Importance of Metal CNC Machining
n the field of modern industrial manufacturing, metal CNC machining is a core technology that uses computer-controlled machine tools to accurately shape metal materials to produce final products or components that meet various needs. Metal CNC machining technology combines advanced computer programming and precision machining principles and is widely used in many industries. In this article, we introduce metal CNC machining in detail, which will help you understand metal processing processes and technologies.
1.What is metal CNC machining?
Metal CNC machining is a complex manufacturing process that uses computer-controlled machine tools to shape metal parts into final products or components. This technology is capable of producing metal parts with high precision and complex geometries, and is essential for industries that require complex components.
2.Workflow of Metal CNC Machining
1.Design Preparation
Engineers use computer-aided design (CAD) software to create a detailed 3D model of the part to be produced, which is the basis of machining.
2.CAM Processing
CAD files are usually converted into CNC machine programs with the help of computer-aided manufacturing (CAM) software, which converts the design into G-code that the CNC machine can interpret.
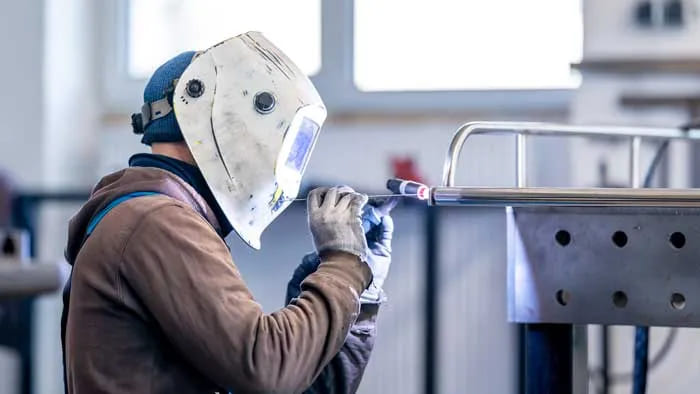
3.Machine Setup
The operator is responsible for installing the correct tools and fixing the raw metal material in place on the CNC machine.
4.Machining
The CNC machine tool follows the program instructions to accurately cut and shape the metal according to the design specifications.
5.Post-processing
After machining, the parts need to go through finishing processes such as polishing and painting to achieve the required surface finish and aesthetic quality.
3.Process types of metal CNC machining
(I) Milling technology
Milling is a machining technology that uses a rotating cutting tool to remove material from a workpiece
Advantages: It can flexibly create complex shapes and fine details under advanced CNC control, with high precision and is suitable for a variety of materials (metals, plastics, composite materials, etc.).
Limitations: Complex parts have a long setup time, a long single-piece processing time, high mass production costs, and as a subtractive process, it is easy to generate waste.
Applicability: It is often used in the processing of fine and complex parts such as engine parts, molds and tools.
(II) Turning technology
Turning is a machining method in which a single-point cutting tool moves linearly when the workpiece rotates, and it plays an important role in metal CNC machining.
Advantages: High production efficiency (especially symmetrical parts), reduced unit cost with scale expansion, excellent surface finish and precise control.
Limitations: Limited to rotationally symmetrical parts, limited incision depth and complexity, and high-quality tools are required to maintain accuracy.
Applicability: Suitable for cylindrical parts such as rods, shafts and fasteners.
(III)Drilling Technology
Drilling is a metal CNC machining technology that uses a multi-point drill to drill holes in materials.
Advantages: It is critical for assembly processes that require bolting or fastening, easy to integrate with other machining operations, and has a high material removal rate.
Limitations: Hole depth and diameter are limited by tool length and strength, and additional finishing processes are often required, and chips and material fragments must be managed.
Applicability: It is widely used in almost all mechanical assembly projects.
