The Basics of Rapid Metal Casting and Its Applications
This article discusses some of the key benefits and possible applications of rapid metal casting, the only rapid prototyping solution for metal casting.
1.Why choose rapid metal casting?
Product designers can benefit from two unique sets of benefits when using rapid metal casting to make prototypes.
①The first set of benefits has to do with the metal casting process itself
For example, die casting is a manufacturing process that uses a mold cavity to create a part from molten metal. This is typically a very expensive process because of the specialized equipment required. However, its benefits are significant.
One of the advantages of pressure die casting is its economies of scale. Unlike CNC machining, die casting is most cost-effective when ordered in large quantities. This is because the mold cavity can be used multiple times to make multiple units of a part, with the unit cost gradually decreasing as the order size increases. This is one of the characteristics it shares with injection molding, which also has high startup costs but lower subsequent unit costs.
Another advantage of die casting is its ability to make very large metal parts, such as automotive engine blocks, camera chassis and floodlight housings, which are difficult to machine from metal blanks. The process also produces excellent surface finish, dimensional accuracy and tensile strength.
Advantages of Pressure Die Casting:
- Low cost of scale
- Large parts
- Good surface finish
- High dimensional accuracy
- High tensile strength
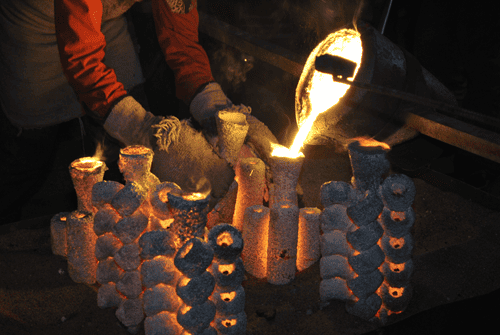
②The second set of advantages involves the rapid prototyping aspect of rapid metal casting
Customers who use our rapid metal casting services not only reap the rewards of the die casting process, but also manufacture parts at speeds, quantities and price points typically associated with low-cost prototyping processes.
One of the main benefits of rapid metal casting is that it provides product designers with a final-stage prototype that may be nearly identical to the finished part. Since die casting is a specialized process for end-use parts, rapid metal casting is one of the most representative prototyping services for such parts. It combines the convenience of prototyping with the quality of end-use.
Likewise, rapid metal casting enables engineers to mechanically test prototypes of products that are about to be cast in a more accurate way. For example, a rapidly cast engine block prototype can be tested in the factory to accurately understand the performance of the final casting.
Combining die casting with rapid prototyping also allows companies to benefit from other aspects of rapid prototyping. First, speed and convenience. With Xavier, your cast metal prototypes can be professionally machined through our CNC machining centers to add details, engraving, or other features.
Advantages of Rapid Metal Casting:
- Small supply (50+)
- Fast turnaround
- Professional process
- Representative prototypes
- Combined with CNC or surface treatment processes
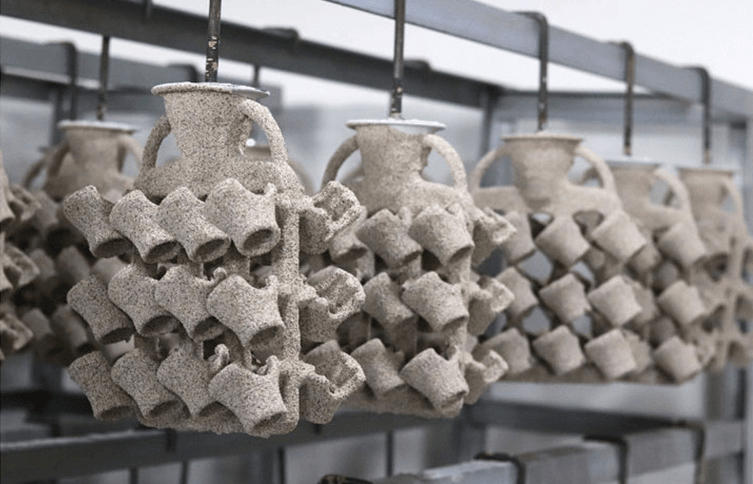
2.Ultra-low quantities with investment casting
When one or a few castings are needed to validate the design of a part, it can be a headache for designers – especially when testing its mechanical properties.
One possible solution is 3D printing. With the increasing popularity of DMLS and SLM, 3D printing metal parts is no longer very expensive. In addition, more and more materials are available: you can 3D print parts in aluminum, steel, stainless steel, titanium, etc. The problem, however, is that the mechanical properties of a 3D printed prototype will never 100% match the finished part due to different manufacturing processes. This is why engineers are so eager to make real castings for mechanical testing.
