A Comprehensive Guide to Sheet Metal Machining
Sheet metal machining allows you to manufacture different products using a combination of various techniques and compatible materials. Hence, the popularity of sheet metal machining techniques demonstrates its importance for a wide range of applications. However, it is vital to understand how the process works so you can take advantage of it.
This article explores the basics of sheet metal machining, describing the relevant techniques and their applications. You will also learn about the various advantages of the process and the materials and finishes that are suitable for metalworking processes. Read on to broaden your knowledge of sheet metal processes.
1.What is sheet metal machining?
Sheet metal machining is a manufacturing technique that involves manufacturing products from flat sheets of metal. Hence, you can manufacture sheet metal using different methods involving advanced machinery to form, bend, cut, and assemble the metal into any desired shape.
The various sheet metal machining processes are compatible with a wide range of metal materials. These include stainless steel, aluminum, copper, brass, zinc, and steel. The thickness of these metal sheets ranges from 0.006 to 0.25 inches. Thinner gauges offer more ductility, while thicker gauges are ideal for heavy-duty applications.
Furthermore, sheet metal machining is performed with the help of computer-aided design applications. It provides a 3D graphical representation of the final production product. 3D files are usually converted into machine code (G-code) that controls the operation. As a result, the machine can accurately cut, join, and form the final product from different metal sheets.
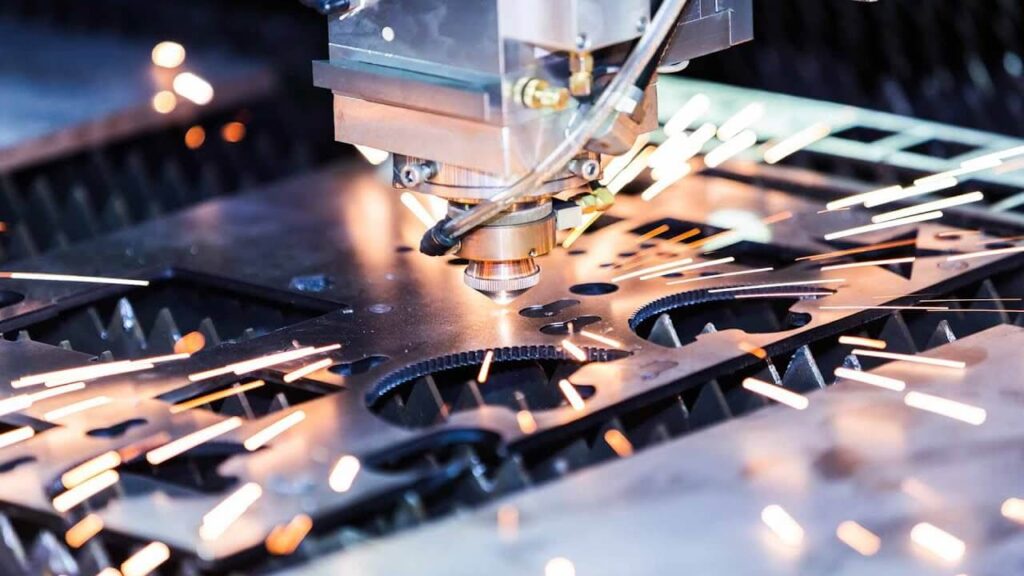
2.3 sheet metal machining techniques
Custom sheet metal manufacturing involves a variety of techniques. Some of these techniques have more advantages and compatibility than others. Therefore, a deep understanding of the different processes is essential to achieve the most effective design.
The following introduces 3 types of sheet metal machining techniques:
- Cutting sheet metal
- Forming sheet metal
- Joining sheet metal
3.Sheet metal machining cutting techniques
Cutting is usually the first stage of the sheet metal machining process. You can cut different shapes or structures from a rectangular sheet of metal to meet the design requirements. The main cutting techniques involve two categories: cutting without shear and cutting with shear.
1) Cutting without shear
There are several processes that can adequately cut sheet metal materials without shearing forces. These techniques involve extreme heat, high pressure, vaporization, and sandblasting to shape sheet metal manufacturing parts.