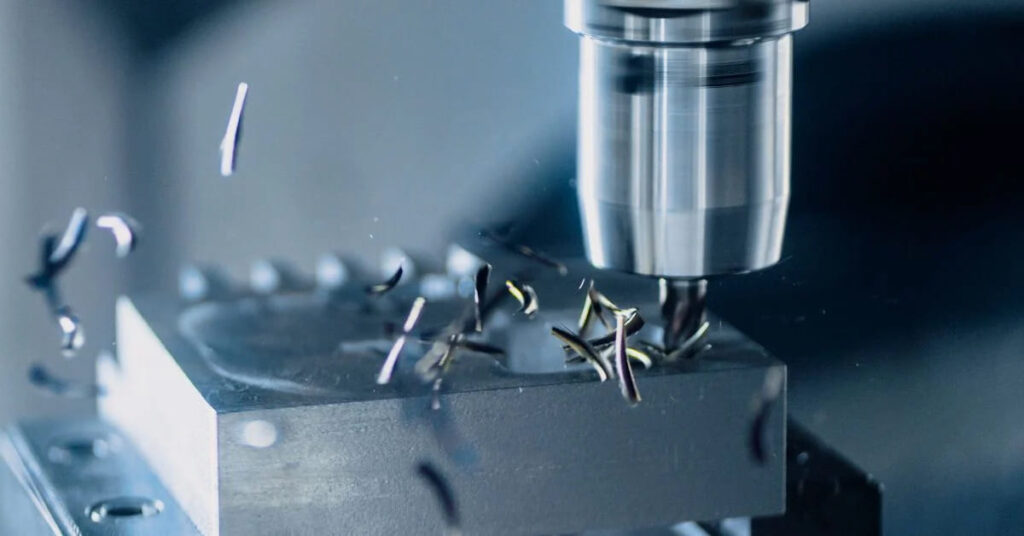
(IV) Boring Technology
Boring is a machining method that uses a single-point cutting tool to refine the existing hole diameter.
Advantages: Improve hole diameter accuracy and surface smoothness, can accurately adjust the hole size, and can correct previous operating errors or misalignments.
Limitations: Pre-existing holes are required, slower and more specialized than drilling, and tool and setup costs are high for high-precision machining.
Applicability: Used in critical applications with strict tolerance requirements for hole size.
(V) Broaching Technology
Broaching is a metal CNC machining technology that uses a toothed tool to remove material in continuous motion.
Advantages: Smooth surface, efficient production of keyways and splines, and precision machining of hard materials.
Limitations: Custom broaches are expensive, not widely used (brroaches are designed for specific shapes), and require careful setup and adjustment.
Applicability: Suitable for mass production of internal gears, slots or complex surface profiles.
(VI) Sawing Technology
Sawing is often used to cut raw materials to the required size before processing.
Advantages: Quick and effective separation of materials, low cost, simple setup and operation.
Limitations: Limited accuracy, generally used for rough cutting, may cause material waste, noise and dust need to be controlled.
Applicability: Suitable for initial material shaping, widely used in manufacturing and construction.
(VII) Grinding Technology
Grinding is a metal CNC machining technology that uses grinding wheels to achieve high precision and high-quality surfaces.
Advantages: Excellent surface finish and dimensional accuracy, suitable for hard materials such as ceramics and hardened steel, and can achieve tight tolerances.
Limitations: Slow material removal rate, not suitable for large-scale material processing, high tool wear cost, requires superb skills and precise settings.
Applicability: Used for final finishing of tools and molds, etc.
(VIII) Tapping Technology
Tapping is a metal CNC machining technology that cuts threads in pre-drilled holes.
Advantages: It is essential for parts that need to be assembled. The high precision of thread production ensures a firm connection. It can be used for a variety of materials.
Limitations: There is a risk of tap breakage if it is not managed properly. The hole size must be accurate before tapping. It is limited by the depth and size of the internal thread.
Applicability: It is a necessary process for manufacturing threaded assembly parts.
4.How to choose the right CNC machining method for metal?
Material compatibility: Different CNC machines work differently on various materials. For example, machining harder materials such as stainless steel may require a more rugged and precise machine (such as a machine with advanced milling capabilities).
Complexity of part design: The complexity of the part to be manufactured will affect the choice of machining process. Designs with intricate details may require a 5-axis milling machine to handle multiple angles and fine cuts.
