The Best Guide to Cold Forging
In today’s industrial field, cold forging, as an important metal forming process, plays a key role in the high-precision and high-strength requirements of various industries for parts. It can not only develop high-value-added products and reduce production costs, but also integrate with other processes to show unique advantages. However, the cold forging process has specific requirements for materials, and different materials perform differently in cold forging. This article will explore cold forging in depth to help readers fully understand this technology.
1.What is cold forging technology?
Cold forging refers to a processing method that forms metal materials by applying pressure without heating at room temperature, also known as “plastic processing”. It uses the plasticity of metal to shape the material during deformation. Almost no metal chips are generated during the manufacturing process. It is processed at room temperature without heating, has high dimensional accuracy, and can process parts of complex shapes at a higher speed.
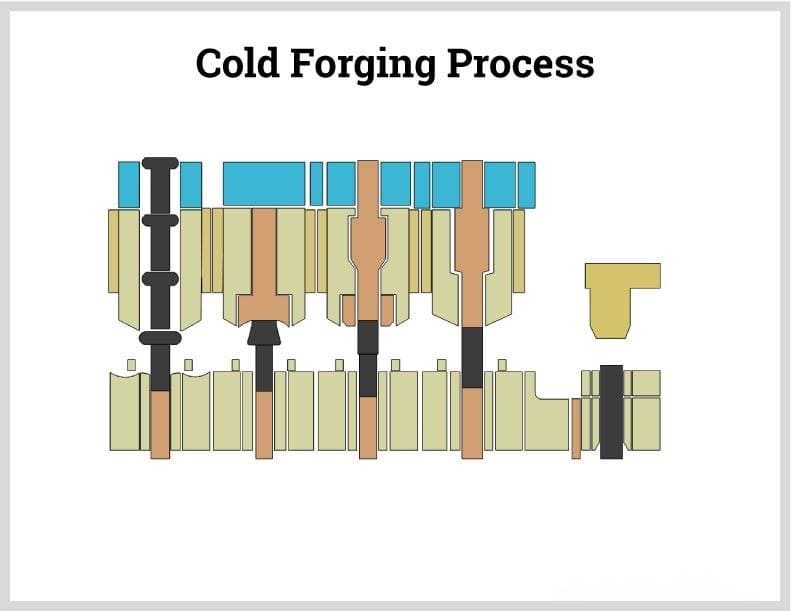
2.Cold Forging Process
(1)Material Selection
Cold forging begins with the selection of suitable materials that can withstand the cold forging pressure, such as steel, aluminum, copper and other metals.
(2)Lubrication
Before forging, the workpiece is lubricated to reduce die friction and wear and promote material flow.
(3)Dies and tools
Customized dies are made, and the die material needs to be harder than the workpiece to withstand the cold forging pressure.
(4)Forging process
The metal workpiece is placed between the dies, and a press (mechanical press or hydraulic press) is used to apply a quick and powerful blow to the workpiece to deform it into the shape of the die cavity. Depending on the complexity of the part, multiple forging operations may be required, which may involve multiple stages of pressing with different die sets.
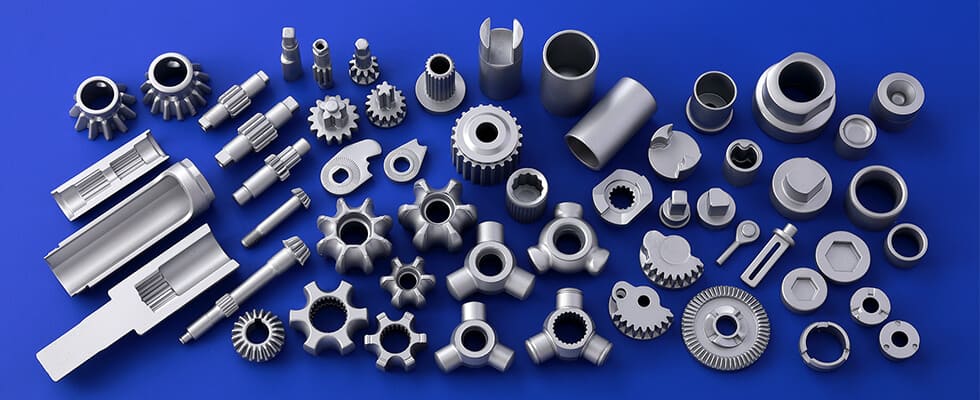
(5)Trimming and finishing
The excess material (burrs) generated during the forging process is trimmed, and finishing processes such as shot peening, cleaning or heat treatment (stress relief) can be performed.