They include the following:
- Laser cutting
Sheet metal laser cutting involves using a focused laser beam to melt metal in a localized area. Laser cutting machines can cut a wide range of metals, from non-ferrous metals to mild steel and stainless steel.
The technology consists of two sub-processes that run simultaneously. The first sub-process involves focusing a high-powered laser beam on a sheet of metal. The material absorbs the thermal energy of the laser beam, causing it to vaporize.
Meanwhile, the second process involves the cutting nozzle providing a gas blow for the laser cutting, which is usually oxygen or nitrogen and helps protect the processing head from spatter and steam during sheet metal processing.
- Plasma Cutting
Plasma cutting is a process that uses an ionized gas (called plasma) to thermally cut metal. This method uses a lot of heat to cut the metal, resulting in large burrs and oxidation zones close to the cutting area. In addition, it allows for faster cutting, high accuracy, and repeatability in sheet metal manufacturing.
Plasma cutting tools are only effective on conductive metal sheets. Therefore, it is one of the most suitable methods for cutting medium-thickness aluminum conductive materials.
- Waterjet Cutting
This cutting process uses a high-pressure water stream to cut sheet metal. Waterjet cutting is versatile and can cut a variety of hard and soft materials using pressurized water and abrasives. It is ideal for cutting soft materials, metal foil, fabric or rubber. At the same time, it is also suitable for cutting hard materials such as copper, carbon steel, aluminum and carbon steel.
The required pressure is usually about 60,000 psi and the speed is 610m/s to cut different types of metal sheets. However, water jet cutting is a better alternative to laser cutting technology.
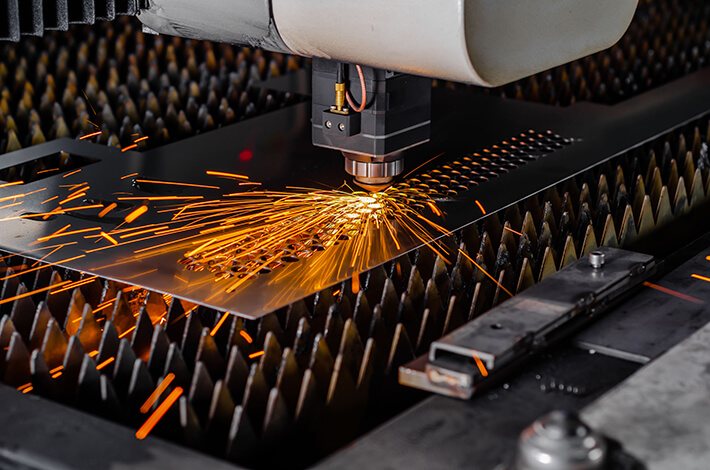
2) Cutting with shears
The processes under this category use shearing forces to overcome the ultimate shear strength of the metal to cut metal materials. They usually involve the use of dies, punches and shears to fully cut the metal.
The technologies here include the following:
- Shearing
Shearing is suitable for large-scale applications and cutting soft materials such as brass, aluminum and mild steel that do not require a clean surface. It cuts straight lines on metal sheets with flat surfaces. The shearing method involves applying shearing forces on the surface to split the flat metal material at the cutting point.
This is usually an ideal process for making straight edges on metal sheets with rough edges. This process is cost-effective for high-volume operations that produce thousands of metal sheet manufacturing parts in a short period of time. However, shearing may not be perfect for applications that require a high-quality surface finish because shearing produces burrs and material deformation.
- Punching
Punching uses shearing forces to create holes in sheet metal. In this sheet metal manufacturing process, the scrap is the material removed from the hole, and the final part is the material remaining on the die.
Punching is suitable for making cutouts and holes of different shapes and sizes. However, using the punching process can be time-consuming. You must match the die and the punch knife correctly.
- Blanking
Blanking is an ideal process for economical sheet metal manufacturing. It involves using a blanking punch and die to remove a section of sheet metal from a larger piece of stock material. The punch applies a “blanking force” to the sheet metal during the blanking process, while the die holds it in place.
The extracted material is the preferred part, while the material remaining on the die is the remaining ferrous stock. The process has high repeatability, dimensional control, and excellent precision, suitable for making economical custom parts.
