Comprehensive Introduction to electro polishing
After metal parts are manufactured or processed, Electro polishing is a crucial surface treatment process. It can not only improve the appearance and corrosion resistance of the parts, but also optimize the electrical or mechanical properties, which has a significant impact on the durability and functionality of the parts.
This article focuses on the electro polishing process, and elaborates on its principles, processes, differences from other processes, and application advantages.
1.What is electro polishing ?
Electro polishing (also known as anodic polishing) is an electrochemical process that removes a thin layer from the surface of a conductive metal through an electric current. This can improve the surface roughness and corrosion resistance of the metal, eliminate discoloration and embedded foreign matter caused by the previous process, and make the finished product bright and clean.
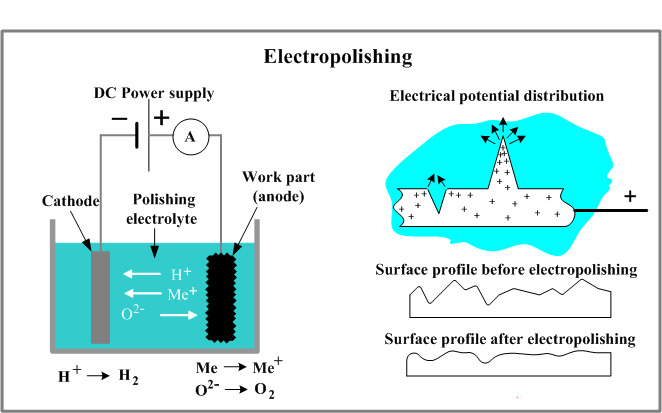
2.Working principle of electro polishing
(I) Principle of electrolytic cell
Electro polishing is based on the principle of electrolytic cell. The workpiece is connected to the positive electrode of the electrolytic cell to become the anode, and the suitable metal is connected to the negative electrode to become the cathode. The power supply is usually a DC rectifier, which converts AC power into DC power.
(II) Process stage
Surface treatment: Electrolytic polishing requires cleaning the surface to ensure uniform current, otherwise contaminants will cause uneven current density and uneven surface corrosion. There may be contaminants such as grease, oil, workshop dirt, fingerprints, etc. on the surface, and their quantity affects the quality of the finished product. First, it needs to be thoroughly cleaned with alkaline and solvent cleaners, then pickled, and the parts are rinsed after each treatment to remove residues.
Electro polishing: The material to be polished is used as the anode, and different suitable metals are used as the cathode, and they are immersed in the electrolyte solution together. The material at the anode generates a positive charge, oxidizes and dissolves in the electrolyte, and the current density at the burrs and corners increases. This process can finely control the thickness of the removal layer. Factors such as metal and electrolyte composition, surface contamination, electrolyte temperature, current density, electrolyte specific gravity, electrolyte stirring method, etc. affect the thickness of the removal layer and surface quality.
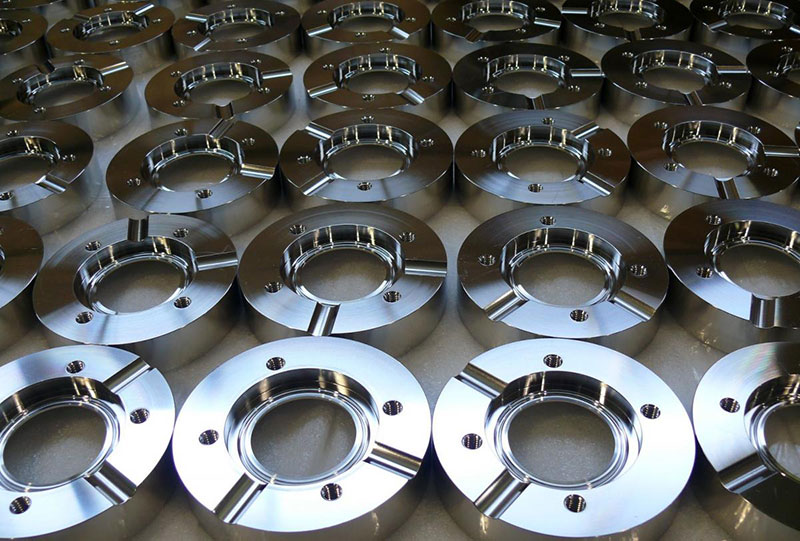
Post-treatment: electro polishing will produce some by-products deposited on the metal surface, which need to be cleaned to obtain a satisfactory finished product, otherwise it will cause inconsistencies, corrosion and staining during use. For stainless steel surfaces, post-treatment uses nitric acid treatment followed by hot washing.