3.Types of cold forging processes
(1)Imprint forging
The material is squeezed into a die cavity with a central opening to form a shape larger than the original diameter. Imprint forging is difficult to produce complex shapes and is generally used for simple situations such as rolling a bar into a disc. Too large an impression ratio may cause problems such as workpiece flying out. Usually, the impression ratio should be below 85%. If it exceeds, it is necessary to divide the process and add dies.
(2)Back extrusion
A processing method that moves the material in the opposite direction of the punching direction.
(3)Forward extrusion
The diameter of the material is reduced by pushing the material into a smaller die, thereby reducing the cross-sectional area. It may be difficult to form high-hardness materials such as stainless steel.
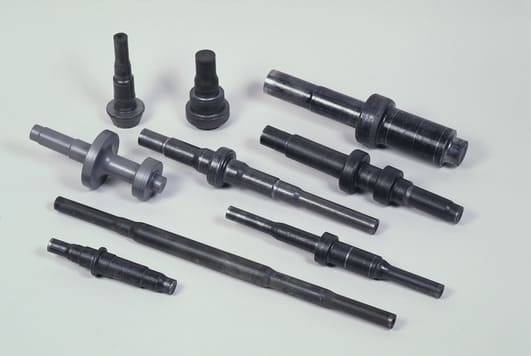
(4)Die forging
Put the workpiece into the die and forge it into the desired shape. The material volume is slightly larger, and flash will be generated on the outside of the finished shape, which will be removed in subsequent processes. There is no flash in the closed die forging shape.
(5)Closed die forging
Put the workpiece into the die cavity, and then close it to form the die shape. The upper and lower punches further move the material to fully form the finished shape.
4.Materials suitable for cold forging
(1)Iron
Iron can be forged, drawn, rolled and processed at different temperatures, and can be diversified through heat treatment. It is also used in alloys such as stainless steel. It has strong versatility, low price, and is suitable for large-volume orders. The surface treatment methods after processing are diverse and can be widely used in various fields. It is a common material for cold forging.
(2)Stainless steel
Alloy steel containing more than 10.5% chromium and less than 1.2% carbon. Chromium can form a passivation film to protect the surface, prevent corrosion, and have a long service life.
(3)Copper
Copper has good thermal conductivity and can be used in cookers, heat pipes and electronic equipment conductors. It will form a protective surface film when exposed to air. Its biggest advantage is good machinability, softness and good ductility, which is suitable for bending and stretching processes through cold forging presses.