- Sawing
Sawing uses a sawtooth tool to make a series of tiny cuts in the metal to cut metal materials. The teeth of a saw use shearing and friction forces to tear small sections of metal material. Band saws have a variety of fine teeth and slightly curved teeth suitable for cutting brass, aluminum, and other non-ferrous metal sheets.
Horizontal band saws help cut longer bars to the required size. On the other hand, vertical band saws help achieve complex cuts that require precise contours of metal parts.
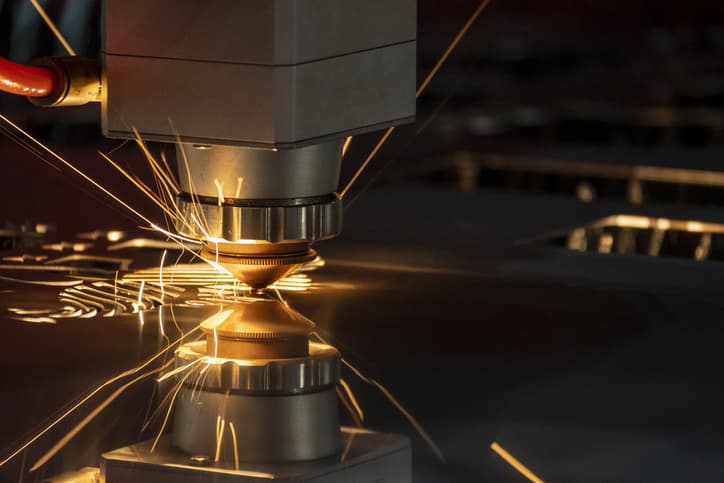
4.Sheet metal machining forming techniques
Sheet metal forming techniques help to reshape the material while keeping it in a solid state. However, these techniques differ in the application of creating custom sheet metal fabrication. This section will explain the basic forming techniques used in sheet metal engineering.
1) Bending
Sheet metal bending is extremely cost-effective in small and medium-scale production. It involves deforming the metal surface with force and bending it at the desired angle to form the desired shape. You can use a press brake and a rolling machine to perform this operation. This technique is suitable for spring steel, copper, and aluminum 5052.
2) Rolling
Rolling is the process of passing a metal piece through a pair of rollers to gradually reduce the thickness of the metal or to obtain a balanced thickness. These rollers rotate continuously and efficiently, creating compressive forces. As a result, these forces plastically change the shape of the workpiece.
Cold rolling and hot rolling are the two main rolling processes. Cold rolling is usually carried out at room temperature, while hot rolling occurs above the recrystallization temperature of the material. Discs, stampings, rims, tubes, and pipes are typical rolled sheet metal fabrication parts.
3) Stamping
Stamping combines complex cutting and forming processes with shorter sheet metal manufacturing operations to create complex parts. Sheet metal stamping is a typical cold forming technology that uses a punch and die to shape raw materials into different shapes. It is compatible with many sheet metal materials, including copper, aluminum, low-carbon steel and high-carbon steel, and brass.
Metal stamping technology is generally low-cost, fast, and requires little tooling and labor time. In addition, you can also automate the stamping process to obtain high-quality precision parts and repeatability. However, the operating cost is high, and it is challenging to change the design during production.
4) Hemming
Hemming is a custom sheet metal manufacturing process that rolls up the edge of the sheet metal to form an area with two layers. It is usually divided into two different stages. The first stage involves mixing the sheet metal and placing it into a V-shaped die. On the other hand, the second stage involves removing the material and placing it into a flattening die. It helps to flatten the hem while giving it the desired shape.
Hemming is usually effective in strengthening the edge of the part and improving its appearance. The process has excellent precision and helps to produce components with high-quality surface effects. However, material deformation usually occurs during this process, resulting in dimensional changes.
5) Curling
Curling is the process of joining a round hollow coil to the edge of a metal sheet. The curling process is usually divided into three stages. The first two stages form the curve of the curling, while the third stage closes the curling.
Curling effectively removes unprocessed sharp edges on the workpiece, making it easier to handle. Curling increases the strength of the workpiece. However, curling can cause burrs and material deformation. Therefore, the process requires extra care to be completed correctly.