Production volume: The number of parts required plays an important role in selecting a CNC machine. Large-volume orders may require a powerful system that can run continuously with little downtime.
Tolerance and precision requirements: The precision requirements of the final part affect the choice of CNC machining method. Industries such as aerospace and medical require extremely high tolerances.
Cost-effectiveness: Total cost is a key factor in manufacturing, including machine cost, operation and maintenance costs.
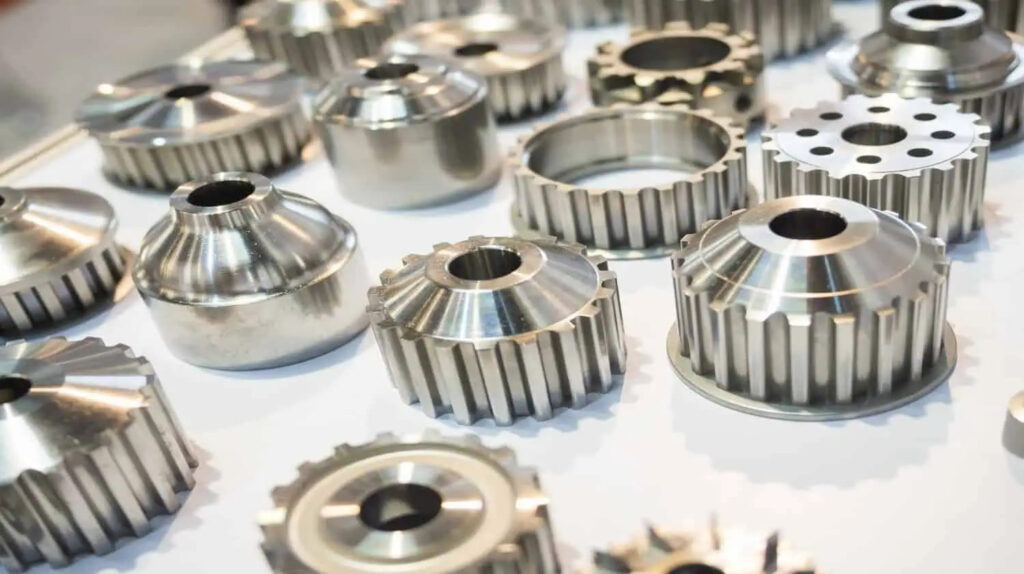
5.Metal materials that can be used for metal CNC machining
(I) Aluminum and aluminum alloys
Aluminum is favored in metal CNC machining because of its good machinability, light weight and corrosion resistance.
6061: Used in aerospace and automotive parts, sharp tools and high cutting speeds are used to prevent material accumulation.
7075: High strength, used for high-stress parts, speed and feed control are required for machining.
2024: Used in aerospace, surface treatment and coolant controlled hardening are required for machining.
(II) Stainless steel
Stainless steel is used in metal CNC machining due to its strength, durability and corrosion resistance.
304: Common, low speed and high feed are used for machining.
316: Strong corrosion resistance, tools must be sharp and cooled for machining.
303: Easy to machine, increasing cutting speed can improve quality.
(III) Brass
Brass (copper-zinc alloy) is used for decoration and low-friction parts in metal CNC machining.
C360: Easy to cut, sharp tools and moderate speed are used for machining.
C330: Slightly lower processing speed and feed.
(IV) Copper and copper alloys
Copper is used for electrical and other applications due to its good thermal and electrical conductivity.
C110: Coolant is used for processing to control temperature.
C101: Feed and speed should be kept stable during processing.
(V) Titanium and titanium alloys
Titanium is used in many industries due to its high strength-to-weight ratio, corrosion resistance, and good biocompatibility.
Level 5: Commonly used, low cutting speed and high feed rate with coolant are used for processing.
Level 2: Sharp tools and cooling are required for processing.