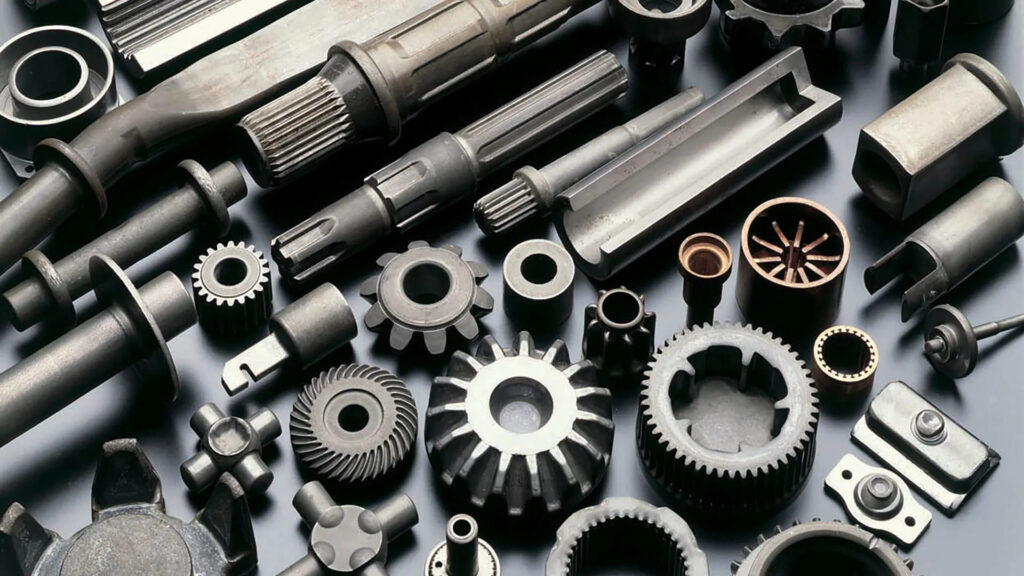
(4)Aluminum
Pure aluminum has low tensile strength, but the strength can be increased by adding alloy elements or process treatment. Aluminum is plastic and can be easily formed into various shapes, which is suitable for cold forging.
5.Advantages of cold forging
(1)High material utilization rate
Cold forging is formed by material deformation and uses an amount of material equivalent to the weight of the finished product, which greatly improves material utilization and reduces material costs.
(2)High-speed production possible
Cold forging technology enables production rates of approximately 100 pieces per minute. Processing at room temperature, no need to heat the metal, small dimensional changes, and the ability to process complex shapes.
(3)improved mechanical properties
Process design that considers fiber streamlines can produce parts with excellent strength and wear resistance.
(4)Can effectively reduce parts costs
When production conditions such as precision and batch size match, the high material efficiency and high-speed processing capabilities of cold forging can significantly reduce part costs in mass production.
6.Disadvantages of cold forging
(1)Requires molds
Mold manufacturing requires initial cost and delivery cycle.
(2)Long process preparation time
Not suitable for small batch production, the preparation work in the process requires a certain amount of time and cost.
(3)Requires professional knowledge
Requires process and mold design expertise, which is more difficult.
(4)Surface treatment restrictions
There are some surface treatment processing restrictions, such as fillet radius.
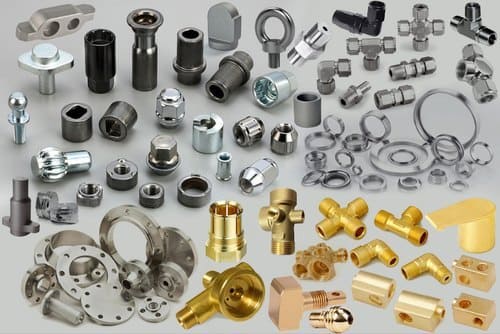
7.Application of cold forging products
Automotive parts: fasteners and screws, gears, shafts, hubs, bearing raceways.
Electrical and electronic: connectors, terminals.
Building and construction hardware: nails and rivets, bolts and nuts.
Tools and hardware: wrenches, hand tool assemblies.
Aerospace parts: fasteners and pins, landing gear assemblies.
Consumer products: watch parts, kitchenware.
Medical devices: implants, surgical instruments.
Summary
In summary, cold forging technology plays an important role in modern industry, and it has a wide range of choices and advantages in material selection, process types and product applications. By rationally utilizing cold forging technology, high-precision and high-strength parts that meet the needs of different industries can be produced.
If you are looking for a professional machining manufacturer, Xavier is undoubtedly your best choice. The Xavier team has excellent equipment and is good at various machining solutions to fully meet your personalized processing needs. If you need more information or to discuss your processing needs with us, please feel free to contact us.