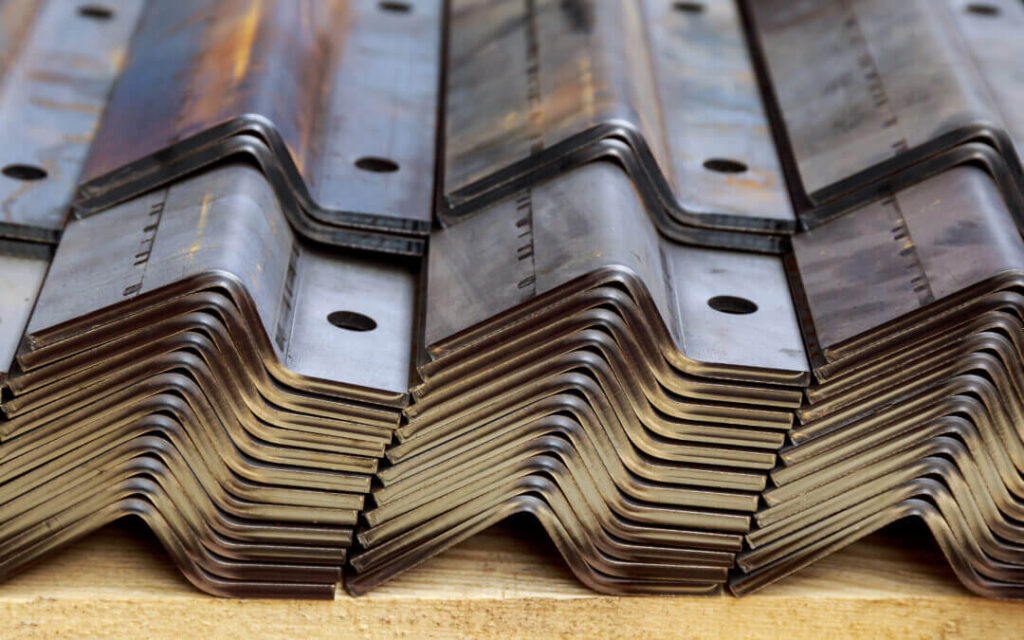
5.Sheet metal machining Joining technology
The following are the joining technologies involved in the sheet metal manufacturing process:
1) Welding
Welding is a standard process of joining metal sheets into a single component by heating them to the melting point and fixing them with a welding gun. It is one of the basic processes in the final stage of sheet metal engineering.
There are several techniques for welding sheet metal, including:
- Metal arc welding (SMAW)
- Metal inert gas (MIG) welding
- Tungsten inert gas (TIG) welding
These three techniques differ in their methods. But they all aim to join metals by melting the edges of the parts and adding filler. As a result, they form a metallurgical bond between the parts, making them firmly connected.
2) Riveting
Riveting involves drilling holes in the metal sheets to be joined and then installing rivets. After the rivet is inserted, it is deformed by squeezing the tail of the rivet. Doing so flattens the tail of the rivet and prevents it from falling off. In addition, riveting is suitable for non-ferrous metal parts such as aluminum and copper.
It comes in two forms: cold riveting and hot riveting. Cold riveting is suitable for non-ferrous metals and lightweight metals with a diameter less than 10 mm. In contrast, hot riveting involves applying heat of 1000 – 1100áµ’C to steel rivets over 10 mm.
6.Advantages of sheet metal machining
Sheet metal machining includes a variety of technologies that help manufacture parts for many industries.
The main benefits of sheet metal machining include:
1) Lightweight component manufacturing
Sheet metal machining is ideal for producing lightweight components. Industries such as aerospace and automotive that require lightweight engine components rely on custom sheet metal manufacturing for quality materials and technologies.
In addition, this machining method helps to manufacture sheet metal parts that improve the fuel economy of aircraft and automobiles while ensuring efficiency.
2) Wide range of technologies and materials
As discussed in this article, the sheet metal machining process involves a variety of technologies. Therefore, there is no shortage of technologies to choose from for your project.