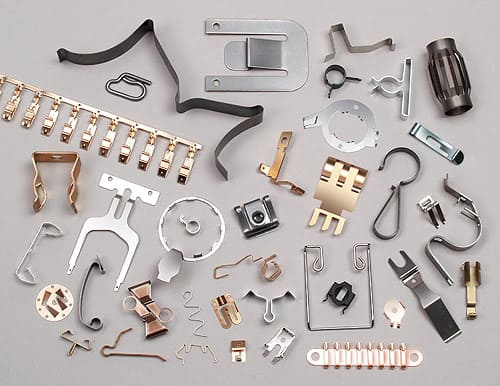
(VI) Tool steel
Tool steel is used to make tools and is critical in metal CNC machining.
A2 tool steel: Preheat before processing, low speed and high feed.
D2 tool steel: Be careful with hardness during processing.
(VII) Nickel alloys
Nickel alloys are corrosion-resistant and heat-resistant, used in harsh environments, and widely used in metal CNC machining.
Inconel 625: Excellent performance, used in aerospace and marine engineering.
Monel 400: Strong corrosion resistance and easy processing.
(VIII) Special alloys
Special alloys are used in challenging environments and perform well in special scenarios.
Hastelloy: Strong chemical resistance, used for parts in corrosive environments.
Zirconium: Heat and corrosion resistance, used for special professional applications.
(IX) Carbon steel
Low carbon: Easy to process, sharp tools and high speeds are used for processing.
Medium carbon: Preheat before processing.
High carbon: Prevent cracking during processing and control cutting parameters.
(X) Alloy steel
4140: Used for a variety of parts, and controlled environment is used for processing.
4340: Used for high-stress aerospace parts, preheat before processing.
(XI) Bronze
Bronze (copper-tin alloy) is the preferred material for bearings and other applications, and is outstanding in metal CNC machining.
Phosphor bronze: Processing quality assurance, use sharp tools and medium speeds.
Aluminum bronze: High hardness, use special tools and cooling methods.
(XII) Magnesium and magnesium alloys
AZ31B: Easy to process, sharp tools and high cutting speeds are used for processing.
AZ91D: Pay attention to brittleness during processing.
(XIII) Zinc and zinc alloys
Zinc alloy 3: Maintain moderate cutting speed during processing.
Zinc alloy 5: For more demanding applications, processing uses a controlled environment.
(XIV) Lead and lead alloys
Lead alloy 300: Process at medium to low speeds.
Lead alloy 500: For special applications, pay attention to ventilation and safety during processing.
6.Industry applications of metal CNC machining
Aerospace industry
Rely on metal CNC machining to manufacture parts that can withstand extreme conditions and have high precision requirements, such as engine brackets, control panels and fuselage structures.
Automotive industry
Used for prototyping and production, common production of engine parts, gearboxes and suspension systems.
Medical industry
It is essential for manufacturing high-precision, sterile medical devices such as implants, surgical instruments and orthotics.
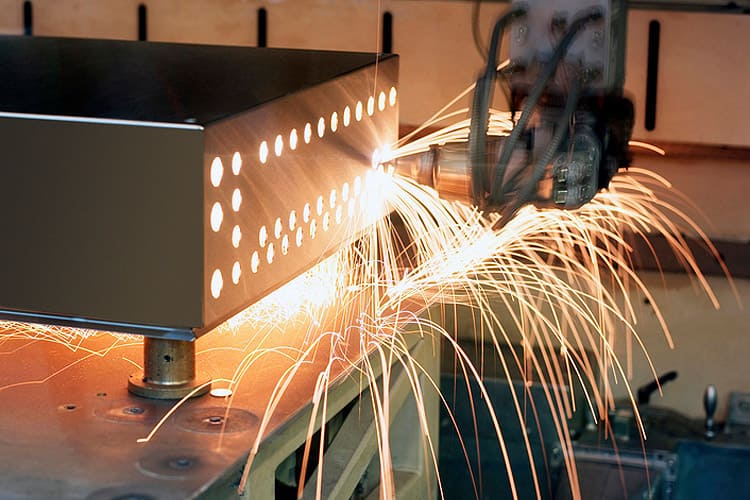
Defense and military
Manufacture rugged and durable parts such as housings, electronic components and other critical hardware.