No large foundry company is willing to make one-off castings because they are set up for large-scale production. It is neither convenient nor economical for them to make small batches of wax patterns. But this is where Xavier comes in. We are able to prepare wax patterns using 3D printing, and when we deliver the wax patterns to casting companies, it becomes a breeze for them.
When making 20 to 50 castings, things are different. Printing more than 20 wax patterns is expensive, while making aluminum molds for the wax patterns is not expensive. So, what is the solution for this order size? Xavier once again gave the answer. We can use 3D printing or CNC machining to make a master pattern, and then use the master pattern to make a silicone mold. Then the 20 to 50 wax patterns can be completed using a vacuum casting process.
For a few hundred castings or more, traditional metal casting companies are more than happy to meet customer needs. However, it is still difficult to find a company with reliable quality. We believe that we have found the most reliable manufacturing partner in this field on the market.
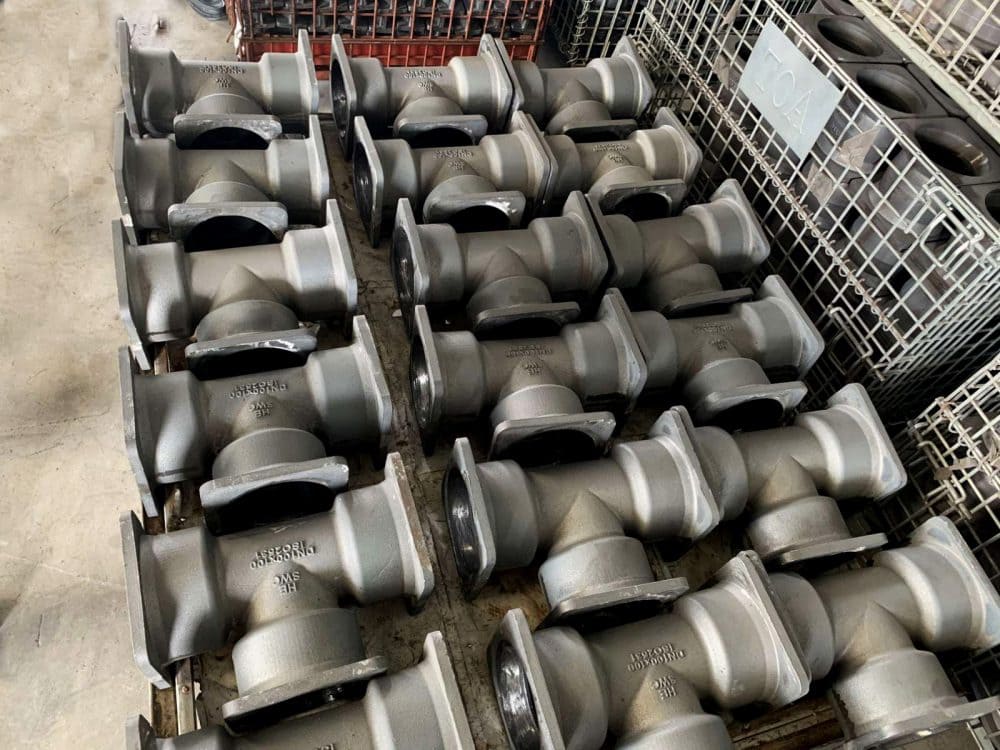
3.Applications of Rapid Metal Casting
Rapid metal casting can be used to make prototypes and small batches of parts in multiple industries. Some of the most common applications of rapid metal casting include:
① Automobile
Die casting is often used to make automotive metal parts, and rapid metal casting enables automotive companies to obtain and test prototypes of new cars.
Cast metal automotive parts include:
- Engine block
- Cooling fan
- Fuel tank cap
- Truck/bus air valve
- Gear lever
- Headlight countersunk
- Gearbox
- Pedals
② Medical
The excellent strength and surface finish of die casting make the process suitable for a variety of healthcare products that can be produced in small batches through rapid metal casting.
Cast metal medical parts include:
- Pacemaker
- Hospital bed parts
- Stethoscope housing
- Monitor
- Dialysis equipment parts
- Oxygen pump
③ Electronic products
Mass production parts for consumer electronics are often made using the die casting process, and rapid metal casting is an effective way to prototype electronic parts or create short-term orders for specialized electronic products.
Cast metal electronic parts include:
- Tablet housing
- Printer coupling
- Headphone housing
- Smart watch buckle
- Camera chassis