This machining process also allows you to choose from a variety of sheet metal materials, including copper, stainless steel, steel, aluminum, and other custom metal sheets. The material you choose will determine the application of the final product.
3) Efficiency and Accuracy
Sheet metal technology improves efficiency and precision manufacturing capabilities. It helps to create prototypes faster with high precision and accuracy. For example, some laser cutting machines can achieve cuts of about 0.0005 inches.
In addition, it is important to understand that most sheet metal technologies are automated. So once you enter the code on the computer, the machine starts running. The process prevents human errors. As a result, the final product usually has little or no deformation.
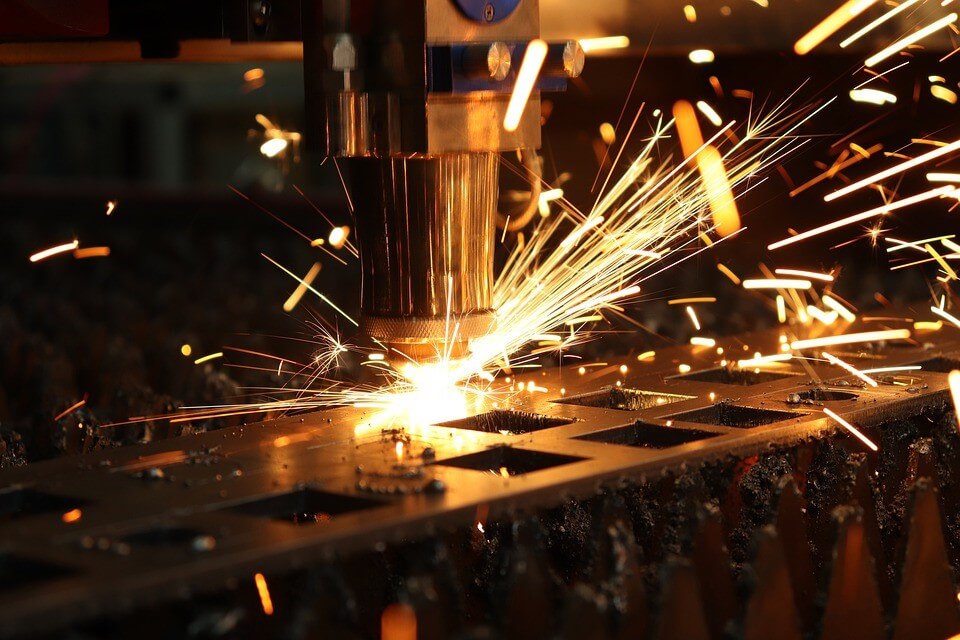
7.Available sheet metal machining materials
There are many materials that are suitable for sheet metal work. Here are some of the common sheet metal fabrication materials:
- Stainless steel
- Hot rolled steel
- Cold rolled steel
- Pre-plated steel
- Carbon steel
- Aluminum
- Copper
- Brass
8.Surface finishing for sheet metal machining
Surface finishing is an essential aspect of custom sheet metal fabrication. It provides both functional and aesthetic advantages to the fabricated parts.
Here are some of the surface finishes for sheet metal fabrication parts:
- Powder coating
- Sandblasting
- Brushing
- Plating
- Anodizing
- Laser engraving
- Screen printing
9.Industrial applications of sheet metal machining parts
Many industries use sheet metal machining parts in their daily operations. Here are some of those industries:
1) Automotive
The sheet metal machining process has paved the way for innovative designs in automobiles due to the availability of production-grade materials. The metal forming capabilities of this technology help to create a perfect frame out of thin sheet metal.
Hence, most automotive parts are stamped and laser machined. For example, the hoods, fenders, side panels, and roofs of most vehicles are sheet metal engineering products.
2) Aerospace
Custom sheet metal machining helps to produce a wide range of space-ready components and lightweight parts. Components used in the aerospace industry often require tighter tolerances and high precision. Therefore, you can combine sheet metals such as aluminum and steel with improved methods to create complex spacecraft and aircraft designs.
3) Healthcare
Sheet metal engineering helps to detect design errors and provide reliable solutions based on the quality and accuracy requirements of medical tools. Sheet metal prototyping and manufacturing is ideal for MRI applications and for producing scalpels and surgical instruments. You can automate these processes to prevent human errors and improve the accuracy of manufacturing medical devices.