Electronics and semiconductors
Produce precision and complex components such as connectors, radiators and housings.
Energy sector
Manufacture parts for power generation equipment such as solar panels and turbines.
Industrial and heavy machinery
Manufacture parts that require ruggedness and precision, such as gears, fasteners and hydraulic components.
7.Why is metal CNC processing the first choice?
(1) Improve accuracy
The high-precision operation of CNC machine tools ensures that parts are produced to precise specifications, which is critical in fields such as aerospace and medical equipment that require extremely high precision.
(2) Faster
Once the design parameters are set, the CNC machine can produce parts in rapid succession without the need for manual adjustments, significantly shortening delivery times and increasing productivity.
(3) Improve efficiency
By accurately cutting materials, reducing waste, programming to obtain the best cutting path and sequence, improving the efficiency of material and time utilization, and reducing the cost of mass production.
(4) Complex design and production
CNC technology enables complex designs, handling complex cuts and fine geometries, expanding design possibilities in metal fabrication.
(5) Multifunctionality
CNC machines can machine a variety of materials, from soft to hard metals, and are used in industries as diverse as automotive, aerospace and electronics.
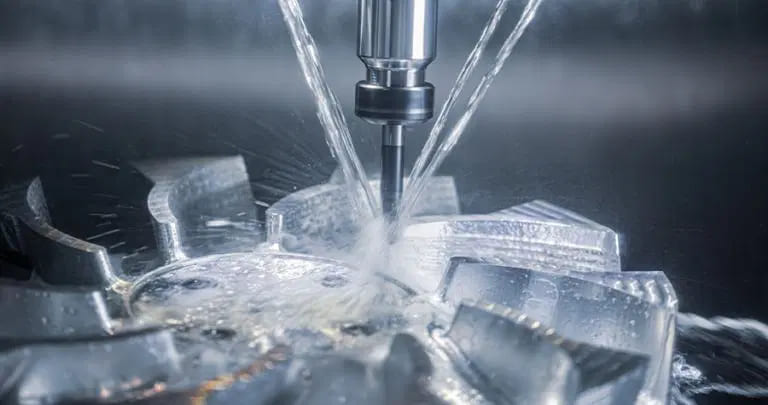
8.Cost considerations for metal CNC processing
(1) Machine investment
CNC machines are technologically advanced and have higher initial costs than traditional machines, but in the long term, increased productivity and lower labor costs justify the investment.
(2) Material cost
The prices of different materials vary significantly. For example, titanium is more expensive than aluminum, which affects the overall production cost.
(3) Design complexity
Complex designs require more complex programming and longer machine operation times, increasing costs but eliminating multiple manufacturing steps.
(4) Production volume
High output reduces setup costs and makes unit costs more economical; in smaller batches, although the cost per piece may be higher, there are advantages in speed and accuracy.
(5) Tools and maintenance
Regular maintenance and tooling costs can add to the overall expense, and CNC machines require specific cutting tools that may wear out and need to be replaced.
(6) Labor costs
Operating complex CNC machines requires skilled technicians, and the cost depends on the level of expertise required.
9. Challenges and Solutions for Metal CNC Machining
(I) Overcoming Specific Material Challenges
Stainless steel: Overheating can lead to work hardening and poor surface finish. Use appropriate coolant flow, optimized cutting speed, and heat-resistant tools.
Titanium: Tools are prone to wear. Use carbide or diamond-coated tools and adjust cutting parameters.
Aluminum: Materials are prone to adhesion. Use lubricants and polished grooves to reduce adhesion.
Copper: Burrs are prone to formation. Use sharp cutting tools and fine-tune feed rates.
Brass: Surface scratches are prone to formation. Keep the working environment clean and tools sharp. Consider using protective film.
Hardened steel: Tool stress is high. Choose slower cutting speeds, higher feed rates, and solid carbide tools.
(II) Quality Control
Vibration: Proper machine maintenance, sharp tools, and optimized machining parameters can reduce vibration and avoid poor surface finish and inaccurate dimensions.
