Basic Introduction to Electronic Manufacturing
As an advanced technology, electronic manufacturing plays an indispensable role in our lives. From the smartphones we use every day, to the laptops we need for work and study, to the smart home devices that add convenience to our lives, their birth is inseparable from the complex and sophisticated process of electronic manufacturing. This blog will guide you through the key steps of the electronic manufacturing process, focusing on the technologies, challenges and future trends that shape this key industry.
1.What is electronic manufacturing?
Electronic manufacturing is the process of designing, assembling and producing electronic components and equipment, covering stages such as electronic design, material procurement, assembly, testing and packaging. It is essential for the manufacturing of products in the fields of consumer electronics, medical equipment, automotive electronics, etc. Electronic manufacturing service (EMS) companies play a core role in this. Printed circuit boards (PCBs) are the basis of electronic devices. Components are installed through SMT or THT technology and require strict testing after assembly.
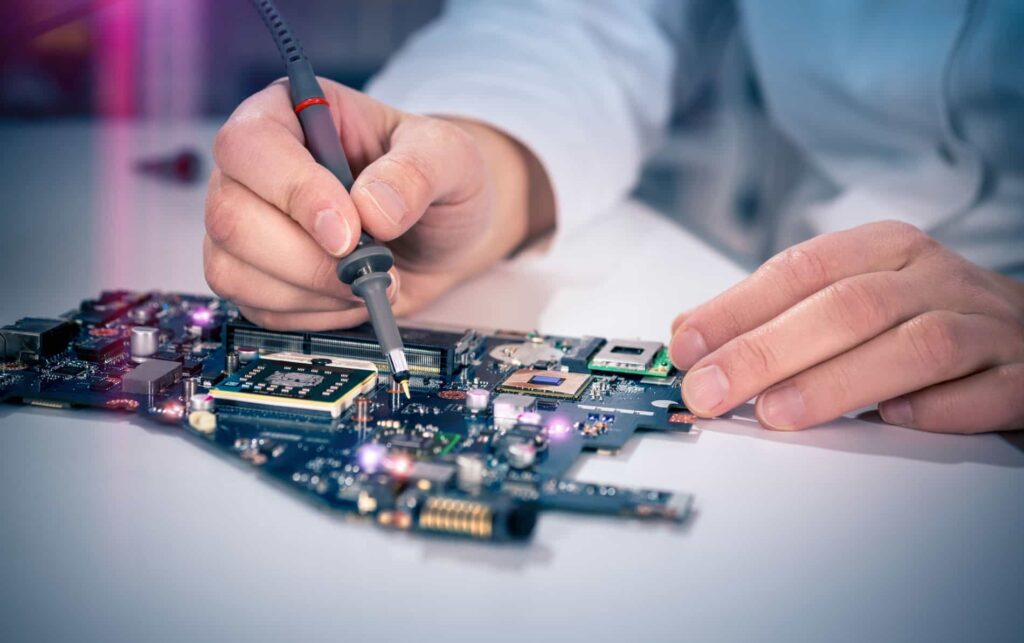
2.Detailed explanation of the electronic manufacturing process
(I) Design and prototyping
Use CAD tools to create a digital blueprint of the product, and then conduct prototype design to verify feasibility, solve potential defects and efficiency problems in a timely manner, and prepare for mass production.
(II) Material procurement
Manufacturers need to purchase various materials required to produce products, including semiconductors, resistors, capacitors, metals, and plastics.
(III) PCB manufacturing
Printed circuit board (PCB) manufacturing involves operations such as etching, layering, drilling, and applying solder mask to create pathways for connecting components. This stage requires advanced technical support to ensure the normal operation of the circuit.
(IV) Component placement and assembly
Depending on the product type, components are placed on the PCB using surface mount technology (SMT) or through-hole technology (THT), and precise operation is carried out with the help of automated equipment to ensure accurate placement of components.
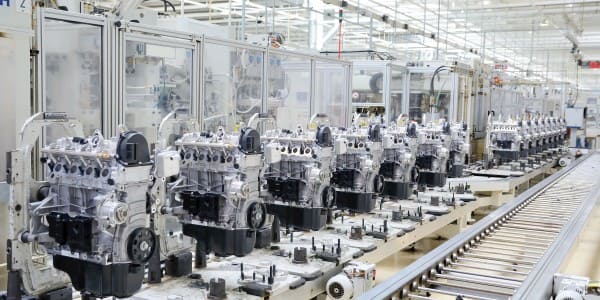
(V) Soldering
After the components are placed, they need to be firmly fixed to the PCB by soldering. Molten metal alloys are used to fix the components, and methods such as reflow soldering or wave soldering can be used to ensure a firm electrical connection.
