Introduction to Stainless Steel Processing
Stainless steel is a versatile and durable material used in a variety of industries, including construction, automotive, and manufacturing, including washing machine spare parts. Its unique properties make it an ideal choice for many applications, but the process of transforming raw stainless steel into a finished product requires careful planning and execution.
In this Ultimate Guide to Stainless Steel Processing, we’ll explore the different stages involved in stainless steel processing, from raw material selection to the final product.
step1
The first step in stainless steel processing is the selection of the raw material. Stainless steel is made up of a combination of iron, chromium, and other elements, which give it its corrosion-resistant properties. Different grades of stainless steel are available, each with its own unique composition and characteristics. The choice of the grade depends on the specific requirements of the end product, such as strength, resistance to heat or chemicals, and aesthetic appeal.
Once the raw material is selected, it goes through a series of processes to shape it into the desired shape. One of the most common methods is hot rolling, where stainless steel is heated and passed through a series of rollers to reduce its thickness and increase its length. The process not only changes the dimensions of the material, but also improves its mechanical properties, such as washing machine spare parts.
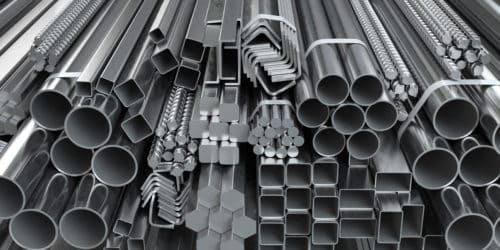
step2
After hot rolling, stainless steel is ready for further processing, such as cold rolling or annealing. Cold rolling involves passing material through rollers at room temperature to achieve a smoother surface finish and tighter tolerances. Annealing, on the other hand, heats stainless steel to a specific temperature and then slowly cools it to eliminate internal stress and improve its ductility.
step3
Another important aspect of stainless steel processing is surface treatment. Stainless steel can be finished in various ways to enhance its appearance and protect it from corrosion. Common surface treatments include polishing, brushing, and passivation. Polishing involves using abrasive materials to remove imperfections and create a smooth, reflective surface. Brushing, on the other hand, creates a textured finish by brushing the stainless steel with a wire brush. Passivation is a chemical process that removes impurities from the surface and forms a protective oxide layer.
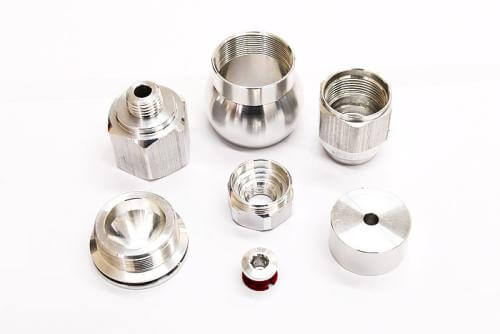
step4
In addition to shaping and surface treatment, stainless steel processing also involves joining different components together. Welding is a commonly used method for joining stainless steel parts. It involves melting the edges of the parts and fusing them together using heat and pressure. Other methods, such as brazing and soldering, can also be used depending on the specific requirements of the application.
step5
Throughout the entire stainless steel processing journey, quality control is of utmost importance. Strict quality control measures are implemented at each stage to ensure that the final product meets the required specifications. This includes testing the material for its mechanical properties, chemical composition, and surface finish. Non-destructive testing methods, such as ultrasonic testing and X-ray inspection, are also used to detect any defects or flaws that may affect the performance of the stainless steel.
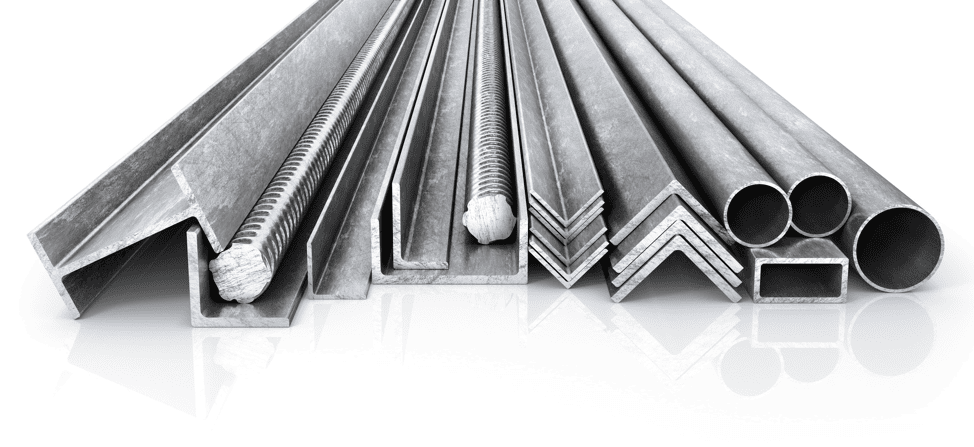
In conclusion, stainless steel processing is a complex and intricate process that involves several stages, from raw material selection to the final product. Each stage requires careful planning and execution to ensure that the stainless steel meets the desired specifications. By understanding the different processes involved in stainless steel processing, manufacturers can produce high-quality stainless steel products that meet the diverse needs of various industries.