Material inconsistency: Use high-quality, consistent material sources and perform material inspections before machining.
Programming errors: Use advanced CAM software with simulation capabilities to detect potential errors.
10.Comparison of Metal CNC Machining with Other Metal Machining Technologies
(I) Comparison with Traditional Machining
Higher precision and better repeatability.
Faster speed, especially for complex or large-volume work.
Flexible, suitable for customization and small-volume production.
High initial cost, but cost-effective in the long run for complex and repetitive work.
More material-saving, advanced software can optimize cutting paths.
(II) Comparison with Additive Manufacturing
CNC parts are more durable and made from solid blocks of material.
Can process more types of metals.
Better surface finish and tighter tolerances.
High-volume production is faster and more cost-effective.
Highly complex parts may cost more, but 3D printing costs do not increase with complexity.
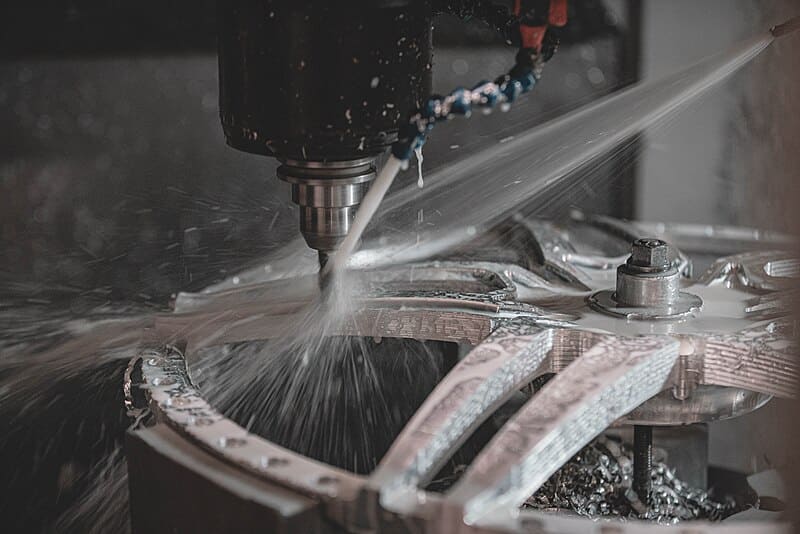
11. How to choose a metal CNC machining supplier
(I) Equipment and technology
Ensure that the supplier uses the latest technology and machines, such as CNC milling machines and lathes, to handle project complexity and provide precise results.
(II) Experience and expertise
Look for suppliers with a good track record and experienced engineers who can provide insights and solutions for specific needs.
(III) Quality control measures
Quality assurance is non-negotiable. Check whether the supplier follows strict quality control procedures, including incoming material inspection, process inspection and final testing.
(IV) Certification and standards
Verify that the supplier adheres to industry standards and holds relevant certifications to demonstrate its commitment to quality and consistency.
(V) Delivery and flexibility
Consider the supplier’s ability to meet schedules. Fast turnaround time is crucial in urgent projects.
(VI) Customer service and communication
Effective communication is key. Choose suppliers who are responsive and transparent in communication to ensure timely updates.
(VII) Scalability
Evaluate whether the supplier can scale up or down operations according to project needs, handle peak loads and expand production.
Conclusion
Metal CNC machining has significant advantages in modern manufacturing and provides high-precision, high-efficiency and high-quality solutions for the metal manufacturing industry.Metal CNC machining plays an important role in different application scenarios. By rationally selecting and applying these technologies, high-precision and high-quality metal parts processing can be achieved to meet the needs of modern industrial manufacturing. In the future, with the continuous advancement of technology, metal CNC machining technology will continue to innovate and develop, bringing more opportunities and challenges to the manufacturing industry.
If you are looking for an experienced metal CNC machining manufacturer, Xavier is your ideal choice. The Xavier team is well-equipped to provide high-quality CNC machining solutions. If you want to learn more or discuss your machining needs with us, please feel free to contact us.