Introduction to Thread Tap Types
Thread taps are essential tools used in the manufacturing and construction industries to create internal threads in materials such as metal, plastic, and wood. These threads are crucial for joining components together securely and ensuring the integrity of the final product. However, not all thread taps are created equal. There are various types of thread taps available, each designed for specific applications and materials. In this comprehensive guide, we will explore the different thread tap types, their uses, and the factors to consider when choosing the right tap for your project.
Before delving into the details of thread tap types, it is also important to understand the basic concepts of threading. Threading involves cutting or forming spiral grooves on the inside surface of a hole to create a passage for a screw or bolt. This process securely fastens the components and ensures the stability and strength of the final assembly.
The most common thread tap types are the taper tap, plug tap, and bottoming tap. Each of these taps serves a specific purpose and has distinct characteristics that make them suitable for different applications. The taper tap, also known as the starting tap, has a gradual taper from the tip to the shank. This design allows for easy alignment and starting of the tap in the hole. Taper taps are commonly used when starting a new thread or when the material being tapped is difficult to work with.
The plug tap, on the other hand, has a more pronounced taper at the tip, which allows for a more aggressive cutting action. This type of tap is used to deepen and clean up existing threads or when a through-hole is required. The plug tap is versatile and can be used in a wide range of materials, making it a popular choice for general-purpose threading.
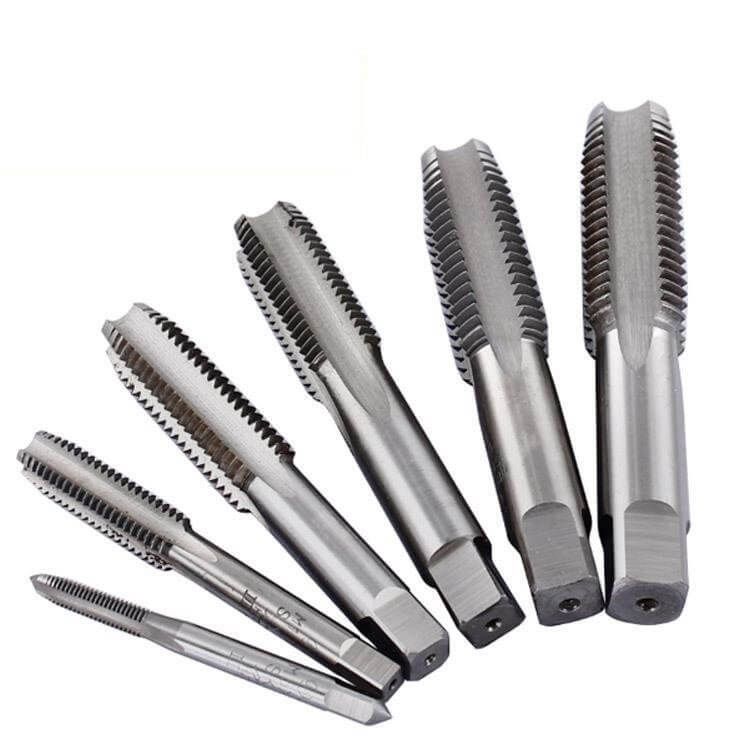
Lastly, the bottoming tap, also known as the finishing tap, has a very short taper and is used to cut threads close to the bottom of a blind hole. Blind holes are holes that do not go all the way through the material. The bottoming tap is designed to reach the bottom of these holes and create threads that are flush with the surface. This type of tap is commonly used in applications where aesthetics and flushness are important, such as in decorative metalwork or when assembling components with limited clearance.
When choosing the right thread tap for your project, several factors need to be considered. The material being tapped is one of the most critical factors. Different materials have different hardness levels, and using the wrong tap can result in poor thread quality or even damage to the tap itself. For example, when tapping soft materials like plastic or aluminum, a high-speed steel tap is usually sufficient. However, when working with harder materials like stainless steel or hardened steel, a cobalt or carbide tap may be required to withstand the increased cutting forces.
Another important consideration is the thread size and pitch. Thread taps come in various sizes and pitches to accommodate different screw or bolt sizes. It is crucial to select the tap that matches the desired thread size and pitch to ensure proper fit and functionality.
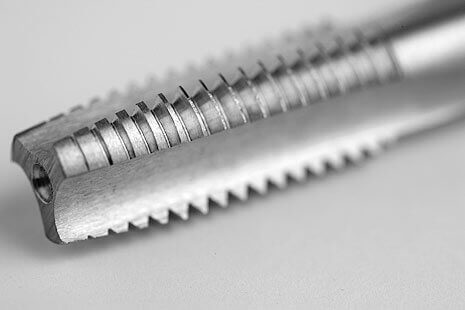
In conclusion, thread taps are indispensable tools in the manufacturing and construction industries. Understanding the different thread tap types and their specific uses is essential for achieving high-quality threaded holes. Whether you are starting a new thread, deepening existing threads, or creating flush threads in blind holes, there is a thread tap designed to meet your needs. By considering factors such as material hardness, thread size, and pitch, you can select the right tap for your project and ensure successful and reliable thread creation.