3.Comparison between electro polishing and other processes
(I) Difference from electroplating
Electro polishing is the opposite of electroplating. Electroplating is the process of depositing a thin layer of metal on another metal through an electrochemical reaction, with the coated metal as the cathode and the deposited metal as the anode. The anode is dissolved and then coated on the cathode. Electro polishing is the process of removing the thin layer of metal, with the workpiece as the anode, so it is also called the reverse electroplating process.
(II) Difference from passivation
Electro polishing is often compared with the passivation process, but neither natural passivation nor chemical passivation involves the use of electricity to form a protective layer.
4.Applicable materials for electro polishing
Electro polishing is applicable to a variety of metals, including aluminum, brass, copper, molybdenum, nickel, titanium, tungsten, zirconium, and nickel, cobalt and copper alloys. Cast iron also benefits to a certain extent, and electrolytic polishing of carbon steel before electroplating can remove burrs and improve surface finish. Electrolytic polishing of stainless steel (especially 300 and 400 series) is the most widely used.
5.Advantages of electro polishing
(I) Eliminating surface defects
This process can effectively remove surface defects such as cracks, fissures, micro-burrs, wear, stains, weld discoloration and peeling, and smooth or eliminate most defects by dissolving the outer layer.
(II) Reducing surface roughness
Electro polishing removes metal faster at the micro-peaks of the rough surface than at the depressions (anodic leveling), which can reduce the height of the depressions and make the surface smoother. Targeted electrolytic polishing can reduce the surface roughness by up to 50%.
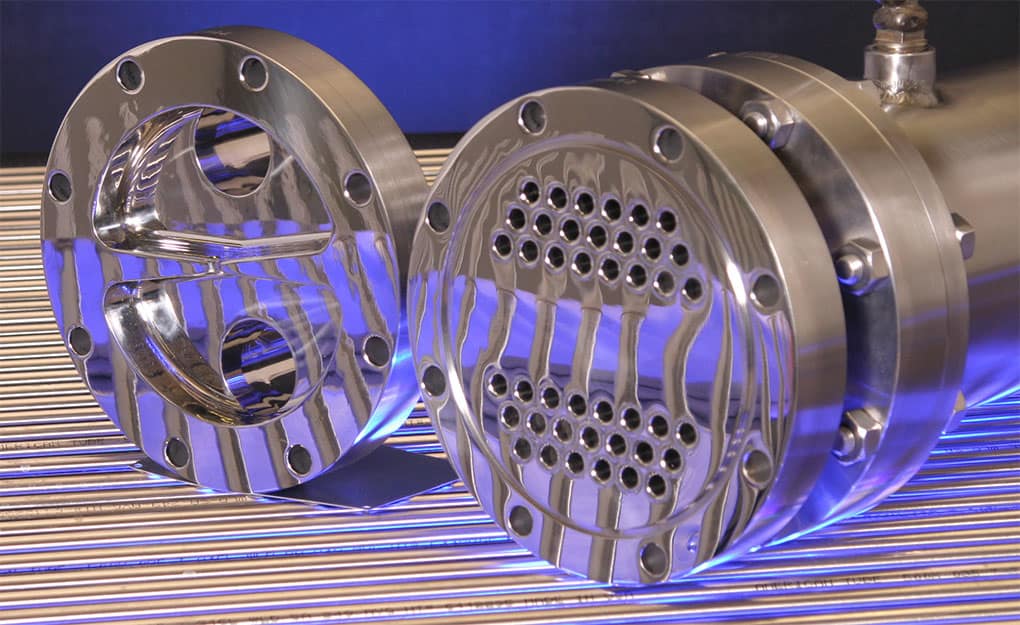
(III) Suitable for complex surface morphology
Electro polishing can handle complex geometric shapes and can remove the same thickness of the entire surface of the part (including grooves and internal channels), which is difficult to achieve when mechanical polishing handles complex geometric shapes.
