Copper Processing Overview
As an important metal material, copper has a wide range of applications. Copper processing plays an indispensable role in various fields, from exquisite artworks to practical cookware, from complex electronic components to high-performance mechanical parts. Copper is not only popular for its natural and beautiful luster, but also for its excellent material and electrical properties, such as good electrical conductivity, thermal conductivity, corrosion resistance and excellent ductility, making it the preferred material in many industries. Next, we will take a deep look at the process, design factors and finishing standards of copper processing.
1.Commonly used techniques for copper processing
Copper is a metal with many excellent properties, but pure copper can be challenging to machine. When copper is alloyed with other elements, its machinability is significantly improved. At present, there are two main methods of copper processing: CNC milling and CNC turning.
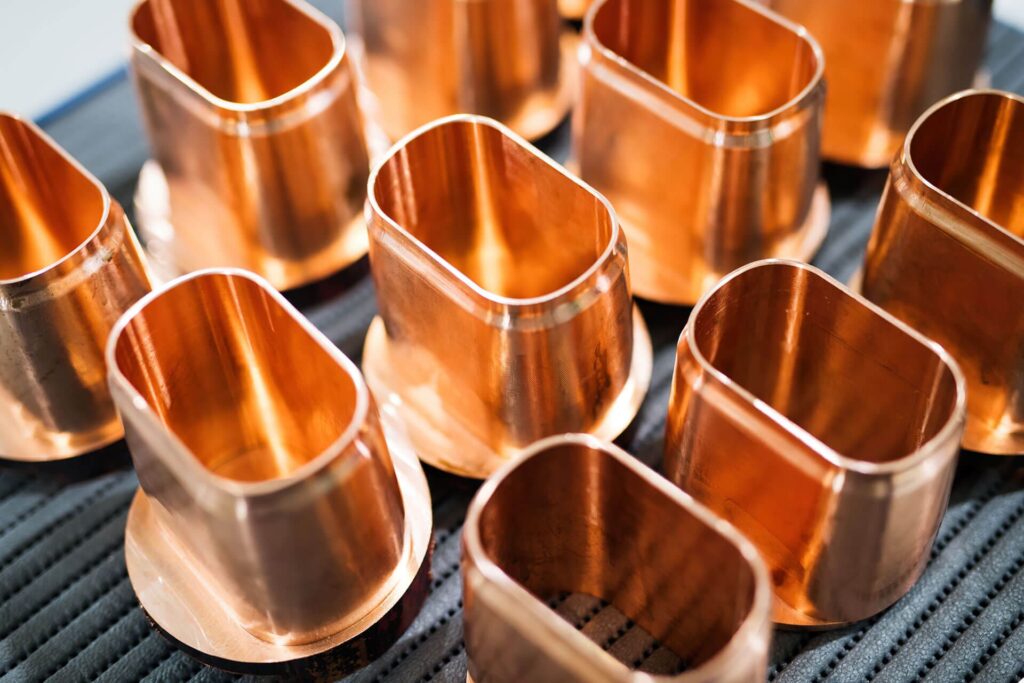
(1) CNC milling
CNC milling of copper alloys is an efficient method of processing copper. CNC milling relies on computer-controlled, multi-point rotating cutting tools that move across the surface of a workpiece, gradually removing excess material to achieve the desired shape and size. Milling can create complex design features such as grooves, notches, pockets, holes, slots, contours and flat surfaces.
When CNC milling copper or copper alloys, care needs to be taken to select the appropriate cutting material. Carbide cutting materials, such as N10 and N20 application groups or HSS grades, can be used for copper processing. At the same time, to extend tool life, the cutting speed can be reduced by 10%. When milling copper cast alloys with cast skins, the cutting speed should be reduced by 15% for carbide tools and 20% for HSS grade tools.
(2) CNC turning
CNC turning is also one of the important means of copper processing. During turning, the tool remains stationary while the workpiece moves to obtain the desired shape. This machining method is widely used in the production of electronic and mechanical components due to its cost-effectiveness, high precision and fast manufacturing speed.
When turning copper workpieces, special attention needs to be paid to speed control. When turning, the cutting tool edge angle should be set in the range of 70° to 95°, with a cutting tool edge angle of approximately 90˚ being more advantageous for softer copper variants that are prone to smears.
Maintaining a constant depth of cut and reducing cutting tool edge angles minimizes tool stress and increases tool life and cutting speeds. At the same time, increasing the angle between the major and minor cutting edges (tool angle) allows the tool to withstand higher mechanical loads, thereby reducing thermal stress.
