial customization cost is high. The cost can be high for small-scale production because a broach is used only for one operation. It is only suitable for large-scale production.
- The design, grinding or repair cost of broaches is challenging and time-consuming. But it is a one-time job.
- The fixture and workpiece must be strong enough to resist the cutting forces.
- It is only effective for removing small amounts of metal and is not recommended for heavy labor.
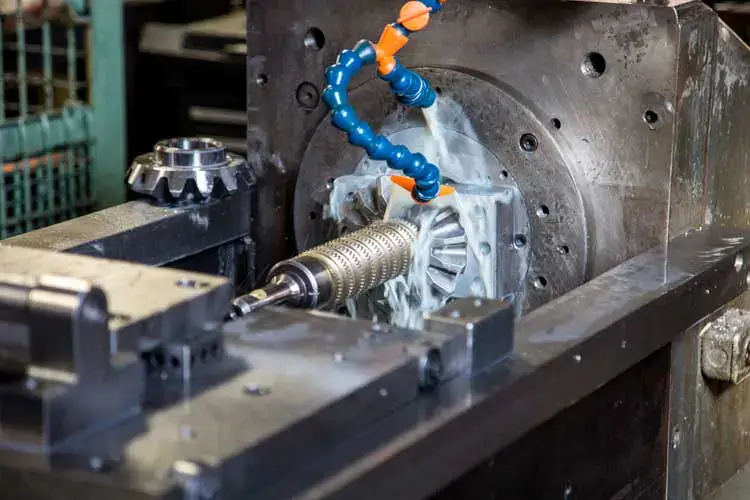
11.Applications of Broaching machining Operations
Broaching machining is an important manufacturing method for producing products with excellent surface finish and dimensional accuracy. Broaching applications include:
- Broaching is used in the automotive industry to make or engrave gears or gear teeth in machines.
- It is also used to make keyways for pulleys and conveyor belts.
- In machining, it is used to engrave grooves during casting and forging processes.
- In the farm implement industry, broaching is used to manufacture a variety of farm machinery parts.
- It can stamp complex structures and carve complex shapes on the workpiece.
- Broaching is a common and very successful practice in some major industries.
Here are some industries that use this technology.
- Industrial Manufacturing
- Automotive
- Agriculture
- Oil and Gas
- Heavy Equipment Manufacturing
- Fasteners and Gears
- Aerospace Parts Manufacturers
12.Conclusion
In summary, broaching is a machining method that uses a special tool called a broach to remove material. It can produce a variety of shapes and features from a variety of materials.
Broaching machines have advantages such as high precision and high efficiency, but also have disadvantages such as high installation costs and limited adaptability. Broaching is a valuable method, but it must be used with caution for special tasks.