(IV) Improving corrosion resistance
Although stainless steel has a passivation film to resist corrosion, it may be insufficient in seawater or other corrosive chemical environments. Electrolytic polishing can improve the corrosion resistance of stainless steel parts by more than 30 times compared to passivation.
(V) Improved fatigue life
For parts subjected to cyclic stretching, bending, flexing or twisting, manufacturing defects may be aggravated under fatigue load and lead to failure. Electro polishing can eliminate or reduce the impact of these surface defects, reduce the impact on crack initiation and propagation, and extend fatigue life.
(VI) Ultra-clean and decorative appearance
Electro polishing strips off the outer layer of metal to reveal a pure layer, making the parts clean and beautiful, and can also remove foreign matter embedded in manufacturing or post-processing.
(VII) Antibacterial surface
Electropolished surfaces can inhibit bacterial growth, especially for stainless steel, changing the charge to prevent bacterial growth and removing surface defects, which can be used in medical, food and hygiene-related applications.
6.Industry Applications
Medical Industry
Electro polishing can clean and disinfect surgical instruments, remove burrs, inhibit bacterial growth, have high precision and good biocompatibility, and improve corrosion resistance.
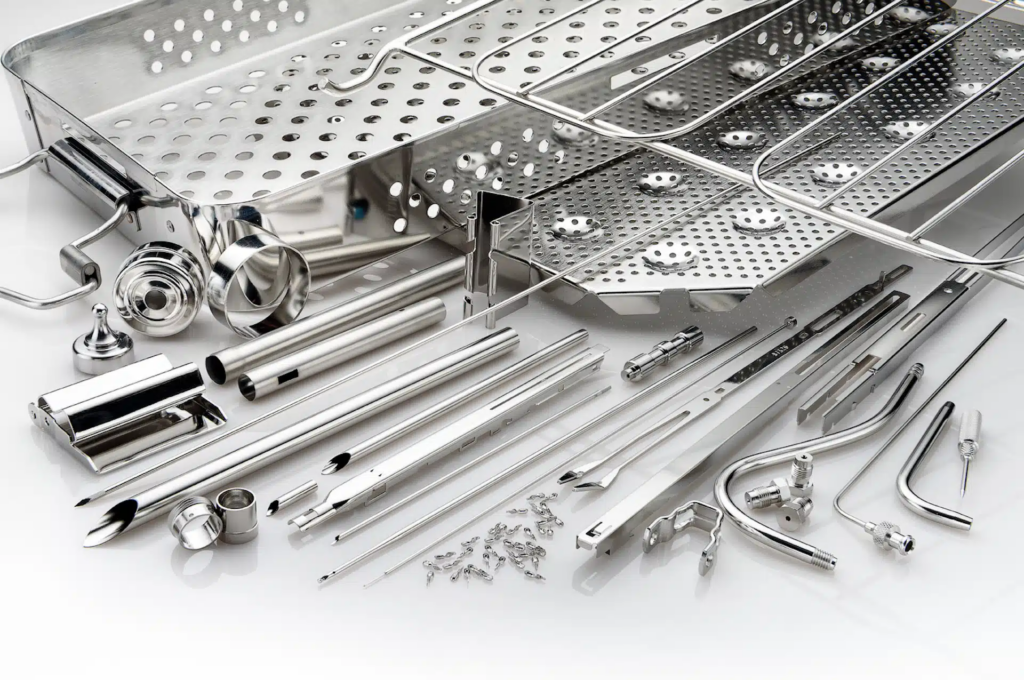
Automobile Manufacturing
Electro polishing of pipes, gears, and fuel lines can reduce friction, improve performance and durability, and make rims, grilles, exhaust components, and flow channels bright and smooth, corrosion-resistant, and long-lasting.
Process Equipment
After electro polishing, industrial process equipment such as heat exchangers, reaction vessels, agitators, storage tanks, and pipelines can reduce friction, corrosion, and surface stress, improve heat transfer efficiency, flow quality, durability, and cleaning ability, and the performance is comparable to that of glass surfaces.
Other Industries
Electropolished parts are also widely used in aerospace, food and beverage processing, nuclear energy, clean rooms, semiconductors, water treatment, and home appliance industries.
Conclusion
As a cost-effective and versatile surface treatment process, electro polishing plays an important role in the surface treatment of metal parts in multiple industries.