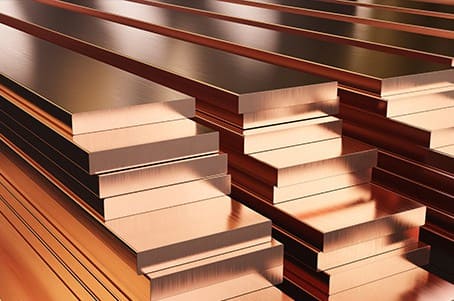
2.Design considerations for machining copper parts
(1)Basis for material selection
When designing parts involving copper processing, multiple factors need to be considered. Copper or copper alloys are selected for their unique properties, such as excellent corrosion resistance, which makes them stable even in harsh environments; excellent electrical and thermal conductivity, which makes them easy to weld and widely used in the electronic and electrical fields; high ductility, which makes it easy to process them into various shapes; as an alloy, it has excellent machinability and can meet different processing needs.
During the design stage, it is crucial to select the right copper grade for the application. Although pure copper (C101) has high purity (99.99% copper) and excellent conductivity, it has poor machinability and low economic efficiency. In contrast, C110 is generally easier to process and more cost-effective. Therefore, the choice of material grade should be determined based on the properties required by the design function.
(2)Design for manufacturability
No matter what copper material is used, design for manufacturability (DFM) is an aspect that needs to be focused on in copper machining. During the design process, we recommend optimizing tolerances while retaining the functions required by the application. Additionally, dimensional checks should be minimized, deep pockets with tight radii should be avoided, and the number of part setups should be limited.
Specifically, when designing for machining copper parts, a minimum wall thickness of 0.5 mm should be maintained. For CNC milling, the maximum part size is 1200 x 500 x 152 mm; for CNC turning, the maximum part size is 152 x 394 mm. When dealing with undercuts, it is best to use a square profile, full radius, or dovetail profile.
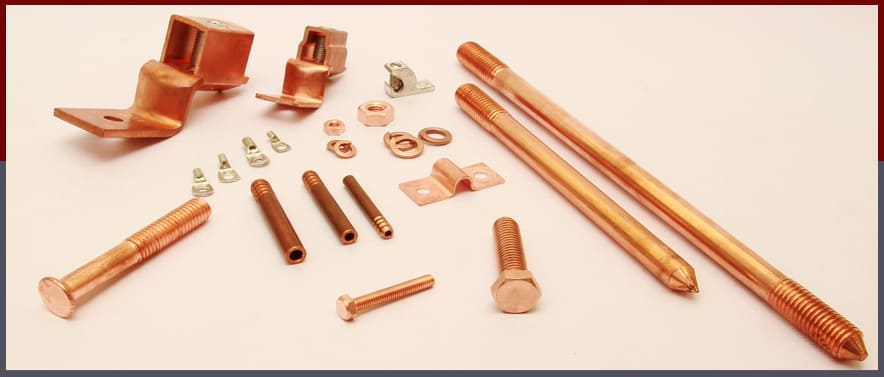
3.Finishing Copper Parts
The finishing stage of copper machining is critical, and many factors affect the choice of finishing method.
(I) Surface finish control
First, surface finish control can be optimized during CNC machining. Some machining parameters can affect the surface quality of the part, such as the tool tip radius or tool corner radius.
For soft copper alloys and pure copper, the surface quality is greatly affected by the tool tip radius. Reducing the tool tip radius can prevent scratches on softer metals, reduce surface roughness, reduce feed marks, and obtain a higher quality cut surface. Polishing blades are more popular than traditional tool tip radius tools because they can improve surface finish without adjusting feed rates.
(2) Post-processing technology
In addition, the desired part finish can be achieved through post-processing technologies, such as:
- Manual polishing: Although labor-intensive, it can give the surface an attractive sheen.
- Sandblasting: It can produce a consistent matte effect and cover minor flaws.
- Electrolytic polishing: Due to copper’s good electrical conductivity, electrolytic polishing is ideal for finishing copper. It can brighten the copper surface and enhance the overall luster.
4.Conclusion
Copper processing is a complex and delicate process, covering many aspects from processing technology, design considerations to finishing. By rationally selecting processing methods, optimizing designs, and adopting appropriate finishing technologies, the excellent properties of copper can be fully utilized to produce high-quality copper processing products that meet various needs. With the continuous development of industrial technology, copper processing technology will continue to innovate and improve, providing better copper products for various fields and further promoting the development of industry.