(VI)Testing and quality control
Any electronic device must undergo rigorous testing before leaving the factory to verify that it meets the necessary performance standards. A variety of testing methods are used to ensure that product performance meets standards, is defect-free, and that the company complies with regulations and quality standards, such as ISO certification.
(VII)Final assembly and packaging
Finally, assembling components into the housing and packaging, connecting external components to ensure stability, packaging to protect the device, and ERP systems to coordinate work, EMS companies meet market needs through integrated manufacturing.
3.Advanced manufacturing technology in electronic manufacturing
(1) Automation and Robots
The application of automation technology significantly reduces the reliance on manual labor in repetitive tasks such as component placement and soldering. Advanced robotic systems can handle complex assembly processes with a precision and speed that exceeds that of human workers, minimizing errors and reducing production time.
(2) Surface mount technology (SMT)
Surface mount technology (SMT), a widely used technology in electronics design and manufacturing, allows components to be mounted directly on the PCB surface without pre-drilling. SMT enables higher component density and faster assembly speeds.
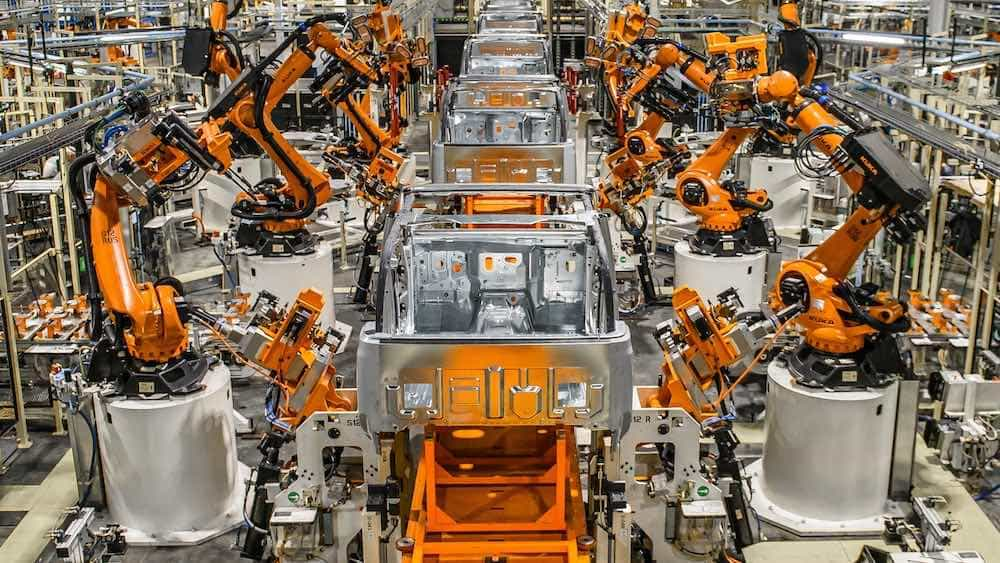
(3) Additive manufacturing (3D printing)
Additive manufacturing, also known as 3D printing, is increasingly popular for rapid prototyping and low-volume production in the electronics manufacturing industry. It enables the manufacture of highly complex and customized components at lower costs and faster turnaround times.
(4) Clean room manufacturing
Clean rooms are required in many electronics manufacturing services, especially when producing sensitive components such as semiconductors and medical devices. Cleanrooms create a controlled environment that keeps dust, contaminants and electrostatic discharge (ESD) to extremely low levels, all of which can damage delicate electronic equipment.
(5) Lean manufacturing and just-in-time (JIT)
To increase efficiency and reduce waste, electronics manufacturing companies often implement lean manufacturing principles and just-in-time (JIT) production strategies. These methods focus on reducing excess inventory, streamlining workflows, and delivering products at the right time.
4.Supply Chain Management in Electronic Manufacturing
(1)Material Procurement
In the supply chain of electronic manufacturing, the procurement of raw materials and electronic components is a key link. Manufacturers need to ensure that there are reliable suppliers for key materials such as semiconductors, capacitors, resistors, and metals. Any fluctuations in the supply chain may cause production delays, so electronic manufacturing companies use advanced ERP systems to manage supplier relationships, monitor inventory levels, and automate procurement to ensure the timely supply of materials and ensure the continuity of production.