4) Housings
Sheet metal machining helps to produce affordable housings to protect sensitive gearboxes and equipment. Moreover, the machined parts protect the tools from environmental impacts and prevent dust ingress. Similarly, using sheet metal machining techniques, you can make various cable connection cutouts, such as glass windows, LED panels, light pipes, and HDMI.
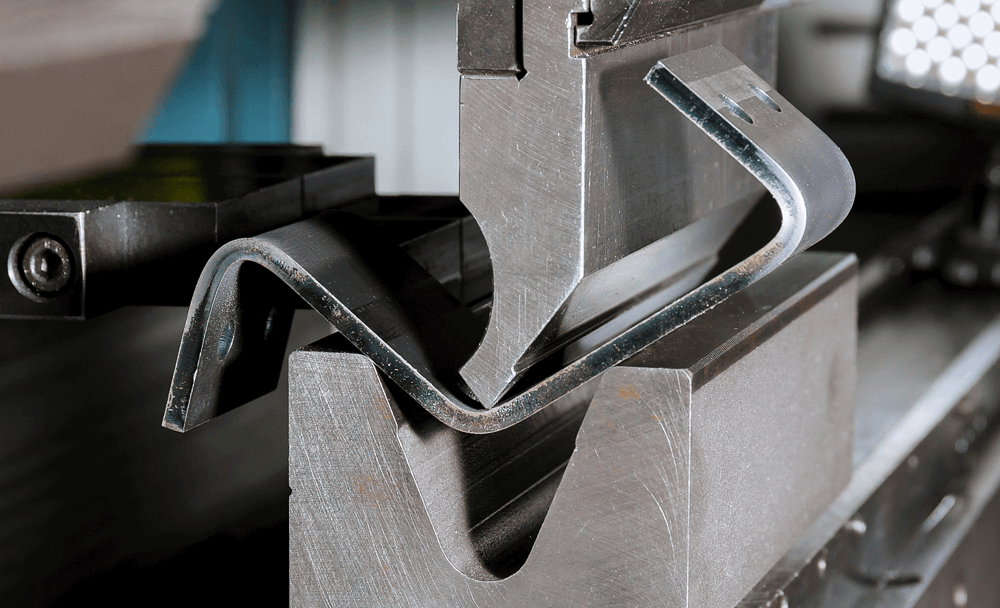
10.sheet metal machining design tips
Here are some sheet metal design tips that are critical for manufacturability:
1) Chamber wall thickness
Since sheet metal parts are made from a single piece of metal sheet, the geometry of each component must maintain a uniform thickness. Generally, you can manufacture sheet metal parts with a thickness of at least 0.9 mm to 20 mm.
However, different custom sheet metal machining technologies are suitable for different thicknesses. For example, laser cutting is suitable for metals with a thickness between 0.5 mm and 10 mm. In contrast, sheet metal bending can be suitable for metal sheets with a thickness between 0.5 mm and 6 mm.
2) Hole and slot orientation
In custom sheet metal manufacturing, the diameter of holes and slots is an important factor to consider when modeling parts. The diameter of holes and slots should be as large as the material thickness. In addition, sufficient space should be left between holes. Never place holes too close to the edge of the material.
3) Bend Allowance and Deduction
Bend allowance is the extra length of material you need to add to the actual measurements of the part to create a flat pattern. On the other hand, bend deduction is the material that needs to be cut out from the flange length to obtain a balanced design.
4) Bend Radius
It is very important to keep the internal bend radius of the sheet metal equal to its thickness. This prevents sheet metal defects and deformation in the final product. Therefore, maintaining a consistent bend radius throughout the part helps ensure excellent positioning and cost-effectiveness of sheet metal engineering.
11.Conclusion
Making parts using sheet metal machining is an excellent choice. It offers several advantages, including efficiency and accuracy, manufacturing lightweight components, and compatibility with a wide range of materials and techniques. Therefore, understanding the different methods, applications, and design techniques involved in this process is essential for the success of the project.