(2)Inventory Management
Inventory management needs to find a balance between the high costs caused by too much inventory and the production bottlenecks caused by too little inventory. Manufacturing ERP solutions provide real-time inventory visibility, helping electronic manufacturing companies implement just-in-time (JIT) strategies, reduce excess inventory, reduce waste, ensure that components are available immediately when needed, and improve production efficiency and cost-effectiveness.
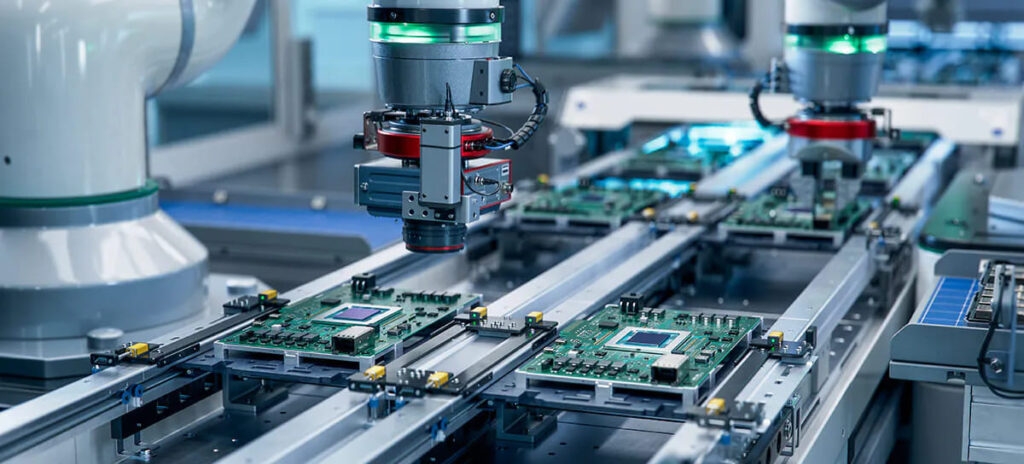
(3)Logistics and Distribution
After product manufacturing is completed, efficient and timely logistics distribution is essential. For large electronic manufacturing service (EMS) companies, coordinating global logistics is challenging, involving many factors such as customs regulations, transportation costs, and delivery times.
(4)Risk Management
The electronics manufacturing industry faces many risks, especially supply chain disruptions, such as natural disasters, political instability or supply shortages, which may affect production. To reduce risks, companies adopt supplier diversification strategies and work with multiple suppliers to supply key components to avoid over-reliance on a single source.
(5)Sustainability
As sustainable development becomes a focus, electronics manufacturers face environmental pressure to ensure that the supply chain meets environmental responsibilities, such as ethically sourcing materials such as rare earth metals and ensuring that suppliers comply with environmental regulations. Companies are also exploring sustainable packaging and energy-saving logistics to reduce their carbon footprint.
5.Challenges and risks in electronic manufacturing and countermeasures
(I) Supply chain disruption
Supply chain disruption is a major risk in electronic manufacturing. Shortages of parts, delayed delivery or price fluctuations may lead to production delays, especially under the influence of global events in recent years.
Solutions include adopting manufacturing ERP systems for predictive analysis, demand forecasting and supply chain diversification, automating inventory management, and implementing just-in-time (JIT) strategies.
(II) Rapid technological progress
Electronic manufacturing technology is changing with each passing day, and keeping up with the pace is a challenge for companies, especially small electronic manufacturing service companies.
The key is to invest in an ERP system that is scalable and adaptable to technological changes, and regularly train employees so that the team can quickly adapt to new production requirements and remain competitive.
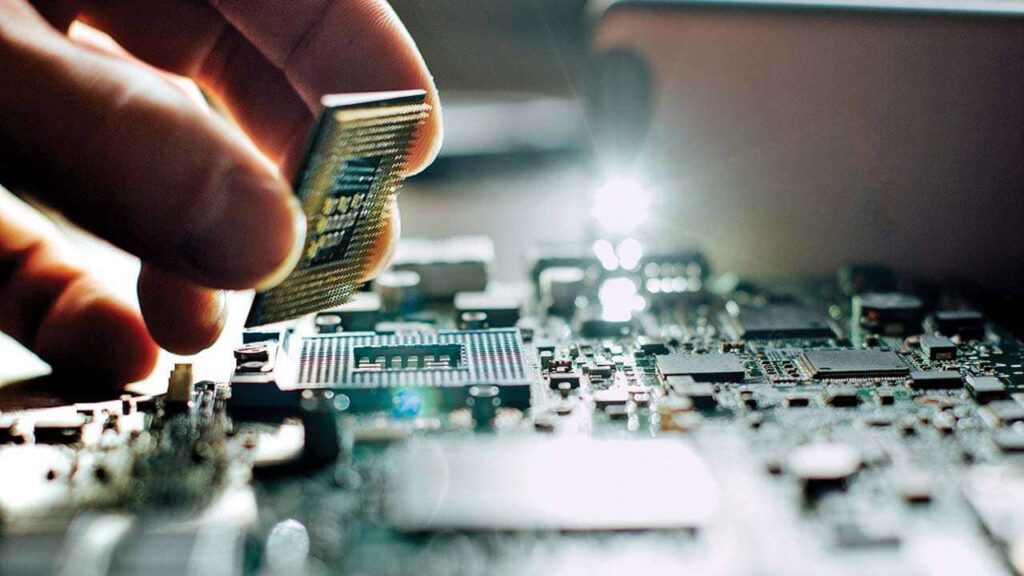
(III) Quality control and product defects
Ensuring high product quality is a key challenge in electronic manufacturing. Defects may lead to recalls, reputation damage and customer dissatisfaction.
Countermeasures include implementing automated testing processes such as automatic optical inspection (AOI) and functional testing, detecting defects in advance through real-time data monitoring integrated with the ERP system, and using lean manufacturing techniques to reduce waste and ensure the quality of the production process.
(IV) Cost pressure
Electronic manufacturing companies face the dual pressure of reducing costs and maintaining high quality and efficiency. Fluctuating material costs, rising labor costs, and technology investment requirements affect profitability.
This can be addressed by implementing efficient automation solutions, using ERP systems to simplify operations, reducing labor costs, adopting lean manufacturing practices to optimize resource utilization, and using ERP systems to manage and predict costs.
(V) Regulatory compliance
Compliance with environmental, product safety, and labor regulations is an important challenge for electronic manufacturing service companies. Regulations vary greatly in different regions, and violations may lead to serious consequences. An ERP system with built-in compliance management tools can help companies understand regulations, ensure that products meet standards, track supply chain compliance, avoid penalties, and maintain corporate reputation.
6. Future Trends in Electronic Manufacturing
(I) Improving Automation and Robotics
Automation is a key driver of electronic manufacturing efficiency, and the trend will continue to grow in the future. Advanced robotics, machine learning, and artificial intelligence (AI) will be more integrated into production lines to improve precision, reduce errors, and optimize processes. Electronic manufacturing companies invest in smart factories, where machines communicate with each other to improve work efficiency and help companies stay competitive.
(II) Internet of Things (IoT)
The IoT has changed the products and processes of electronic manufacturing. IoT-enabled devices collect real-time data to help manufacturers monitor equipment performance, predict maintenance needs, reduce downtime, and improve supply chain visibility.
(III) Sustainability and Green Manufacturing
As consumers and regulators pay more attention to environmental protection, sustainability is becoming increasingly important in electronic manufacturing. Companies are focusing on reducing carbon footprints, electronic waste, and improving energy efficiency, exploring sustainable materials, green energy, and environmentally friendly production processes.
(IV) Additive Manufacturing (3D Printing)
Additive manufacturing is expected to transform the electronic manufacturing process, achieve rapid prototyping and small-scale production, enable manufacturers to more flexibly and quickly manufacture complex electronic components, reduce dependence on traditional manufacturing methods, reduce costs, support customized production, and help electronic design and manufacturing companies bring products to market faster.
(V) Advanced Materials and Miniaturization
The demand for small and powerful electronic devices drives innovation in materials and components. Advances in nanotechnology, flexible electronics, and high-performance materials enable manufacturers to produce smaller, lighter, and more energy-efficient devices, which is particularly important for industries such as wearable technology and medical devices.
(VI) Globalization and Localized Manufacturing
Globalization is a long-term feature of electronic manufacturing, but the trend of localized manufacturing is increasing, driven by time to market, supply chain flexibility, and local market customization needs. Localized manufacturing shortens delivery time, reduces costs, and meets regional regulatory requirements. The manufacturing system coordinates global and local operations to ensure consistency and compliance in different markets.